Technology and Applications of 3d metal printed
3D metal printing, also known as additive manufacturing, involves creating three-dimensional objects from metal powders through layer-by-layer printing. This technology leverages techniques like Selective Laser Melting (SLM) and Electron Beam Melting (EBM), which use lasers or electron beams to fuse particles together. The benefits of 3D metal printing include enhanced design freedom, reduced material waste, and the ability to produce complex geometries that are difficult or impossible to achieve with traditional manufacturing methods.
Applications of 3D metal printing span various industries. In aerospace, components like turbine blades and structural parts are produced to reduce weight while maintaining strength. The automotive industry uses this technology to create lightweight prototypes and parts, often optimizing designs for performance and fuel efficiency. Medical applications include custom implants and surgical tools, tailored to individual patient anatomy, improving patient outcomes.
Moreover, 3D metal printing is increasingly used in oil and gas, where it can produce durable, heat-resistant parts for harsh environments, as well as in tooling and molds, significantly speeding up production processes. The technology also facilitates rapid prototyping, allowing companies to iterate designs quickly, reducing time-to-market.
Despite its advantages, challenges such as high costs, limited material availability, and post-processing requirements remain. Nevertheless, ongoing advancements in materials and printing technologies promise to expand the scope and efficiency of 3D metal printing, making it a vital player in the future of manufacturing.
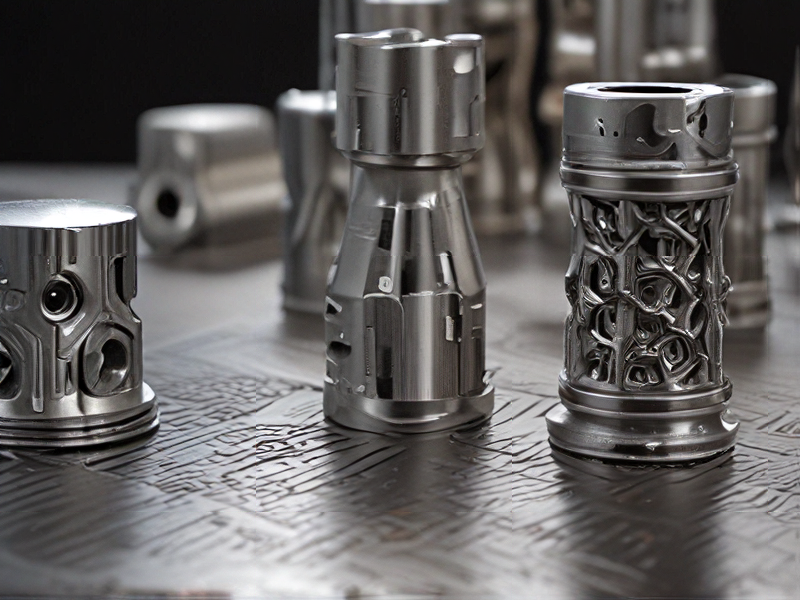
Quality Testing Methods for 3d metal printed and how to control quality
Quality testing of 3D metal printed parts is critical to ensure structural integrity, performance, and reliability. Here are key methods and practices for controlling quality:
1. Visual Inspection: Initial checks involve examining the surface finish, geometry, and any visible defects such as cracks or irregularities. This can be done with the naked eye or through magnification.
2. Dimensional Measurements: Utilize coordinate measuring machines (CMM) or laser scanners to verify that dimensions conform to CAD specifications. This helps in identifying deviations caused during the printing process.
3. Non-Destructive Testing (NDT): Techniques like ultrasonic testing, X-ray, and magnetic particle inspection are used to detect internal defects without damaging the part. These methods are vital to assessing the structural integrity of the component.
4. Mechanical Testing: Conduct tensile, compression, and fatigue tests to evaluate the mechanical properties of the printed parts. This helps in understanding how the material behaves under stress.
5. Microstructural Analysis: Use techniques like scanning electron microscopy (SEM) or optical microscopy to examine the microstructure of the printed metal. This analysis provides insights into grain size, phase distribution, and any potential defects at the microscopic level.
6. Process Control: Employ in-process monitoring systems that track temperature, laser power, and material flow during printing. Implementing real-time data analytics can help detect anomalies and adjust parameters to ensure consistency.
