Technology and Applications of cnc meaning
CNC, or Computer Numerical Control, refers to the automated control of machine tools through a computer system. It allows for the precise machining of materials like metal, wood, and plastic by interpreting 2D or 3D designs into commands that direct the movement of cutting tools with high accuracy.
Applications of CNC:
1. Manufacturing: CNC machines are widely used in the production of components for various industries, including aerospace, automotive, and electronics. They enable mass production with consistent quality and minimal waste.
2. Prototyping: Designers and engineers employ CNC technology to create prototypes quickly, allowing for rapid testing and iteration of designs before moving to full-scale production.
3. Woodworking: CNC routers are essential for cutting, shaping, and engraving wood, facilitating complex designs that would be difficult to achieve manually.
4. Medical Devices: CNC technology plays a critical role in producing intricate components for medical devices, where precision is paramount.
5. Art and Sculpture: Artists utilize CNC machines to create detailed sculptures and installations, blending technology with creativity.
6. Education and Training: CNC technology is increasingly incorporated into educational programs to prepare students for careers in manufacturing and engineering.
Benefits of CNC:
– Precision: CNC machines achieve high levels of accuracy, ensuring that parts are manufactured to exact specifications.
– Efficiency: Automation reduces manual labor and speeds up production processes, leading to cost savings.
– Flexibility: CNC systems can easily adapt to different tasks or products by changing the programming.
In conclusion, CNC technology is a transformative force in modern manufacturing and design, enabling increased productivity, precision, and creativity across numerous industries.
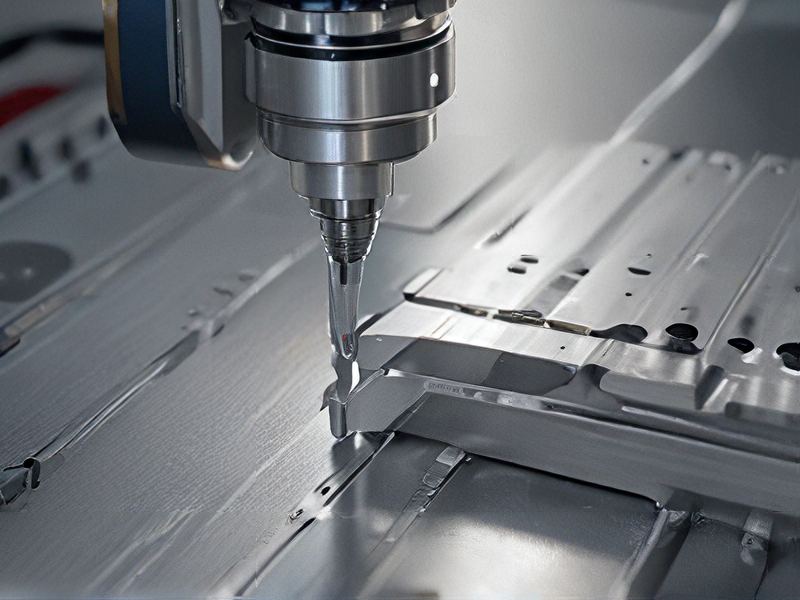
Quality Testing Methods for cnc meaning and how to control quality
Quality testing in CNC (Computer Numerical Control) machining is essential to ensure that parts meet specified tolerances and quality standards. Here are some key methods and controls used:
1. Dimensional Inspection: Utilizing micrometers, calipers, and CMM (Coordinate Measuring Machines) to measure finished parts against design specifications. This ensures that dimensions, tolerances, and geometries are within acceptable limits.
2. Visual Inspection: A quick method to detect surface defects such as scratches, dents, or irregularities. Experienced operators can often identify issues that might not meet aesthetic or functional standards.
3. Functional Testing: For components that require specific operational functions (like fittings), performing fit tests ensures that parts assemble correctly and operate as intended.
4. Material Verification: Testing the raw materials for hardness, tensile strength, and other properties ensures that they meet the required specifications before machining.
5. Non-Destructive Testing (NDT): Techniques such as ultrasonic, magnetic particle, or dye penetrant testing help to find internal defects without damaging the part.
6. Process Monitoring: Implementing real-time feedback systems during CNC machining can help monitor parameters like spindle speed, feed rates, and temperature, allowing immediate adjustments to prevent defects.
To control quality effectively, companies should utilize Statistical Process Control (SPC) methods, which analyze data from machining processes to identify trends and deviations. Regular training of personnel and adherence to ISO standards can further enhance quality assurance. By integrating these methods, manufacturers can achieve consistent quality in CNC machined parts, minimizing waste and maximizing customer satisfaction.
