Technology and Applications of machining shop
Machining shops leverage advanced technologies and applications to shape, cut, and finish materials with precision. The core processes include turning, milling, drilling, and grinding, typically executed on computer numerical control (CNC) machines. CNC technology enhances accuracy and consistency by automating tool movement based on pre-programmed coordinates.
Modern machining shops utilize various materials, including metals, plastics, and composites. Techniques such as additive manufacturing (3D printing) complement traditional methods, enabling rapid prototyping and complex geometries that would be difficult to achieve through conventional machining.
Key technologies in machining shops also encompass advanced tooling, like carbide and ceramic tools, which improve durability and performance. Additionally, the use of robotics in material handling and assembly streamlines operations, reducing labor costs and increasing productivity.
Software applications play a crucial role in machining. Computer-aided design (CAD) allows for the creation of precise models, while computer-aided manufacturing (CAM) software translates these designs into machine operations. Integrated manufacturing systems further enhance efficiency by coordinating processes from design to production.
Quality control technologies, including coordinate measuring machines (CMM) and laser scanning, ensure that the final products meet stringent specifications. Industry 4.0 principles are increasingly being adopted, incorporating IoT sensors for real-time monitoring and data analytics to optimize processes and predict machine failures.
In summary, machining shops are at the forefront of manufacturing, utilizing a combination of traditional and modern technologies to deliver high-quality products efficiently and cost-effectively. This synergy of tools, software, and innovative practices continues to evolve, driving advancements in various industries.
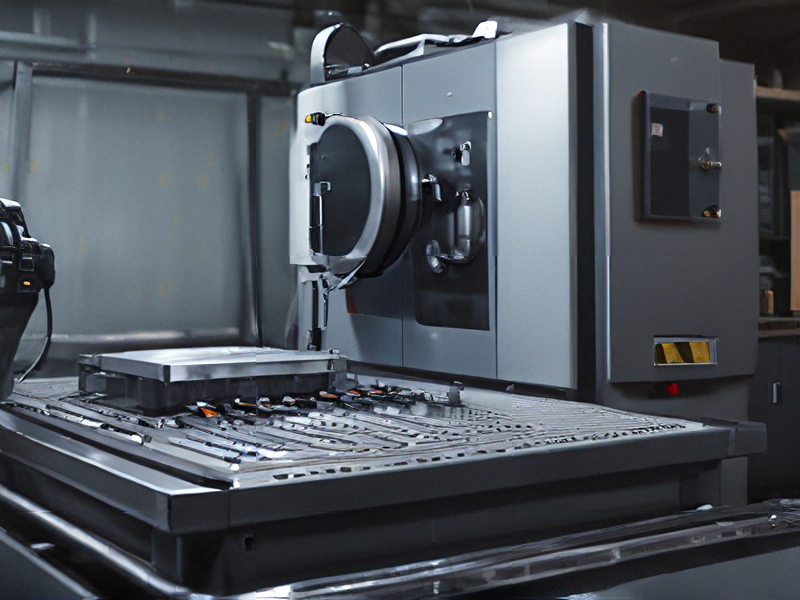
Quality Testing Methods for machining shop and how to control quality
Quality testing in a machining shop is essential for ensuring that products meet specified standards and customer expectations. Here are several effective methods and control strategies:
1. In-Process Inspection: Conduct inspections during various stages of the machining process. Utilize tools like calipers, micrometers, and gauges to measure dimensions and tolerances in real-time, allowing for immediate corrections if deviations are found.
2. Final Inspection: After machining, perform a comprehensive inspection. This may include visual checks, dimensional measurements, and functional testing. Sampling can be employed to assess batches when production volume is high, ensuring that any defects are caught.
3. Statistical Process Control (SPC): Use SPC techniques to monitor process performance. By collecting and analyzing data from machining operations, trends and variations can be identified early, helping to maintain machine performance and product quality.
4. Non-Destructive Testing (NDT): Where applicable, implement NDT methods such as ultrasonic testing or magnetic particle inspection to assess internal and surface defects without damaging parts.
5. Documentation and Traceability: Maintain thorough records of all inspections and tests. This documentation helps trace defects back to specific processes or machinery and promotes accountability within the shop.
