Technology and Applications of 304 stainless steel vs 316
304 and 316 stainless steels are both widely used due to their corrosion resistance and durability, but they differ in composition and applications.
304 stainless steel, primarily composed of iron, chromium, and nickel, offers good general corrosion resistance. It’s used extensively in food processing, construction, automotive parts, and household appliances. Its affordability and weldability make it a popular choice for these applications.
316 stainless steel, containing molybdenum in addition to the elements found in 304, boasts superior corrosion resistance, particularly against chloride-containing environments. This makes it ideal for marine applications, chemical processing, medical instruments, and pharmaceutical equipment.
While 304 is suitable for mild corrosive environments, 316 is necessary when facing highly corrosive conditions. 316’s added cost is justified by its enhanced performance in demanding situations.
Ultimately, the choice between 304 and 316 stainless steel depends on the specific application and the level of corrosion resistance required.
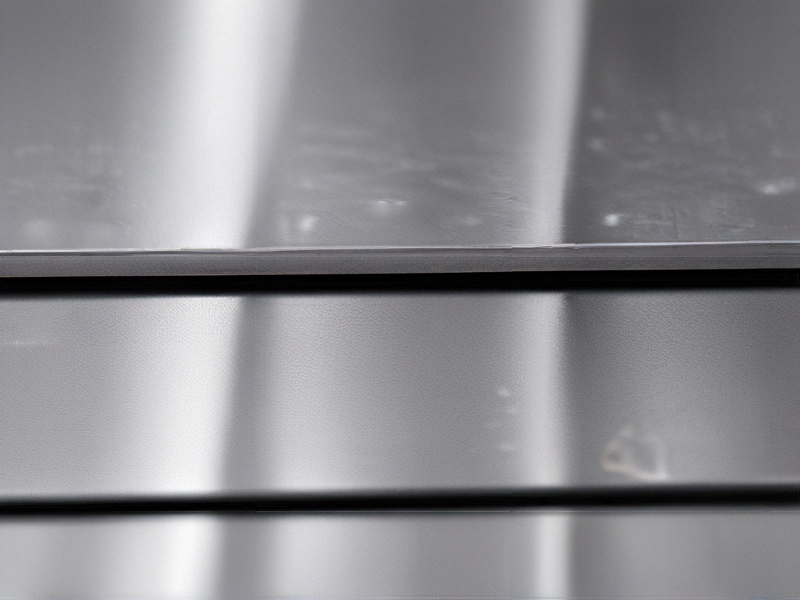
Quality Testing Methods for 304 stainless steel vs 316 and how to control quality
Quality testing methods for 304 and 316 stainless steel primarily focus on ensuring the materials meet their specified properties and standards. Here are the common methods and controls:
Testing Methods
1. Chemical Analysis:
– Spectroscopy: Used to confirm the composition of the stainless steel. Ensures the correct amounts of chromium, nickel, and molybdenum (especially important for 316) are present.
– X-ray Fluorescence (XRF): Non-destructive method to verify elemental composition.
2. Mechanical Testing:
– Tensile Test: Measures the material’s strength and ductility.
– Hardness Test: Determines the hardness and ensures it meets required standards.
3. Corrosion Resistance Testing:
– Salt Spray Test: Evaluates the corrosion resistance, especially critical for 316 due to its superior resistance to chloride environments.
– Pitting Resistance Test: Specifically checks for pitting corrosion which 316 resists better than 304.
4. Microstructural Analysis:
– Optical Microscopy: Examines the grain structure and phase distribution.
– Scanning Electron Microscopy (SEM): Provides detailed images to identify potential defects.
Quality Control
1. Standard Compliance:
– Ensure all batches conform to relevant standards (e.g., ASTM, ISO).
– Regular audits and certification checks.
2. Process Control:
– Maintain strict control over manufacturing processes to avoid contamination and ensure consistency.
– Implement Statistical Process Control (SPC) to monitor production quality in real-time.
3. Inspection and Testing:
– Conduct regular in-process inspections.
– Implement final inspection protocols before shipment.
4. Traceability:
– Maintain detailed records of each batch’s origin, processing history, and testing results.
– Use barcoding or RFID systems for tracking.
5. Training and Personnel:
– Ensure that staff are well-trained in quality control procedures and testing methods.
– Regularly update training programs to incorporate the latest standards and technologies.
These methods and controls help ensure that 304 and 316 stainless steels meet the desired quality standards and perform reliably in their intended applications.