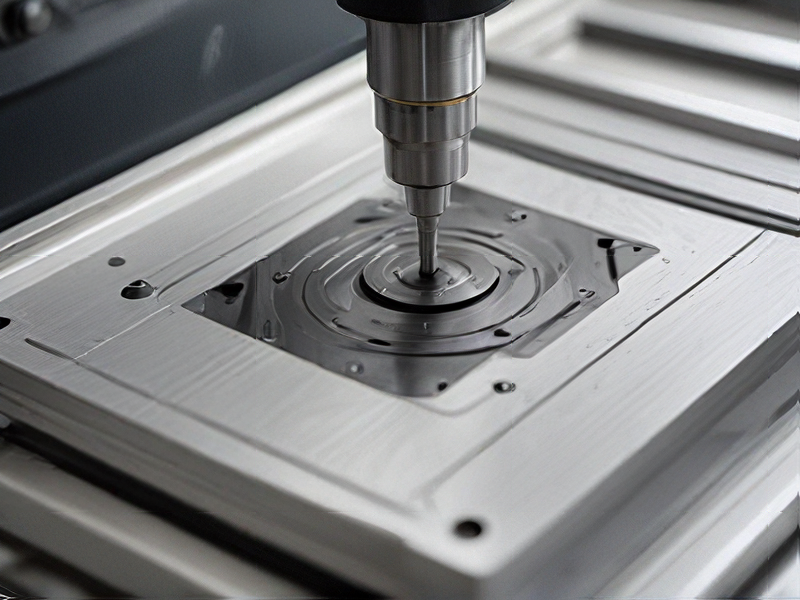
Tips for Procurement and Considerations when Purchasing from cnc meaning
Certainly! When considering procurement from CNC (Computer Numerical Control) suppliers, keep the following tips and considerations in mind:
1. Understand Your Requirements
– Define Specifications: Clearly define the specifications of your parts or services, including materials, dimensions, tolerances, and finishes.
– Volume Needs: Determine the quantity needed to assess production capacity.
2. Supplier Evaluation
– Reputation & Experience: Research suppliers’ reputation in the industry. Look for established firms with a strong portfolio and positive reviews.
– Certifications: Ensure suppliers have necessary certifications (e.g., ISO 9001) to ensure quality management and standards.
3. Cost Analysis
– Total Cost of Ownership: Evaluate not just the purchase price but also shipping, handling, and potential rework costs.
– Quotes Comparison: Request quotes from multiple suppliers to ensure competitive pricing.
4. Quality Assurance
– Sample Production: Request samples to evaluate the quality before committing to larger orders.
– Quality Control Processes: Inquire about the quality control measures employed to maintain standards during production.
5. Communication & Support
– Supplier Communication: Ensure there’s open and effective communication between your team and the supplier. Clarity can prevent mistakes.
– Technical Support: Assess the level of technical support the supplier offers, especially for complex projects.
6. Lead Times & Flexibility
– Delivery Times: Confirm lead times and evaluate the supplier’s ability to adapt to changes in demand or schedule shifts.
– Flexibility: Choose suppliers who can accommodate adjustments in orders without significant penalties.
Conclusion
A thorough evaluation process and an understanding of your needs ensure successful procurement from CNC suppliers, paving the way for long-term partnerships and quality outcomes.

FAQs on Sourcing and Manufacturing from cnc meaning in China
FAQs on Sourcing and Manufacturing CNC in China
1. What does CNC mean?
CNC stands for Computer Numerical Control. It refers to the automated control of machining tools (like drills, lathes, and mills) through computer programming.
2. Why source CNC manufacturing in China?
China offers competitive pricing, advanced manufacturing technology, and a vast workforce, making it an attractive option for businesses looking to reduce costs and increase production capacity.
3. What industries benefit from CNC manufacturing in China?
CNC manufacturing is used across various industries, including automotive, aerospace, electronics, and medical devices, providing precision parts and components crucial for these sectors.
4. How do I find a reliable CNC supplier in China?
Start by researching online platforms like Alibaba and Global Sources, checking reviews, and asking for certifications. Attending industry trade shows or fairs in China can also help you assess potential partners.
5. What are the common challenges when sourcing in China?
Language barriers, quality control, time zone differences, and variations in manufacturing standards can be challenges. It’s essential to conduct due diligence and consider working with local agents or consultants.
6. How can I ensure product quality?
Establish clear specifications, conduct factory audits, and implement quality control processes. It’s beneficial to have a third-party inspection service to verify product quality before shipment.
7. What is the typical lead time for CNC manufacturing in China?
Lead times can vary based on complexity and order size, but it usually ranges from a few weeks to a few months. Always confirm timelines with your supplier and plan accordingly.
8. Are there any legal considerations?
Understand intellectual property rights and ensure that you have non-disclosure agreements in place to protect your designs and proprietary information.
