Technology and Applications of 3d metal printing
3D metal printing, also known as additive manufacturing, is revolutionizing various industries by enabling the production of complex geometries that traditional methods struggle to achieve. This technology utilizes techniques like Direct Metal Laser Sintering (DMLS) and Electron Beam Melting (EBM), where metal powders are fused layer by layer using high-energy lasers or electron beams.
One major application of 3D metal printing is in aerospace, where lightweight, intricately designed components can significantly reduce the overall weight of aircraft, improving fuel efficiency. For instance, companies like Boeing and Airbus leverage this technology to create parts for engines and structural components.
Another critical sector is healthcare, where personalized implants and prosthetics can be produced to fit individual patients’ anatomy. This customization leads to better surgical outcomes and increased patient comfort.
In automotive manufacturing, 3D printing facilitates rapid prototyping and the production of complex parts that enhance vehicle performance. Manufacturers can quickly iterate designs, reducing time to market.
Moreover, the tool and die industry benefits from 3D printed tooling, which can be produced faster and at a lower cost than traditional methods, allowing for more flexible and efficient production processes.
The technology also contributes to sustainability by minimizing waste, as materials are added only where needed. Furthermore, it allows for the recycling of metal powders, reducing overall material consumption.
As 3D metal printing continues to evolve, its applications are expanding in fields like defense, electronics, and architecture, highlighting its potential to transform manufacturing and product design. The convergence of design freedom and material innovation positions 3D metal printing at the forefront of future industrial practices.
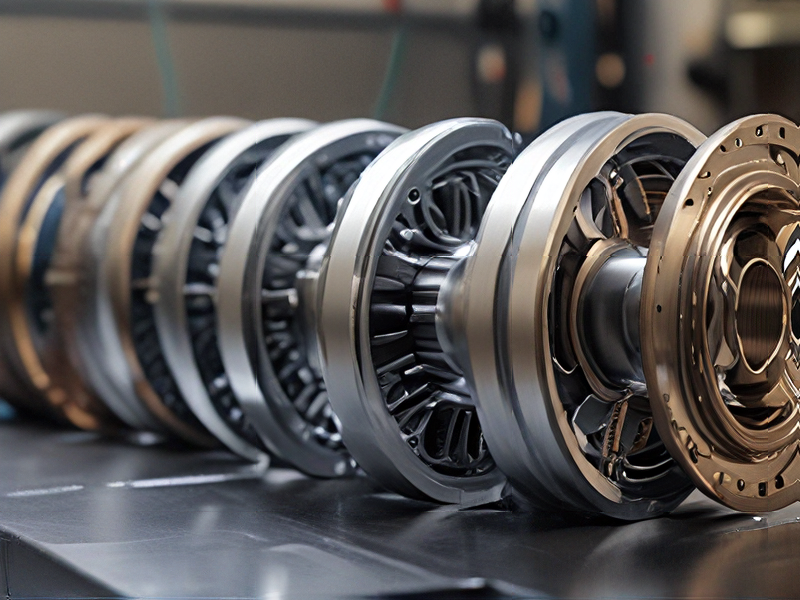
Quality Testing Methods for 3d metal printing and how to control quality
Quality testing of 3D metal printing involves several methods to ensure the integrity, precision, and performance of printed components. Key testing methods include:
1. Visual Inspection: Initial checks for surface defects, dimensional accuracy, and adherence to design specifications.
2. Non-Destructive Testing (NDT): Techniques like ultrasonic testing, X-ray computed tomography, and magnetic particle testing identify internal and surface defects without damaging the part.
3. Mechanical Testing: Assessing tensile strength, fatigue resistance, and hardness through standardized tests (e.g., tensile tests, impact tests) to evaluate material properties.
4. Microstructural Analysis: Using techniques like scanning electron microscopy (SEM) and metallography to examine the microstructure, identify grain size, and locate defects or inconsistencies in the material.
5. Thermal Analysis: Analyzing thermal properties and behaviors during printing processes, such as thermal cycling tests to understand performance under varying temperatures.
To control quality, consider the following practices:
1. Standardized Processes: Implement industry standards (e.g., ISO 9013 for laser metal powder bed fusion) to establish consistent quality benchmarks.
