Technology and Applications of computer numerical machine
Computer Numerical Control (CNC) machines are advanced manufacturing tools that utilize computer systems to control machine functions. These machines can operate with high precision and efficiency, enabling intricate designs and automated processes in various industrial applications.
Technology:
CNC machines operate via a computer program coded with G-code, which dictates the machine’s movements. The technology often combines mechanical components, such as motors and drives, with software algorithms, allowing for the automation of tasks like cutting, milling, drilling, and shaping materials. Advanced CNC machines may include features like 3D printing capabilities, laser cutting, and multi-axis operations, which expand their versatility across different manufacturing needs.
Applications:
1. Manufacturing: CNC machines are extensively employed in production settings for fabricating parts and components in industries such as automotive, aerospace, and electronics. They ensure consistent quality and can handle mass production efficiently.
2. Metalworking: CNC lathes and mills are widely used for shaping and finishing metal components, allowing for complex geometries that would be difficult to achieve manually.
3. Woodworking: CNC routers are employed to create intricate designs in wood, including furniture-making and cabinetry, enhancing craftsmanship while reducing labor time.
4. Medical: CNC technology is pivotal in manufacturing medical devices and implants, ensuring accuracy and enabling the creation of customized solutions tailored to individual patient needs.
5. Prototyping: Rapid prototyping utilizes CNC machines to quickly produce models for testing and design verification, facilitating innovation and product development.
In summary, CNC machines revolutionize manufacturing through their precise, automated operations across various industries, improving productivity and enabling complex designs with higher efficiency.
Quality Testing Methods for computer numerical machine and how to control quality
Quality testing for Computer Numerical Control (CNC) machines is crucial to ensure precision and reliability. There are several methodologies and techniques used to maintain and control quality effectively.
1. Calibration and Verification: Regular calibration of CNC machines is essential. Utilizing standard gauge blocks and calibration tools helps ensure that the machine’s movements are accurate. Verification against known standards can highlight inconsistencies.
2. In-Process Monitoring: Employing real-time monitoring systems can provide immediate feedback on the machining process. This includes using sensors and data acquisition systems to track parameters like temperature, vibration, and spindle speed, which can indicate performance deviations.
3. Inspection and Measurement: Post-process inspection using tools like Coordinate Measuring Machines (CMM), dial indicators, and laser scanners ensures that produced components meet the required specifications. Statistical Process Control (SPC) can also monitor these measurements over time to identify trends.
4. Tool Condition Monitoring: Regularly assessing the condition of cutting tools is vital. Techniques such as visual inspections, tool wear measurement, and checks for breakage can prevent defects caused by tool degradation.
5. Software Simulation: Before actual machining, using simulation software to model machining processes can help identify potential issues and optimize tool paths, leading to higher quality outcomes.
6. Employee Training: Ensuring operators are well-trained in both machine operation and quality standards maximizes accuracy. Regular workshops and training sessions can update skills and knowledge.
Implementing these quality testing methods creates a robust framework for maintaining CNC machine quality, ultimately leading to consistent production of high-quality components.
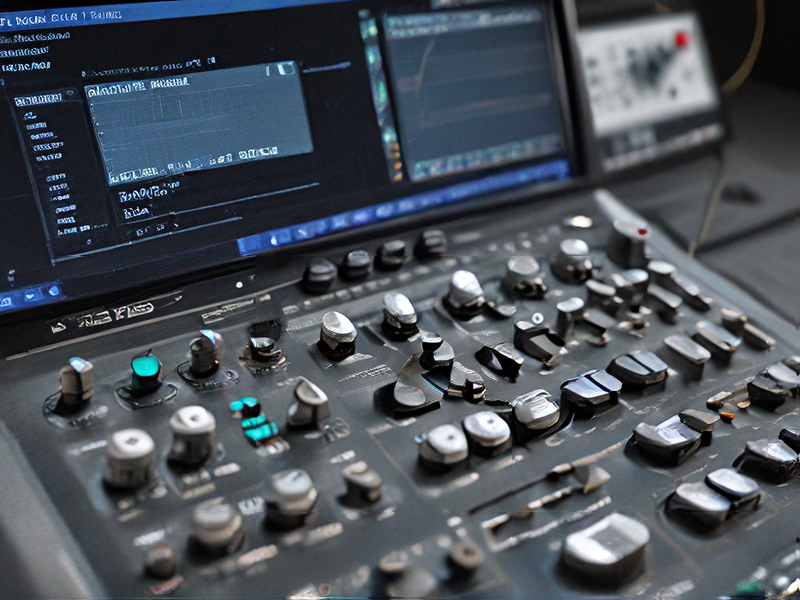
Tips for Procurement and Considerations when Purchasing from computer numerical machine
When procuring a computer numerical control (CNC) machine, consider the following tips and factors:
1. Assess Your Needs: Clearly define the specifications based on your production requirements. Consider factors such as material types, dimensions, and complexity of parts to ensure the CNC machine meets your needs.
2. Budgeting: Establish a budget that includes not just the purchase price but also installation, training, maintenance, and any necessary software. Be realistic about potential hidden costs.
3. Technology and Features: Evaluate the machine’s technology, including the type of CNC system, control software, and tooling compatibility. Advanced features like automation and precision should align with your production goals.
4. Supplier Reputation: Research potential suppliers thoroughly. Look for companies with strong customer reviews, reliable support, and a proven track record in the CNC industry.
5. Support and Training: Determine the level of technical support and training offered by the supplier. A good training program can enhance operator efficiency and minimize downtime.
