Technology and Applications of 1018 steel
1018 steel, a low-carbon steel, finds versatile applications due to its excellent weldability and machinability. It contains around 0.18% carbon and 0.6-0.9% manganese, making it relatively soft and easy to work with while retaining sufficient strength for many uses.
Applications:
1. Machined Parts: Used extensively in the automotive and machinery industries for parts requiring precise dimensions and smooth finishes.
2. Shafts and Axles: Commonly used in manufacturing shafts due to its strength and good surface hardness after heat treatment.
3. Fasteners: Bolts, nuts, and screws benefit from 1018 steel’s ease of fabrication and ability to withstand moderate loads.
4. Construction: Structural components such as beams, angles, and plates where weldability and moderate strength are essential.
5. Tooling and Dies: Used for forming dies, jigs, and fixtures due to its machinability and wear resistance.
Technology:
– Welding: 1018 steel welds easily using any conventional welding method, making it suitable for structures and assemblies requiring joining.
– Machinability: The steel can be readily machined into complex shapes with minimal tool wear, reducing manufacturing costs and time.
– Heat Treatment: Although not typically hardened by heat treatment, it can be case-hardened to increase surface hardness and wear resistance.
In conclusion, 1018 steel’s combination of ease of fabrication, moderate strength, and affordability makes it indispensable in various industries, from automotive to construction, where its properties contribute to efficient manufacturing processes and reliable end products.
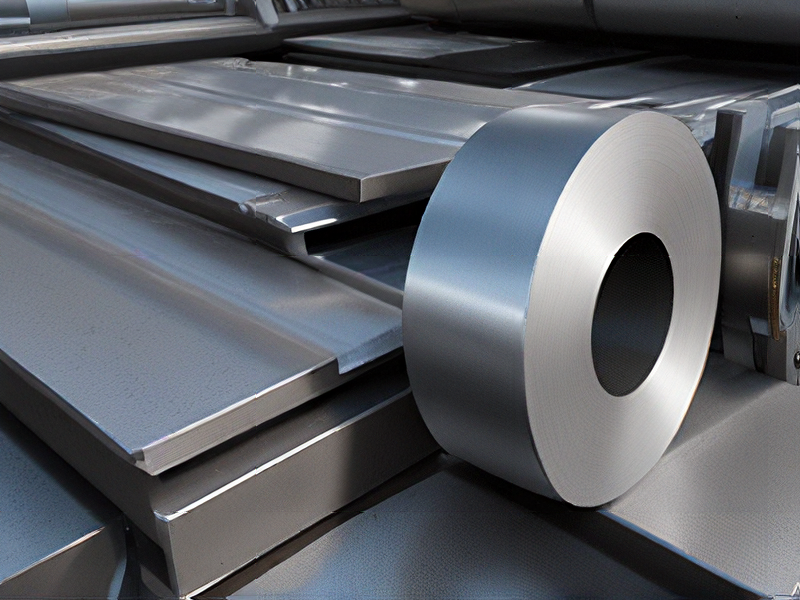
Quality Testing Methods for 1018 steel and how to control quality
Quality testing for 1018 steel involves various methods to ensure its mechanical properties and composition meet standards. Here are key testing methods and quality control practices:
Testing Methods:
1. Chemical Analysis:
– Spectroscopy: Determines the chemical composition to verify the presence of carbon, manganese, and other elements within specified limits.
2. Mechanical Testing:
– Tensile Test: Measures the steel’s strength and ductility by pulling a sample until it breaks.
– Hardness Test: Commonly done using Rockwell or Brinell hardness scales to assess the material’s resistance to deformation.
– Impact Test: Charpy or Izod tests determine the toughness by measuring the energy absorbed during fracture at different temperatures.
3. Non-Destructive Testing (NDT):
– Ultrasonic Testing (UT): Detects internal flaws or inclusions by sending high-frequency sound waves through the material.
– Magnetic Particle Testing (MPT): Identifies surface and near-surface defects in ferromagnetic materials using magnetic fields and ferrous particles.
– X-ray or Radiographic Testing: Reveals internal defects using X-ray imaging.
4. Microstructural Analysis:
– Microscopy: Examines grain size and phase distribution to assess the material’s structural integrity.