2. Process Monitoring: Utilize real-time monitoring techniques (e.g., laser power, scanning speed) to adjust parameters dynamically during printing based on feedback.
3. Post-Processing Procedures: Apply procedures such as heat treatment, machining, or surface finishing to eliminate residual stresses and improve final part characteristics.
4. Certification and Traceability: Maintain a detailed record of material certificates, process parameters, and quality tests to ensure traceability and compliance.
By integrating these testing methods and control measures, organizations can significantly enhance the reliability and performance of 3D-printed metal components.
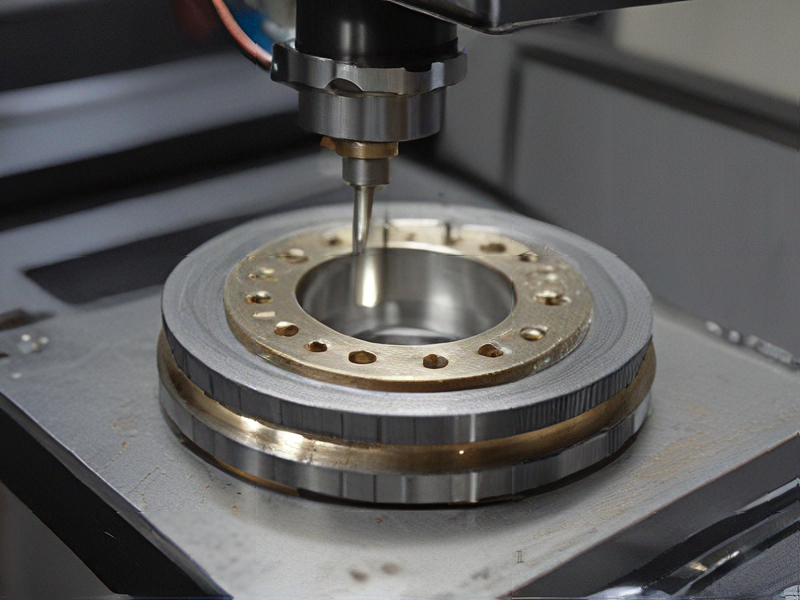
Tips for Procurement and Considerations when Purchasing from 3d metal printing
When procuring 3D metal printing services, several key considerations can enhance your purchasing decisions:
1. Material Selection: Understand the range of metals available (e.g., titanium, aluminum, stainless steel) and choose one that meets your application’s mechanical and thermal properties.
2. Technology Type: Familiarize yourself with different 3D printing technologies, such as Direct Metal Laser Sintering (DMLS) or Electron Beam Melting (EBM). Each has unique advantages depending on your project needs.
3. Quality Standards: Ensure that the service provider adheres to industry standards (ISO 9001, AS9100) for quality assurance and possesses certifications relevant to your sector, such as aerospace or medical.
4. Design Constraints: Discuss your design thoroughly with the provider, considering manufacturability and limitations inherent to 3D printing processes. They can offer insights to optimize your design for better results.
5. Lead Time and Scalability: Assess the provider’s capabilities concerning production timelines and the ability to scale orders, especially if you anticipate increasing demands.
6. Cost Analysis: Balance the cost of materials, processing, and post-processing against the overall value delivered. Consider the total lifecycle cost, not just the initial quote.
7. Post-Processing Services: Investigate available post-processing options like heat treatment, surface finishing, or machining, which can significantly affect the properties and appearance of the final product.
8. Supplier Reputation: Research the supplier’s track record by reviewing case studies, customer testimonials, and portfolios. A reliable partner can enhance project success.
By focusing on these criteria, you will ensure that your procurement process is efficient and aligns with your production goals.
