Technology and Applications of cnc machining milling
CNC (Computer Numerical Control) machining, particularly milling, is a revolutionary manufacturing process that automates the manipulation of tools to shape and cut materials with precision. Utilizing a computer program, CNC milling machines can produce complex parts by controlling the movement of a cutting tool along multiple axes (typically 3, 4, or 5).
The technology behind CNC milling involves several key components, including the CNC controller, which interprets the design files (often in G-code format), and the milling machine itself, equipped with a rotating cutting tool that removes material from the workpiece. The ability to operate along multiple axes allows for intricate designs and tight tolerances, making CNC milling suitable for aerospace, automotive, medical, and consumer products.
Applications of CNC milling are vast. In aerospace, precise component fabrication is crucial for safety and efficiency, while in the automotive industry, it is used to produce engine parts and prototypes. The medical field benefits from the creation of custom implants and surgical instruments, ensuring high standards for biocompatibility and precision.
Furthermore, CNC milling enhances flexibility in production, as designs can be easily modified in the software without the need for redesigning physical tools. This adaptability, combined with reduced waste and increased production speed, positions CNC milling as a vital process in modern manufacturing.
Overall, CNC milling underscores the significance of automation in achieving high-quality, cost-effective production, while meeting the increasingly complex demands of various industries.
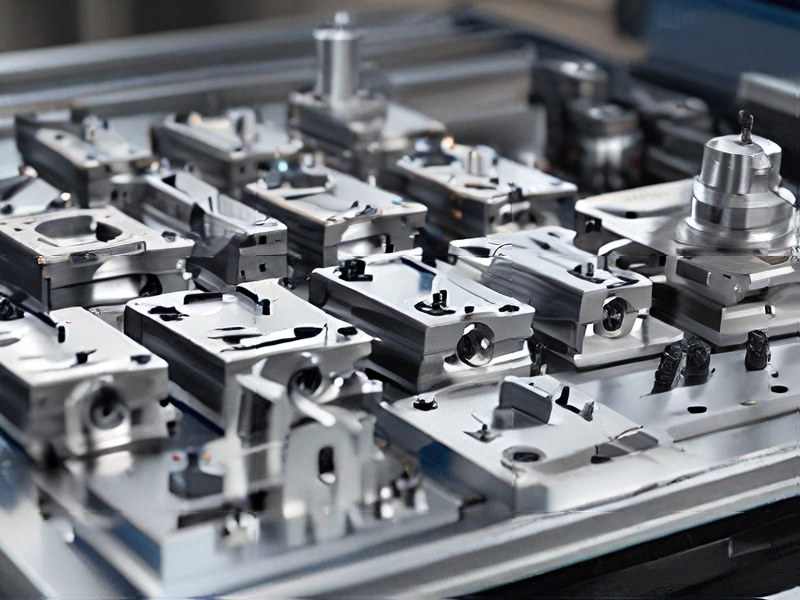
Quality Testing Methods for cnc machining milling and how to control quality
Quality testing in CNC machining milling is crucial to ensure dimensional accuracy, surface finish, and overall integrity of the manufactured parts. Effective methods and controls include:
1. Dimensional Inspection: Utilize precision measuring tools such as calipers, micrometers, and coordinate measuring machines (CMM) to verify that the machined parts meet specified tolerances. Conduct dimensional checks at various stages of the milling process.
2. Visual Inspection: Regularly inspect parts for visible defects like burrs, chips, and surface irregularities. This can be done with the naked eye or magnifying tools.
3. Surface Roughness Measurement: Employ a surface roughness tester to assess the quality of the surface finish. This ensures that the surface meets customer specifications for texture and smoothness.
4. Tooling Inspection: Regularly monitor and inspect cutting tools for wear and damage. Tool condition directly affects quality; hence, implementing a preventive maintenance schedule is crucial.
5. First Article Inspection (FAI): After initial production runs, perform a comprehensive inspection of the first part produced to verify all specifications are met before mass production begins.
6. Statistical Process Control (SPC): Utilize statistical methods to monitor and control the milling process. Track variations in dimensions over time and use control charts to analyze trends and ensure consistent quality.
