Technology and Applications of 304 or 316 stainless steel
Stainless steel grades 304 and 316 are widely used due to their excellent corrosion resistance, durability, and versatility.
304 stainless steel, an austenitic grade, is known for its good general corrosion resistance, making it suitable for applications like:
* Food and beverage industry: Utensils, tanks, pipes, and processing equipment.
* Construction: Architectural cladding, window frames, handrails, and structural components.
* Automotive industry: Exhaust systems, fuel tanks, and interior trim.
316 stainless steel, also austenitic, offers superior corrosion resistance to 304, particularly against chloride ions. This makes it ideal for:
* Marine environments: Shipbuilding, offshore structures, and desalination plants.
* Chemical processing: Reactors, tanks, and piping systems handling corrosive chemicals.
* Medical devices: Implants, surgical instruments, and diagnostic equipment.
Both grades can be further processed into various forms like sheets, coils, bars, tubes, and wires, allowing for diverse applications across industries.

Quality Testing Methods for 304 or 316 stainless steel and how to control quality
Quality Testing Methods for 304 and 316 Stainless Steel
1. Chemical Analysis: Utilizes spectrometers or X-ray fluorescence (XRF) to verify alloy composition, ensuring it meets the specified grade (e.g., 18% chromium, 8-10% nickel for 304).
2. Mechanical Testing: Involves tensile tests to measure strength, ductility, and elongation. Hardness tests (e.g., Rockwell or Brinell) assess material hardness.
3. Corrosion Resistance Testing: ASTM G48 or salt spray tests evaluate resistance to pitting and crevice corrosion, especially critical for 316, which contains molybdenum for enhanced resistance.
4. Microstructure Analysis: Optical microscopy or scanning electron microscopy (SEM) examines grain size and phase distribution, checking for unwanted phases like sigma phase.
5. Non-Destructive Testing (NDT): Methods like ultrasonic testing, radiography, or dye penetrant inspections detect internal or surface defects without damaging the material.
Quality Control Measures
1. Material Certification: Ensure all raw materials come with mill test certificates (MTC) verifying compliance with specifications.
2. Process Control: Implement strict controls during manufacturing, such as maintaining proper temperatures during welding to prevent carbide precipitation.
3. Inspection and Testing Protocols: Establish routine inspection schedules and testing protocols throughout the production process to identify and address issues early.
4. Supplier Audits: Conduct regular audits of suppliers to ensure they adhere to quality standards and use proper testing methods.
5. Documentation and Traceability: Maintain thorough documentation of testing and inspection results, ensuring full traceability from raw materials to finished products.
6. Training and Certification: Regularly train and certify staff in quality control procedures and testing techniques to maintain high standards.
By employing these methods and controls, manufacturers can ensure the consistent quality and performance of 304 and 316 stainless steel products.
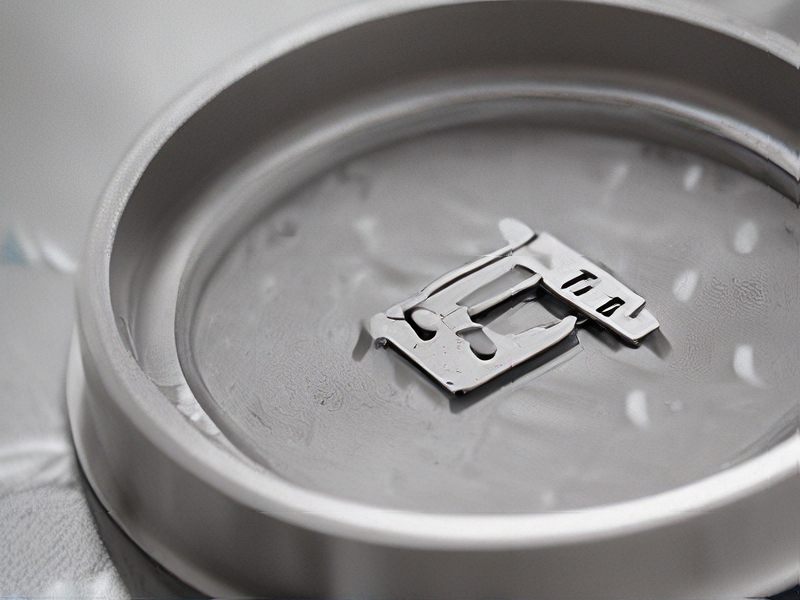
Tips for Procurement and Considerations when Purchasing from 304 or 316 stainless steel
## Stainless Steel Procurement: 304 vs. 316
Choosing between 304 and 316 stainless steel depends on your application’s needs.
304 Stainless Steel:
– Composition: Primarily iron, chromium, and nickel.
– Benefits: Cost-effective, excellent corrosion resistance, formable, weldable.
– Applications: General-purpose, food processing, kitchenware, construction.
316 Stainless Steel:
– Composition: Similar to 304, with added molybdenum.
– Benefits: Superior corrosion resistance, especially against saltwater and chlorides.
– Applications: Marine environments, chemical processing, medical instruments.
