Technology and Applications of 3d printer printing metal
3D printing of metal, known as metal additive manufacturing, utilizes various technologies to create complex three-dimensional objects from metal powders. Key techniques include Selective Laser Melting (SLM), Electron Beam Melting (EBM), and Binder Jetting.
In SLM, a high-powered laser selectively melts powdered metal layer by layer, allowing high-resolution and dense component production. EBM, on the other hand, employs an electron beam in a vacuum to melt metal powders, enabling the fabrication of parts with superior mechanical properties, particularly for aerospace applications.
Binder Jetting combines a binding agent with metal powders. After printing, parts undergo a sintering process to fuse the material, offering versatility and the ability to produce intricate geometries.
Applications for metal 3D printing range across various industries. In aerospace, it enables the production of lightweight, complex components like turbine blades, significantly reducing material waste and manufacturing costs. The automotive industry benefits from rapid prototyping and the production of custom, high-performance parts. Healthcare sees advancements in tailored implants and surgical tools, improving patient outcomes.
Moreover, metal 3D printing facilitates low-volume production runs and customization, making it particularly valuable for industries requiring unique or specialized components. With the continuous evolution of materials like titanium, aluminum, and alloys, and the enhancement of additive manufacturing technologies, metal 3D printing is set to revolutionize manufacturing, driving innovation and efficiency across sectors.
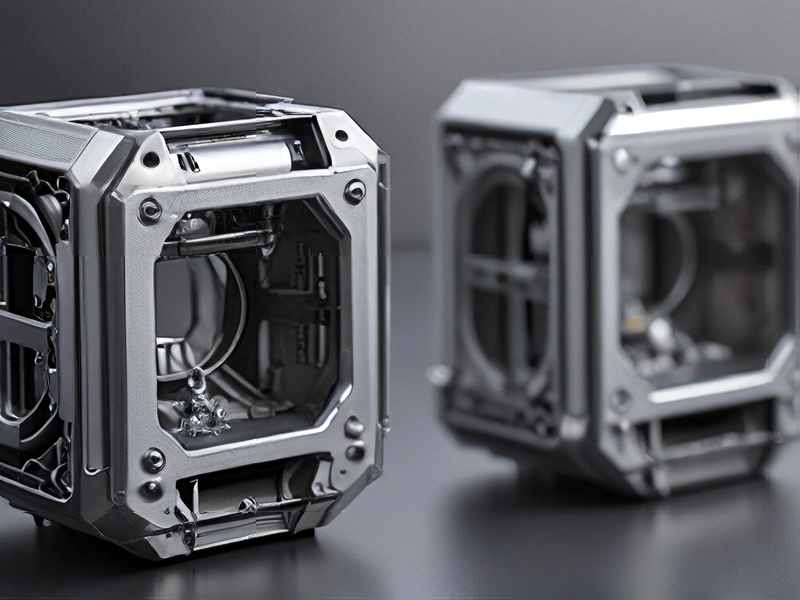
Quality Testing Methods for 3d printer printing metal and how to control quality
Quality testing of 3D-printed metal components is essential to ensure their reliability and performance. Here are some effective methods and strategies to control quality:
1. Visual Inspection: Start with a visual examination of the printed parts to identify surface defects, build anomalies, or signs of poor adhesion.
2. Dimensional Accuracy: Utilize calipers and coordinate measuring machines (CMM) to assess the dimensional tolerances of critical features, ensuring they meet specifications.
3. Mechanical Testing: Conduct tensile tests, hardness testing (e.g., Rockwell or Vickers), and fatigue tests to evaluate the material properties and mechanical performance.
4. Metallographic Assessment: Examine the microstructure using optical or scanning electron microscopy (SEM). Evaluate grain structure, porosity, and inclusions that could indicate issues in the printing process.
5. Non-Destructive Testing (NDT): Implement techniques like X-ray computed tomography (CT) and ultrasonic testing to detect internal defects such as voids or cracks without damaging the part.
6. Powder Quality Control: Monitor the quality of metal powder used for printing. Ensure consistency in particle size distribution, morphology, and chemical composition to prevent printing defects.
7. Process Monitoring: Utilize sensors and software for real-time monitoring of printing parameters (temperature, speed, layer thickness). Automated feedback systems can detect and rectify deviations during the printing process.
