Technology and Applications of 3d printers with metal
3D printing with metal, often referred to as metal additive manufacturing, has revolutionized various industries by enabling the production of complex geometries that are difficult or impossible to achieve with traditional manufacturing methods. Key technologies in this domain include Direct Metal Laser Sintering (DMLS), Selective Laser Melting (SLM), and Binder Jetting.
DMLS and SLM utilize high-powered lasers to melt and fuse metal powder layer by layer, resulting in high-density parts with superior mechanical properties. These methods are commonly used in aerospace, automotive, and medical sectors, where lightweight and strong components are essential.
Binder Jetting, on the other hand, involves depositing a liquid binding agent onto layers of metal powder, which are then sintered in a furnace to create dense structures. This technique offers the advantage of faster production speeds and lower costs, making it suitable for both prototyping and low-volume production.
Applications of metal 3D printing are vast and include the fabrication of custom implants in healthcare, complex tooling in manufacturing, and lightweight components in aerospace. Companies are also leveraging this technology for rapid prototyping, allowing for faster design iterations and reduced time to market.
Moreover, advancements in materials science have expanded the range of metals suitable for 3D printing, including titanium, stainless steel, and inconel, enhancing application possibilities.
Despite its benefits, challenges such as post-processing requirements, surface finish, and high initial equipment costs remain. Nonetheless, the future of metal 3D printing looks promising as innovations continue to drive efficiency and expand its applications across diverse industries.
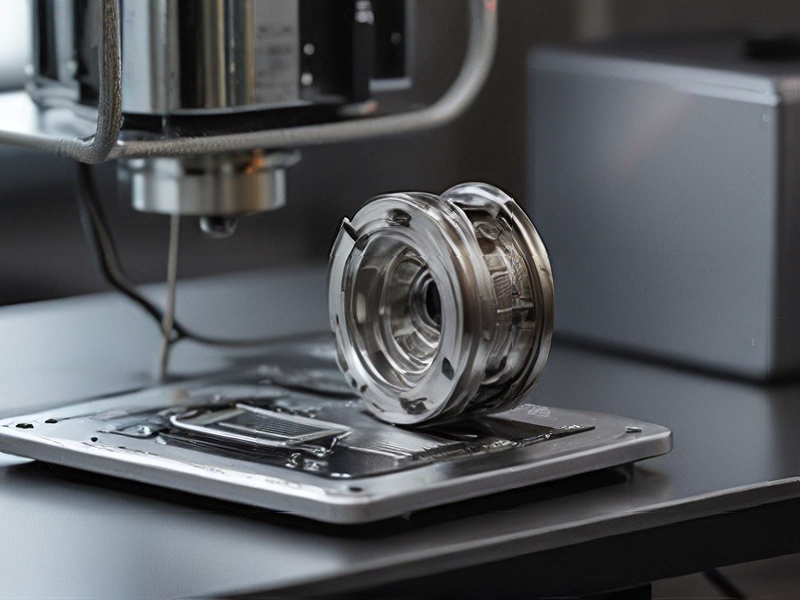
Quality Testing Methods for 3d printers with metal and how to control quality
Quality testing for metal 3D printers is crucial to ensure that parts meet specifications and perform reliably. Here are some key methods and control measures:
1. Dimensional Accuracy Measurement: Use precision instruments like calipers and gauges to measure the dimensions of printed parts. Compare these measurements against CAD models to ensure they conform to design specifications.
2. Visual Inspection: Conduct a thorough visual inspection for defects, such as layer delamination, surface roughness, or inconsistencies. High-resolution imaging can aid in identifying flaws that may not be immediately visible.
3. Mechanical Testing: Perform tensile, compressive, and fatigue tests to evaluate the mechanical properties of printed parts, such as strength and ductility. This helps ensure they meet industry standards.
4. Non-Destructive Testing (NDT): Techniques like ultrasonic testing or X-ray computed tomography (CT) are useful for detecting internal defects, such as voids or inclusions, without damaging the parts.
5. Microstructural Analysis: Use optical microscopy or scanning electron microscopy (SEM) to examine the microstructure of the printed metal. This analysis can reveal issues related to the printing process, such as grain size and phase distribution.
6. Process Monitoring: Implement real-time monitoring systems that track parameters like temperature, laser power, and scanning speed during printing. This data can help identify deviations that may affect quality.
7. Post-Processing Checks: After printing, parts often require heat treatment or surface finishing. Regular checks during these processes can help maintain consistency and quality.
Controlling quality involves setting strict guidelines for each stage of production, conducting routine audits, and employing a closed-loop system for continuous improvement, ensuring that every printed piece meets requisite standards.

Tips for Procurement and Considerations when Purchasing from 3d printers with metal
When considering the procurement of metal 3D printers, it’s essential to evaluate several key factors to ensure a successful investment.
1. Material Compatibility: Assess the range of metals the printer can handle (e.g., titanium, aluminum, stainless steel). Ensure it aligns with your intended applications.
2. Printing Technology: Familiarize yourself with the various 3D printing technologies available, such as Selective Laser Melting (SLM) or Electron Beam Melting (EBM). Each has its advantages and limitations in terms of speed, cost, and material properties.
3. Build Volume: Consider the printer’s build volume to ensure it can accommodate the size of parts you need to produce. Larger volumes may increase versatility but could also mean higher costs.
4. Post-Processing Requirements: Understand the necessary post-processing steps for parts made from metal, such as sintering or surface finishing, and whether your facility can handle these processes.