Procurement Tips:
– Specify grade: Ensure the steel meets the required standards (e.g., ASTM A276 for 304, ASTM A276 for 316).
– Consider form: Choose the appropriate form (sheets, bars, tubes, etc.) based on your application.
– Check certifications: Request material certifications to verify composition and quality.
– Source responsibly: Opt for suppliers with ethical sourcing practices and environmental standards.
Remember to consult with a qualified engineer or metallurgist for specialized applications or specific material requirements.
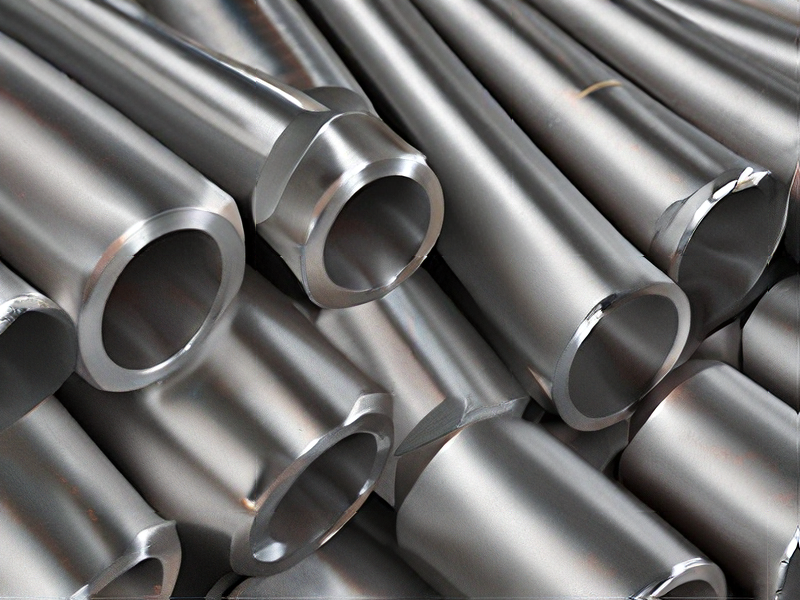
FAQs on Sourcing and Manufacturing from 304 or 316 stainless steel in China
Sourcing and manufacturing 304 or 316 stainless steel in China can be efficient and cost-effective, but it’s crucial to navigate the process strategically.
Sourcing:
* Identify Reputable Suppliers: Leverage online directories, trade shows, and industry connections to find certified suppliers with a proven track record.
* Request Samples and Certifications: Always request material samples and relevant certifications (e.g., ISO, ASTM) to verify quality and adherence to standards.
* Negotiate Pricing and Payment Terms: Compare quotes from multiple suppliers and negotiate favorable terms, considering factors like order volume and lead times.
Manufacturing:
* Choose the Right Manufacturer: Select a manufacturer specializing in stainless steel fabrication with expertise in your specific product requirements.
* Communicate Clearly: Provide detailed drawings, specifications, and quality standards to ensure accurate production.
* Quality Control: Implement rigorous quality control measures throughout the manufacturing process, including inspections at key stages.
Key Considerations:
* Corrosion Resistance: 316 stainless steel offers superior corrosion resistance compared to 304, often preferred in demanding environments.
* Lead Times: Manufacturing lead times can vary based on complexity, order size, and supplier capacity. Plan accordingly.
* Logistics and Shipping: Factor in transportation costs and ensure safe and timely delivery.
By following these guidelines, you can successfully source and manufacture high-quality 304 or 316 stainless steel products in China.
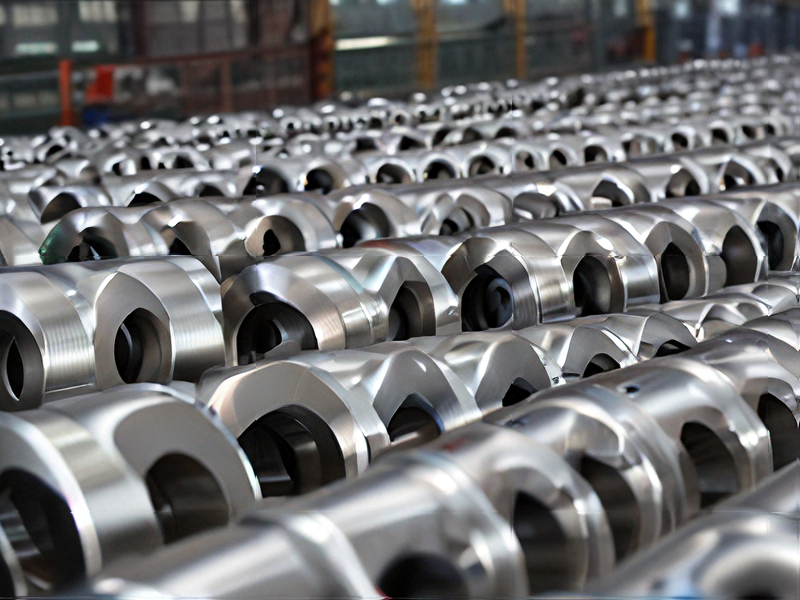