Technology and Applications of 3d printer with metal
3D printing with metal, also known as metal additive manufacturing, utilizes advanced technologies to create complex metal parts layer by layer. This process enables the production of intricate geometries that traditional manufacturing methods often struggle to achieve.
Key technologies in metal 3D printing include Direct Metal Laser Sintering (DMLS) and Electron Beam Melting (EBM). DMLS employs a high-powered laser to fuse metallic powders, while EBM uses an electron beam in a vacuum environment. Both processes are capable of producing high-strength, lightweight components used in aerospace, automotive, and medical industries.
The applications of metal 3D printing are vast. In aerospace, it enables the production of lightweight components that enhance fuel efficiency and performance. Companies like Boeing and GE Aviation have integrated metal 3D printed parts into their aircraft to reduce weight and improve functionality. In the medical field, custom implants and prosthetics are created to match the specific anatomy of patients, improving comfort and effectiveness.
Moreover, metal 3D printing facilitates rapid prototyping, allowing for quick iterations in design, ultimately speeding up time-to-market. This technology also supports on-demand production, reducing inventory costs and material waste.
As the technology evolves, advancements in materials and printing processes are expected to broaden the scope of applications and improve cost efficiency. Thus, metal 3D printing represents a significant leap forward in manufacturing, poised to reshape industries by combining flexibility, efficiency, and precision.
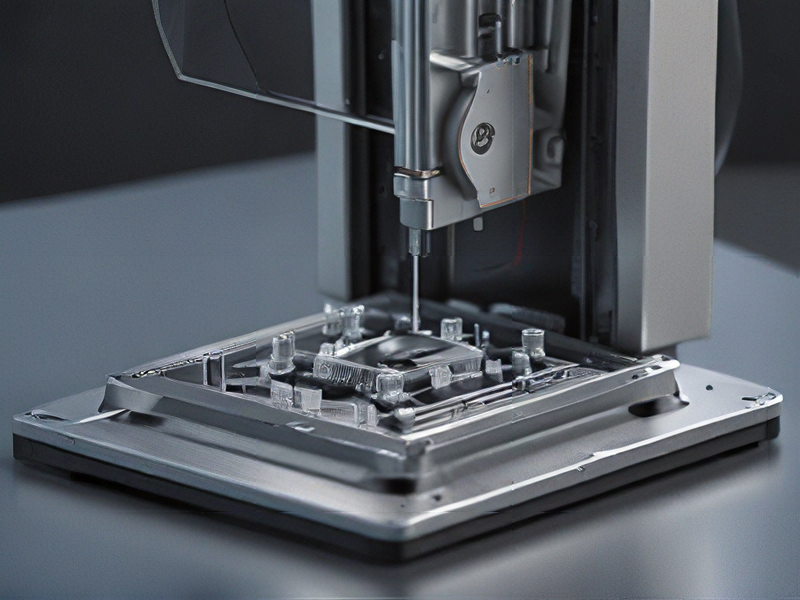
Quality Testing Methods for 3d printer with metal and how to control quality
Quality testing for 3D-printed metal parts is crucial for ensuring mechanical integrity and performance. Here are key methods and controls for maintaining quality:
1. Material Verification: Use spectral analysis (e.g., X-ray fluorescence) to confirm the alloy composition before printing. This ensures that the material meets required specifications.
2. In-Process Monitoring: Utilize real-time monitoring systems to track temperature, laser power, and feed rate during the additive manufacturing process. This helps in identifying deviations that could lead to defects.
3. Dimensional Inspection: Post-printing, employ coordinate measuring machines (CMM) or laser scanners to verify the geometric accuracy of the part against CAD specifications. Tolerances should be established based on the application requirements.
4. Non-Destructive Testing (NDT): Implement methods like ultrasonic testing, X-ray imaging, and dye penetrant inspection to identify internal defects such as porosity or cracks without damaging the part.
5. Mechanical Testing: Conduct tensile, fatigue, and impact tests on samples to assess mechanical properties. This provides insight into how the part will perform under operational conditions.
6. Microstructural Analysis: Use scanning electron microscopy (SEM) or metallography to evaluate grain structure and porosity. This helps in understanding the effects of processing parameters on material properties.
