Technology and Applications of 3d printer for metals
3D printing, or additive manufacturing, has revolutionized metal fabrication, offering innovative technologies and diverse applications. Key methods include Selective Laser Melting (SLM), Electron Beam Melting (EBM), and Binder Jetting.
SLM and EBM utilize high-energy beams to selectively melt metal powders layer by layer, allowing for complex geometries that traditional subtractive methods cannot achieve. This capability supports industries such as aerospace, automotive, and medical, where lightweight, intricate designs are essential. Examples include producing turbine blades and custom implants tailored to patient-specific anatomy.
Binder Jetting works differently; it involves depositing a binding agent onto metal powder layers, which are subsequently sintered in a furnace to achieve full density. This technique is notable for its speed and cost-efficiency, particularly in producing large metal parts like molds and tooling for manufacturing.
The technology enables rapid prototyping, reducing lead times and costs associated with traditional manufacturing. Additionally, it supports sustainable production by minimizing waste, as material is only used where necessary.
Recent advancements include the development of metals with enhanced properties, such as titanium alloys and stainless steel, increasing the scope of applications. Industries are also leveraging 3D printed metals for low-volume production runs, custom tooling, and repair parts, thus enhancing operational efficiency.
In summary, metal 3D printing is transforming manufacturing by enabling complex designs, reducing waste, and offering quick turnaround times, setting the stage for future innovations across various sectors.
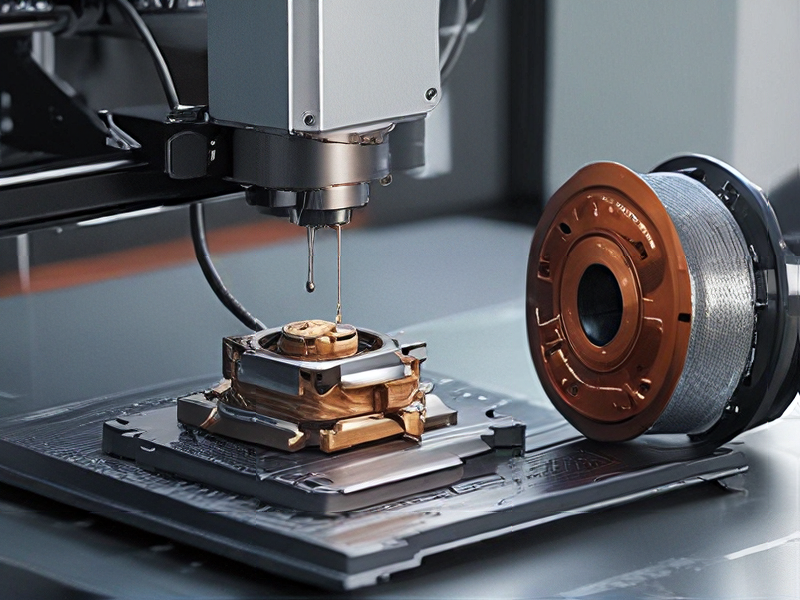
Quality Testing Methods for 3d printer for metals and how to control quality
Quality testing for 3D-printed metal components is critical to ensure structural integrity, mechanical properties, and overall performance. Several methods are employed to control and assure quality:
1. Visual Inspection: Initial assessments involve visual examinations for surface defects, layering issues, and overall appearance. This method is quick and useful for identifying obvious flaws.
2. Dimensional Verification: Employ coordinate measuring machines (CMM) or laser scanners to ensure the dimensions of the printed part meet the specified tolerances. This step is crucial for parts requiring precise fits.
3. Non-destructive Testing (NDT): Techniques like ultrasonic testing or X-ray computed tomography can reveal internal flaws without damaging the component. These methods help detect voids, cracks, or inclusions that could compromise part strength.
4. Mechanical Testing: Samples should undergo tensile, fatigue, and hardness tests to determine material properties. These tests provide insights into the strength, elasticity, and durability of the printed metal.
5. Microstructural Analysis: Scanning electron microscopy (SEM) or optical microscopy can be employed to analyze grain structure and observe potential defects at the micro-level, enabling a deeper understanding of the material properties.
6. Process Control Monitoring: Implement sensors and real-time monitoring during the printing process to track parameters like temperature, layer thickness, and laser power (for powder bed fusion). This data helps to facilitate adjustments and predict potential quality issues.