6. Employee Training: Invest in training programs for machinists to ensure they understand quality standards and how to achieve them. Well-trained staff are crucial for maintaining quality.
7. Feedback Loop: Establish a system for regular feedback on quality metrics from all stakeholders, including machinists and quality control personnel. This promotes a culture of continuous improvement.
Implementing these methods can significantly enhance quality control in machining operations, leading to improved product reliability and customer satisfaction.
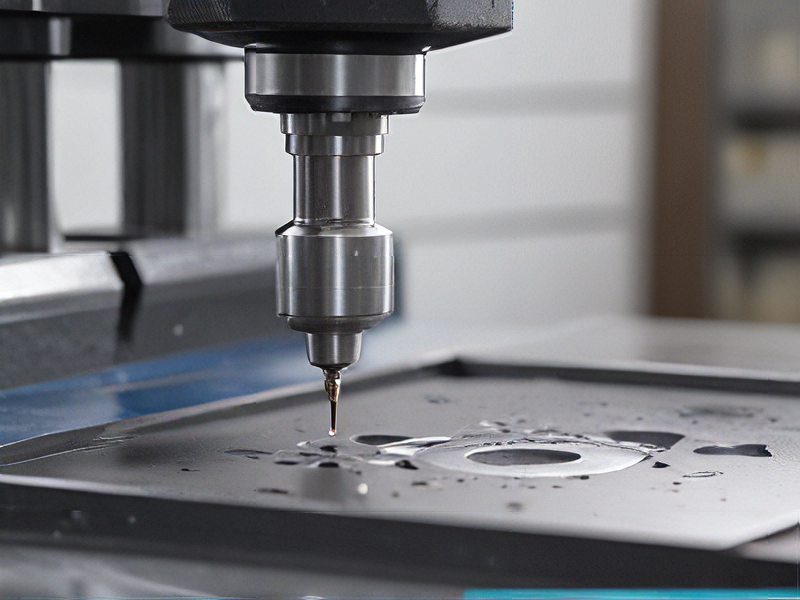
Tips for Procurement and Considerations when Purchasing from machining shop
When procuring from a machining shop, several key tips and considerations can ensure a successful purchasing experience:
1. Define Your Needs: Clearly outline your specifications, including materials, tolerances, finishes, and quantities. This helps the machining shop provide accurate quotes and streamline the process.
2. Research Shops: Evaluate potential vendors by checking their reputation, experience, and specialties. Look for shops with relevant certifications (e.g., ISO 9001) to ensure quality standards.
3. Request Samples: If possible, ask for samples or prototypes. This allows you to assess the quality of work and precision before committing to larger orders.
4. Get Multiple Quotes: Obtain quotes from several shops to compare pricing and capabilities. While cost is important, consider the overall value, including quality and delivery timelines.
5. Evaluate Lead Times: Discuss production timelines upfront. Machine shops may have varying workloads, so understanding their capacity will help avoid delays.
6. Establish Communication: Effective communication is key. Ensure that the machining shop understands your requirements and can provide updates throughout the process.
7. Discuss Payment Terms: Clarify payment terms before the project begins. Some shops might require deposits or milestone payments, while others may offer net terms.
8. Inspect Quality Control Processes: Inquire about the shop’s quality assurance measures. Understanding their inspection and testing processes helps ensure your products meet your standards.
9. Build Relationships: Establishing a good relationship with your chosen shop can improve collaboration and lead to better pricing and priority service in the future.
10. Plan for Contingencies: Consider potential issues such as material shortages or machine breakdowns, and have a contingency plan in place to mitigate disruptions.
By applying these tips and considerations, you can enhance your procurement process when purchasing from a machining shop.
