Technology and Applications of 3d printers metal
3D printing, or additive manufacturing, has revolutionized various industries by allowing for the precise creation of complex geometries and customized components. Metal 3D printing, particularly, utilizes techniques such as Selective Laser Melting (SLM), Electron Beam Melting (EBM), and Direct Metal Laser Sintering (DMLS).
These technologies involve the layer-by-layer fusion of metal powder using high-energy lasers or electron beams, resulting in dense and high-quality metal parts. SLM and DMLS are popular for producing intricate designs that are often impossible to achieve with traditional machining methods. EBM, utilizing an electron beam, is particularly effective for high-temperature applications and alloys like titanium.
Applications of metal 3D printing span diverse fields, including aerospace, automotive, medical, and tooling. In aerospace, it enables lightweight structures such as brackets and supports, reducing fuel consumption. The automotive industry benefits from rapid prototyping and the creation of customized components that improve performance. In medicine, custom implants and surgical instruments can be produced, tailored to individual patient needs.
Challenges in metal 3D printing include the high costs of machinery and materials, along with post-processing requirements such as heat treatment and machining to achieve desired mechanical properties and surface finishes. Moreover, ensuring consistency and quality in production remains critical.
Despite these challenges, the future of metal 3D printing looks promising, with ongoing advancements in technology and materials, making it increasingly viable for widespread industrial use. As innovations continue, metal 3D printing is likely to play a pivotal role in shaping the future of manufacturing.
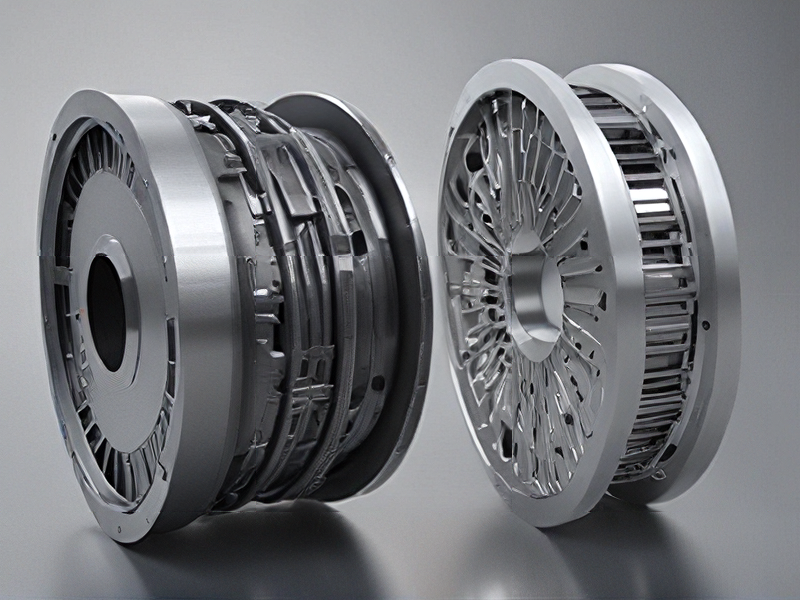
Quality Testing Methods for 3d printers metal and how to control quality
Quality testing for metal 3D printing is crucial to ensure the integrity, performance, and safety of printed components. Key methods and controls include:
1. Visual Inspection: Before and after printing, visually inspect parts for surface defects, layer adhesion issues, or anomalies. This initial check helps identify obvious defects.
2. Dimensional Accuracy: Use calibrated measuring tools (calipers, CMMs) to verify that printed parts meet specified geometric tolerances. Regular calibration of measurement tools is essential for consistent results.
3. Density and Porosity Analysis: Employ techniques such as Archimedes’ principle or X-ray computed tomography to evaluate density and identify any internal voids or porosity, which can affect mechanical properties.
4. Mechanical Testing: Conduct tensile, compression, and fatigue tests to assess strength, ductility, and overall mechanical performance. ASTM standards should guide these tests.
5. Thermal Analysis: Use Differential Scanning Calorimetry (DSC) or Thermogravimetric Analysis (TGA) to study thermal properties. This can provide insights into phase changes, which are critical for materials like titanium and aluminum alloys.
6. Microstructural Examination: Perform optical and electron microscopy to analyze grain structure and identify defects at the micro-level. This is vital for understanding material behavior under load.