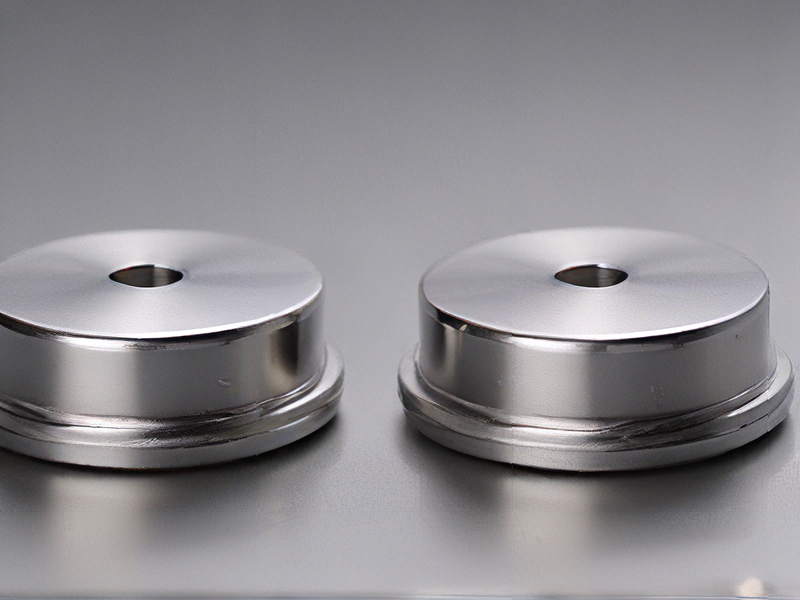
Tips for Procurement and Considerations when Purchasing from 304 stainless steel vs 316
When procuring stainless steel, understanding the differences between 304 and 316 grades is crucial. Here are some tips and considerations:
1. Corrosion Resistance:
– 304 Stainless Steel: Known for its good corrosion resistance, suitable for most general applications.
– 316 Stainless Steel: Contains molybdenum, providing enhanced resistance to chlorides and marine environments. Ideal for coastal and industrial applications.
2. Cost:
– 304 Stainless Steel: Generally less expensive than 316. It’s cost-effective for applications where extreme corrosion resistance is not a priority.
– 316 Stainless Steel: Higher cost due to added molybdenum but offers superior durability in harsh environments.
3. Mechanical Properties:
– Both grades have similar mechanical properties, but 316 tends to have slightly higher tensile strength and creep resistance at elevated temperatures.
4. Application Suitability:
– 304 Stainless Steel: Suitable for kitchen equipment, food processing, brewing, and interior architectural applications.
– 316 Stainless Steel: Preferred in chemical processing, marine environments, medical devices, and environments exposed to salts and acids.
5. Maintenance:
– 304 Stainless Steel: Requires regular cleaning to maintain its aesthetic appeal, especially in aggressive environments.
– 316 Stainless Steel: Lower maintenance due to its superior corrosion resistance.
6. Availability and Fabrication:
– Both grades are readily available and can be fabricated using standard techniques. However, 316 might be slightly harder to machine due to its toughness.
7. Certification and Standards:
– Ensure that the supplier provides proper certification and complies with international standards (e.g., ASTM, ISO).
8. Environmental Factors:
– Consider the specific environmental conditions the material will be exposed to. For example, high salinity or chemical exposure would favor 316 over 304.
By considering these factors, you can make an informed decision on whether 304 or 316 stainless steel is more appropriate for your specific needs, balancing cost with performance requirements.
