Technology and Applications of cold metal transfer
Cold Metal Transfer (CMT) is an advanced welding process that has emerged as a significant innovation in the field of material joining. CMT utilizes a unique arc welding technique, characterized by a controlled transfer of metal droplets from the welding electrode to the workpiece. This process operates at a low heat input, minimizing thermal distortion and reducing the risk of warping or damaging sensitive materials.
One of the primary applications of CMT is in the automotive industry, where it is used for joining lightweight materials such as aluminum and high-strength steels. These materials are increasingly being utilized to enhance fuel efficiency and reduce overall vehicle weight. The CMT process ensures high-quality welds with minimal spatter and a high degree of aesthetic appeal, which is crucial in automotive applications.
Beyond automotive, CMT finds applications in aerospace, shipbuilding, and electronics manufacturing. Its ability to weld thin materials with precision makes it ideal for the fabrication of complex components that require a high degree of structural integrity without compromising the properties of the base material.
Moreover, CMT is particularly well-suited for robotic welding applications, allowing for increased automation and productivity in manufacturing processes. The technology’s ease of use and adaptability contribute to its growing popularity across various industries.
In summary, Cold Metal Transfer is a versatile and efficient welding technology that offers distinct advantages in terms of quality, precision, and material compatibility, making it an essential tool in modern manufacturing and fabrication processes.
Quality Testing Methods for cold metal transfer and how to control quality
Quality testing methods for Cold Metal Transfer (CMT) welding involve a combination of visual inspections, non-destructive testing, and mechanical property assessments to ensure the integrity of the welds.
1. Visual Inspection: The initial step involves a thorough visual examination of welds. Inspectors look for defects such as undercuts, porosity, and incomplete fusion. This method is quick and can often catch obvious issues before more detailed testing.
2. Non-Destructive Testing (NDT): Various NDT methods can be employed:
– Ultrasonic Testing (UT): This uses high-frequency sound waves to detect internal flaws and assess the size and disposition of defects.
– X-ray or Gamma-ray Radiography: This method provides a detailed image of the weld’s internal structure, identifying any inconsistencies.
– Magnetic Particle Testing (MPT): Suitable for ferromagnetic materials, this method detects surface and near-surface defects using magnetic fields and fine iron particles.
3. Mechanical Testing: This includes tensile, impact, and hardness tests to evaluate the weld’s structural integrity and performance under load. Samples are extracted from the welded section to determine how well the materials will perform under actual service conditions.
4. Quality Control (QC) Procedures: Implementing a robust QC management system is essential. This involves setting standard operating procedures, conducting routine audits, and maintaining traceability through documentation. Training operators and continuing education on CMT technology and best practices will further enhance consistent quality.
In summary, employing a combination of visual inspections, NDT methods, mechanical testing, and stringent QC protocols will effectively control and assure the quality of CMT welding processes.
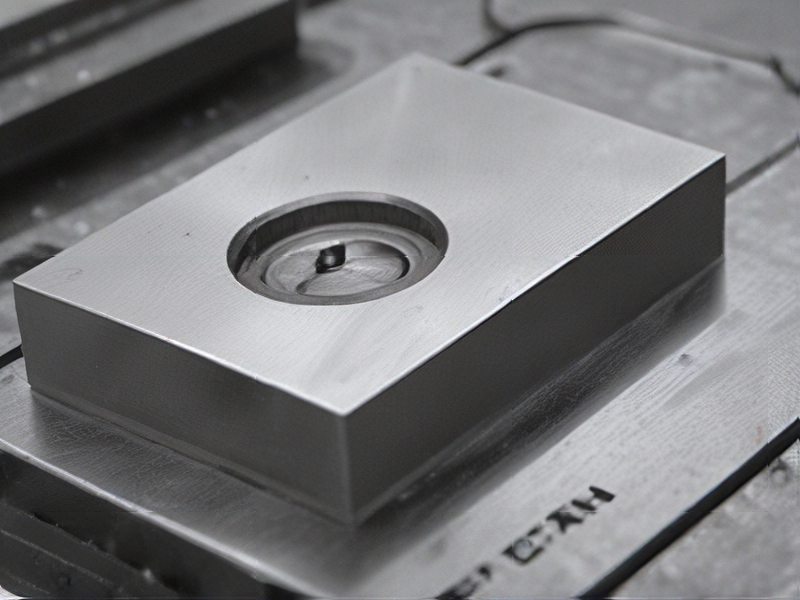
Tips for Procurement and Considerations when Purchasing from cold metal transfer
When procuring equipment and services related to Cold Metal Transfer (CMT), consider the following tips and considerations:
1. Understand the Technology
Before making a purchase, familiarize yourself with CMT technology—its benefits like reduced heat input, minimal distortion, and ability to weld dissimilar metals. Knowing how CMT differs from traditional welding processes will help you make informed decisions.
2. Identify Your Needs
Assess your specific requirements—material types, thicknesses, production volume, and desired weld quality. This will guide you in selecting the right CMT equipment and accessories suited for your operations.
3. Vendor Reputation
Research potential suppliers and their reputations. Look for companies with a track record of reliability and customer support in CMT technology. Reviews and case studies can provide insights into their performance.
4. Cost vs. Value
Evaluate the total cost of ownership (TCO) instead of just the initial purchase price. Consider factors like maintenance, consumables, warranty, and potential downtime. Sometimes, a higher initial investment can lead to better long-term savings.
