Technology and Applications of 3d printers that print metal
3D printing technology, particularly for metals, has revolutionized manufacturing processes across various industries. This technology, known as metal additive manufacturing, includes methods such as Powder Bed Fusion, Directed Energy Deposition, and Binder Jetting.
Powder Bed Fusion is the most widely used method, which involves fusing metallic powder layers using a laser or electron beam. This allows for high precision and the creation of complex geometries not possible with traditional machining processes. It’s particularly beneficial in aerospace and medical sectors, where customized parts are crucial.
Directed Energy Deposition employs a focused energy source, often a laser, to melt metal wire or powder as it’s deposited. This method is ideal for repairing existing components or adding details to parts, making it suitable for the aerospace industry and tooling applications.
Binder Jetting, another emerging method, utilizes a binder to join metal powder particles. Post-printing, the part undergoes sintering, where heat is applied to create a solid piece. This approach is cost-effective for producing large batches of parts with reduced material wastage.
Applications of metal 3D printing span from the creation of lightweight components in aerospace to custom implants in healthcare. The automotive industry also sees benefits in rapid prototyping and lightweight structures for improved fuel efficiency.
In addition, the ability to produce complex designs with minimal material means that metal 3D printing supports sustainability efforts. As technology advances, we can expect further integration of metal 3D printing into mainstream manufacturing, paving the way for innovative designs and improved efficiencies across sectors.
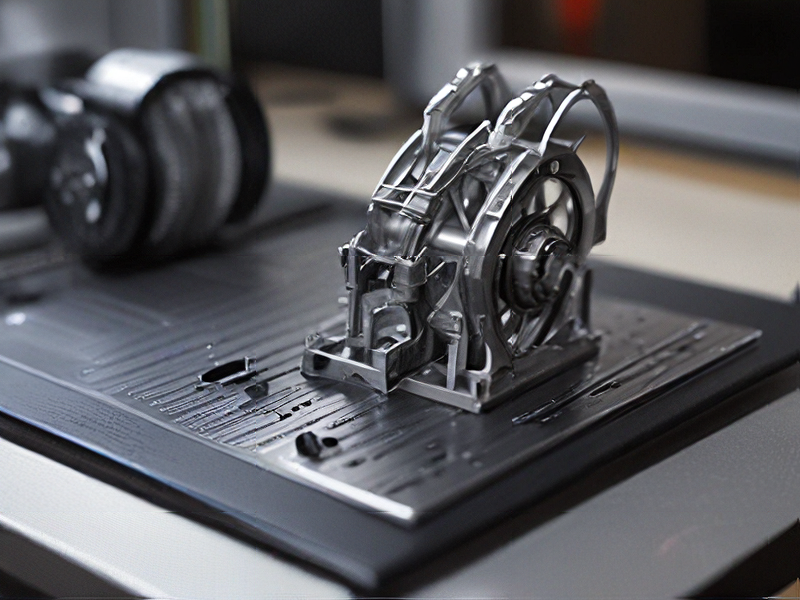
Quality Testing Methods for 3d printers that print metal and how to control quality
Quality testing methods for metal 3D printing involve a combination of in-process monitoring, post-process inspection, and testing to ensure that the final product meets desired specifications and standards. Here are key methods and strategies:
1. In-Process Monitoring: Implement real-time monitoring of the printing process through sensors that measure temperature, pressure, and laser intensity. This data helps detect anomalies during printing that could affect final part quality.
2. Visual Inspection: After printing, a visual inspection can identify surface defects such as warping, cracks, or incomplete layers. Advanced imaging techniques, like digital microscopy, enhance defect detection.
3. Dimensional Analysis: Use coordinate measuring machines (CMM) or laser scanners to compare the printed parts against CAD models. This ensures that the dimensions fall within specified tolerances.
4. Material Properties Testing: Conduct mechanical tests such as tensile, fatigue, and hardness testing to evaluate the material strength, ductility, and overall performance, ensuring they meet industry standards.
5. Non-Destructive Testing (NDT): Employ techniques like X-ray computed tomography (CT), ultrasound, or eddy current testing to identify internal flaws without damaging the part. This is critical for components used in safety-critical applications.