7. Post-Processing Inspection: After finishing processes (like machining or heat treatment), perform additional inspections to ensure that the final part meets design specifications and performance standards.
By combining these methods and establishing a robust quality management system, manufacturers can significantly enhance the reliability and performance of 3D metal printed components.
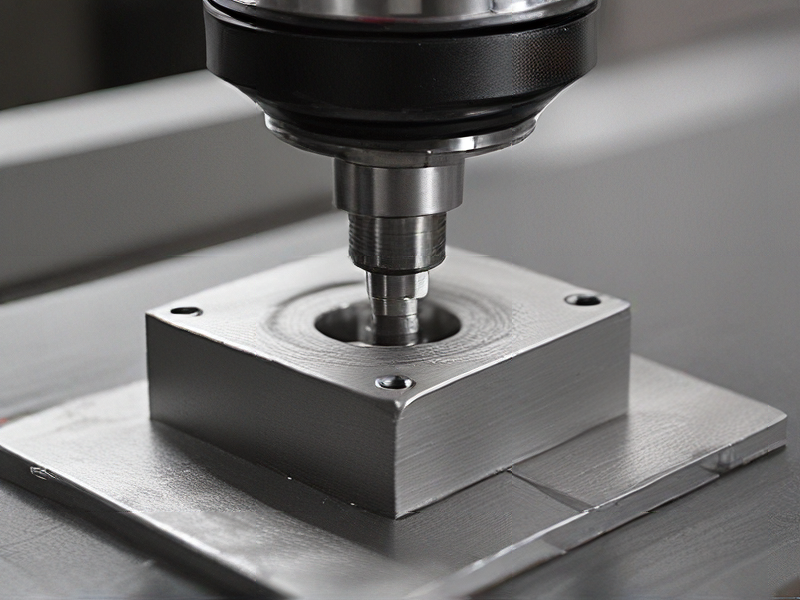
Tips for Procurement and Considerations when Purchasing from 3d metal printed
When procuring 3D metal printed parts, it’s essential to consider several factors to ensure quality, cost-effectiveness, and timely delivery.
1. Material Selection: Understand the different metals available (e.g., titanium, stainless steel, aluminum) and their mechanical properties to ensure compatibility with your application.
2. Supplier Expertise: Choose suppliers with proven expertise in metal 3D printing. Evaluate their experience, certifications, and past projects to ensure they meet industry standards.
3. Design Requirements: Collaborate closely with your supplier during the design phase. Utilize design optimization specific to additive manufacturing (AM) to enhance part performance and reduce material usage.
4. Quality Assurance: Investigate the supplier’s quality control processes. Ensure they utilize advanced inspection technologies (like CT scanning) to verify part integrity and precision.
5. Post-Processing: Understand the post-processing requirements (e.g., heat treatment, surface finishing) and how they impact lead time and cost. Some applications may require additional treatments to achieve desired specifications.
6. Cost Analysis: Analyze total cost considerations, not just the initial part price. Factor in material costs, production speed, post-processing, and any custom tooling or fixtures needed.
7. Scalability: Assess the supplier’s capability to scale production if demand increases. This includes their ability to maintain quality across multiple runs.
8. Lead Time: Establish clear timelines for production and delivery. Ensure the supplier can meet your project schedules without compromising quality.
9. Intellectual Property Considerations: If the design is proprietary, ensure that you have a clear agreement regarding intellectual property rights and confidentiality.
By taking these factors into account, you can make informed procurement decisions that align with your project requirements and contribute to successful outcomes in 3D metal printing.