7. Post-Processing Controls: Implement quality controls during post-processing steps like heat treatment or surface finishing, which can affect the final properties of the part.
By integrating these methods into the production workflow, manufacturers can ensure that 3D-printed metal components consistently meet quality and performance standards. Regular audits and feedback loops enhance process reliability and material performance over time.
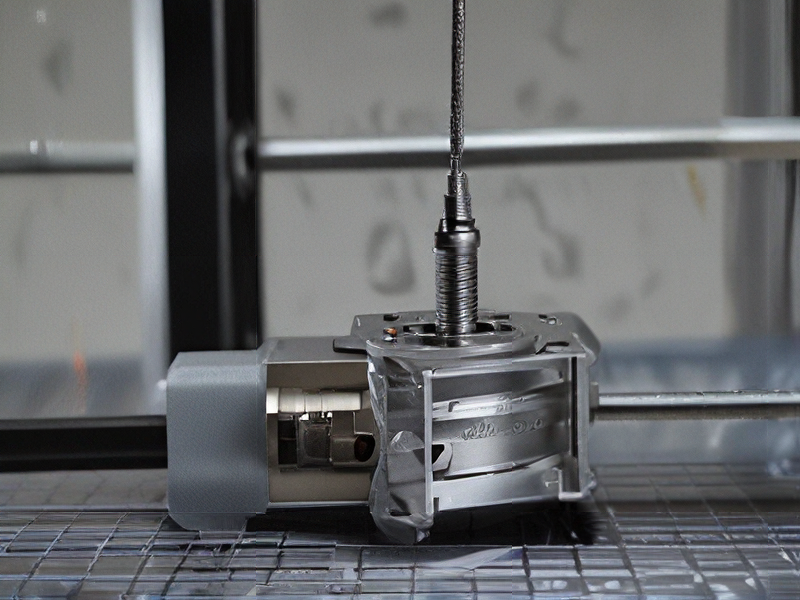
Tips for Procurement and Considerations when Purchasing from 3d printer with metal
When purchasing a metal 3D printer, consider the following tips and considerations:
1. Technology Type: Understand the different metal printing technologies available, such as Selective Laser Melting (SLM), Electron Beam Melting (EBM), and Binder Jetting. Each has distinct capabilities and applications.
2. Material Compatibility: Verify the range of metals the printer supports, such as titanium, aluminum, and stainless steel. Ensure it aligns with your project requirements.
3. Build Size: Assess the maximum build dimensions to ensure the printer can accommodate your largest anticipated parts.
4. Print Speed: Evaluate the machine’s speed and throughput. Faster printing can improve productivity, but may affect part quality.
5. Post-Processing Needs: Consider the finishing processes required after printing, such as heat treatment or machining, and whether the printer’s output meets your standards.
6. Software and Control: Check the ease of use of the included software for design, slicing, and monitoring. Robust software is vital for smooth operation.
7. Supplier Support: Research the manufacturer’s reputation for customer support, including training, maintenance, and troubleshooting assistance, which is crucial for successful operation.
8. Cost of Ownership: Beyond initial purchase price, factor in operating costs, maintenance, material expenses, and potential part failures.
9. Applications and Industry: Ensure that the printer is suitable for your specific applications (e.g., aerospace, automotive, medical) and adheres to industry standards.
10. User Feedback and Reviews: Look for reviews or testimonials from existing users to gain insight into performance and reliability.
Taking these considerations into account will lead to a more informed purchasing decision, optimizing your investment in metal 3D printing technology.