6. Post-Processing Control: Implement standardized post-processing methods (e.g., heat treatment, surface finishing) to improve microstructure and finish, ensuring consistency.
7. Traceability and Documentation: Maintain detailed records of each print job, including material batch numbers and process parameters, to allow for traceability and quality assurance.
By integrating these methods, manufacturers can effectively control the quality of metal 3D-printed parts, ensuring they meet necessary performance and safety criteria.
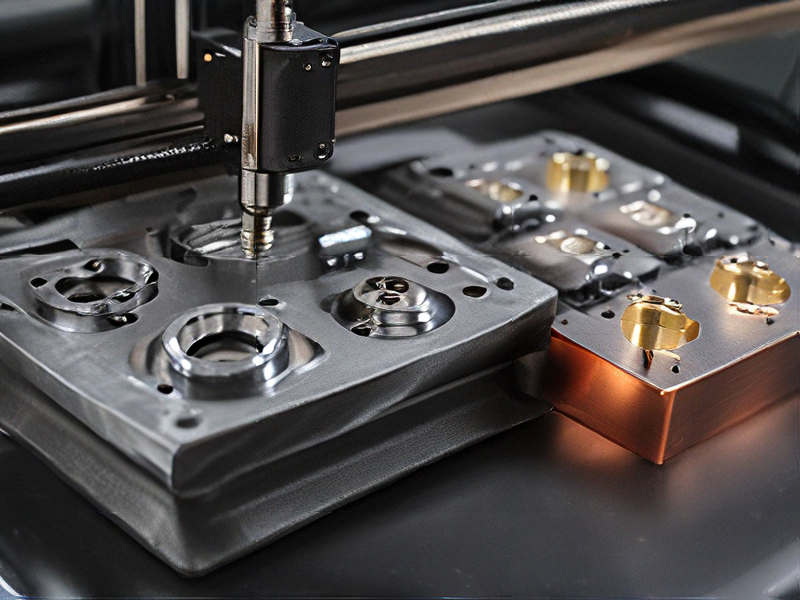
Tips for Procurement and Considerations when Purchasing from 3d printers that print metal
When procuring metal 3D printers, several key factors should be considered to ensure a successful investment:
1. Technology Type: Familiarize yourself with different metal printing technologies, such as Selective Laser Melting (SLM), Electron Beam Melting (EBM), and Metal Binder Jetting. Each has distinct capabilities and limitations suited to specific applications.
2. Material Compatibility: Evaluate the range of metals the printer can handle, like stainless steel, titanium, or aluminum. Ensure the printer supports the materials that are critical to your projects.
3. Build Size: Consider the maximum build volume. This will determine the size of parts you can produce, which should align with your projects’ specifications.
4. Print Quality & Resolution: Investigate the printer’s layer thickness and the resulting surface finish. Higher resolution may be necessary for intricate designs or functional parts.
5. Post-Processing Requirements: Understand the post-printing processes needed, such as heat treatment or machining, and whether the printer provider offers integrated solutions.
6. Cost of Operation: Assess operational costs, including material, maintenance, and energy consumption. A lower initial investment may lead to higher long-term costs.
7. Support and Training: Evaluate the manufacturer’s support services. Strong technical support and training can significantly reduce downtime and improve efficiency.
8. User Community and Resources: A robust community and available resources (like forums or tutorials) can be invaluable for troubleshooting and sharing best practices.
9. Regulatory Compliance: Ensure the printer meets relevant industry standards and regulations, especially if you are in sectors like aerospace or medical.
By carefully considering these aspects, you can make a more informed decision when purchasing a metal 3D printer tailored to your needs.
