Technology and Applications of 304 vs 316 stainless steel
304 and 316 stainless steels are widely used in various industries due to their corrosion resistance and durability. Both are austenitic stainless steels, meaning they contain high levels of chromium and nickel, which contribute to their non-magnetic properties and good formability.
304 Stainless Steel
Composition:
– Chromium: 18-20%
– Nickel: 8-10.5%
Applications:
– Kitchen equipment (sinks, cutlery, cookware)
– Food processing equipment
– Chemical containers
– Architectural applications
Properties:
– Good corrosion resistance in mild environments
– High tensile strength
– Versatile and cost-effective
316 Stainless Steel
Composition:
– Chromium: 16-18%
– Nickel: 10-14%
– Molybdenum: 2-3%
Applications:
– Marine environments (boat fittings, coastal architectural elements)
– Medical devices (surgical instruments, implants)
– Pharmaceutical equipment
– Chemical processing and storage
Properties:
– Superior corrosion resistance, especially against chlorides and other industrial solvents
– High tensile strength and creep resistance at high temperatures
– More expensive due to higher nickel and molybdenum content
Comparison
– Corrosion Resistance: 316 offers better resistance to harsh environments, particularly chloride exposure, making it ideal for marine and chemical applications.
– Cost: 304 is more cost-effective and sufficient for many general-purpose applications where extreme corrosion resistance is not critical.
– Mechanical Properties: Both have similar mechanical properties, but 316 can withstand higher temperatures and more aggressive chemical conditions.
Conclusion
Choosing between 304 and 316 stainless steels depends on the specific environmental conditions and requirements of the application. For most standard uses, 304 is adequate and more economical. However, for harsher environments and higher corrosion resistance, 316 is the preferred choice despite its higher cost.
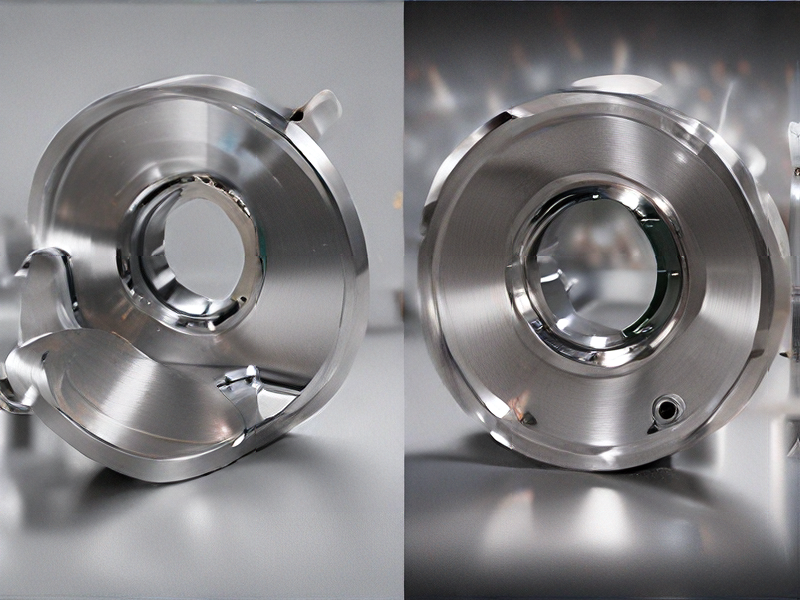
Quality Testing Methods for 304 vs 316 stainless steel and how to control quality
Quality testing for 304 and 316 stainless steel involves several methods to ensure their integrity, durability, and specific properties are met. Here’s a brief overview:
Testing Methods
1. Chemical Analysis:
– Spectroscopy (e.g., XRF, OES): Determines the precise composition of the alloy, ensuring it meets the specific grade requirements.
– Wet Chemistry: Traditional method for verifying elemental composition.
2. Mechanical Testing:
– Tensile Testing: Measures strength and ductility.