Quality Control Practices:
1. Standard Compliance: Ensure that the material meets ASTM A108 or similar standards for 1018 steel.
2. Batch Testing: Regular testing of random samples from each batch ensures consistency and compliance.
3. Process Control: Implement Statistical Process Control (SPC) to monitor and control the manufacturing process.
4. Inspection Protocols: Set up rigorous inspection protocols at various stages of production, including raw material inspection, in-process inspection, and final product inspection.
5. Documentation: Maintain thorough records of all test results, process adjustments, and inspections to trace and address any quality issues.
6. Training: Ensure that personnel are well-trained in testing methods and quality control procedures.
By combining these testing methods and quality control practices, manufacturers can ensure that 1018 steel meets required specifications and maintains high quality.
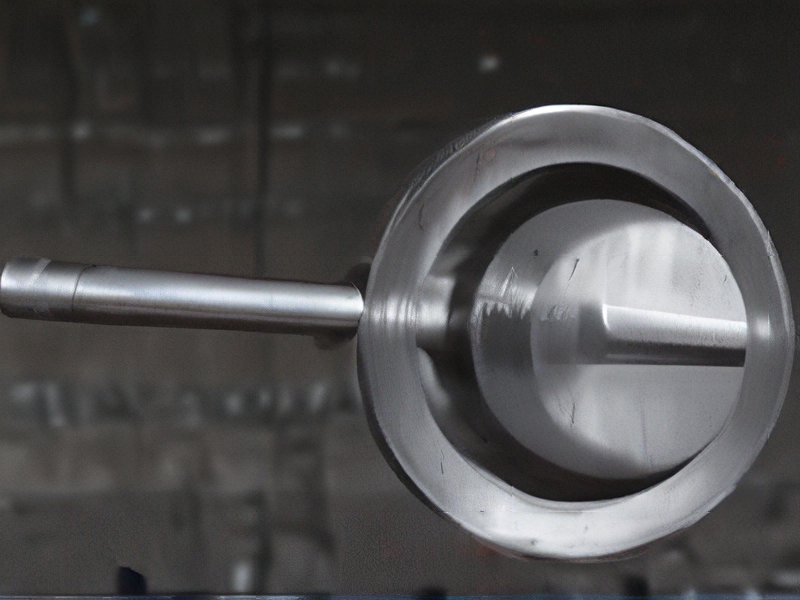
Tips for Procurement and Considerations when Purchasing from 1018 steel
When purchasing 1018 steel, several key considerations can help ensure effective procurement:
1. Material Specifications: Verify that the 1018 steel meets your project’s required specifications for strength, hardness, and machinability. 1018 steel is known for its good weldability and formability, making it suitable for a variety of applications.
2. Supplier Reputation: Choose a reputable supplier known for consistent quality and reliable delivery times. Look for certifications that demonstrate adherence to industry standards.
3. Cost and Budget: Compare prices from multiple suppliers to ensure competitiveness. Consider any additional costs such as shipping, handling, and potential tariffs or duties.
4. Quantity and Lead Time: Determine the required quantity of 1018 steel and ensure the supplier can meet your project timelines. Factor in lead times for production and delivery.
5. Material Testing and Certification: Request material test reports (MTRs) to verify chemical composition, mechanical properties, and conformity to specifications. This ensures the steel’s reliability and suitability for your application.
6. Customer Support and Services: Evaluate the supplier’s customer service and technical support capabilities. A responsive supplier can help address any issues promptly and provide guidance when needed.
7. Environmental and Regulatory Compliance: Ensure the supplier complies with environmental regulations and industry standards for sustainability and ethical practices.
By considering these factors, you can make informed decisions when purchasing 1018 steel, ensuring it meets your project requirements while maintaining cost-effectiveness and quality standards.