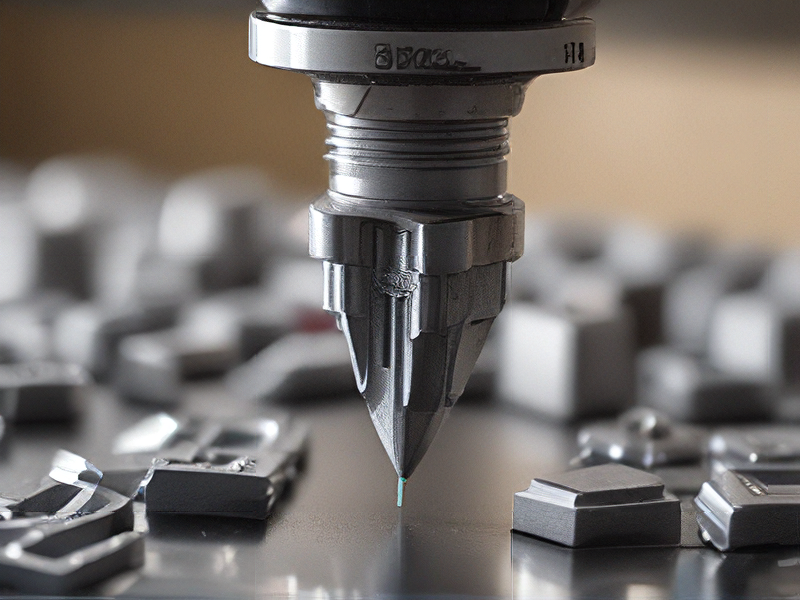
FAQs on Sourcing and Manufacturing from 3d printers that print metal in China
FAQs on Sourcing and Manufacturing with Metal 3D Printers in China
1. What types of metal can be printed using 3D printers in China?
Many 3D printers available in China can print with various metals, including stainless steel, titanium, aluminum, and cobalt-chromium. The choice depends on the printer technology and manufacturer.
2. What technologies are commonly used for metal 3D printing?
The most common technologies include Selective Laser Melting (SLM), Direct Metal Laser Sintering (DMLS), and Metal Binder Jetting. Each has unique benefits and suitable applications.
3. How does sourcing from China benefit my manufacturing processes?
Sourcing from China can reduce manufacturing costs, provide faster production times, and offer access to advanced technologies and skilled fabrication expertise.
4. What are the quality assurance measures in place?
Reputable manufacturers implement stringent quality control standards such as ISO certifications, material testing, and post-processing inspections to ensure high-quality outputs.
5. Can I get custom designs and prototypes?
Yes, many Chinese manufacturers specialize in customized designs and quick prototyping services. You must provide detailed specifications or CAD files for accurate production.
6. What are the lead times for metal 3D printing?
Lead times vary based on complexity and order size, typically ranging from a few days for prototypes to several weeks for larger production runs.
7. How do I navigate import regulations and shipping?
Collaborate with your manufacturer to ensure compliance with import regulations. Many companies offer logistics services to streamline shipping and customs clearance.
8. What post-processing options are available?
Post-processing services may include machining, surface finishing, heat treatment, and coating, enhancing the mechanical properties and aesthetics of printed parts.
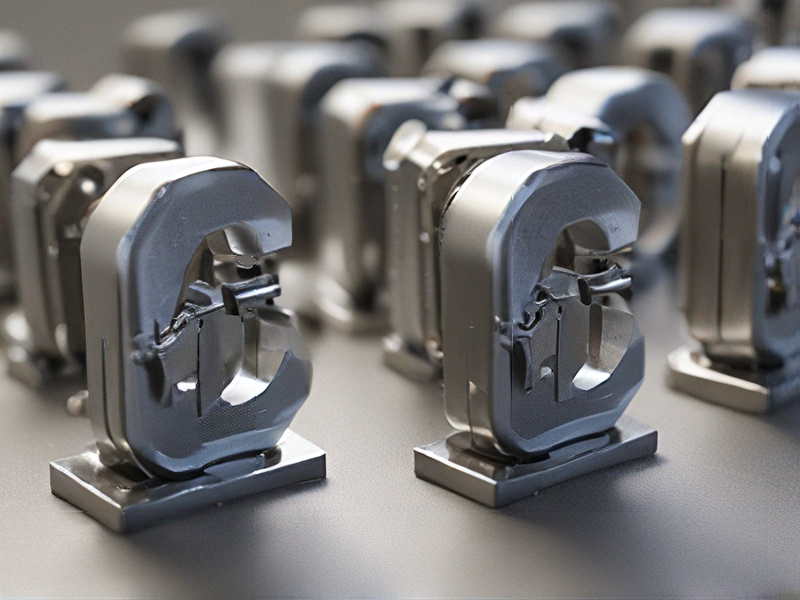