8. Post-Processing Verification: After post-processing treatments (e.g., heat treatment, surface finishing), perform further inspections to ensure the final properties align with design requirements.
Incorporating these methods into a comprehensive quality management system helps optimize the performance and reliability of 3D-printed metal parts, ultimately enhancing customer satisfaction and reducing costs associated with failures.
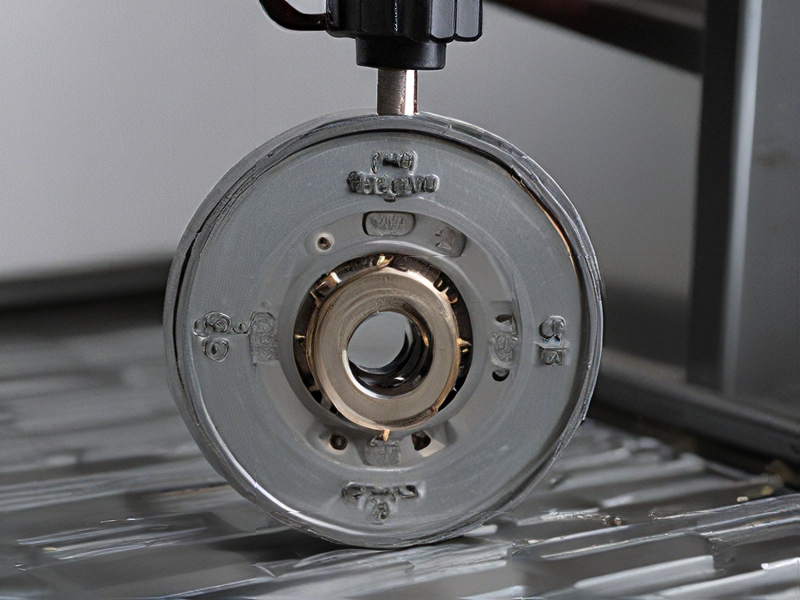
Tips for Procurement and Considerations when Purchasing from 3d printer printing metal
When purchasing a metal 3D printer, several key considerations and tips should be taken into account to ensure a successful procurement process:
1. Technology Understanding: Familiarize yourself with the different metal 3D printing technologies, such as Selective Laser Melting (SLM), Electron Beam Melting (EBM), and Binder Jetting. Each has unique advantages, limitations, and material compatibility.
2. Material Options: Assess the range of materials the printer can handle. Common metals include stainless steel, titanium, aluminum, and cobalt-chrome. Ensure the printer can accommodate the specific alloys required for your projects.
3. Print Quality and Resolution: Evaluate the printer’s specifications for layer thickness, build volume, and resolution. Higher precision may be essential depending on your application, so prioritize equipment that meets your required tolerances.
4. Post-Processing Requirements: Understand the post-processing needs of the printed parts, such as heat treatment, machining, or surface finishing. These can impact lead time and cost.
5. Cost of Ownership: Analyze the total cost, including the printer’s purchase price, maintenance, materials, and energy consumption. Sometimes, lower initial costs can lead to higher operating expenses.
6. Vendor Reputation and Support: Choose reputable manufacturers known for quality and customer support. Access to training, technical assistance, and a community of users can significantly enhance your experience.
7. Application Fit: Consider how the 3D printer fits into your overall production strategy. Ensure it aligns with your current capabilities and meets future scalability needs.
8. Regulatory and Certification: Ensure compliance with industry standards, especially if you plan to use the printed components in regulated sectors like aerospace or medical devices.
By carefully considering these factors, you can make an informed decision and enhance your operational efficiency in metal 3D printing.