7. Post-Processing Checks: After printing, consider additional treatments such as heat treatment or surface finishing, and perform inspections to ensure requirements are met.
By combining these methods, manufacturers can maintain robust quality control in metal 3D printing, ensuring each component meets stringent industry standards.
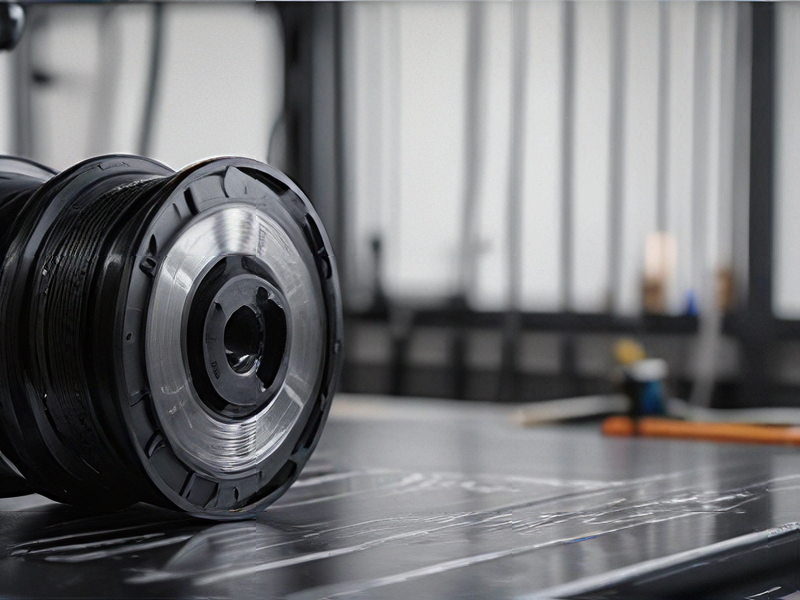
Tips for Procurement and Considerations when Purchasing from 3d printer for metals
When procuring a metal 3D printer, consider the following key tips and factors:
1. Technology Type: Familiarize yourself with different metal 3D printing technologies such as Selective Laser Melting (SLM), Electron Beam Melting (EBM), and Metal Binder Jetting. Each has unique strengths and applications.
2. Material Compatibility: Ensure the printer supports a wide range of metal materials (e.g., stainless steel, titanium, aluminum, nickel alloys) that suit your intended applications.
3. Build Volume: Assess the build size relative to your intended projects. Larger volumes allow for bigger parts or multiple parts in one cycle, improving efficiency.
4. Resolution and Precision: Review the printer’s layer thickness and resolution capabilities. Higher precision is crucial for applications requiring tight tolerances, such as aerospace and medical components.
5. Post-Processing Needs: Understand the post-printing requirements (e.g., heat treatment, machining). Some technologies may necessitate extensive post-processing, impacting overall production time and costs.
6. Software Integration: Check if the printer comes with reliable slicing software and ease of integration into your existing workflows. Good software can streamline the design-to-print process.
7. Support and Maintenance: Research the manufacturer’s reputation for customer support, service warranties, and maintenance requirements. A reliable support structure is essential for minimizing downtimes.
8. Cost of Ownership: Consider not just the initial purchase price but also ongoing costs such as materials, maintenance, and training. Calculate total cost of ownership to ensure budget alignment.
9. Safety Features: Ensure the printer has adequate safety mechanisms in place, particularly for handling metal powders and maintaining operational safety.
Evaluate these considerations to select the right metal 3D printer that aligns with your business needs and objectives.