7. Post-Processing Quality Control: Implement quality checks after processes such as heat treatment, machining, or surface finishing. These steps can significantly impact final part properties.
8. Process Monitoring: Use in-situ monitoring technologies (like laser triangulation or infrared cameras) to track the printing process in real time, enabling immediate adjustments to maintain quality.
By integrating these methods into a comprehensive quality management system, manufacturers can significantly enhance the reliability and performance of metal 3D-printed parts. Regular audits and adherence to industry standards further solidify quality control practices.
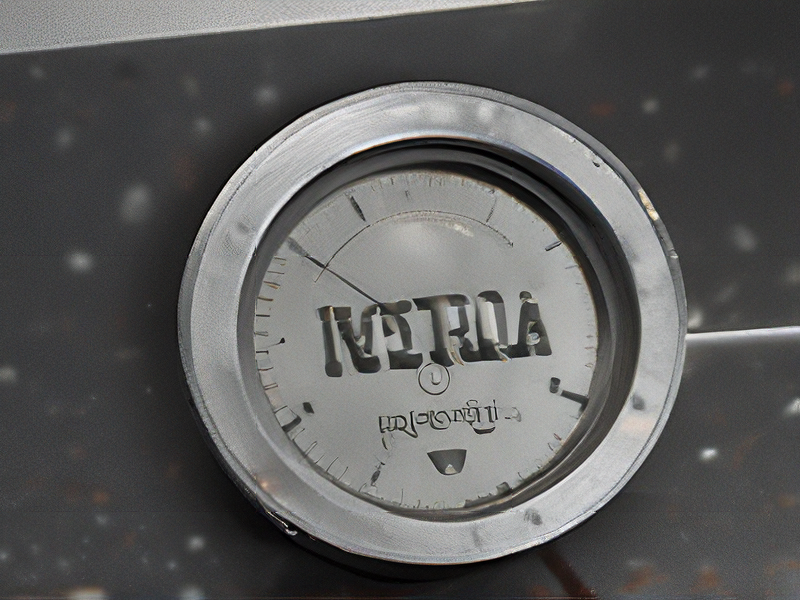
Tips for Procurement and Considerations when Purchasing from 3d printers metal
When procuring metal 3D printers, several key tips and considerations can help ensure you make an informed decision:
1. Identify Your Needs: Clearly define your application requirements, including materials, dimensions, and specific properties needed for your end products. Understand the volume of production and whether you need a machine for prototyping or production-scale manufacturing.
2. Material Compatibility: Investigate the types of metals compatible with the printer, such as titanium, steel, or aluminum. Ensure the printer can meet your requirements for mechanical properties, corrosion resistance, and heat treatment capabilities.
3. Technology Type: Different 3D printing technologies (e.g., Powder Bed Fusion, Direct Energy Deposition) have unique advantages. Evaluate which technology aligns best with your operational needs and budget.
4. Vendor Reputation: Research manufacturers and their track records for reliability, support, and service. Look for user testimonials and case studies to gauge satisfaction and performance.
5. Cost of Ownership: Beyond initial purchase price, consider maintenance costs, material costs, software licenses, and training expenses. Calculate the total cost of ownership to avoid unexpected expenses.
6. Post-Processing Requirements: Understand the post-processing needed for printed parts. Some methods may need additional work such as heat treatment, machining, or surface finishing that can add to lead time and costs.
7. Future Scalability: Ensure the printer can adapt to evolving technology or increasing production demands. Look for modular designs or software that can be upgraded.
8. Support and Training: Verify the vendor provides adequate training and post-sale support. Strong technical assistance is crucial for a successful integration into your workflow.
Taking these factors into account will aid in making a well-informed purchasing decision that meets your specific metal 3D printing needs.
