Technology and Applications of silk screening machines
Silk screening, or screen printing, is a versatile printing technique used to transfer designs onto various surfaces, including fabrics, plastics, glass, and metal. The process involves creating a stencil (or screen) that allows ink to pass through only where the design is intended, making it ideal for both small-scale and large-scale production.
Technology
Modern silk screening machines have evolved significantly, incorporating advanced technology such as automatic screen printing systems. These machines can streamline the process by offering features like multi-color printing, adjustable print speeds, and precise registration systems. Computerized systems enhance accuracy and allow for intricate designs, reducing the setup time and labor costs associated with manual printing.
Applications
1. Textiles: Widely employed in fashion and promotional wear, silk screening allows for bold, vibrant designs on T-shirts, hoodies, and other apparel.
2. Merchandising: It is prevalent in creating custom merchandise for events, brands, and bands, enabling businesses to expand their promotional capabilities.
3. Packaging: Screen printing is used to print labels and packaging materials, providing a durable and visually striking finish that enhances branding.
4. Electronics: Specialized screen printing techniques are used to apply conductive inks on circuit boards, making it crucial for the electronics industry.
5. Signage: Silk screening is commonly used for creating eye-catching signage and decals, making effective marketing tools for businesses.
In summary, silk screening machines combine traditional craftsmanship with modern technology, making them indispensable across various industries. Their ability to produce high-quality, detailed prints on a wide range of materials makes them a preferred choice for many applications.
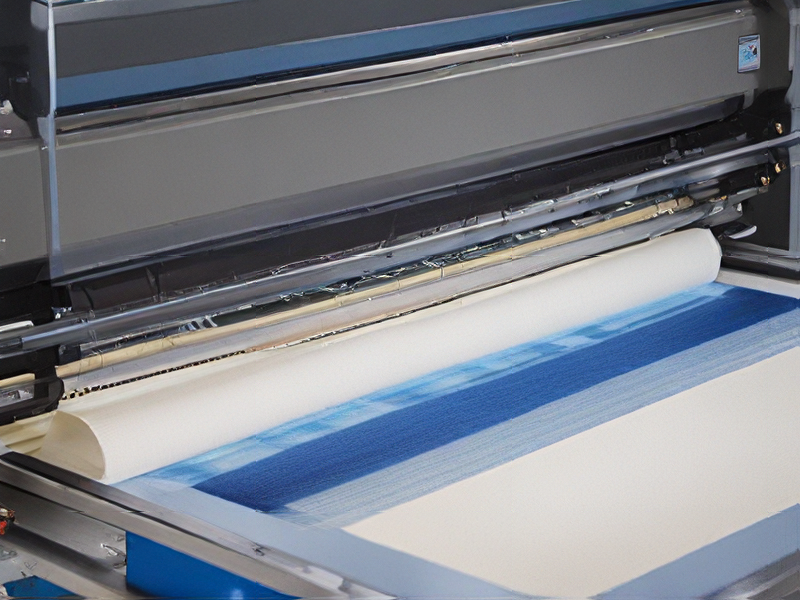
Quality Testing Methods for silk screening machines and how to control quality
Quality testing for silk screening machines is crucial to ensure precision and consistency in the printing process. Here are some effective methods and strategies to control quality:
1. Pre-Production Inspections: Before commencing production, inspect the silk screening machine for any physical damage or malfunctions. Check components like the squeegee, emulsion-coated screens, and the alignment mechanisms.
2. Calibration Checks: Regular calibration of the machine is essential. Use standardized test prints to verify that the machine is producing the correct colors, pressure, and registration. Adjust settings as needed to maintain precision.
3. Ink Consistency Tests: Conduct viscosity tests on inks used. Consistent viscosity ensures uniform flow during printing, which helps achieve consistent print quality.
4. Dot Gain Measurement: Monitor dot gain (the increase in the size of printed dots compared to the original design) by using a spectrophotometer. This helps in adjusting the screen exposure time and ink application.
5. Print Samples Analysis: After the first run, analyze print samples for color accuracy, registration, and finish quality. Compare with a control sample to check for discrepancies.
6. Routine Maintenance: Implement a regular maintenance schedule to clean and service the machines, which helps to prevent malfunctions and ensures longevity.
