Technology and Applications of broach metal
Broaching is a machining process that utilizes a toothed tool, known as a broach, to remove material from a workpiece. This process is efficient for producing complex shapes and features, including keyways, splines, and various internal profiles. Broaches are typically made from high-speed steel (HSS) or carbide, providing durability and sharp cutting edges.
Technology of Broaching:
Broaching machines can vary in type, including vertical, horizontal, and rotary broaching systems. The broaching tool is designed with sequential teeth that progressively cut into the material, allowing for precise removal of material in a single pass. This technology is well-suited for mass production, as it maintains high accuracy and surface finish while significantly reducing cycle times compared to traditional machining methods.
Applications of Broaching:
Broaching finds extensive applications across various industries. It is commonly used in the automotive sector for manufacturing components like gears, camshafts, and various fasteners. In aerospace, broaching is critical for producing complex fittings and housings that require tight tolerances. Other applications include woodworking, manufacturing of medical devices, and the production of hardware and fixtures in construction.
Broaching’s ability to create intricate shapes efficiently, combined with its scalability for large production volumes, makes it a preferred choice in industries where precision and reliability are paramount. As industries continue to advance, the ongoing development of broaching tools and machines aims to enhance cutting efficiency and reduce operational costs, further solidifying broaching’s role in modern manufacturing processes.
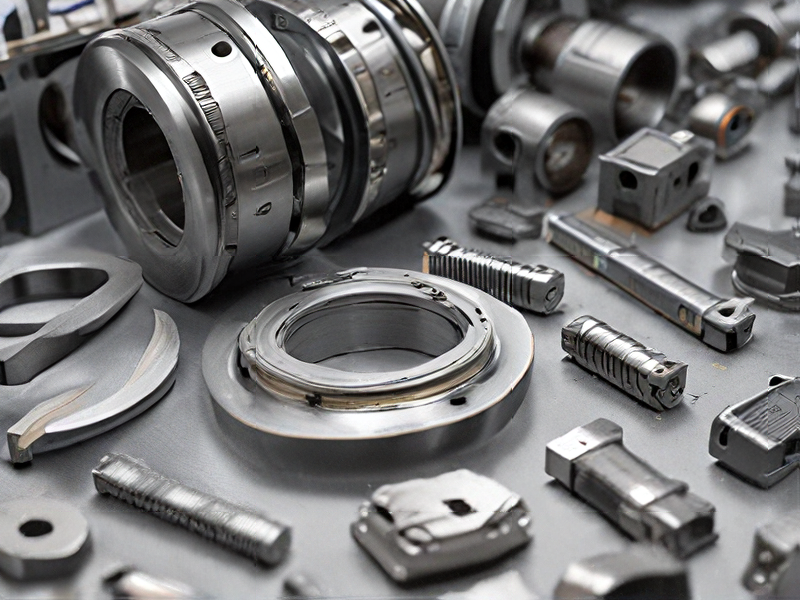
Quality Testing Methods for broach metal and how to control quality
Quality testing methods for broach metal are essential to ensure that these cutting tools meet performance and durability standards. Key methods include:
1. Visual Inspection: Before any mechanical testing, a thorough visual inspection is crucial. Inspect for surface defects such as cracks, voids, or irregularities that may affect performance.
2. Hardness Testing: Hardness can be evaluated using Rockwell, Brinell, or Vickers tests. These methods provide insights into the broach’s material properties and its ability to withstand wear during cutting operations.
3. Microstructure Analysis: Metallographic examination through microscopy helps assess the grain structure, phase distribution, and any inclusions. This analysis is vital for understanding tensile strength and ductility.
4. Tensile Testing: Performing tensile tests assesses the yield strength, ultimate tensile strength, and elongation, providing data on how the broach will perform under operational stress.
5. Dimensional Inspection: Using precision measurement tools, check the geometry of the broach to ensure it meets specifications. Consistency in dimensions affects cutting precision.
To control quality, implementing an effective quality management system (QMS) is critical. This includes:
– Standard Operating Procedures (SOPs): Establish clear protocols for production and testing processes to ensure consistency.
– Training Programs: Staff should receive training on quality standards, testing methods, and problem identification.
– Regular Audits: Conduct internal audits to assess compliance with QMS and identify areas for improvement.
– Feedback Loops: Encourage feedback from operators and engineers to continuously refine processes based on real-world performance.
By employing these testing methods and quality control measures, manufacturers can ensure the reliability and effectiveness of broach metals in their applications.

Tips for Procurement and Considerations when Purchasing from broach metal
When procuring broach metal, consider the following key tips and considerations:
1. Material Specifications:
– Choose the Right Alloy: Understand the specific metal alloy required for your project (e.g., high-speed steel, carbide). Different alloys offer varying hardness, wear resistance, and machinability.
– Tolerance Requirements: Ensure that the materials meet your tolerance specifications to avoid issues in production.
2. Supplier Selection:
– Reputation: Select suppliers with a solid reputation for quality and reliability. Research their history and customer feedback.
– Certifications: Check for relevant certifications (e.g., ISO, ASTM) that demonstrate adherence to industry standards.
3. Cost-Effectiveness:
– Total Cost of Ownership: Look beyond the initial price. Factor in maintenance, durability, and potential downtime.
– Bulk Purchasing: Consider buying in bulk to reduce costs, but ensure it aligns with your production needs and storage capabilities.
