Technology and Applications of 3d print on metal
3D printing, or additive manufacturing, has revolutionized the production of metal parts, offering unique advantages in various industries. Key technologies include Selective Laser Melting (SLM), Electron Beam Melting (EBM), and Direct Metal Laser Sintering (DMLS). These methods use high-energy beams to fuse metal powders layer by layer, creating intricate geometries that are often impossible to achieve with traditional subtractive manufacturing.
One significant application of metal 3D printing is in aerospace, where lightweight, complex components can enhance fuel efficiency and performance. Boeing and Airbus, for instance, utilize 3D-printed parts for their aircraft, significantly reducing material waste and lead times. Similarly, the automotive industry leverages this technology for both prototyping and producing end-use components, such as custom brackets and structural parts, which also leads to weight reduction and improved performance.
Moreover, the medical sector benefits from personalized implants and prosthetics tailored to individual patient anatomies, improving patient outcomes and recovery times. In the energy sector, companies employ metal 3D printing for producing heat exchangers and turbine blades that withstand extreme conditions, enhancing efficiency and longevity.
Despite the advantages, challenges remain, including the high costs of metal powders and the necessity for advanced post-processing techniques to ensure optimal mechanical properties. Nonetheless, ongoing research and development promise to overcome these hurdles, further expanding the applicability of metal 3D printing across diverse sectors, making it a game-changer in modern manufacturing. As the technology matures, we can expect increased accessibility and a broader range of uses, positioning metal 3D printing at the forefront of industrial innovation.
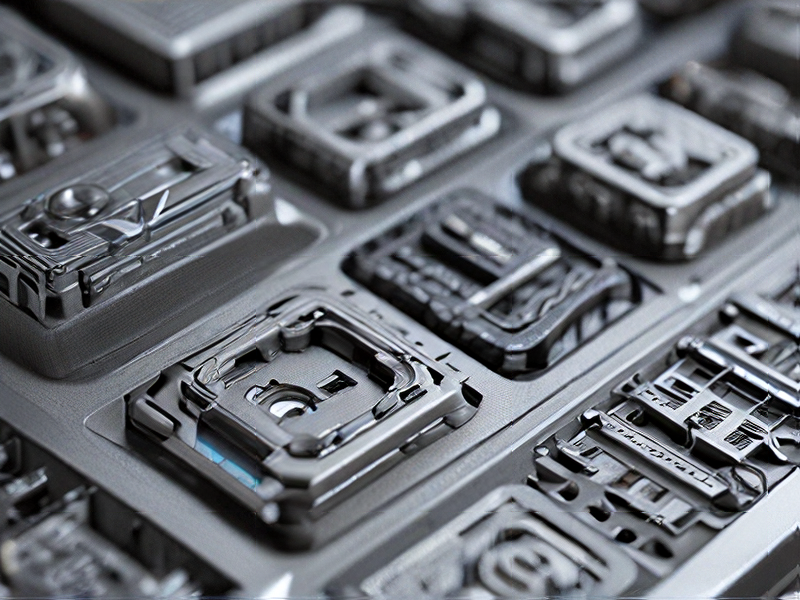
Quality Testing Methods for 3d print on metal and how to control quality
Quality testing for 3D-printed metal parts is crucial to ensure structural integrity and performance. Several methods can be employed to assess the quality of these components:
1. Visual Inspection: Initial checks for surface defects, layer adhesion, and overall finish can often be performed by simple visual inspection.
2. Dimensional Accuracy: Use calipers and gauges to measure critical dimensions against CAD specifications, ensuring parts meet tolerances.
3. Non-Destructive Testing (NDT):
– Ultrasonic Testing: Detects internal flaws by sending ultrasonic waves through the material.
– X-ray or CT Scanning: Provides a detailed view of internal geometries and voids that could affect performance.
4. Mechanical Testing:
– Tensile Testing: Evaluates material strength and ductility.
– Hardness Testing: Determines resistance to deformation and wear.
5. Microstructure Analysis: Metallographic examination reveals grain structure, phase distribution, and any anomalies that could affect mechanical properties.
6. Thermal Analysis: Techniques like Differential Scanning Calorimetry (DSC) or Thermogravimetric Analysis (TGA) assess thermal properties and reactions.
To control quality in metal 3D printing:
– Material Selection: Use high-quality powders that meet industry standards.
