Technology and Applications of machining with a lathe
Machining with a lathe is a fundamental manufacturing process used to shape materials, primarily metals and plastics, into precise components. The lathe operates by rotating the workpiece against a stationary cutting tool, allowing for the creation of cylindrical shapes, threads, and complex geometries.
Technologies in Lathe Machining:
1. CNC Lathes: Computer Numerical Control (CNC) lathes have revolutionized traditional machining. They provide automated precision and consistency by executing complex programs for intricate parts. CNC lathes can handle multiple operations, such as milling and drilling, reducing the need for multiple machines.
2. Tooling Innovations: Modern lathes utilize advanced tooling materials, like carbide and ceramic inserts, which offer superior wear resistance and cutting performance. This extends tool life and reduces downtime for replacements.
3. Multi-Tasking Lathes: These machines combine the functions of a lathe and a milling machine, allowing machining of complex parts in a single setup. This diminishes the need for secondary operations and enhances production efficiency.
Applications of Lathe Machining:
1. Aerospace Components: Precision machining of flight-critical components, such as shafts and housings, where accuracy is paramount.
2. Automotive Parts: Manufacturing various engine components, axles, and gears that require high tolerance levels.
3. Medical Devices: Creating custom parts like surgical instruments and implants, often from exotic materials, which necessitate strict adherence to specifications.
4. Custom Fabrication: Lathes can be employed for prototyping and small-scale production, allowing for flexibility in design and rapid iteration.
In conclusion, lathe machining plays a crucial role across multiple industries, driven by technological advancements that enhance precision, efficiency, and flexibility in production processes.
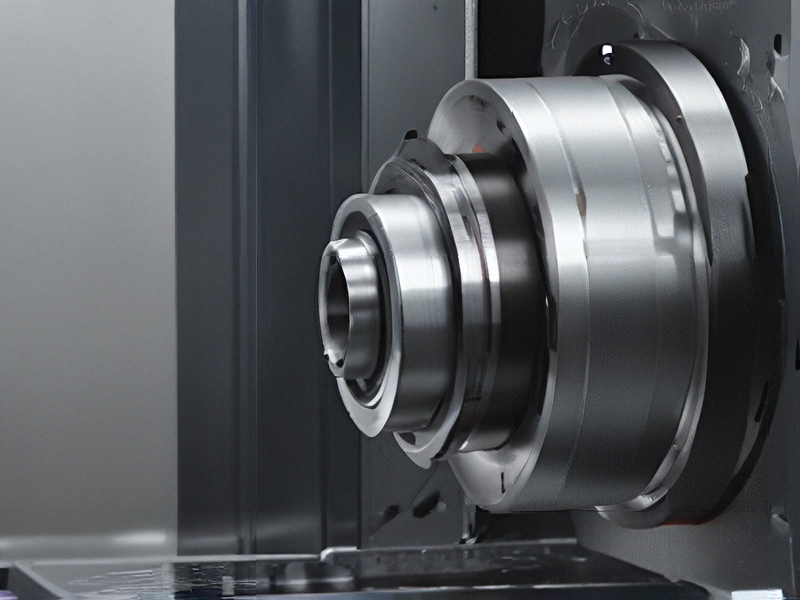
Quality Testing Methods for machining with a lathe and how to control quality
Quality testing in lathe machining is crucial for ensuring precision and compliance with specifications. Here are several effective methods to control quality:
1. Visual Inspection: This initial step involves checking for surface defects, tool marks, or inconsistencies. Operators should be trained to identify unacceptable finishes and other noticeable flaws.
2. Dimensional Measurement: Using tools like calipers, micrometers, or coordinate measuring machines (CMM), machinists measure critical dimensions (diameter, length, and tolerance) to ensure they meet design specifications.
3. Tolerancing: Ensure that tolerances are clearly defined in the design phase. Utilize geometric dimensioning and tolerancing (GD&T) to guarantee positional accuracy and relationships between features.
4. Surface Roughness Measurement: Employ a surface roughness tester to quantify the finish quality of the machined part. This measurement indicates how smooth the surface is, which may affect the part’s functionality.
5. GD&T Verification: This method uses visualization techniques to ensure features conform to specified geometric tolerances, often involving the use of fixtures or gages.