– Hardness Testing: Assesses resistance to deformation (Rockwell, Brinell).
3. Corrosion Testing:
– Salt Spray Test: Evaluates resistance to salt corrosion, crucial for 316 due to its marine applications.
– Pitting Resistance Test: Determines susceptibility to localized corrosion, important for differentiating 316 (better pitting resistance due to molybdenum content).
4. Microstructural Analysis:
– Metallography: Examines the grain structure and phase distribution using optical or electron microscopy.
– Ferrite Testing: Ensures the balance of austenitic and ferritic phases.
5. Non-Destructive Testing (NDT):
– Ultrasonic Testing: Detects internal flaws.
– Dye Penetrant Inspection: Reveals surface cracks and defects.
Quality Control
1. Standard Compliance:
– Ensure all materials meet standards like ASTM A240 for stainless steel plates, ASTM A276 for bars.
2. Batch Testing:
– Perform random sampling and testing of batches to verify consistency.
3. Traceability:
– Maintain thorough documentation and traceability of raw materials and processes.
4. Inspection Protocols:
– Implement regular inspection schedules and protocols, including incoming material inspection, in-process inspection, and final product inspection.
5. Supplier Quality Management:
– Work with certified suppliers and conduct periodic audits to ensure raw materials meet specifications.
6. Continuous Improvement:
– Utilize feedback loops and quality management systems (e.g., ISO 9001) to continuously improve processes and product quality.
By implementing these testing methods and quality control measures, manufacturers can ensure that both 304 and 316 stainless steels meet their required specifications and performance standards.

Tips for Procurement and Considerations when Purchasing from 304 vs 316 stainless steel
Choosing between 304 and 316 stainless steel for your procurement depends on the application’s specific needs.
304 Stainless Steel:
* Pros: Cost-effective, good general corrosion resistance, widely available.
* Cons: Susceptible to pitting and crevice corrosion in chloride-rich environments.
316 Stainless Steel:
* Pros: Superior corrosion resistance, including against chlorides, making it suitable for marine applications and harsh environments.
* Cons: More expensive than 304.
Procurement Tips:
* Clearly define your application: Identify the environment, potential corrosive agents, and required strength/durability.
* Consider cost vs. performance: 304 is economical for less demanding applications, while 316 offers superior protection for demanding environments.
* Specify the form: Choose the most appropriate form (sheet, plate, bar, pipe, etc.) based on your needs.
* Verify material certification: Ensure the supplier provides documentation verifying the steel grade and quality.
* Negotiate pricing and delivery: Obtain quotes from multiple suppliers and compare terms.
Remember, consulting with a materials engineer can provide tailored advice for your specific project.