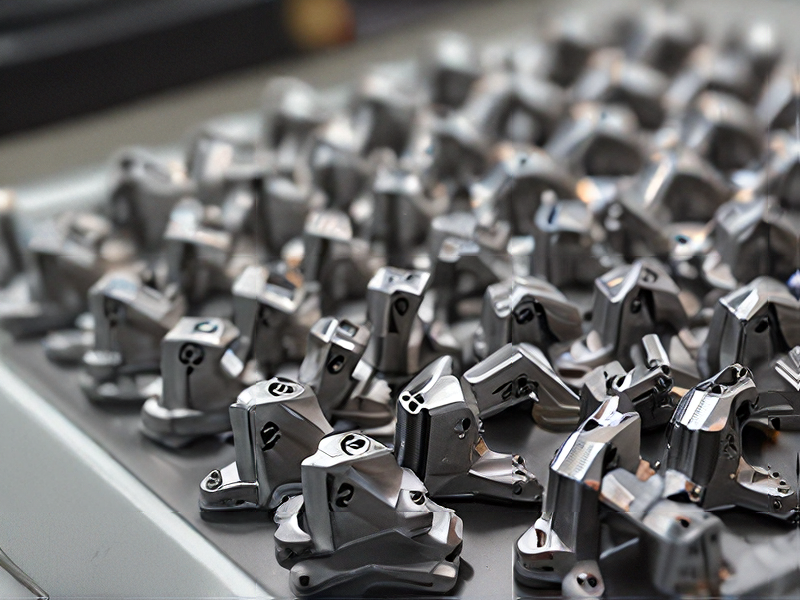
FAQs on Sourcing and Manufacturing from 3d printers metal in China
FAQs on Sourcing and Manufacturing with 3D Metal Printing in China
Q1: What are the advantages of using metal 3D printing in China?
A1: Metal 3D printing offers design flexibility, rapid prototyping, and reduced material waste. China’s advanced technology and competitive pricing make it an attractive option for businesses seeking efficient manufacturing solutions.
Q2: What materials are commonly used in metal 3D printing?
A2: Common materials include stainless steel, titanium, aluminum, and cobalt-chrome alloys. These materials provide strength and durability suitable for various applications.
Q3: How can I find reliable manufacturers in China?
A3: Research potential manufacturers through platforms like Alibaba, Globalsources, or Made-in-China. Check customer reviews, certifications, and request samples to assess quality before committing.
Q4: What are the lead times for metal 3D printing?
A4: Lead times can vary, typically ranging from a few days for prototypes to several weeks for larger orders depending on complexity and volume.
Q5: What quality control measures should I expect?
A5: Reputable manufacturers should implement quality control processes, including material inspections, dimensional checks, and final product testing to ensure adherence to specifications.
Q6: Are there intellectual property concerns?
A6: Yes, it’s essential to protect your designs. Use non-disclosure agreements (NDAs) and consider working with manufacturers who respect IP rights.
Q7: What is the cost structure for 3D metal printing?
A7: Costs depend on material, complexity, and volume. Generally, expect initial setup costs followed by variable costs based on production requirements.
Q8: Can I customize my designs?
A8: Yes, 3D printing allows for high customization, enabling you to modify designs easily to meet specific needs.
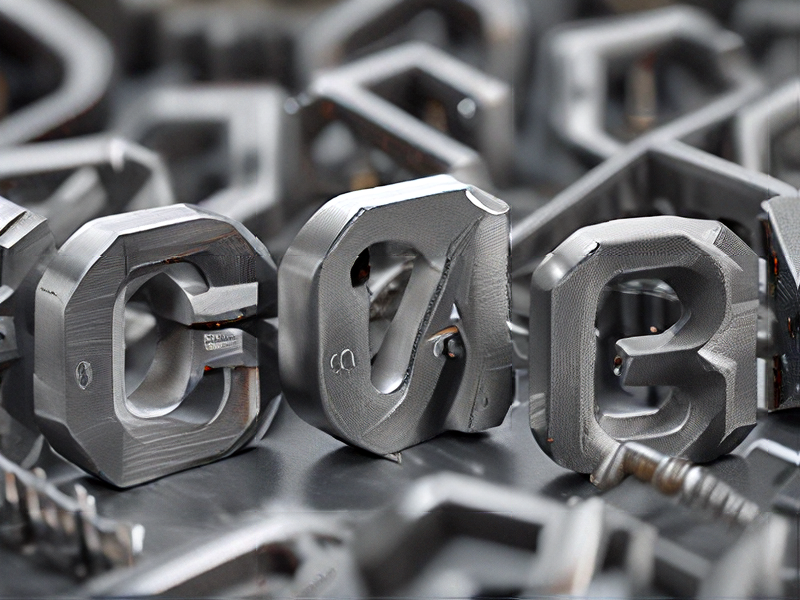