Technology and Applications of machine shops
Machine shops play a critical role in modern manufacturing, utilizing advanced technology to produce precise engineering components. These facilities are equipped with various tools and machinery, such as Computer Numerical Control (CNC) machines, lathes, milling machines, and 3D printers, allowing them to create parts with high accuracy and repeatability.
CNC technology has revolutionized machine shops by automating machining processes. Operators input designs from computer-generated models, which the CNC machines interpret to execute complex shapes and geometries with minimal human intervention. This enhances efficiency, reduces errors, and improves productivity.
Additionally, machine shops utilize advanced materials such as titanium, composites, and specialty steels, which meet the demanding requirements of industries including aerospace, automotive, and medical devices. The ability to work with these materials opens up new avenues for innovation and application.
Machine shops also integrate technologies like additive manufacturing, which allows for the layer-by-layer creation of components, reducing waste and enabling the production of customized parts that are lightweight yet strong. This is particularly beneficial in industries requiring intricate designs or small production runs.
Furthermore, Industry 4.0 concepts, including the Internet of Things (IoT) and automation, are slowly being adopted in machine shops. These technologies enable real-time monitoring of machinery and processes, enhancing maintenance and operational efficiency.
In summary, modern machine shops leverage advanced technologies and materials to improve manufacturing capabilities, allowing for the production of complex, high-quality components. Their applications span numerous industries, signifying their crucial role in the evolution of manufacturing.
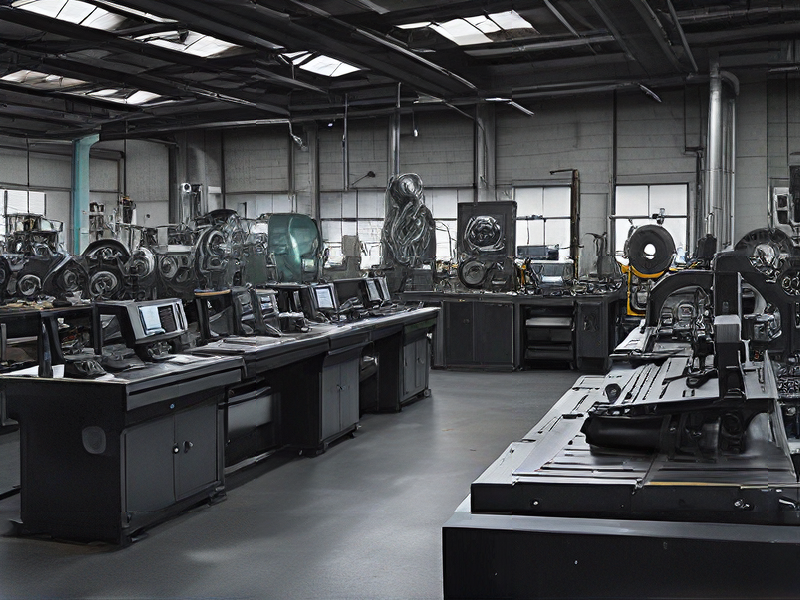
Quality Testing Methods for machine shops and how to control quality
Quality testing in machine shops is crucial for ensuring that products meet specifications and standards. Here are several effective methods for quality testing and control:
1. Incoming Material Inspection: Before production begins, raw materials should be inspected for compliance with specified standards. This can involve measuring dimensions, checking for defects, and verifying material certificates.
2. In-Process Inspections: Implementing periodic checks during production helps catch errors early. Techniques include visual inspections, gauge measurements, and differentiation checks at various stages of machining.
3. Final Inspection: Completed parts should undergo thorough examination against specifications. Tools like coordinate measuring machines (CMM), optical comparators, or functional testing may be employed to ensure accuracy.
4. Statistical Process Control (SPC): Utilize control charts to monitor process variations over time. By analyzing data, machine shops can identify trends and make adjustments before issues escalate.
5. Non-Destructive Testing (NDT): Techniques such as ultrasonic testing, magnetic particle testing, or dye penetrant testing help detect internal and surface defects without damaging the parts.
6. Documentation and Traceability: Maintain records of inspections, tests, and processes to ensure traceability. This not only aids in identifying issues but also enhances accountability.