6. Warranty and Service Agreements: Review warranty options and service agreements. A comprehensive warranty and access to customer service can provide peace of mind and protect your investment.
7. Flexibility and Scalability: Consider whether the machine can adapt to future needs. As your business grows, you may require additional capabilities or features.
8. Visit the Facility: If possible, visit the supplier’s facility to see the machines in action. This provides insight into build quality and operational efficiency.
By carefully evaluating these considerations, you can make a more informed decision that aligns with your operational goals and budgetary constraints.
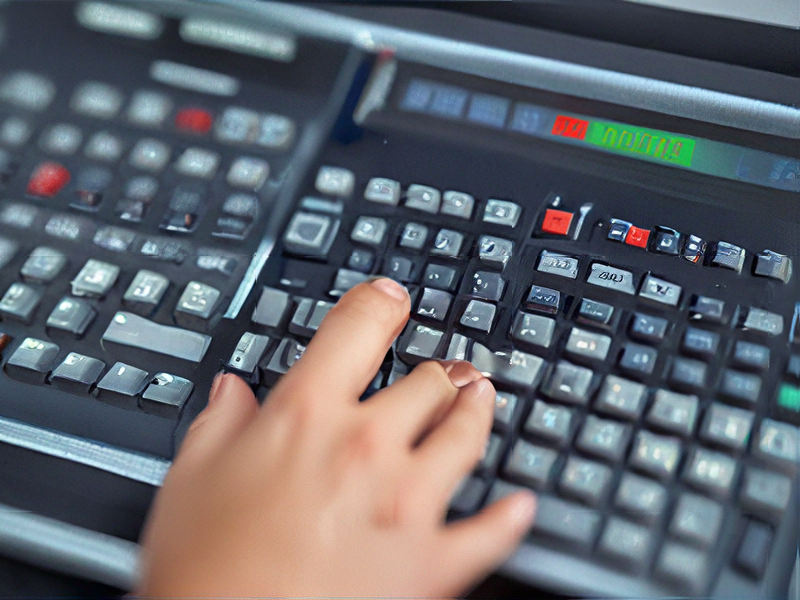
FAQs on Sourcing and Manufacturing from computer numerical machine in China
FAQs on Sourcing and Manufacturing CNC Machines in China
1. Why source CNC machinery from China?
China offers competitive pricing, a wide range of suppliers, and advanced manufacturing technologies. This makes it an attractive option for sourcing CNC machines.
2. How do I find reliable CNC manufacturers in China?
Start by using B2B platforms like Alibaba, Global Sources, or Made-in-China. Attend trade shows, verify company credentials, and look for reviews or references.
3. What are the quality control measures?
Ensure the manufacturer complies with international standards like ISO 9001. Conduct pre-production samples, in-process inspections, and final quality checks. Hiring third-party inspection services can also be beneficial.
4. What are the lead times for CNC machinery production?
Lead times vary based on customization and order size, typically ranging from 4 to 12 weeks. Always discuss and agree on timelines during the negotiation phase.
5. How do I handle shipping and logistics?
Work with freight forwarders experienced in importing machinery. Clearly specify shipping methods and terms (FOB, CIF) in your contract for smoother logistics.
6. What about after-sales service and support?
Confirm the manufacturer’s warranty and support terms before purchasing. Many reputable suppliers offer technical support, spare parts, and even on-site assistance.
7. Are there language barriers when dealing with Chinese manufacturers?
Language can be a challenge. Consider hiring a translator or work with manufacturers who have English-speaking staff. Clear communication is essential for successful collaboration.
8. What payment methods are commonly used?
Popular payment methods include bank transfers (T/T), PayPal, or L/C. Be cautious with large payments; ensure the manufacturer has a good reputation before proceeding.
9. How can I protect my intellectual property (IP)?
Sign a Non-Disclosure Agreement (NDA) and specify IP rights in your contract. However, it’s essential to understand that enforcement in China can be challenging.
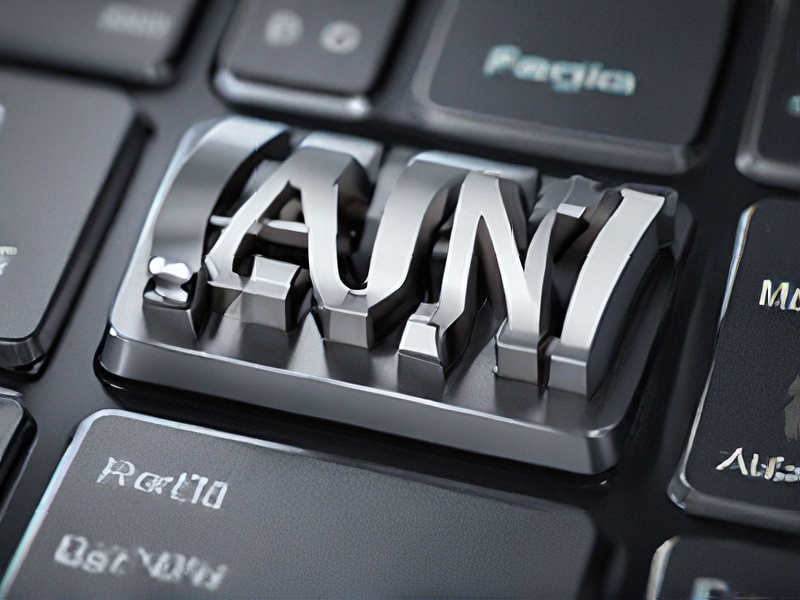