Technology and Applications of 304 and 316 stainless steel
304 Stainless Steel:
304 stainless steel, known for its excellent corrosion resistance and formability, is the most common stainless steel grade. Composed of 18-20% chromium and 8-10.5% nickel, it offers good oxidation resistance and is suitable for a variety of applications.
Applications:
1. Household Appliances: Used in kitchen sinks, cutlery, and cookware due to its resistance to rust and ease of cleaning.
2. Industrial Uses: Employed in chemical containers, food processing equipment, and brewing tanks because of its ability to withstand various chemicals.
3. Construction: Utilized in architectural paneling, railings, and trim due to its aesthetic appeal and durability.
Technology:
The technology involves cold working techniques to enhance its strength and hardness. It’s often processed through stamping, bending, and welding for various applications. Advanced methods like laser cutting and 3D printing are also used.
316 Stainless Steel:
316 stainless steel contains 16-18% chromium, 10-14% nickel, and 2-3% molybdenum, which enhances its resistance to pitting and crevice corrosion, particularly in chloride environments. This makes it more durable in harsh conditions.
Applications:
1. Marine Environments: Used in boat fittings, valves, and pump parts due to its superior resistance to saltwater corrosion.
2. Medical Devices: Preferred for surgical instruments and implants because of its biocompatibility and resistance to bodily fluids.
3. Chemical Processing: Ideal for equipment in chemical and petrochemical plants, as it withstands highly corrosive substances.
Technology:
The processing of 316 involves advanced techniques like electropolishing to enhance its corrosion resistance. Additive manufacturing and high-precision machining are also employed to create complex parts for specialized uses.
In summary, while both 304 and 316 stainless steels are used across various industries due to their corrosion resistance and durability, 316’s additional molybdenum content makes it more suitable for challenging environments. The choice between them depends on the specific requirements of the application, particularly regarding exposure to corrosive elements.
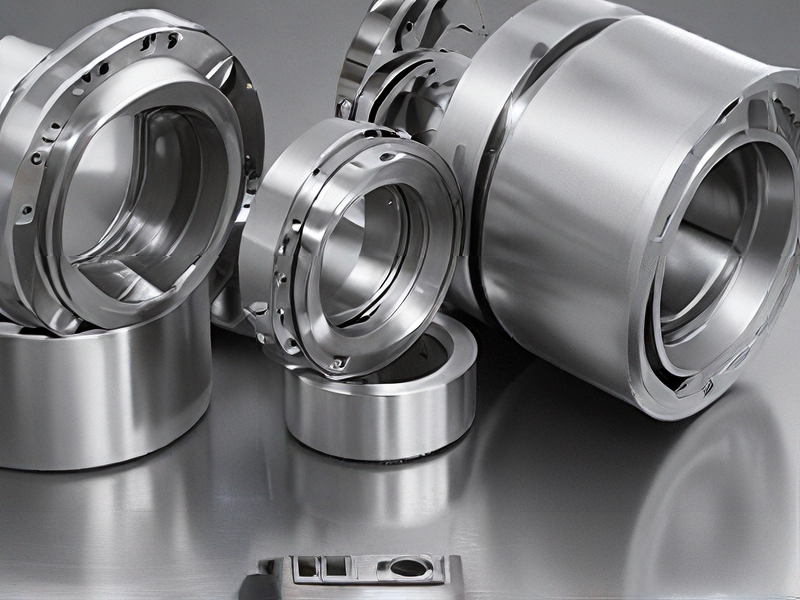
Quality Testing Methods for 304 and 316 stainless steel and how to control quality
Quality testing methods for 304 and 316 stainless steel include:
1. Chemical Analysis: Verify the composition using spectrometers or X-ray fluorescence (XRF) to ensure the correct amounts of chromium, nickel, and molybdenum.
2. Mechanical Testing: Conduct tensile, hardness, and impact tests to check for strength, ductility, and toughness. Tensile tests measure the force required to break the steel, while hardness tests assess resistance to indentation. Impact tests evaluate material behavior under sudden force.
3. Corrosion Testing: Use methods like salt spray tests or immersion tests to evaluate resistance to rust and corrosion. This is crucial for environments where the steel will be exposed to harsh conditions.