4. Lead Times:
– Delivery Times: Confirm the delivery timelines, especially if you have tight production schedules.
– Flexibility: Ensure suppliers can accommodate changes in order volume or specifications.
5. Technical Support:
– Expertise: Evaluate the technical support available from suppliers for troubleshooting and guidance on broaching processes.
– Customization Options: Discuss potential customization of materials or dimensions to suit specific applications.
6. Sustainability:
– Recycling Options: Investigate if the supplier offers recycled metals or sustainable practices to reduce your environmental footprint.
By carefully considering these aspects, you can enhance your procurement process and ensure you select the right broach metal for your needs.
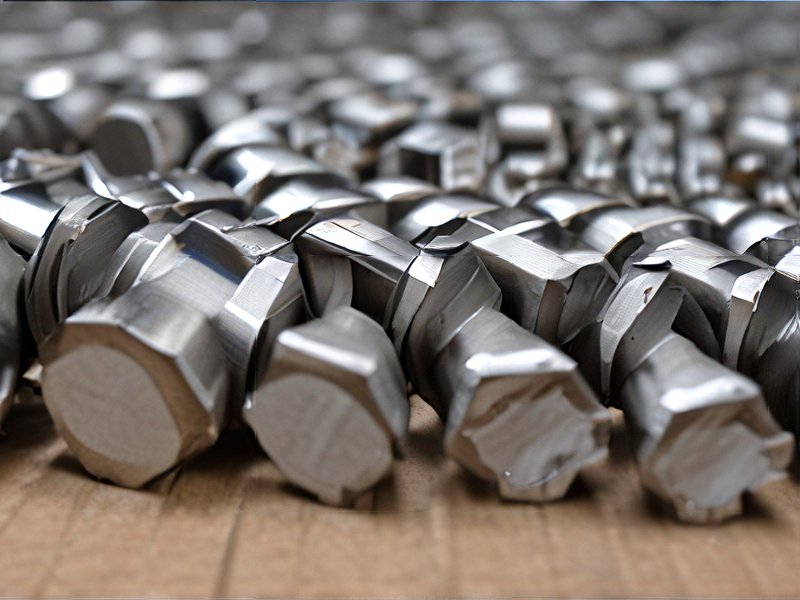
FAQs on Sourcing and Manufacturing from broach metal in China
FAQs on Sourcing and Manufacturing Broach Metal in China
1. What is broach metal?
Broach metal refers to the materials used in manufacturing broaches, which are tools for shaping and cutting materials. Common materials include high-speed steel, carbide, and tool steel.
2. Why source broach metal from China?
China offers competitive pricing, a wide range of manufacturing capabilities, and a large pool of skilled labor. This makes it an attractive option for sourcing metal and tools like broaches.
3. What should I look for in a manufacturer?
When selecting a manufacturer, consider factors such as industry experience, production capacity, quality certifications (ISO, etc.), lead times, and customer reviews. A good manufacturer should also be able to provide samples.
4. How do I ensure quality control?
Establish clear quality standards and maintain regular communication with the manufacturer. Consider hiring a third-party inspection service to verify product quality before shipment.
5. What are the minimum order quantities (MOQs)?
MOQs can vary significantly among manufacturers. Some might accept small batches, while others may require larger orders. It’s advisable to discuss this during initial negotiations.
6. How do I handle shipping and logistics?
Work with a reliable freight forwarder who understands customs regulations and can navigate the logistics process efficiently. Clarify shipping terms (FOB, CIF, etc.) with your supplier.
7. Is it safe to work with Chinese manufacturers?
While many reputable manufacturers exist, due diligence is crucial. Research potential partners, visit factories if possible, and utilize legal contracts to protect your interests.
8. What are payment options?
Common payment methods include wire transfers, PayPal, or letters of credit. Discuss secure options with your supplier to prevent fraud.
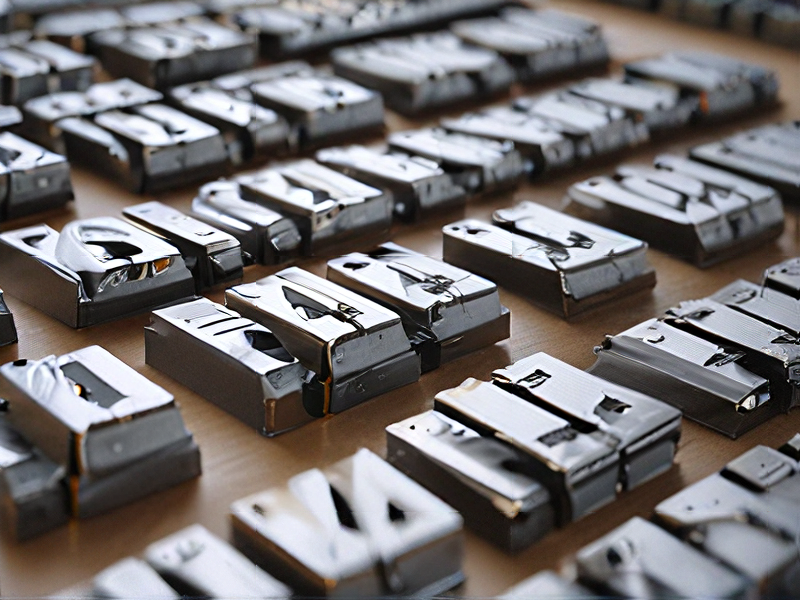