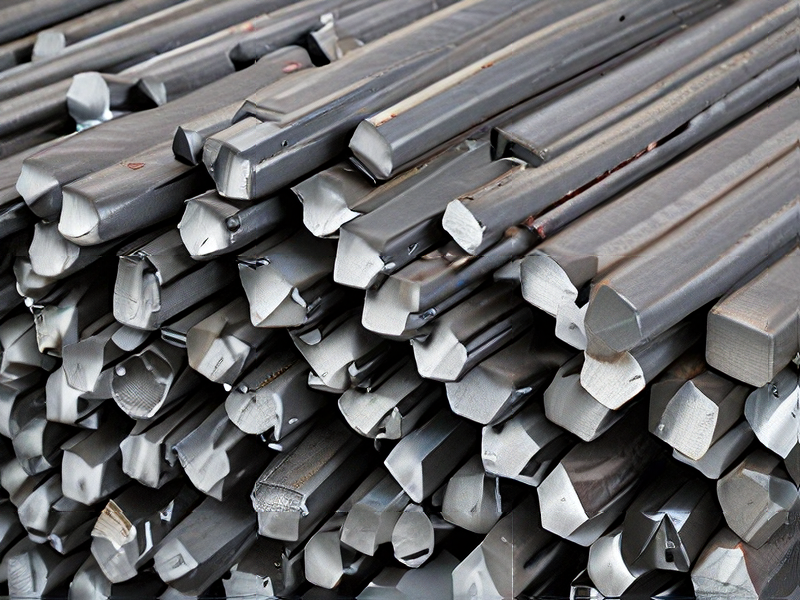
FAQs on Sourcing and Manufacturing from 1018 steel in China
Sourcing and manufacturing products from 1018 steel in China involves several key considerations:
1. Supplier Selection: Choose suppliers with proven experience in handling 1018 steel. Look for certifications like ISO 9001 for quality management and ISO 14001 for environmental management.
2. Material Quality: Verify the quality of 1018 steel through material certifications (e.g., ASTM A108). Conduct inspections or request samples to ensure compliance with your specifications.
3. Manufacturing Processes: Ensure that the supplier uses appropriate manufacturing processes such as cold drawing, hot rolling, or machining, depending on your product requirements.
4. Cost and Pricing: Compare quotes from multiple suppliers to ensure competitive pricing. Consider factors like shipping costs, tariffs, and import duties when calculating total costs.
5. Communication and Contracts: Clearly communicate your requirements regarding quality standards, delivery schedules, and payment terms. Have a well-defined contract that includes provisions for quality control and dispute resolution.
6. Logistics and Shipping: Plan logistics carefully to manage lead times and potential delays. Consider partnering with freight forwarders or logistics providers experienced in international shipping.
7. Quality Control: Implement quality control measures throughout the manufacturing process. Conduct inspections at key stages to ensure consistency and compliance with specifications.
8. Intellectual Property: Protect your intellectual property by outlining confidentiality and proprietary rights in contracts. Consider legal advice to safeguard designs, processes, and trademarks.
By addressing these aspects diligently, you can effectively source and manufacture products from 1018 steel in China while ensuring quality, cost-effectiveness, and compliance with your specifications.
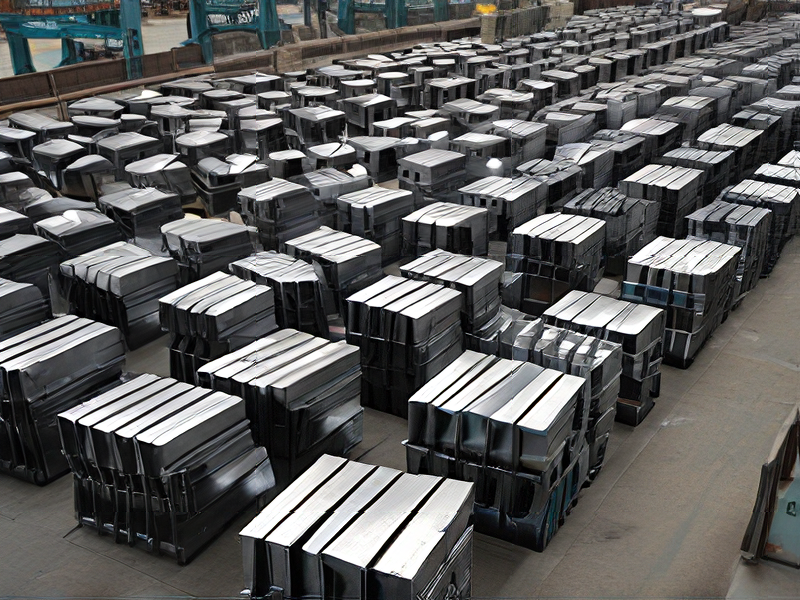