5. Training and Support
Choose vendors that offer comprehensive training and ongoing technical support. CMT can require skill and knowledge to operate effectively, and having access to training resources can enhance your team’s capabilities.
6. Future-Proofing
With technology advancing rapidly, consider how adaptable the equipment is to new techniques and materials. Investing in machines that allow for upgrades can save costs in the long run.
7. Sample Testing
Whenever possible, arrange for sample testing or demonstrations. This allows you to evaluate the performance of the equipment and assess its suitability for your specific applications.
Making informed decisions in CMT procurement ensures quality, efficiency, and long-term satisfaction.
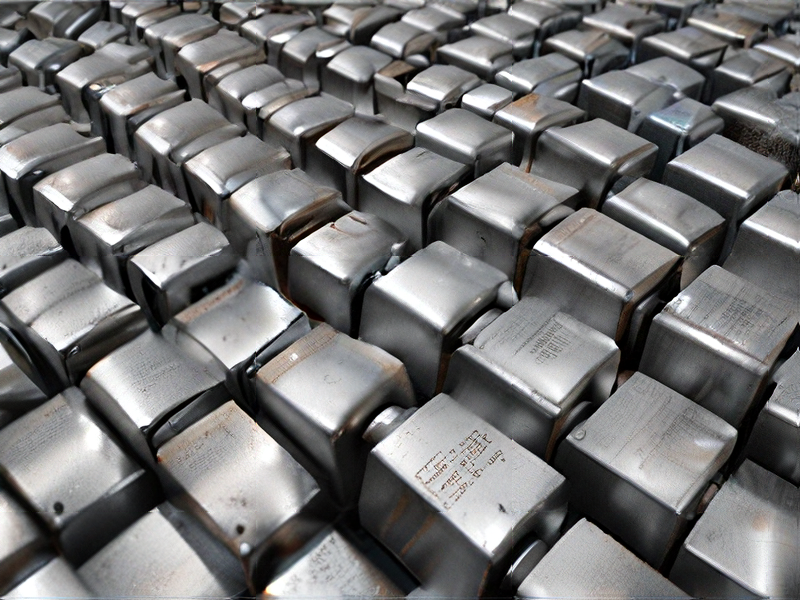
FAQs on Sourcing and Manufacturing from cold metal transfer in China
FAQs on Sourcing and Manufacturing with Cold Metal Transfer (CMT) in China
1. What is Cold Metal Transfer (CMT)?
CMT is a welding process that uses low heat input to ensure minimal thermal distortion and optimal weld quality. It’s ideal for joining thin materials and is particularly effective with aluminum and steel.
2. Why choose CMT for manufacturing in China?
CMT offers high precision and control, making it suitable for complex designs and lightweight components. China’s advanced manufacturing infrastructure can support high-quality CMT processes.
3. What industries can benefit from CMT in China?
CMT is widely used in automotive, aerospace, electronics, and general manufacturing, offering benefits such as reduced weight and enhanced structural integrity.
4. How do I find CMT manufacturers in China?
You can source manufacturers through trade platforms (like Alibaba), industry fairs, or by engaging sourcing agents familiar with the CMT process.
5. What should I consider when selecting a manufacturer?
Evaluate their expertise in CMT, production capacity, quality management systems (like ISO certifications), and previous project portfolios to ensure they meet your specific needs.
6. What are the lead times for CMT manufacturing?
Lead times vary based on order complexity and volume. Typically, samples can take weeks, while large production runs may require several months.
7. How can I ensure quality control?
Implement regular audits and on-site inspections. Additionally, working with third-party quality assurance services can help maintain production standards.
8. Are there any challenges in sourcing CMT in China?
Potential challenges include communication barriers, cultural differences, and varying standards of quality. It’s crucial to establish clear specifications and maintain ongoing communication.
For further inquiries or specific needs, it’s advisable to consult directly with experienced CMT manufacturers in China.
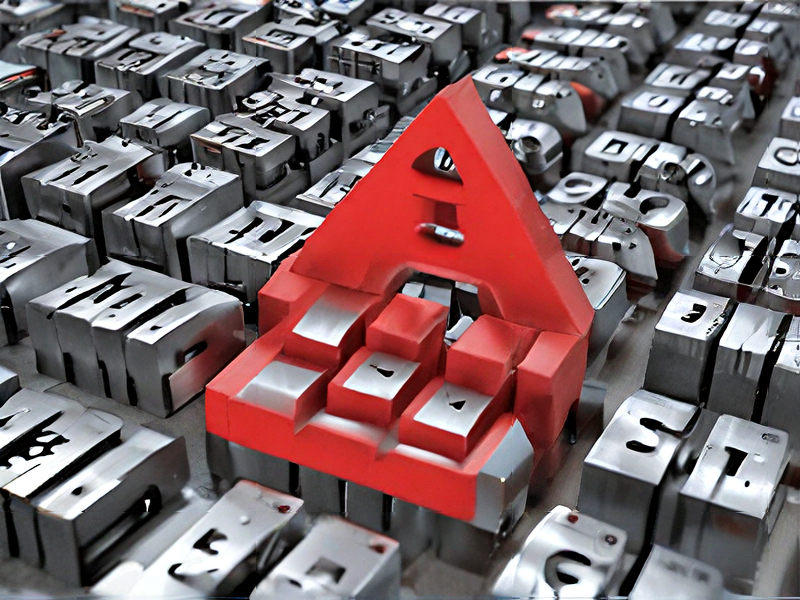