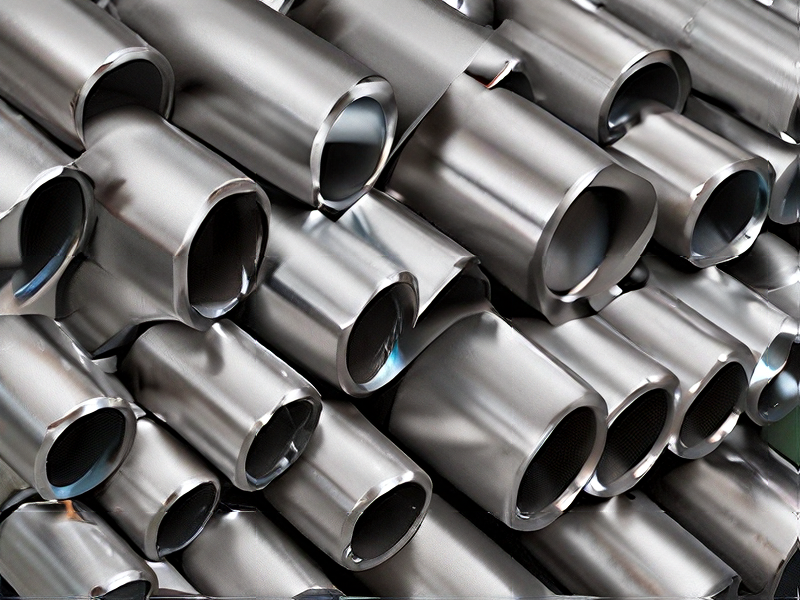
FAQs on Sourcing and Manufacturing from 304 stainless steel vs 316 in China
FAQs on Sourcing and Manufacturing 304 vs 316 Stainless Steel in China
1. What are the main differences between 304 and 316 stainless steel?
– 304 Stainless Steel: Contains 18% chromium and 8% nickel. It is resistant to oxidation and corrosion, making it suitable for a wide range of applications.
– 316 Stainless Steel: Contains 16% chromium, 10% nickel, and 2% molybdenum. The addition of molybdenum improves corrosion resistance, especially against chlorides and other industrial solvents.
2. Which one is more cost-effective?
– 304 Stainless Steel: Generally more affordable due to its lower nickel content.
– 316 Stainless Steel: More expensive because of the additional molybdenum and higher nickel content.
3. What are common applications for each type?
– 304 Stainless Steel: Used in kitchen equipment, chemical containers, automotive parts, and architectural applications.
– 316 Stainless Steel: Preferred for marine environments, pharmaceutical and food processing equipment, and chemical manufacturing.
4. How do I choose the right manufacturer in China?
– Experience: Look for manufacturers with extensive experience in producing stainless steel products.
– Certifications: Ensure the manufacturer has relevant certifications (ISO, ASTM).
– Quality Control: Check for robust quality control processes.
– References: Ask for references and inspect past work.
5. Are there specific challenges in sourcing stainless steel from China?
– Quality Assurance: Ensuring consistent quality can be challenging; always request samples.
– Communication: Language barriers and time zone differences may affect communication.
– Intellectual Property: Protect designs and specifications with clear contracts.
6. What are the typical lead times for manufacturing?
– Lead times can vary but typically range from 4 to 8 weeks, depending on the complexity of the order and the manufacturer’s capacity.
7. How can I ensure compliance with international standards?
– Inspections: Conduct third-party inspections.
– Specifications: Clearly define material specifications and standards in the contract.
– Testing: Require material testing reports to verify compliance.
Choosing between 304 and 316 stainless steel depends on the application requirements and budget considerations. Selecting a reputable manufacturer in China is crucial to ensuring product quality and compliance with international standards.
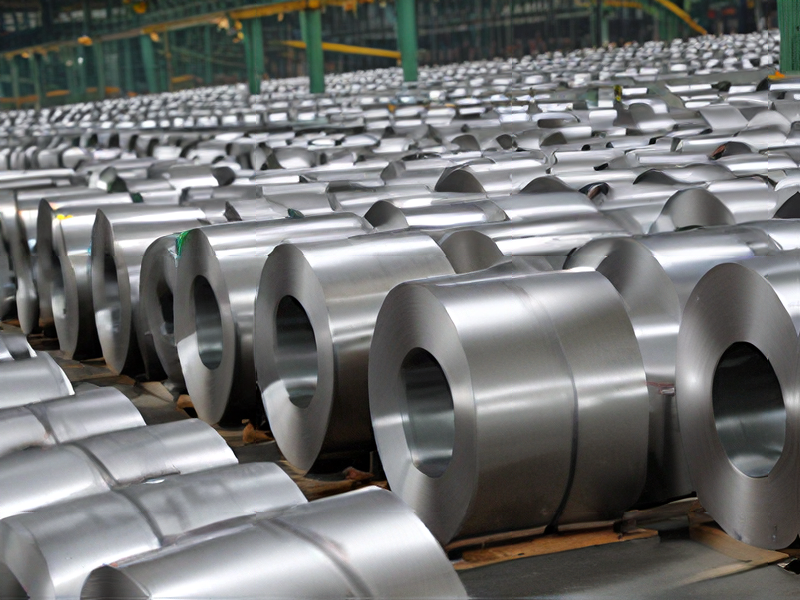