7. Quality Management Systems (QMS): Implement a robust QMS such as ISO 9001 to establish standardized processes for quality assurance and continuous improvement.
By integrating these methods and controls, manufacturers can effectively manage and ensure the quality of CNC machined parts, minimizing defects and enhancing customer satisfaction.
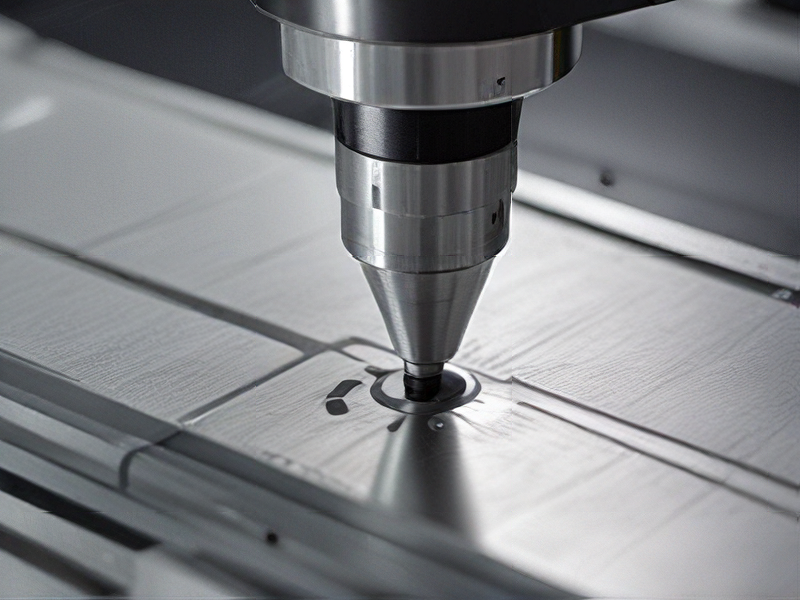
Tips for Procurement and Considerations when Purchasing from cnc machining milling
When procuring CNC machining and milling services, it’s essential to keep several key considerations in mind to ensure a successful purchase:
1. Supplier Evaluation: Research potential suppliers thoroughly. Check their reputation, certifications (e.g., ISO 9001), and customer reviews. Visit their facility if possible to assess their capabilities.
2. Capabilities and Equipment: Ensure the supplier has the right machines for your specific project, including the type of CNC machines they use. Verify that they are equipped to handle the materials you’re working with, whether metals, plastics, or composites.
3. Quality Assurance: Confirm that the supplier has robust quality control processes in place. Ask about their inspection methods and whether they can provide documentation like First Article Inspection (FAI) reports.
4. Lead Times and Capacity: Inquire about their production capacity and typical lead times. Consider how this aligns with your project timelines. A reliable supplier should be able to meet your deadlines consistently.
5. Cost Structure: Understand the pricing model. Get detailed quotations that outline costs associated with materials, setup, labor, and any additional services. Beware of hidden costs!
6. Communication: Choose a supplier who communicates clearly and promptly. Open communication is vital for addressing potential issues early on and ensuring the final product meets your specifications.
7. Prototype and Testing: If possible, start with a prototype. This allows you to evaluate the supplier’s quality and capabilities before committing to larger volumes.
8. Long-term Partnership: Look for a supplier with whom you can build a long-term relationship. Strong partnerships can lead to better pricing, priority service, and favorable terms as your needs evolve.
By considering these factors, you can make informed decisions that align with your manufacturing goals.