– Process Parameters: Optimize parameters like laser power, scanning speed, and layer thickness to reduce defects.
– Post-Processing: Implement techniques such as heat treatment or surface finishing to enhance mechanical properties and surface quality.
– Regular Calibration: Ensure that printers are regularly calibrated to maintain accuracy and repeatability.
– Document Control: Maintain thorough documentation of quality checks, process parameters, and material certifications for traceability.
Implementing these strategies ensures a robust quality assurance framework for metal 3D printing.
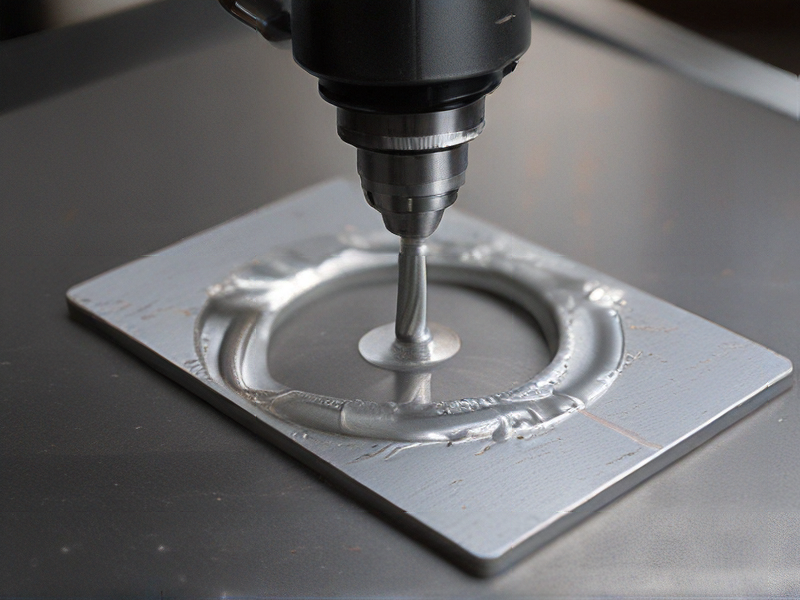
Tips for Procurement and Considerations when Purchasing from 3d print on metal
When procuring 3D printed metal parts, several key considerations can ensure a successful purchase:
1. Material Selection: Understand the specific metal alloys available for 3D printing, such as titanium, stainless steel, or aluminum. Each material has unique properties affecting strength, weight, and corrosion resistance.
2. Supplier Credentials: Choose reputable suppliers with expertise in metal 3D printing. Check for certifications, such as ISO 9001 or AS9100, which indicate adherence to high-quality standards.
3. Production Capabilities: Inquire about the supplier’s printing technology (e.g., Selective Laser Melting, Electron Beam Melting). Different technologies can impact the final part’s quality, accuracy, and surface finish.
4. Design Considerations: Collaborate with your design team to ensure that parts are optimized for 3D printing. This may involve simplifying geometries or incorporating design features that take advantage of additive manufacturing, such as lattice structures.
5. Post-Processing Options: Discuss post-processing methods with the supplier. Techniques like machining, heat treatment, or surface finishing can significantly enhance the component’s performance.
6. Lead Times and Production Volumes: Establish the supplier’s capabilities regarding lead times for prototyping and production runs. Make sure they can meet your delivery schedules and volume requirements.
7. Cost Analysis: Understand the pricing structure, including costs for material, printing, and post-processing. Compare quotes from multiple suppliers to ensure competitive pricing.
8. Intellectual Property Protection: If applicable, discuss how the supplier safeguards your designs and proprietary information.
By addressing these considerations, you can make informed decisions when purchasing 3D printed metal parts, ensuring quality and performance align with your project requirements.