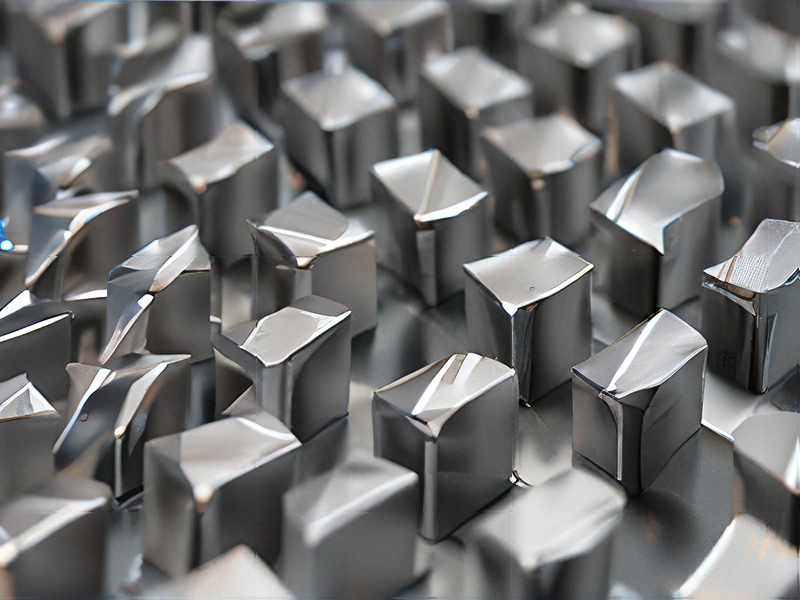
FAQs on Sourcing and Manufacturing from 3d printer for metals in China
FAQs on Sourcing and Manufacturing with Metal 3D Printers in China
1. What are the benefits of using metal 3D printing in China?
Metal 3D printing offers design flexibility, reduced material waste, and faster prototyping. China has a growing number of advanced facilities that can produce complex geometries at competitive prices.
2. What industries benefit the most from metal 3D printing?
Key industries include aerospace, automotive, medical, and tooling, where precision and customization are critical.
3. How do I choose a reliable 3D printing supplier in China?
Evaluate suppliers based on their technology, experience, certifications, and past projects. Customer reviews and case studies can provide insight into their capabilities.
4. What materials can be used in metal 3D printing?
Common materials include titanium, stainless steel, aluminum, and cobalt-chrome alloys. The choice depends on the application and desired properties.
5. What are the typical costs associated with metal 3D printing?
Costs can vary widely based on the part’s complexity, material used, and volume. Initial setup can be higher, but lower production costs may offset this for large orders.
6. How long does the manufacturing process take?
Processing times depend on order size and complexity. Prototyping can take a few weeks, while production runs may take several months.
7. What quality control measures are in place?
Reputable manufacturers conduct thorough quality checks including dimensional inspections, material testing, and final product reviews to ensure adherence to specifications.
8. Are there any export regulations I should consider?
Yes, be aware of export regulations regarding materials and technology when sourcing from China, especially in specialized industries. Consulting with experts or legal advisors is recommended.
9. How do I handle logistics and shipping?
Work with your supplier to determine the best shipping method based on cost and delivery timelines. Ensure all customs documentation is prepared to avoid delays.
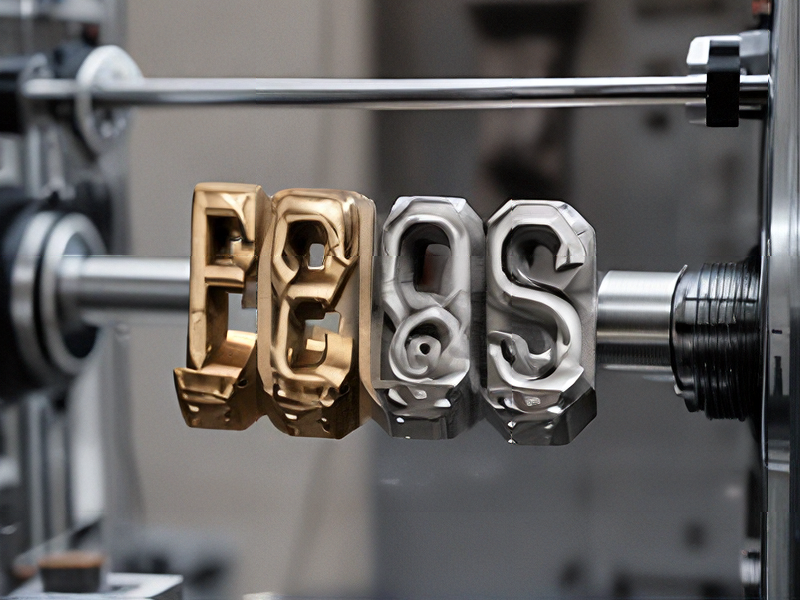