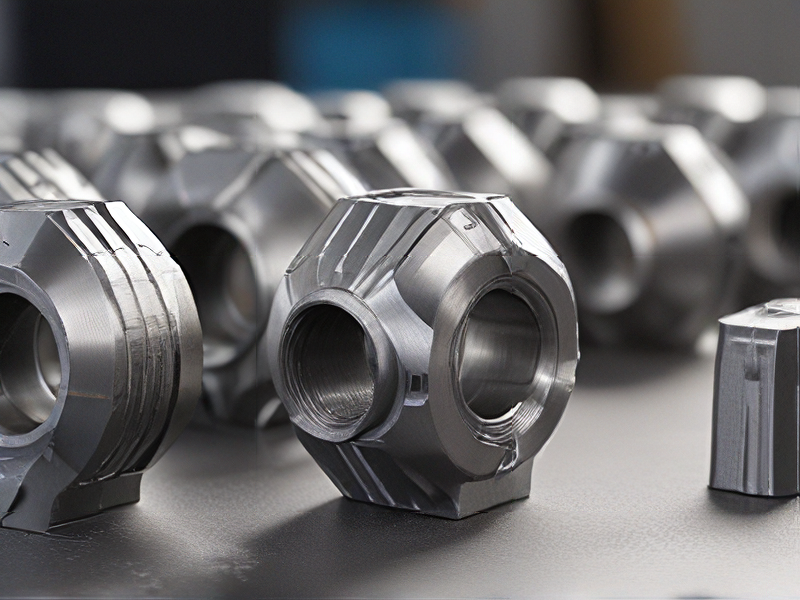
FAQs on Sourcing and Manufacturing from 3d metal printing in China
FAQs on Sourcing and Manufacturing with 3D Metal Printing in China
Q1: What advantages does 3D metal printing offer?
A: 3D metal printing allows for complex geometries, reduced material waste, faster prototyping, and customization. It’s ideal for industries like aerospace, automotive, and healthcare.
Q2: How do I choose a reliable supplier in China?
A: Look for suppliers with ISO certifications, a strong portfolio, positive customer reviews, and years of experience. Verify their manufacturing capabilities through audits or visits if possible.
Q3: What materials can be used in 3D metal printing?
A: Common materials include titanium, aluminum, stainless steel, and cobalt-chromium alloys. The choice of material depends on the application and required properties.
Q4: How do I ensure quality control?
A: Establish clear quality standards, conduct regular inspections, and request certification documentation. Utilizing third-party quality assurance services can also be beneficial.
Q5: What are the typical lead times for production?
A: Lead times vary based on complexity and order size, but you can generally expect anywhere from a few weeks to a couple of months for production and delivery.
Q6: How can I reduce costs?
A: Optimize designs for 3D printing, order larger quantities, and choose local suppliers to minimize shipping expenses. Additionally, consider the total cost of ownership, including post-processing and finishing.
Q7: Are there any regulatory concerns?
A: Ensure compliance with both local and international regulations, especially for industries like aerospace and medical, where standards are stringent.
Q8: What post-processing options are available?
A: Common post-processing methods include heat treatment, surface finishing, and machining to meet specific tolerances and surface quality requirements.
For further inquiries, consider consulting industry experts or engineering professionals.
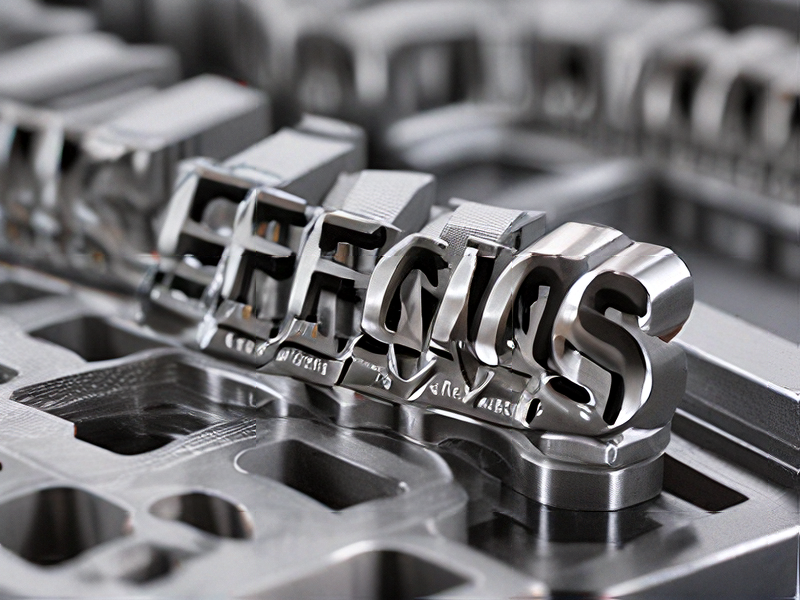