7. Training and Standard Operating Procedures (SOPs): Ensure that operators are well-trained on machine settings and quality standards. Develop clear SOPs for the entire printing process to maintain quality control.
8. Feedback System: Establish a system for gathering feedback from production staff and customers to identify potential quality issues quickly.
By employing these methods, manufacturers can enhance the reliability and quality of silk screening processes, ultimately reducing waste and increasing customer satisfaction.
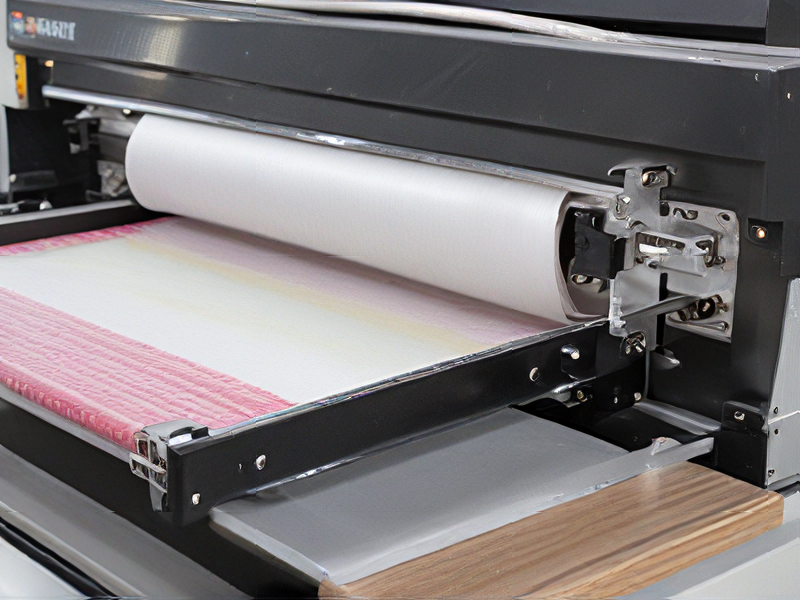
Tips for Procurement and Considerations when Purchasing from silk screening machines
When considering the procurement of silk screening machines, several essential tips and considerations can guide your decision-making process:
1. Understand Your Needs: Assess your production volume and the types of materials you will be printing on. Different machines cater to various needs – from small tabletop units for small businesses to larger industrial machines for mass production.
2. Budget: Establish a budget that includes not only the machine’s cost but also accessories, maintenance, and potential operational costs. Remember to consider both initial outlay and long-term operating expenses.
3. Machine Features: Look for key features like print size compatibility, speed, precision, and automation options. Machines with adjustable squeegee pressure and registration accuracy are particularly valuable for high-quality prints.
4. Quality and Brand Reputation: Research brands and manufacturers known for their reliability and customer support. Check reviews and testimonials from other users to gauge performance and durability.
5. Training and Support: Consider whether the manufacturer offers training and continued technical support. This is crucial, especially if your team is new to silk screening.
6. Warranty and Service Agreements: A robust warranty can provide peace of mind. Ensure you understand the terms and any service agreements offered.
7. Material Compatibility: Confirm that the machine can handle the inks and substrates you plan to use. Compatibility ensures optimal performance and print quality.
8. Future Scalability: Choose a machine that can grow with your business. If you anticipate increased production needs, consider models that offer upgrade options or expansion capabilities.
9. Environmental Considerations: Evaluate the machine’s environmental impact, such as energy consumption and ink waste. Opting for eco-friendly machines can enhance your brand’s sustainability efforts.
By carefully considering these factors, you can make a well-informed purchase that meets your business requirements and supports long-term growth.