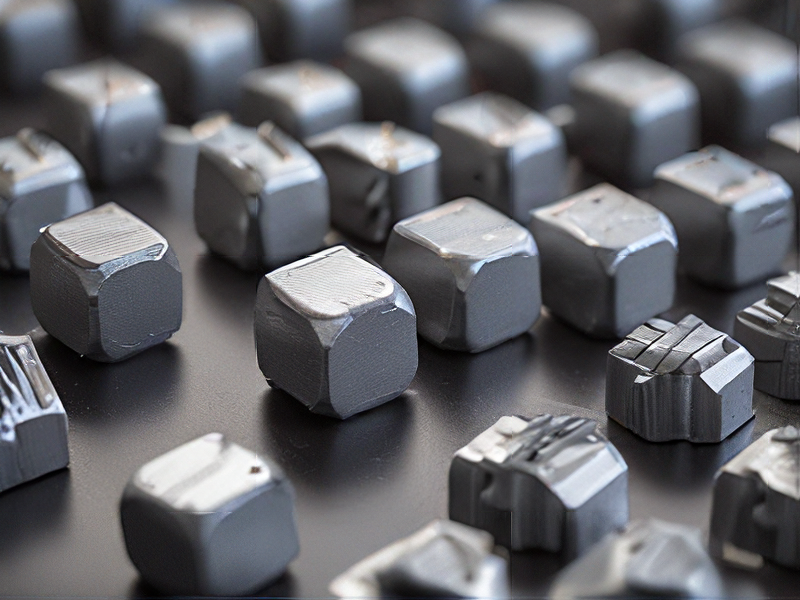
FAQs on Sourcing and Manufacturing from 3d print on metal in China
FAQs on Sourcing and Manufacturing 3D Metal Printing in China
1. What materials can be used for 3D metal printing?
Common materials include stainless steel, titanium, aluminum, and cobalt chrome. The choice depends on the specific application and required properties.
2. What technologies are commonly used for metal 3D printing?
The most prevalent technologies include Selective Laser Melting (SLM), Electron Beam Melting (EBM), and Direct Metal Laser Sintering (DMLS).
3. How do I choose a manufacturer in China?
Look for manufacturers with certifications (e.g., ISO 9001), experience in your industry, and a solid portfolio. Request samples to assess quality.
4. What are the cost factors?
Costs are influenced by material choice, printing technology, design complexity, finishing processes, and order volume.
5. What lead times can I expect?
Lead times vary but typically range from a few weeks to several months, depending on order complexity and manufacturing capacity.
6. How can I ensure quality control?
Implementing a clear quality assurance process, including inspections, certifications, and regular updates from the manufacturer, is essential.
7. Are there intellectual property risks?
Yes, IP protection is a concern. It’s advisable to use non-disclosure agreements (NDAs) and choose reputable manufacturers to mitigate risks.
8. What post-processing options are available?
Common post-processing methods include heat treatment, finishing (e.g., polishing, painting), and machining to improve surface quality and performance.
9. Can I get small batch production runs?
Yes, many manufacturers in China offer small batch production, making it feasible for prototyping and low-volume needs.
10. What shipping options are available?
Shipping options include air freight for faster delivery and sea freight for cost efficiency, depending on project timelines and budgets.
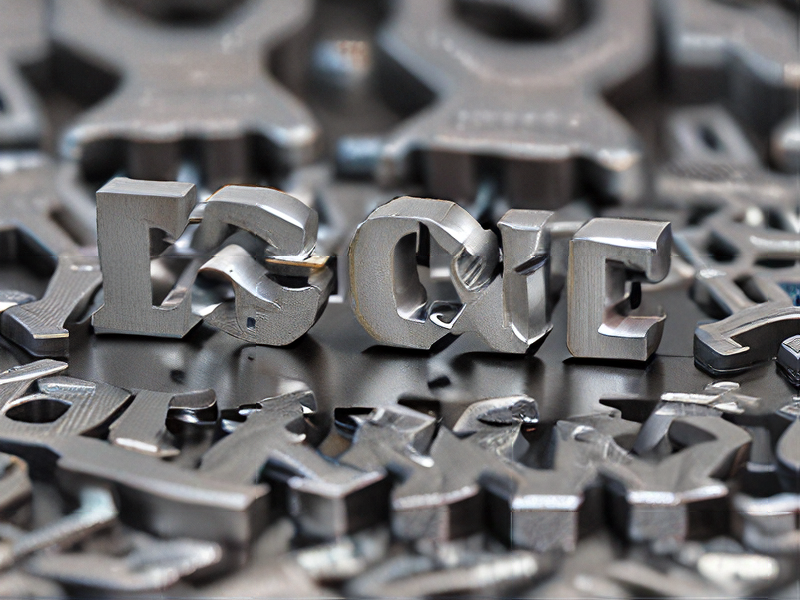