6. Non-Destructive Testing (NDT): Techniques such as ultrasonic testing or dye penetrant inspection can identify internal flaws without damaging the part, especially useful for critical components.
7. Statistical Process Control (SPC): Implement SPC to monitor and control the machining process. Collect data on key variables to identify trends and prevent defects proactively.
8. Process Audits: Regular audits of the machining process help verify that quality standards are maintained and identify potential areas for improvement.
By integrating these quality testing methods and controls, manufacturers can enhance the reliability of lathe machining operations and ensure that products meet required standards.
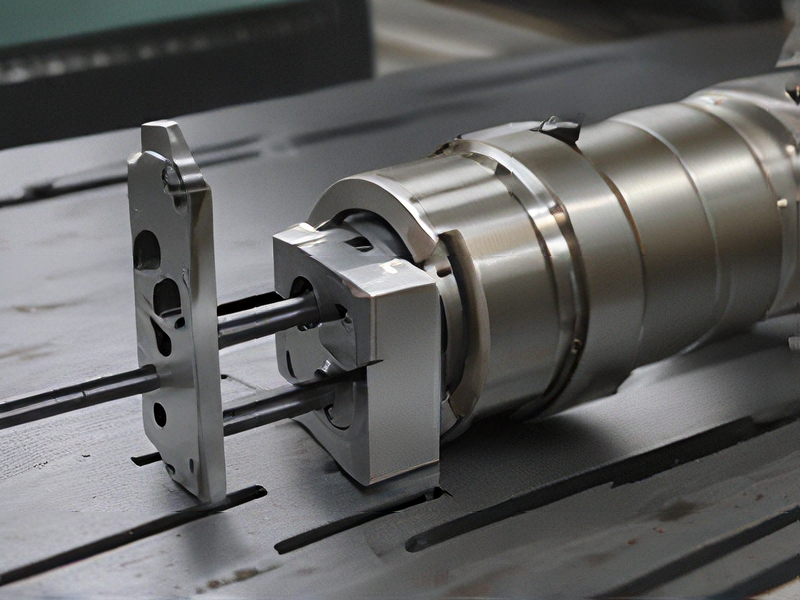
Tips for Procurement and Considerations when Purchasing from machining with a lathe
When procuring machining services using a lathe, several key considerations can help ensure a successful and cost-effective purchase:
1. Supplier Selection: Evaluate suppliers based on their technical capabilities, equipment quality, and industry experience. Look for those with a strong reputation and positive reviews from previous clients.
2. Material Requirements: Clearly specify the materials required for your project. Different lathes handle various materials differently, so ensure the supplier can work with your chosen material effectively.
3. Precision and Tolerances: Define the necessary precision and tolerances for your parts. Providing detailed specifications will help the supplier understand your quality requirements and avoid errors.
4. Lead Time: Discuss lead times during the procurement process. Ensure that the supplier can meet your deadlines and has a reliable schedule to reduce delays in production.
5. Capacity and Scalability: Consider the supplier’s production capacity and the scalability of their services. If you anticipate future increases in demand, ensure they can accommodate larger orders without compromising quality.
6. Costs and Payment Terms: Obtain detailed quotes that include all possible costs such as setup, material, labor, and shipping. Clearly outline payment terms to avoid misunderstandings.
7. Quality Assurance: Inquire about the supplier’s quality control processes and certifications. Ensure they have reliable methods in place to inspect and test finished products.
8. Post-Purchase Support: Understand the supplier’s policies regarding support, warranty, and maintenance for products purchased. This is crucial for resolving any issues that may arise after manufacturing.
By considering these factors, you can facilitate a smoother procurement process and establish a reliable partnership with your lathe machining supplier.