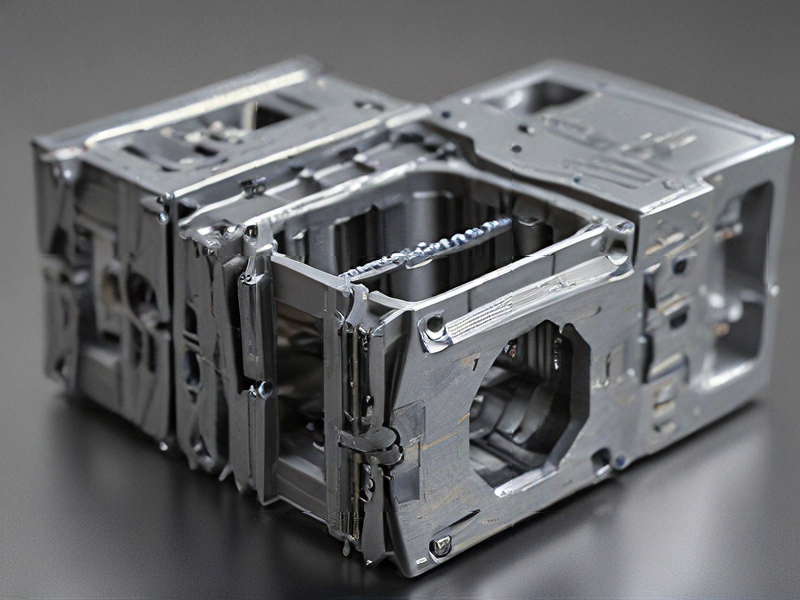
FAQs on Sourcing and Manufacturing from 3d printer with metal in China
FAQs on Sourcing and Manufacturing from 3D Printers with Metal in China
1. What types of metal can be utilized in 3D printing in China?
Common metals include titanium, stainless steel, aluminum, and cobalt-chromium. The choice of metal depends on the intended application and mechanical properties required.
2. What industries benefit from metal 3D printing in China?
Industries such as aerospace, automotive, medical, and tooling are the primary beneficiaries due to the need for lightweight, high-strength components and complex geometries.
3. How does the quality control process work?
Reputable manufacturers employ rigorous quality control measures, including regular inspections, testing of material properties, and adherence to industry standards like ISO and ASTM.
4. What are the lead times for 3D printed metal parts?
Lead times vary based on complexity and quantities but typically range from a few days to several weeks. Advanced planning and clear communication with the manufacturer can help streamline the process.
5. How do I find a reliable manufacturer in China?
Research online platforms like Alibaba or Global Sources, and consider attending industry trade shows. Always check reviews, request samples, and seek manufacturers with certifications.
6. What cost factors should I consider?
Costs can be influenced by material type, design complexity, post-processing needs, and quantity ordered. It’s essential to get detailed quotes and consider all aspects of production.
7. Are there legal considerations for sourcing from China?
Ensure compliance with export regulations and intellectual property rights. Consulting with legal experts may be advisable to protect your designs and technology.
8. How can I ensure my designs are optimized for 3D printing?
Engage with your manufacturer early in the design phase. They can provide insights into optimization for printability and material usage.
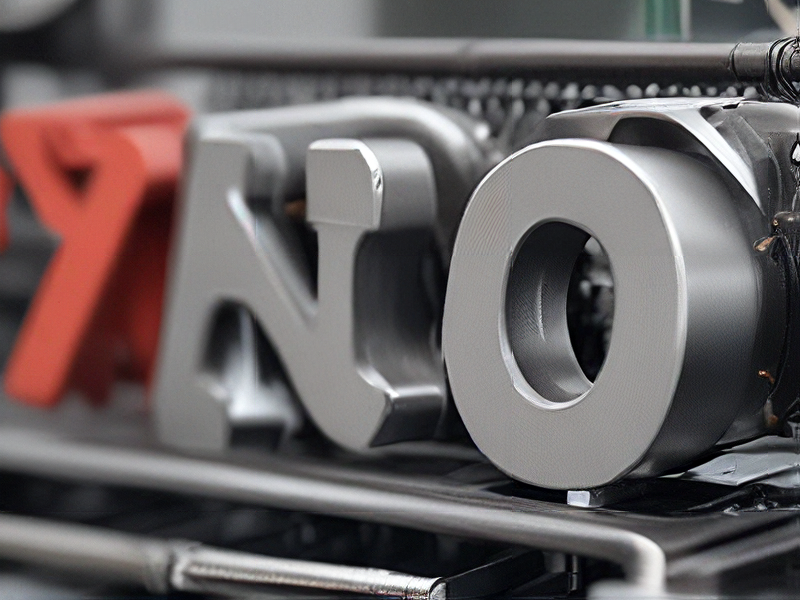