Technology and Applications of meaning of cnc
CNC stands for Computer Numerical Control, a technology that automates machine tools through computer programming. It is widely used in manufacturing to enhance precision, efficiency, and scalability. CNC machines can operate lathes, mills, routers, and cutters, executing complex designs with minimal human intervention.
The primary advantage of CNC technology is its ability to produce intricate parts consistently, reducing the potential for human error. By translating designs created in Computer-Aided Design (CAD) software into precise movements, CNC machines can fabricate components from a variety of materials, including metals, plastics, and composites. This level of automation allows for rapid prototyping, mass production, and individualized products, catering to diverse industries such as aerospace, automotive, and medical devices.
CNC systems operate through a series of commands encoded in G-code, instructing the machine on how to move, what speed to use, and how deep to cut. This programmability enables quick modifications to designs, allowing manufacturers to adapt swiftly to changing market demands or custom requests.
Applications of CNC technology include everything from creating simple parts to complex assemblies. CNC machining centers can create automotive components, intricate jewelry designs, and even complex aerospace structures. Beyond traditional manufacturing, CNC is also applied in fields like woodworking, textile production, and even additive manufacturing, where CNC-controlled 3D printers produce layers of material.
In summary, CNC represents a significant advancement in manufacturing, empowering businesses to achieve greater productivity, precision, and flexibility while minimizing waste and labor costs.
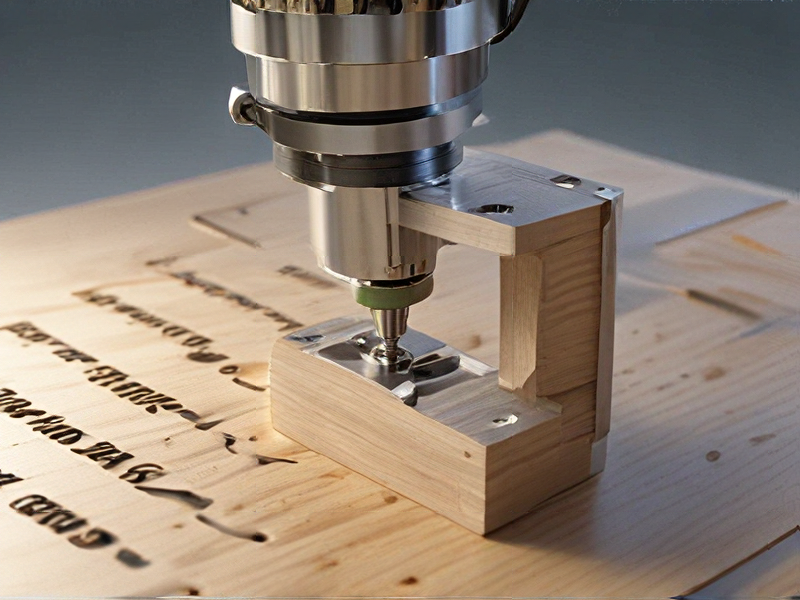
Quality Testing Methods for meaning of cnc and how to control quality
Quality Testing Methods for CNC (Computer Numerical Control)
CNC refers to the automation of machine tools using precise coded instructions. To ensure quality in CNC machining, several methods can be implemented:
1. Programming Verification: Before executing a CNC program, it’s crucial to verify the code for errors. Simulation software can mimic the machining process, allowing operators to catch mistakes that could lead to defects.
2. Tool Calibration: Regular calibration of CNC machines and cutting tools ensures consistent performance. Measuring tools against known standards helps maintain precision in dimensions and angles.
3. In-Process Inspection: Employing real-time measurement systems, such as laser scanners or touch probes, can detect deviations during production. This allows for immediate adjustments, minimizing waste and maintaining quality.
4. End-of-Process Inspection: Conducting thorough inspections of the final machined parts is essential. Techniques include dimensional measuring with calipers or micrometers, and surface finish analysis using roughness testers.
5. Statistical Process Control (SPC): Utilizing statistical methods to monitor and control production processes helps in identifying variations and trends. Control charts can signal when a process is going out of control, prompting immediate action.