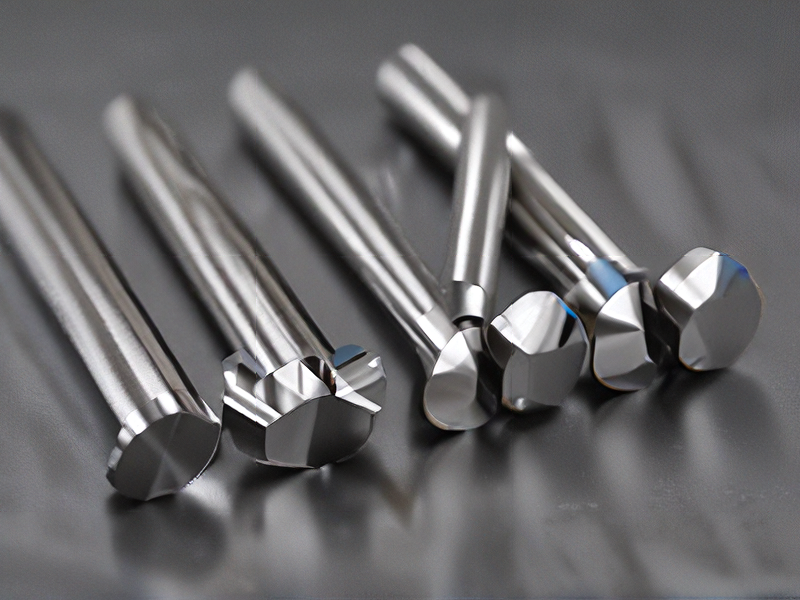
FAQs on Sourcing and Manufacturing from 304 vs 316 stainless steel in China
FAQs on Sourcing and Manufacturing from 304 vs 316 Stainless Steel in China
1. What are the key differences between 304 and 316 stainless steel?
– 304 Stainless Steel: Composed of 18% chromium and 8% nickel, it is cost-effective and widely used for general-purpose applications.
– 316 Stainless Steel: Contains 16% chromium, 10% nickel, and 2% molybdenum, offering superior corrosion resistance, especially against chlorides and acids.
2. Why choose 304 stainless steel?
– Affordability: 304 is less expensive than 316.
– Versatility: Suitable for a wide range of applications including kitchen equipment, storage tanks, and architecture.
3. Why choose 316 stainless steel?
– Corrosion Resistance: Ideal for marine environments, chemical processing, and medical devices.
– Durability: Better performance in harsh environments due to added molybdenum.
4. Is there a significant price difference between 304 and 316 stainless steel in China?
– Yes, 316 stainless steel is typically 20-30% more expensive than 304 due to the higher cost of raw materials.
5. How does sourcing from China affect quality and cost?
– Quality: Chinese manufacturers can produce high-quality stainless steel, but it’s crucial to verify certifications and perform quality checks.
– Cost: Lower labor and production costs in China can result in significant savings.
6. What should be considered when choosing a Chinese supplier?
– Certification: Ensure the supplier is ISO certified.
– Reputation: Check references and reviews.
– Capacity: Confirm the supplier can meet your volume and lead time requirements.
7. How does the choice between 304 and 316 affect manufacturing processes?
– Machinability: Both grades are similar, but 316 may require slower speeds and more powerful equipment due to its hardness.
– Welding: Both are weldable, but 316 requires more careful handling to avoid contamination and corrosion.
8. Are there environmental considerations?
– Both 304 and 316 stainless steels are recyclable, but the energy consumption and emissions from production should be considered when choosing a supplier.
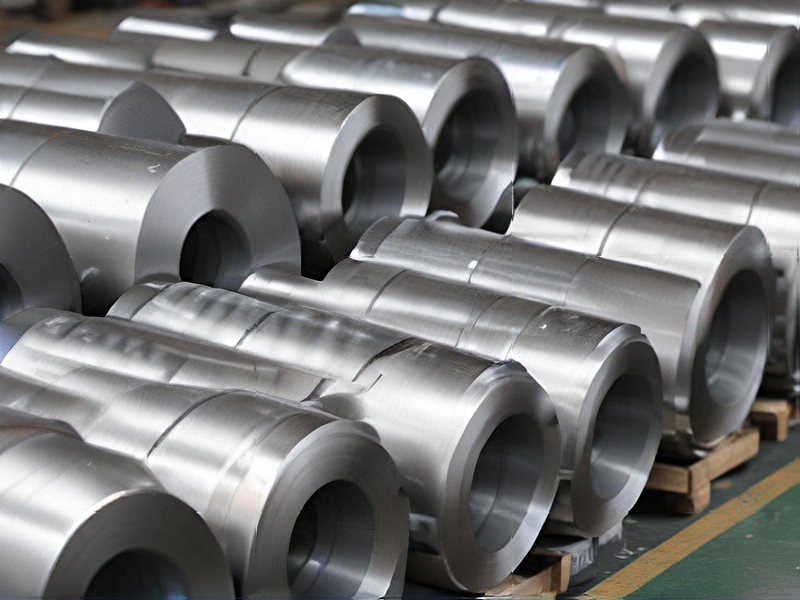