5. Cost of Ownership: Factor in not just the initial purchase price, but also the costs related to maintenance, material consumption, software, and necessary training for your team.
6. Supplier Reputation: Research the manufacturers and suppliers for their reliability, customer support, and service records. Reviews and case studies can provide valuable insights.
7. Future-Proofing: Consider the scalability and upgrades offered by the manufacturer to ensure the printer can evolve with your future needs.
8. Regulatory Compliance: Ensure that the printer meets industry-specific standards and regulations, especially if you’re in aerospace, automotive, or medical sectors.
By carefully evaluating these considerations, you can make informed decisions that align with your strategic objectives and enhance your production capabilities.
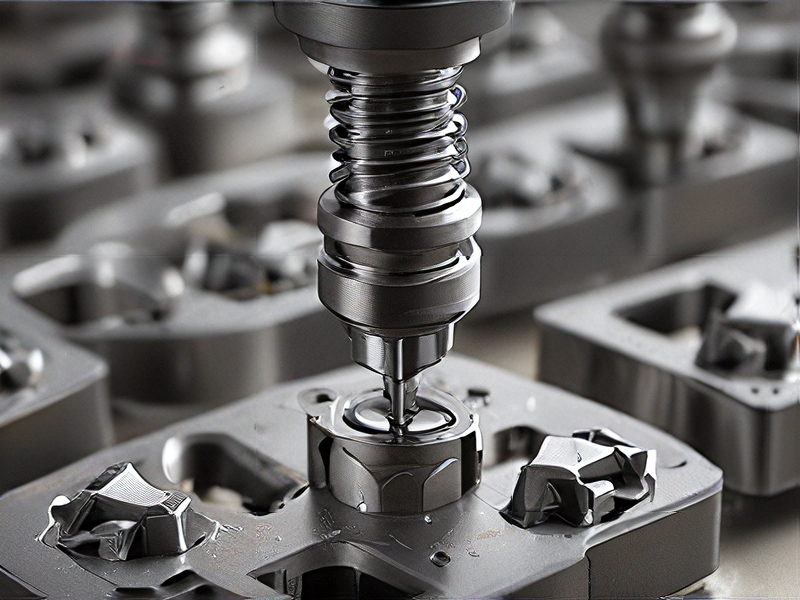
FAQs on Sourcing and Manufacturing from 3d printers with metal in China
FAQs on Sourcing and Manufacturing with Metal 3D Printers in China
1. What are the benefits of using metal 3D printing in China?
Metal 3D printing offers rapid prototyping, design flexibility, and reduced material waste. China also provides competitive pricing and access to advanced technologies.
2. What types of metals can be 3D printed?
Commonly used metals include stainless steel, titanium, aluminum, and cobalt-chrome. The choice of metal depends on the application and desired properties.
3. How do I choose a reliable manufacturer?
Consider factors like certifications (ISO, AS9100), customer reviews, production capabilities, and experience in your specific industry. Request samples to assess quality.
4. What are the typical lead times for production?
Lead times can vary based on complexity and scale, typically ranging from a few weeks to several months. Detailed project timelines should be discussed upfront.
5. What are the costs involved?
Costs depend on the complexity of the design, chosen material, and volume. It’s essential to get detailed quotations, including setup fees, post-processing, and shipping.
6. How is quality controlled in metal 3D printing?
Quality control methods include regular inspections, non-destructive testing, and compliance with industry standards. Ensure your manufacturer has robust quality assurance protocols.
7. Are there design limitations for metal 3D printing?
While metal 3D printing allows for complex geometries, there are limits related to size, support structures, and material properties. Working closely with your manufacturer can help optimize your design.
8. What should I know about intellectual property?
Discuss IP protection upfront. Use non-disclosure agreements (NDAs) and ensure your manufacturer understands the importance of safeguarding your designs.
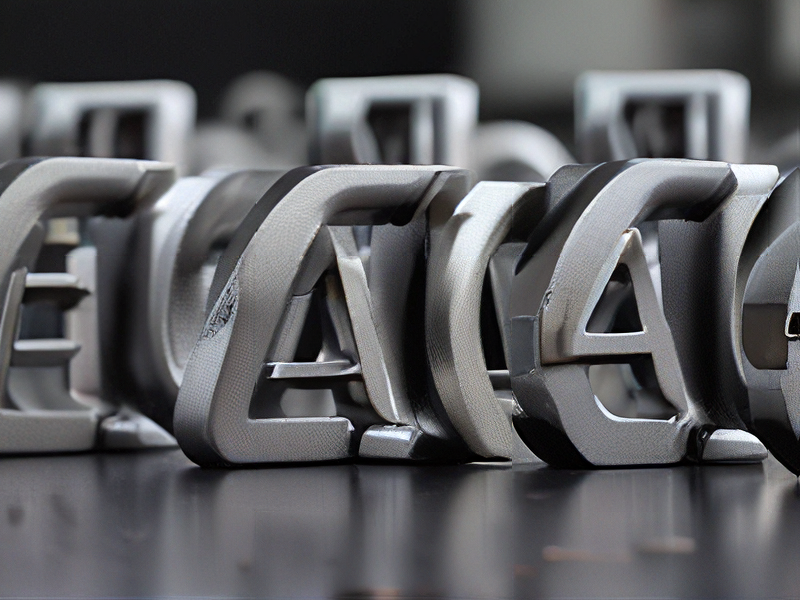