Technology and Applications of cnc machine machine
CNC (Computer Numerical Control) machines have revolutionized manufacturing by automating processes that once required manual labor. These machines utilize computer programs to control their movements and operations with high precision, making them essential in various industries.
Technology: At the core of CNC technology is a computer system that interprets a numerical control (NC) program, which consists of a sequence of commands written in standardized coding languages like G-code. This program directs the machine’s tools—such as lathes, mills, and routers—on how to move, cut, and shape materials. Sensors and feedback loops enhance precision, allowing for intricate designs and consistent production quality. Modern CNC machines often incorporate advanced features like 3D printing integration, robotics, and IoT connectivity, enabling smarter manufacturing processes.
Applications: CNC machines find extensive applications across numerous sectors. In the automotive industry, they are used for manufacturing complex engine components and body parts. Aerospace manufacturers rely on CNC technology for producing lightweight, high-strength components while ensuring precision and safety. The healthcare sector utilizes CNC machining for creating customized prosthetics and surgical instruments. Additionally, CNC machines are prevalent in woodworking, metalworking, and plastic fabrication, allowing artisans and manufacturers to create detailed designs and prototypes with efficiency.
The versatility, accuracy, and repeatability of CNC machines have made them indispensable in modern manufacturing, driving innovations and improving productivity across various domains. With ongoing advancements, the future of CNC technology promises even greater capabilities, including enhanced automation and smart manufacturing solutions.
Quality Testing Methods for cnc machine machine and how to control quality
Quality testing of CNC machines is crucial to ensure precision, reliability, and optimal performance. Here are some effective methods and practices for quality control:
1. Calibration: Regular calibration of CNC machines is essential. Use calibrated measurement tools to verify that machine axes are correctly aligned, ensuring accurate movements.
2. First Article Inspection (FAI): Conduct an FAI for the first part produced after a setup change or tool replacement. Compare it against design specifications to confirm that manufacturing processes are up to standard.
3. In-Process Inspection: Implement real-time inspections during production. Use tools like laser scanners or touch probes to ensure that key dimensions remain within tolerance throughout the machining process.
4. Statistical Process Control (SPC): Employ SPC techniques to monitor production quality. Collect data on key metrics and use control charts to identify trends or variations that may indicate quality issues.
5. Maintenance Checks: Regular preventive maintenance checks help identify wear and tear in machine components, thus reducing the risk of quality deviations.
6. Visual Inspections: After the machining process, conduct visual inspections to detect surface defects, burrs, or other irregularities that could compromise part quality.
7. Material Verification: Ensure that raw materials meet specified criteria before machining. Use certificates of analysis and conduct material tests as necessary.
8. Feedback Loop: Encourage feedback from operators regarding machining performance and part quality. Implement corrective actions promptly to address any identified issues.
By integrating these methods into a robust quality control plan, manufacturers can enhance the precision and reliability of CNC machined parts while minimizing defects and rework.
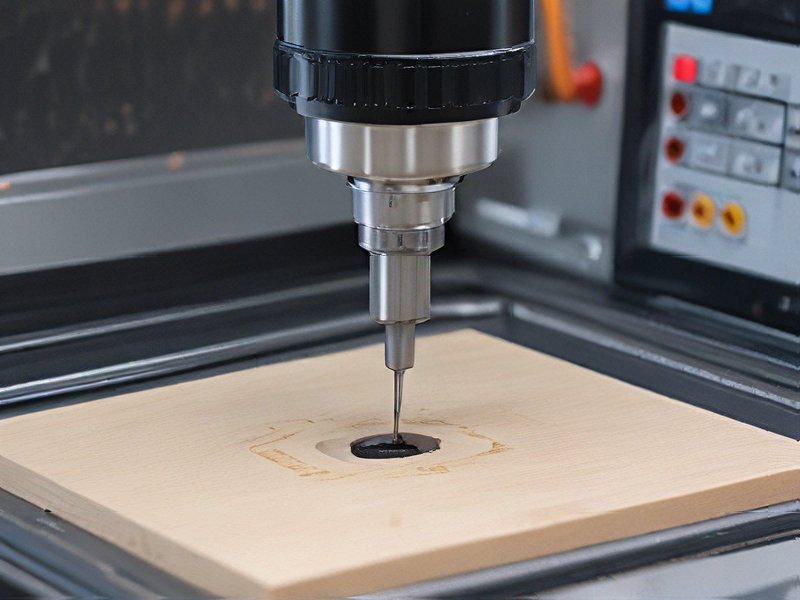
Tips for Procurement and Considerations when Purchasing from cnc machine machine
When considering the procurement of a CNC machine, it’s essential to approach the process methodically to ensure you choose the right equipment for your needs. Here are key tips and considerations:
1. Assess Your Needs: Determine the types of materials, part sizes, and complexity of the components you will manufacture. This will guide you in selecting the appropriate CNC machine type (e.g., milling, turning, plasma cutting).
2. Budget: Establish a budget that includes not just the purchase price, but also installation, training, maintenance, and operational costs. Don’t forget about potential future upgrades.
3. Research Suppliers: Look for reputable suppliers with a track record in the CNC market. Read reviews, seek references, and investigate their after-sales support and warranties.
4. Machine Specifications: Analyze the technical specifications such as axis movement, spindle speed, tooling options, and precision. Ensure that these meet your production requirements.