7. Employee Training: Invest in continuous training for employees on best practices and quality standards. Engaged workers are more likely to identify potential quality issues.
8. Lean Manufacturing Principles: Implementing lean practices can minimize waste and improve efficiency, leading to better quality outcomes.
By combining these methods, machine shops can actively control quality, reduce defects, and ensure customer satisfaction. Regular reviews and updates to quality control processes will further enhance this commitment.
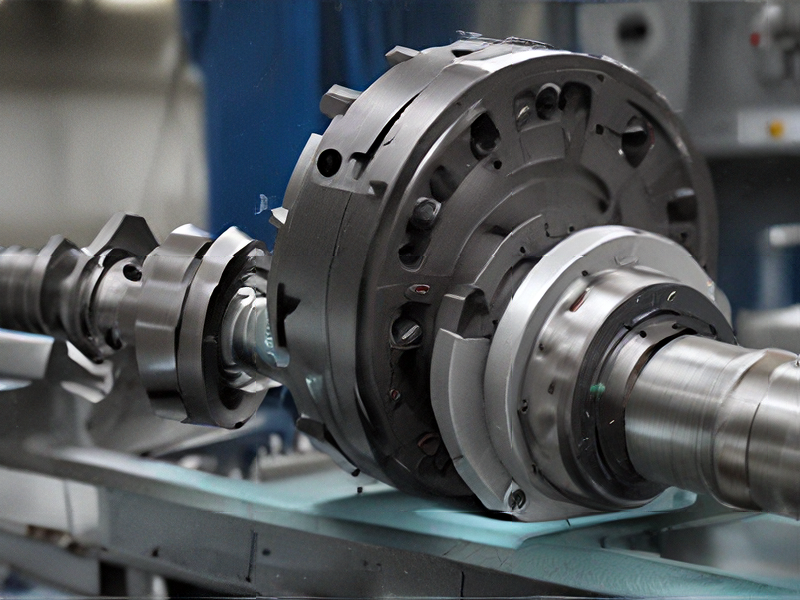
Tips for Procurement and Considerations when Purchasing from machine shops
When procuring from machine shops, it’s crucial to consider several key factors to ensure quality, cost-effectiveness, and timely delivery. Here are some tips:
1. Define Requirements Clearly: Start with a detailed specification of your project, including dimensions, tolerances, material types, and surface finishes. Clear requirements minimize miscommunication and defects.
2. Evaluate Capabilities: Research potential machine shops to assess their capabilities, technology, and experience. Ensure they have the right machinery for your specific needs, such as CNC machining, welding, or laser cutting.
3. Quality Assurance: Inquire about the quality control processes in place. Look for certifications like ISO 9001, which indicate a commitment to quality. Request samples or references to gauge their workmanship.
4. Cost Structure: Understand the pricing model—cost per part, hourly rates, or setup fees. Obtain detailed quotes from multiple shops to compare costs comprehensively.
5. Lead Time: Discuss lead times and ensure they align with your project timeline. Flexibility might be necessary, but ensure the shop can meet your deadlines without compromising quality.
6. Communication: Establish a clear line of communication. A responsive shop can address issues proactively and adapt to changes in your order.
7. Post-Production Support: Check if the machine shop offers additional services like assembly, finishing, or packaging, which can save you time and effort.
8. Build Relationships: Forming a long-term partnership with a reliable machine shop can lead to better pricing, priority service, and improved collaboration on future projects.
By considering these factors, you can make informed decisions that enhance the efficiency and success of your procurement process.