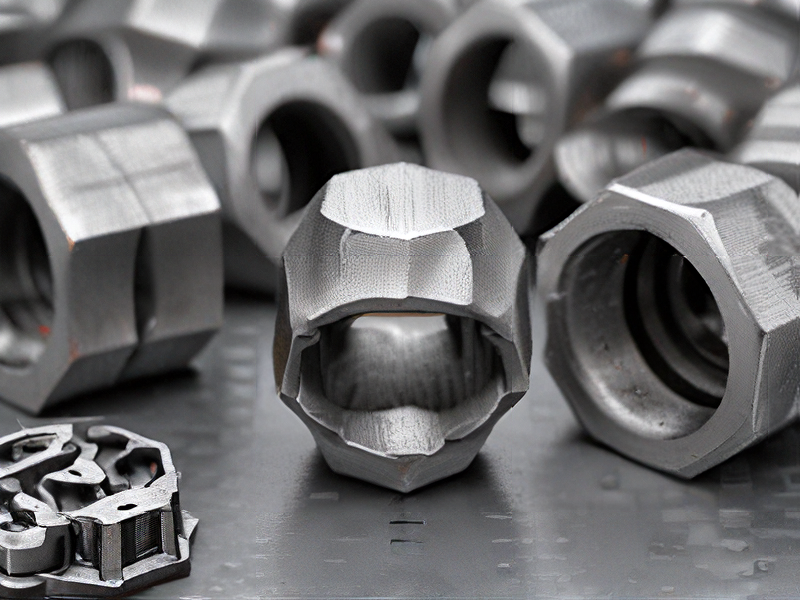
FAQs on Sourcing and Manufacturing from 3d metal printed in China
FAQs on Sourcing and Manufacturing 3D Metal Printing in China
1. What is 3D metal printing?
3D metal printing is an additive manufacturing process that creates objects layer by layer from metal powder. It allows for complex geometries that traditional methods cannot achieve.
2. Why consider China for 3D metal printing?
China offers advanced technology, skilled labor, competitive pricing, and a well-established supply chain for metal printing and related materials.
3. What types of materials are commonly used?
Common materials include stainless steel, titanium, aluminum alloys, and cobalt-chromium, each suited for different applications based on strength and thermal resistance.
4. What industries benefit from 3D metal printing?
Industries like aerospace, automotive, healthcare, and tooling benefit significantly due to the ability to create lightweight, strong components tailored to specific needs.
5. How do I ensure quality in manufacturing?
Choose vendors with ISO certifications and experience in 3D metal printing. Request samples and perform inspections to verify material properties and dimensional accuracy.
6. What are the lead times for production?
Lead times vary but generally range from a few days to several weeks depending on the complexity of the part and production capacity.
7. Are there export regulations I should be aware of?
Yes, ensure compliance with both U.S. and Chinese export regulations, especially if your parts are used in sensitive industries or government contracts.
8. What is the cost structure?
Cost involves material selection, production time, post-processing, and shipping. Request quotes from multiple suppliers to understand market rates.
9. Can I prototype before mass production?
Absolutely! Prototyping is a key advantage of 3D printing, allowing you to test designs before committing to larger production runs.
For more detailed inquiries, consider consulting with sourcing experts familiar with the Chinese market.
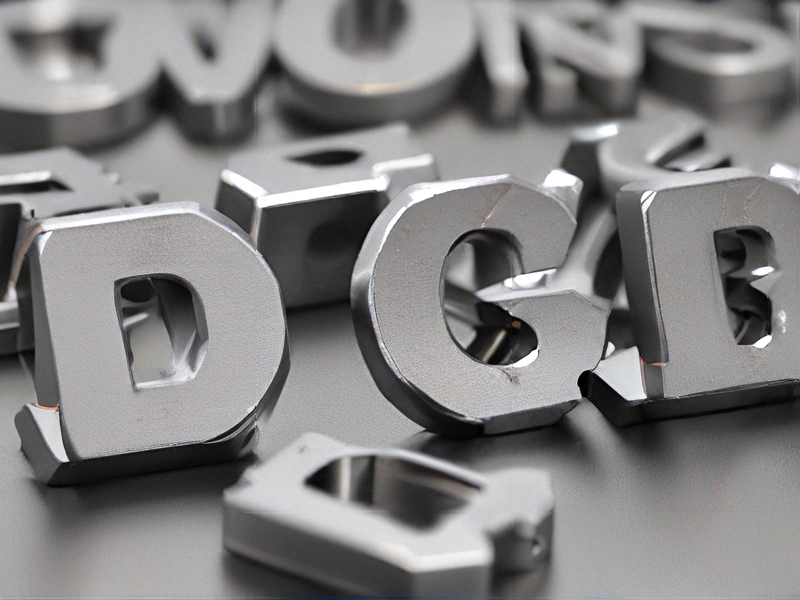