6. Documentation and Standards Compliance: Adhering to industry standards (like ISO 9001) and maintaining thorough documentation of processes and results fosters accountability and consistency.
7. Feedback Loop: Establishing a feedback mechanism from inspection results to production adjustments helps continuously improve quality control measures.
By employing these methods, manufacturers can maintain high standards of precision and quality in CNC machining, ensuring products meet specified tolerances and customer expectations.
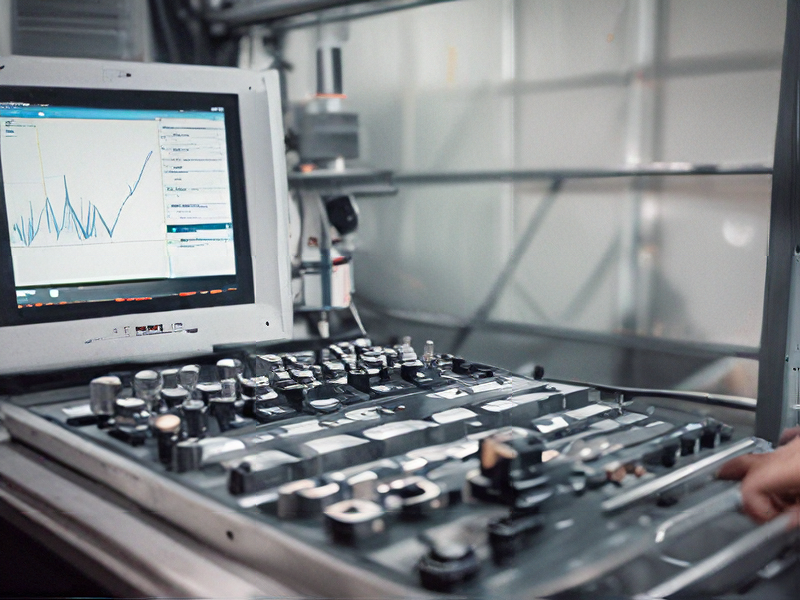
Tips for Procurement and Considerations when Purchasing from meaning of cnc
When procuring CNC (Computer Numerical Control) machinery, there are several key considerations to ensure successful purchasing and implementation:
1. Define Your Needs: Identify the specific applications for which the CNC machine will be used. Consider factors like material types, sizes, and complexity of parts to be produced.
2. Budgeting: Establish a budget that not only covers the purchase price but also includes installation, maintenance, tooling, and training costs.
3. Supplier Reputation: Research potential suppliers thoroughly. Look for reviews, testimonials, and case studies. A reputable supplier will offer customer support and have a track record of quality and reliability.
4. Machine Specifications: Assess the machine’s specifications, including spindle speed, axis movement, accuracy, and repeatability. Ensure the chosen machine meets your production requirements.
5. Technology Upgrades: Consider the availability of software and technology updates. CNC machines often benefit from the latest programming tools for improved efficiency.
6. Training and Support: Ensure the supplier provides adequate training for your team. Ongoing technical support is crucial for troubleshooting and maintenance.
7. Flexibility and Versatility: Look for machines that offer versatility in operations (e.g., milling, turning) and the ability to adapt to different projects.
8. Maintenance and Warranty: Review the warranty terms and maintenance options. A good warranty can save significant costs down the line.
9. Lead Times: Be aware of lead times for delivery and installation, especially if the machine is essential for meeting production deadlines.
By taking these considerations into account, you can make an informed decision that aligns with your operational goals and enhances productivity.