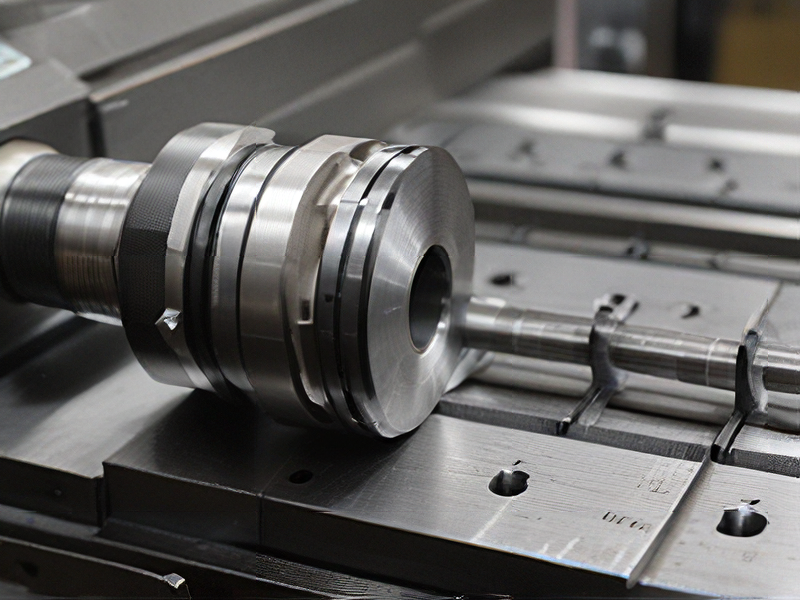
FAQs on Sourcing and Manufacturing from machining with a lathe in China
FAQs on Sourcing and Manufacturing with Lathes in China
#### 1. What is machining with a lathe?
Lathe machining is a manufacturing process where a workpiece is rotated against a stationary cutting tool to shape it into desired dimensions. It’s commonly used for cylindrical parts, such as shafts and bearings.
#### 2. Why source machining services in China?
China is a global manufacturing hub, known for its cost-effective production, advanced machinery, and skilled labor. Sourcing from China can significantly reduce manufacturing costs while maintaining quality.
#### 3. What should I consider when choosing a manufacturer?
– Quality Standards: Ensure they meet international standards (ISO, CE).
– Experience: Look for manufacturers with a proven track record in lathe machining.
– Capabilities: Verify they can handle your specific material and design requirements.
#### 4. How do I ensure quality control?
Implement a robust quality assurance process, including:
– Pre-production samples
– In-process inspections
– Final quality checks before shipment
Using third-party inspection services can also help.
#### 5. What are the shipping options?
Common shipping methods include air freight for quicker delivery and sea freight for larger volumes. Factors like urgency, cost, and destination will influence your choice.
#### 6. What about intellectual property protection?
Always have a Non-Disclosure Agreement (NDA) and ensure that your designs are protected. Research manufacturers who respect intellectual property rights.
#### 7. What are typical lead times?
Lead times can vary but generally range from 2 to 6 weeks depending on the complexity of the part and the manufacturer’s workload.
#### 8. How do I communicate my specifications?
Provide detailed technical drawings, specifications, and tolerances to ensure clarity. Using industry-standard formats (like CAD) is highly recommended.
By following these guidelines, you can successfully navigate sourcing and manufacturing lathe-turned parts in China.
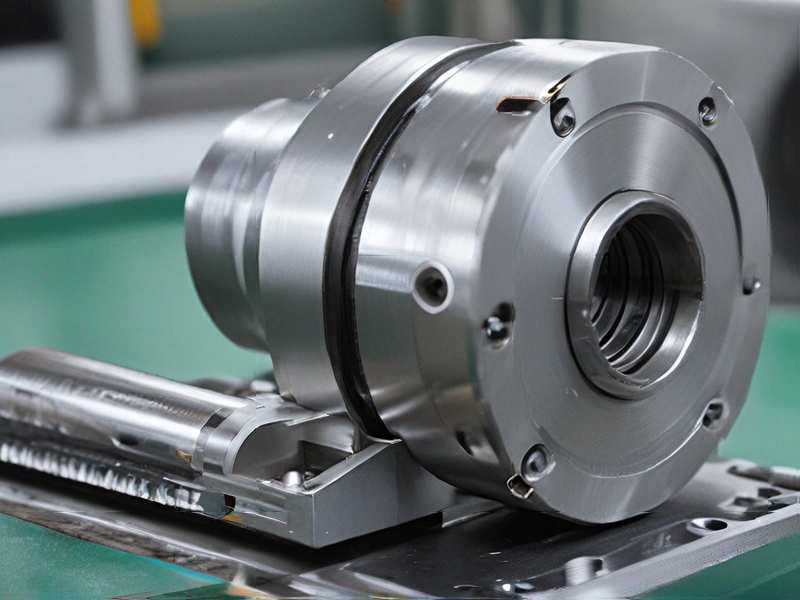