5. Software Compatibility: Verify the compatibility of the CNC machine with your existing design and manufacturing software. Consider whether you need additional software for programming.
6. User-Friendliness: Consider the ease of use and training requirements. A machine with intuitive controls and good training support can significantly reduce downtime.
7. After-Sales Support: Inquire about customer support, maintenance services, and availability of spare parts. Reliable after-sales service can prolong the machine’s lifespan and productivity.
8. Visit Demonstrations: If possible, visit facilities where the machines are in use. Hands-on demonstrations can provide insight into performance and user experience.
By carefully weighing these considerations, you can make an informed decision leading to successful integration of CNC technology into your operations.
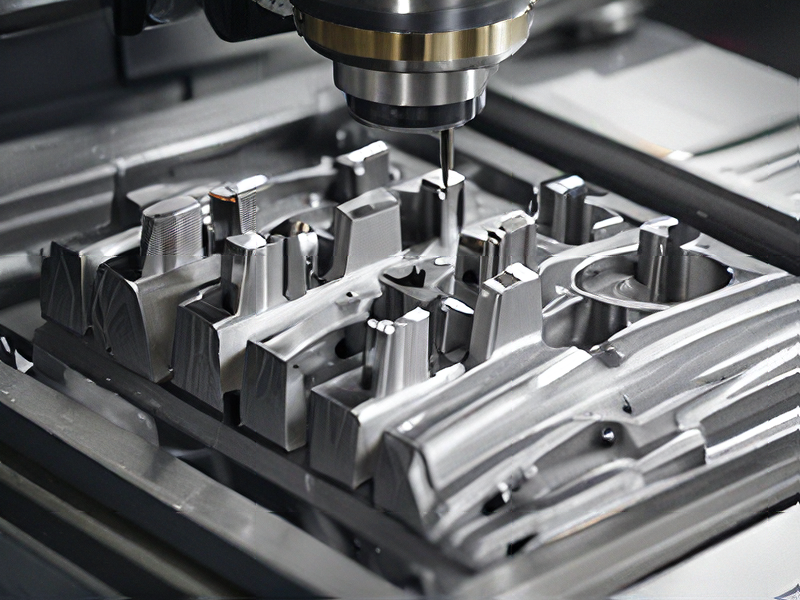
FAQs on Sourcing and Manufacturing from cnc machine machine in China
FAQs on Sourcing and Manufacturing CNC Machines in China
1. Why source CNC machines from China?
China is one of the largest manufacturers of CNC machines, offering competitive prices, a wide range of options, and advanced technology. Many suppliers also provide customization based on specific requirements.
2. What should I consider when choosing a supplier?
Look for a supplier with a good reputation, experience, certifications (like ISO), and positive customer reviews. It’s crucial to assess their manufacturing capabilities and quality control processes.
3. How do I ensure quality?
Request samples, visit the factory if possible, and ask for quality assurance documentation. Some companies also offer third-party inspection services to ensure product quality before shipment.
4. What are the common payment methods?
Common payment methods include wire transfers, PayPal, and letters of credit. Ensure you use secure payment methods to minimize risk.
5. What is the typical lead time for CNC machines?
Lead times can vary based on complexity and order size, generally ranging from 30 to 90 days. Discuss timelines with your supplier early in the process.
6. Are there any import duties or tariffs?
Yes, importing CNC machines may incur customs duties and taxes. Check the regulations in your country to understand applicable tariffs.
7. How important is shipping and logistics?
Shipping and logistics are critical; choose a reliable shipping partner. Consider freight options (air vs. sea) based on urgency and budget.
8. What after-sales support should I expect?
Reliable suppliers should provide technical support, spare parts availability, and warranty services. Always clarify these terms before finalizing the deal.
For a successful sourcing experience, thorough research and clear communication with suppliers are essential.
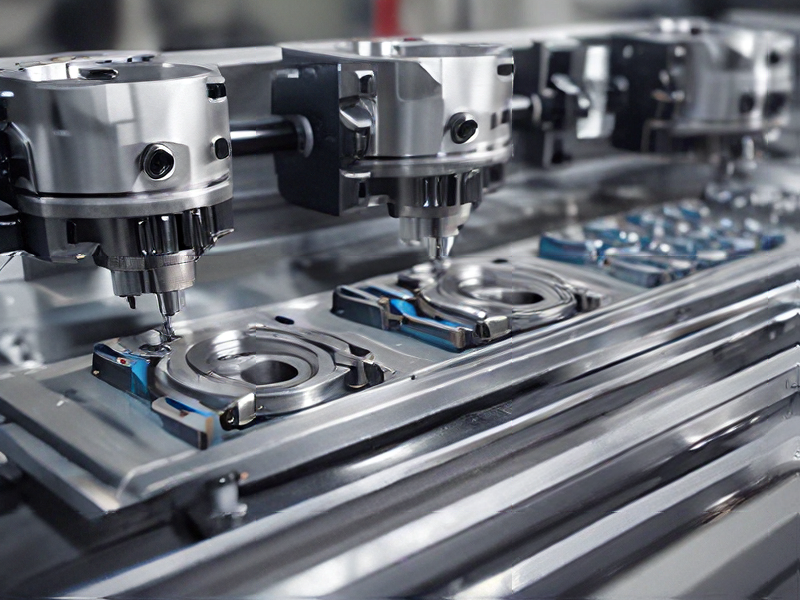