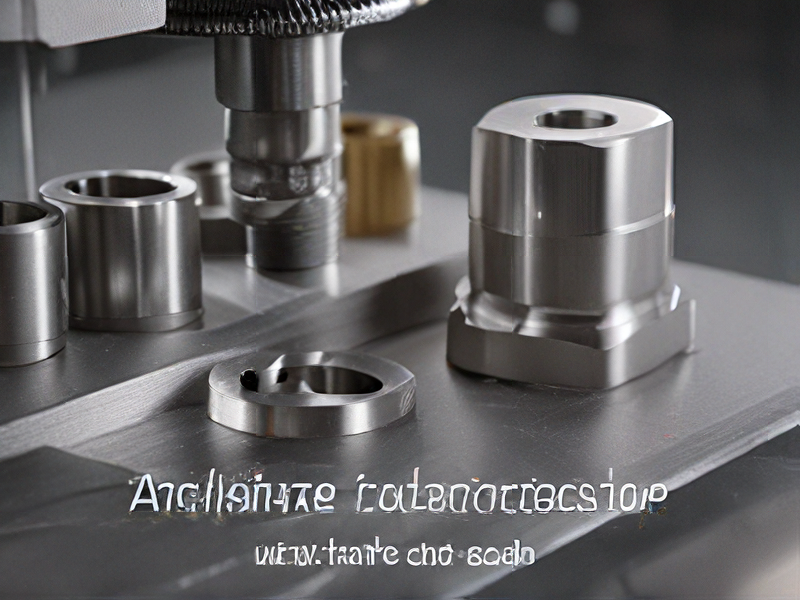
FAQs on Sourcing and Manufacturing from machining shop in China
FAQs on Sourcing and Manufacturing from a Machining Shop in China
1. Why choose a machining shop in China?
China offers competitive pricing, advanced technology, and a vast workforce, making it an attractive destination for sourcing precision machining services.
2. What types of machining services are available?
Common services include CNC machining, CNC turning, milling, electrical discharge machining (EDM), and surface finishing.
3. What materials can be sourced?
Machining shops can work with various materials such as aluminum, stainless steel, brass, plastic, and titanium.
4. How do I ensure quality control?
Request detailed quality assurance processes, ask for certifications (like ISO 9001), and consider third-party inspections before shipment.
5. What is the typical lead time for production?
Lead times vary based on complexity and order volume but usually range from 2 to 8 weeks. Consider clear communication of timelines.
6. How do I communicate my design requirements?
Provide detailed CAD drawings and specifications. Effective communication, potentially through an intermediary, can help avoid misunderstandings.
7. What are the minimum order quantities?
Minimum order quantities (MOQs) differ by supplier, but many machining shops can accommodate small to medium-sized orders.
8. What is the payment process?
Common payment methods include bank transfers, credit terms, or PayPal, with many suppliers requesting a deposit before production.
9. Are there any hidden costs?
Be aware of potential extra costs like shipping, customs duties, and taxes. Always clarify these aspects upfront.
10. How do I handle shipping?
Most suppliers can assist with logistics. Consider sea freight for larger orders to minimize costs but factor in longer shipping times.
By addressing these FAQs, businesses can navigate sourcing and manufacturing from Chinese machining shops more effectively.
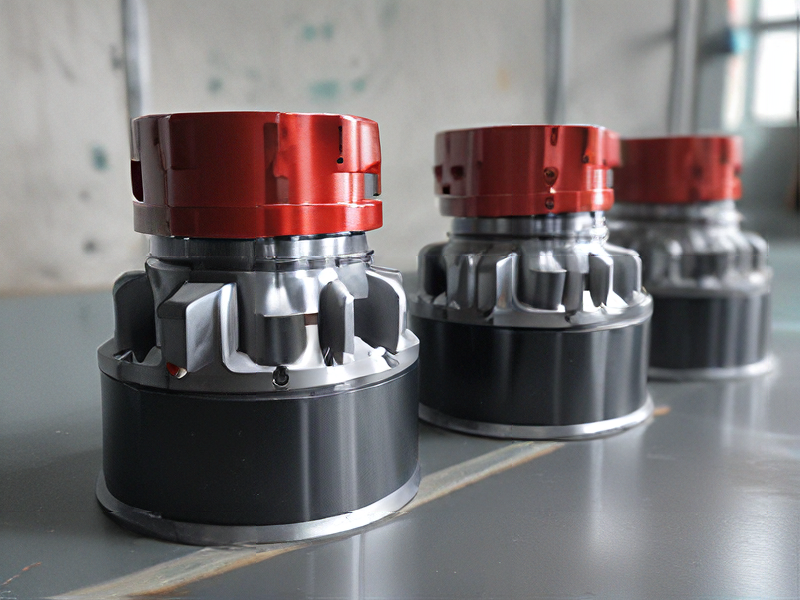