4. Microstructural Analysis: Perform metallography using optical or electron microscopes to inspect grain size, phase distribution, and detect inclusions or defects.
5. Nondestructive Testing (NDT): Techniques such as ultrasonic testing, radiography, and dye penetrant testing help identify surface and subsurface defects without damaging the material.
Quality Control Measures
1. Standard Operating Procedures (SOPs): Establish and adhere to SOPs for all processes, ensuring consistency in production and testing.
2. Supplier Quality Assurance: Source raw materials from reputable suppliers and conduct incoming inspections to verify quality.
3. In-Process Monitoring: Implement continuous monitoring and control of key process parameters like temperature, pressure, and chemical concentrations during manufacturing.
4. Final Inspection: Conduct a comprehensive review of the finished product, including visual inspections and final mechanical and chemical tests.
5. Certification and Documentation: Maintain detailed records of all tests and inspections, and provide certifications of compliance with industry standards (e.g., ASTM, ISO).
6. Training and Competency: Ensure that personnel involved in testing and quality control are properly trained and certified.
By combining these testing methods and quality control measures, manufacturers can ensure the reliability and performance of 304 and 316 stainless steel in their intended applications.
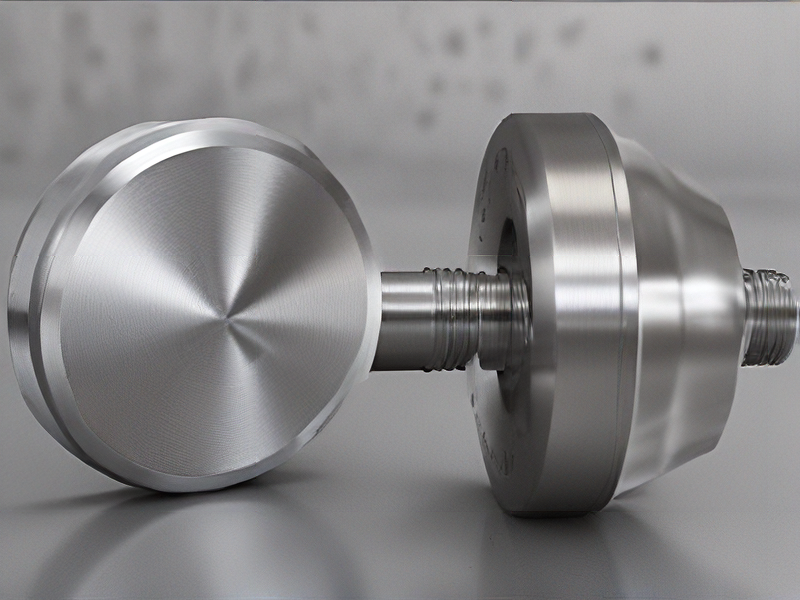
Tips for Procurement and Considerations when Purchasing from 304 and 316 stainless steel
When procuring stainless steel, understanding the differences between 304 and 316 grades is crucial for making informed decisions. Here are some key tips and considerations:
1. Corrosion Resistance:
– 304 Stainless Steel: Offers good corrosion resistance and is suitable for most indoor applications.
– 316 Stainless Steel: Contains molybdenum, which enhances resistance to chlorides and other corrosives, making it ideal for marine and harsh chemical environments.
2. Cost:
– 304 Stainless Steel: Generally more affordable than 316 due to the absence of molybdenum.
– 316 Stainless Steel: More expensive but provides better longevity in corrosive environments.
3. Applications:
– 304 Stainless Steel: Commonly used in kitchen equipment, storage tanks, and indoor architectural elements.
– 316 Stainless Steel: Preferred for applications like chemical processing equipment, outdoor furniture, and marine applications due to its superior corrosion resistance.
4. Weldability and Fabrication:
– Both 304 and 316 stainless steels have excellent weldability and are easy to fabricate, though 316 may require more precise handling due to its higher alloy content.
5. Temperature Tolerance:
– 304 Stainless Steel: Suitable for a wide range of temperatures but may not perform well in extreme conditions.