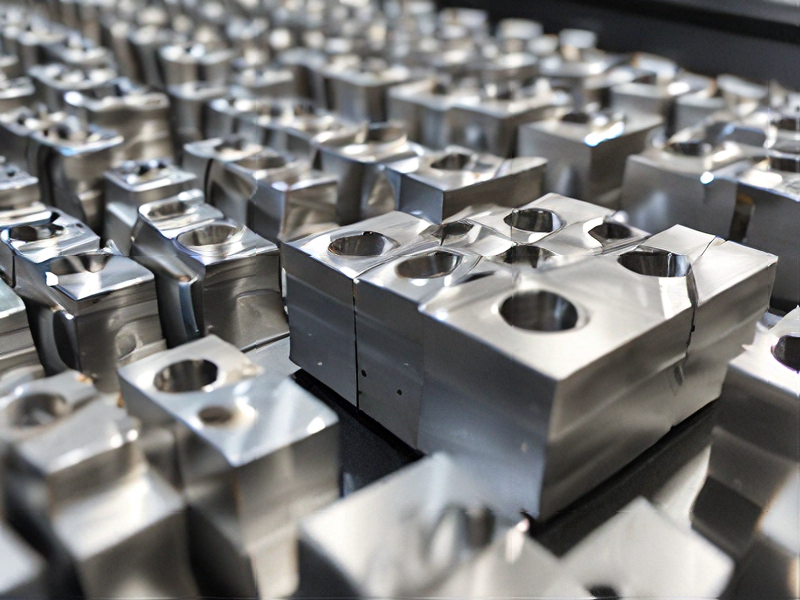
FAQs on Sourcing and Manufacturing from cnc machining milling in China
FAQs on Sourcing and Manufacturing CNC Machining Milling in China
1. What is CNC machining milling?
CNC (Computer Numerical Control) machining milling is a manufacturing process that utilizes computerized controls to operate machine tools. This allows for precise shaping of materials, commonly metals and plastics, to create complex parts.
2. Why source CNC machining in China?
China offers competitive pricing, advanced technology, and a vast manufacturing ecosystem. The country has skilled labor and a well-established supply chain, making it an attractive option for sourcing CNC machining services.
3. How do I find a reliable CNC machining manufacturer in China?
Start by researching online directories, trade shows, and industry associations. Verify manufacturer credentials through reviews, references, and certifications (like ISO). Consider visiting facilities if possible.
4. What are the minimum order quantities (MOQs)?
MOQs can vary by manufacturer but typically range from a few units to thousands, depending on the complexity of the part and the production process.
5. What lead times can I expect?
Lead times for CNC machining can range from a few days to several weeks, depending on the complexity of the parts, quantity, and the manufacturer’s workload.
6. How do I ensure quality control?
Request a quality assurance plan, including inspections and testing methods. Many manufacturers provide detailed quality reports and certifications upon request.
7. What are the shipping options?
Shipping can be done via air freight for quicker delivery or sea freight for cost efficiency. Ensure you factor in customs duties and logistics costs when planning.
8. What should I consider regarding intellectual property (IP)?
Protect your designs and patents by working with a reputable manufacturer and using non-disclosure agreements (NDAs). Always conduct due diligence before sharing sensitive information.
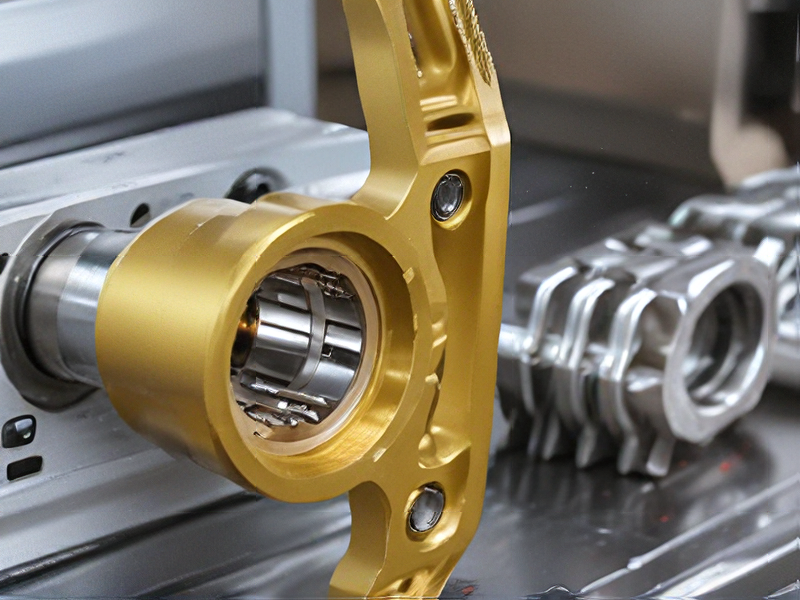