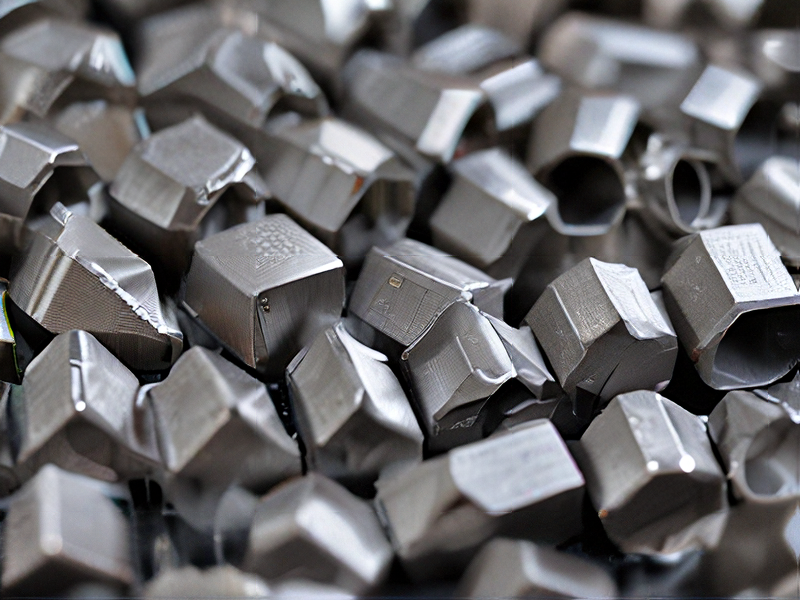
FAQs on Sourcing and Manufacturing from 3d printer printing metal in China
FAQs on Sourcing and Manufacturing with Metal 3D Printing in China
1. What is metal 3D printing?
Metal 3D printing, or additive manufacturing, involves creating metal parts layer by layer using techniques like Direct Metal Laser Sintering (DMLS) or Selective Laser Melting (SLM).
2. Why choose China for metal 3D printing?
China offers competitive pricing, advanced manufacturing technologies, and a broad network of suppliers and skilled labor. The rapid growth of the 3D printing industry has enabled China to become a global hub.
3. What materials are commonly used?
Common materials include stainless steel, titanium alloys, aluminum alloys, and cobalt-chrome. Each material has specific properties suited for different applications.
4. What industries benefit from metal 3D printing?
Industries such as aerospace, automotive, medical, and tooling frequently utilize metal 3D printing for custom parts, prototypes, and complex geometries.
5. How do I ensure quality control?
To ensure quality, partner with reputable manufacturers who follow strict standards (like ISO certifications) and implement quality assurance processes. Request samples and conduct factory audits if possible.
6. What is the typical lead time?
Lead times vary based on complexity and volume, but generally range from a few weeks to several months. Discuss timelines with your manufacturer upfront.
7. What are the costs associated with metal 3D printing?
Costs depend on design complexity, material selection, and production volume. Initial setup and post-processing may also affect overall pricing.
8. Can I get support with design?
Many manufacturers offer design assistance, including optimizing parts for 3D printing. Collaborate early in the process to enhance manufacturability.
By partnering with an experienced manufacturer in China, businesses can leverage the benefits of metal 3D printing for innovative solutions.
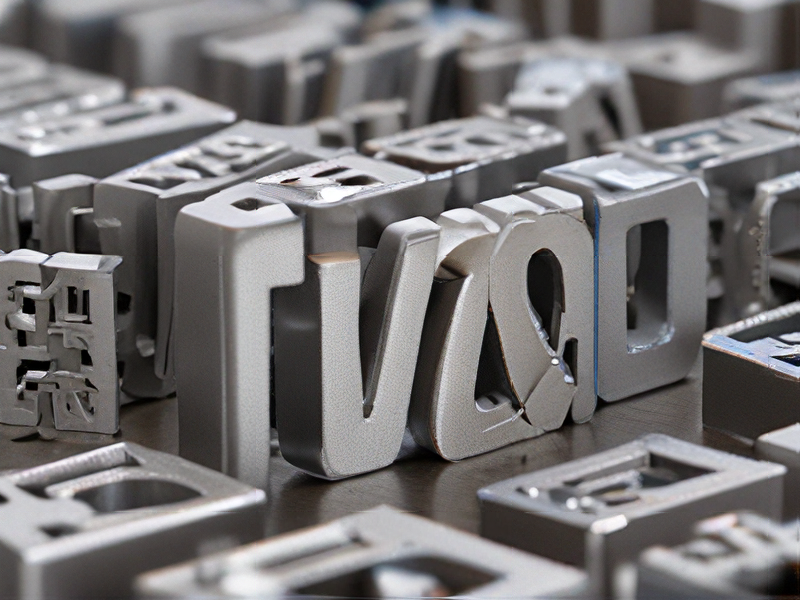