– 316 Stainless Steel: Offers better performance in extreme temperatures and environments.
6. Aesthetic Considerations:
– 304 Stainless Steel: Often used where appearance is important and less exposure to harsh conditions.
– 316 Stainless Steel: Chosen for both appearance and durability in aggressive environments.
7. Maintenance:
– Regular cleaning is essential for both grades to maintain their appearance and prevent staining.
Key Takeaway: Choose 304 stainless steel for cost-effective, general-purpose applications. Opt for 316 stainless steel when superior corrosion resistance and durability are required, especially in harsh or marine environments.

FAQs on Sourcing and Manufacturing from 304 and 316 stainless steel in China
FAQs on Sourcing and Manufacturing from 304 and 316 Stainless Steel in China
1. What are 304 and 316 stainless steel?
– 304 stainless steel: Known for its corrosion resistance and versatility, 304 contains 18% chromium and 8% nickel.
– 316 stainless steel: Offers better corrosion resistance, especially against chlorides, due to 2-3% molybdenum addition.
2. Why source stainless steel from China?
– Cost-effectiveness: Lower production costs and economies of scale.
– Manufacturing capacity: Extensive infrastructure and capabilities for high-volume production.
– Quality standards: Many Chinese manufacturers comply with international standards like ASTM and ISO.
3. How to ensure quality when sourcing from China?
– Certification: Request material certifications (e.g., ASTM, ISO).
– Audits: Conduct factory audits and inspections.
– Samples: Obtain and test samples before large orders.
– Third-party inspections: Use services for additional verification.
4. What are common applications for 304 and 316 stainless steel?
– 304: Kitchen equipment, food processing, architecture, and chemical containers.
– 316: Marine environments, pharmaceuticals, medical implants, and chemical processing.
5. What challenges might arise in sourcing from China?
– Communication barriers: Language differences can affect clarity.
– Quality control: Variability in standards requires stringent checks.
– Logistics: Shipping and customs processes can be complex.
6. How to choose the right manufacturer?
– Research: Look for manufacturers with good reputations and reviews.
– Experience: Prefer manufacturers with experience in your specific industry.
– Compliance: Ensure they adhere to relevant standards and regulations.
7. What are the lead times for production?
– Typically ranges from 4-12 weeks, depending on the order size and complexity.
8. How to handle intellectual property concerns?
– NDA agreements: Ensure robust Non-Disclosure Agreements.
– Patents: Register patents in China to protect your IP.
9. What are the import duties and taxes?
– Varies by country; consult with a customs broker for specific details related to your location.
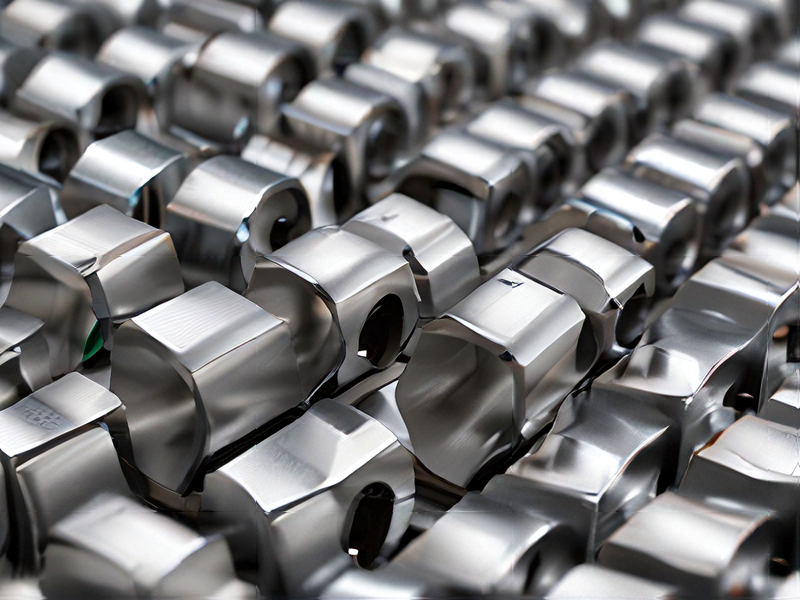