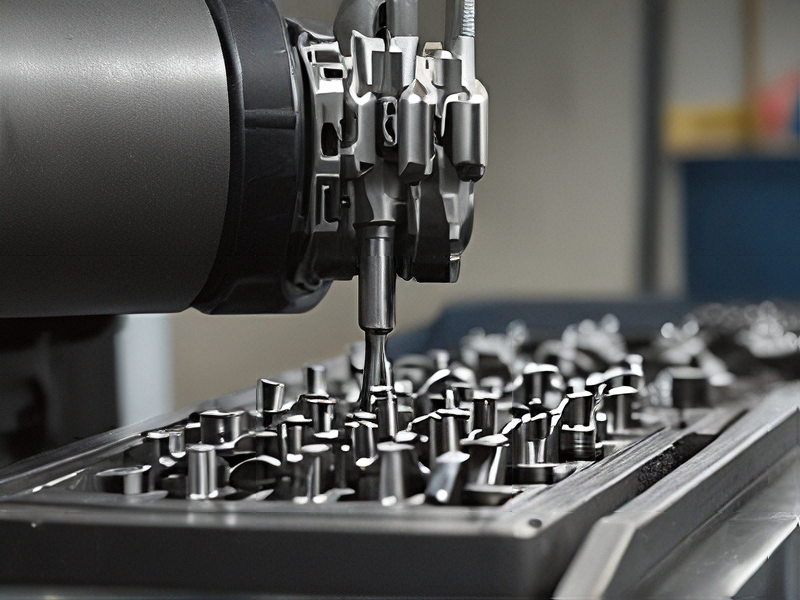
FAQs on Sourcing and Manufacturing from machine shops in China
FAQs on Sourcing and Manufacturing from Machine Shops in China
1. What should I consider when choosing a machine shop in China?
Evaluate the shop’s capabilities, experience, certifications (like ISO), and previous projects. Ensure they specialize in your required processes.
2. How can I ensure quality control?
Request samples before full production, conduct regular quality inspections, and consider third-party inspection services. Clear specifications and standards are essential.
3. What is the typical lead time for manufacturing?
Lead times can vary widely based on complexity and volume, ranging from a few weeks to several months. It’s vital to discuss timelines upfront.
4. How do I handle language barriers?
Engage a skilled translator or sourcing agent if necessary. Clear communication is crucial to avoid misunderstandings about specifications and requirements.
5. What shipping options are available?
You can choose air freight for quicker delivery or sea freight for cost-saving on larger orders. Ensure you clarify shipping terms like FOB or CIF.
6. Are there minimum order quantities (MOQs)?
Many machine shops have MOQs depending on the type of product and manufacturing process. Be sure to confirm this before placing orders.
7. How do I protect my intellectual property (IP)?
Use Non-Disclosure Agreements (NDAs), and if possible, register your IP in China. Discuss your concerns with potential suppliers.
8. What are the payment terms?
Payment terms vary, but common practices include a deposit upfront and balance upon delivery. Ensure terms are agreed upon in writing.
9. Can I visit the factory?
Yes, factory visits are highly recommended for building relationships, understanding capabilities, and ensuring quality. If visiting isn’t possible, consider virtual tours.
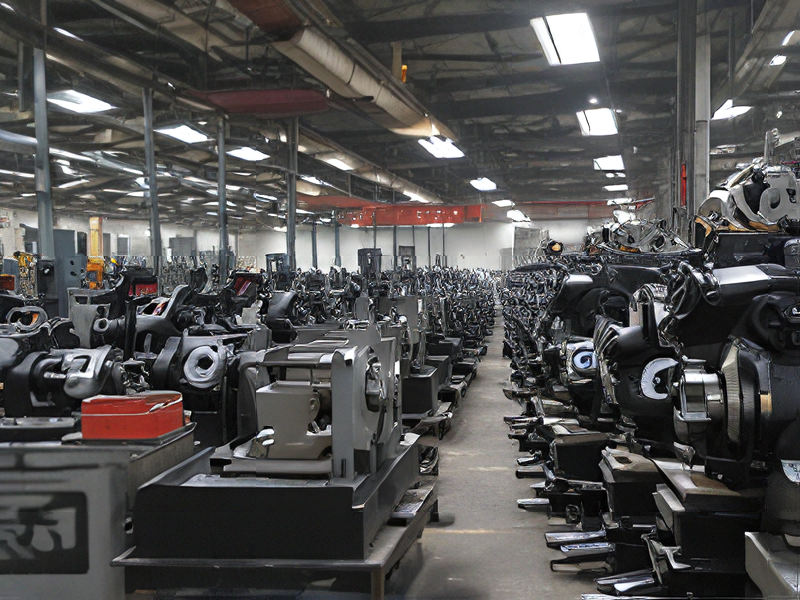