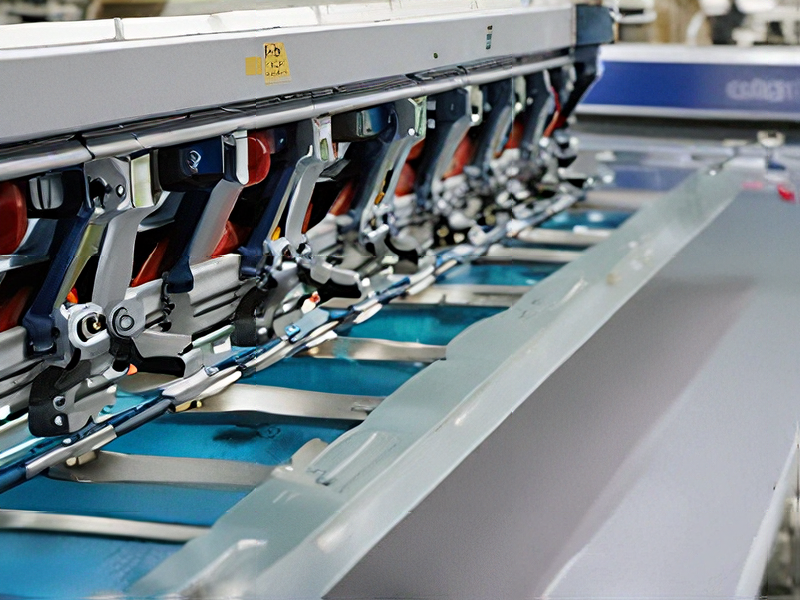
FAQs on Sourcing and Manufacturing from silk screening machines in China
FAQs on Sourcing and Manufacturing Silk Screening Machines in China
1. What is silk screening?
Silk screening, or screen printing, is a process where ink is pushed through a mesh screen onto a substrate, creating designs on materials like textiles, paper, and plastics.
2. Why choose China for sourcing?
China offers competitive pricing, a wide range of suppliers, advanced technology, and vast manufacturing capabilities. The country’s established infrastructure also supports efficient production and logistics.
3. How do I find reliable suppliers?
Utilize platforms like Alibaba, Global Sources, or local trade fairs. Check supplier credentials, read reviews, and request references. It’s beneficial to visit factories if feasible.
4. What should I consider in the manufacturing process?
Evaluate the manufacturer’s equipment, production capacity, quality control processes, and lead times. Ensure they can meet your specific requirements, including customization options.
5. What are common quality standards?
Look for ISO certifications and adherence to international quality standards. Request product samples for inspection before placing bulk orders.
6. What are the typical costs involved?
Costs can vary by machine type, features, and order quantity. Consider additional expenses like shipping, customs duties, and potential tariffs.
7. How do I ensure my designs are protected?
Register your designs and trademarks in China. Create Non-Disclosure Agreements (NDAs) with suppliers to safeguard your intellectual property.
8. What are the lead times for manufacturing?
Lead times vary based on order size and complexity. Generally, expect 4-8 weeks but confirm with your supplier.
9. What about after-sales support and maintenance?
Inquire about warranty policies, technical support, and availability of spare parts. A reliable manufacturer will offer comprehensive after-sales service.
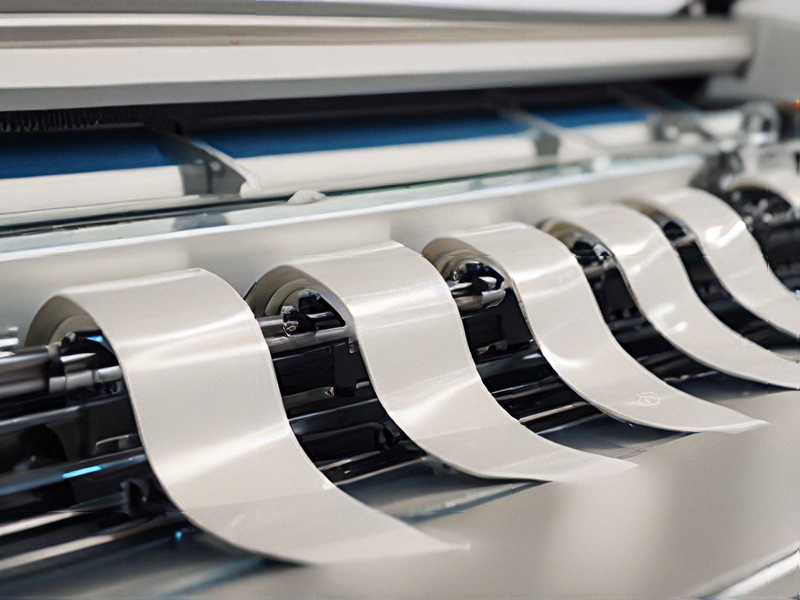