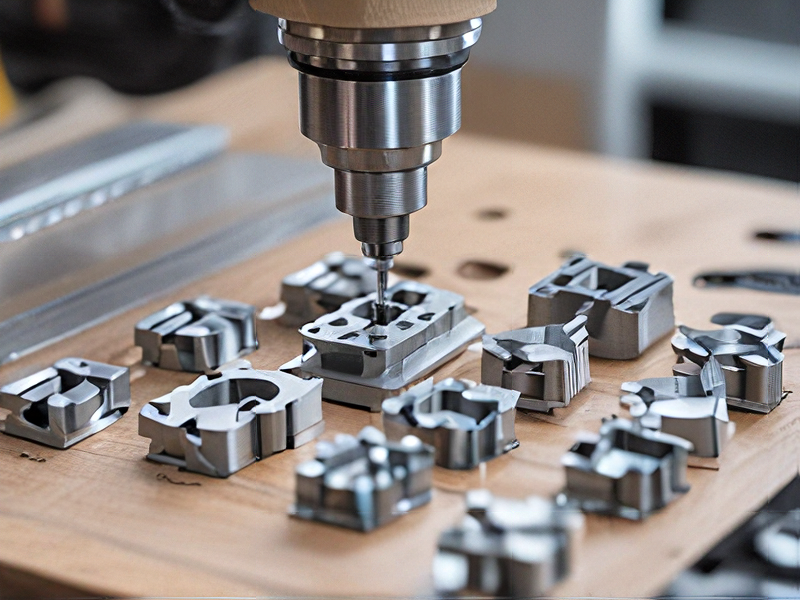
FAQs on Sourcing and Manufacturing from meaning of cnc in China
FAQs on Sourcing and Manufacturing in China
Q1: What does CNC stand for?
A1: CNC stands for Computer Numerical Control. It refers to the automated control of machining tools and 3D printers by computers. CNC machines can perform various tasks, including milling, turning, and laser cutting, with high precision.
Q2: Why source products from China?
A2: China is a global manufacturing hub known for its cost-effective production, vast supply chains, and skilled labor force. Sourcing from China can help businesses reduce costs and access a wide range of manufacturing capabilities.
Q3: What are the main advantages of CNC machining in China?
A3: CNC machining in China offers numerous benefits, including high precision, scalability, faster production times, and the ability to work with various materials. This technology allows manufacturers to create complex designs with tight tolerances.
Q4: How can I ensure product quality when sourcing from China?
A4: To ensure quality, it’s essential to conduct thorough research on potential suppliers, request samples, and perform factory visits or audits. Engaging third-party inspection services can also help verify product standards before shipment.
Q5: What should I be aware of regarding lead times?
A5: Lead times in China can vary based on factors like order size, complexity, and current factory workloads. It’s crucial to communicate clearly with your manufacturer about timelines and plan for potential delays.
Q6: How can I navigate customs and regulations when importing from China?
A6: Understanding customs regulations in your country is vital. Working with a freight forwarder or customs broker can streamline the import process and ensure compliance with all legal requirements.
By addressing these FAQs, businesses can better navigate the complexities of sourcing and manufacturing in China, particularly with CNC technologies.
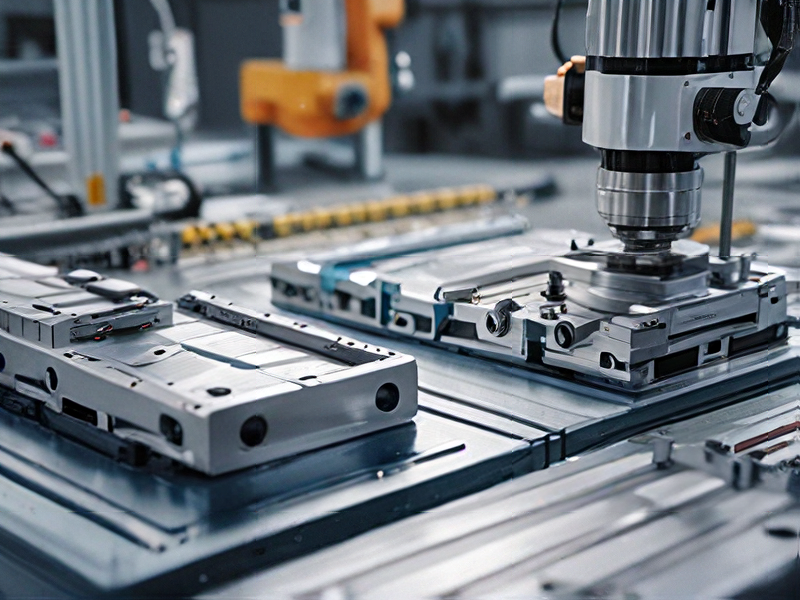