Technology and Applications of 3d print metals
3D printing of metals, also known as metal additive manufacturing, is revolutionizing various industries through its ability to create complex geometries that traditional manufacturing cannot achieve. The process involves techniques such as Selective Laser Melting (SLM), Electron Beam Melting (EBM), and Binder Jetting, which enable the layer-by-layer construction of parts from powdered metal.
One primary advantage of metal 3D printing is design freedom. Engineers can create lightweight structures with intricate internal features, reducing material waste and overall weight. This is particularly beneficial in sectors like aerospace, automotive, and medical devices, where optimized performance and weight savings are critical.
The applications of 3D printed metals are diverse. In aerospace, parts like brackets and turbine components are produced with reduced weight and improved performance. The automotive industry utilizes 3D metal printing for tooling and bespoke parts, accelerating production timelines. In medical fields, custom implants and prosthetics tailored to individual patients are becoming increasingly common.
Moreover, metal 3D printing enables rapid prototyping, allowing companies to quickly iterate designs and test functionality without the lengthy lead times associated with traditional manufacturing methods. This leads to innovation and faster product development cycles.
Challenges remain, such as the high cost of metal powders and equipment, as well as the need for stringent quality controls to ensure part integrity. However, advancements in materials science and printing technologies are continually addressing these issues. As the technology matures, its adoption across various sectors is expected to grow, driving efficiency and innovation in manufacturing processes.
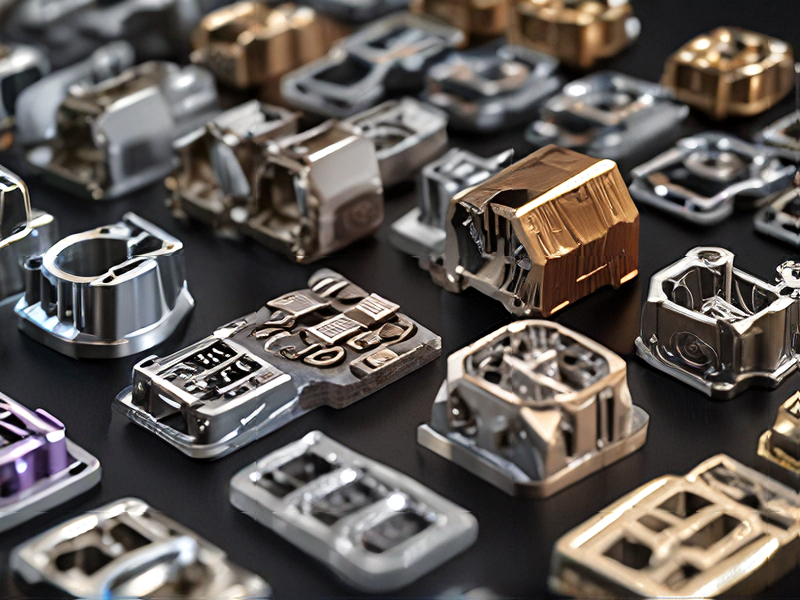
Quality Testing Methods for 3d print metals and how to control quality
Quality testing of 3D-printed metals is essential to ensure structural integrity and performance. Key methods include:
1. Visual Inspection: Initial checks for obvious defects like warping, layer separation, or surface roughness can be performed using the naked eye or magnification tools.
2. Dimensional Analysis: Using calipers and coordinate measuring machines (CMM), measure critical dimensions to verify they meet design specifications.
3. Non-Destructive Testing (NDT): Techniques like Ultrasonic Testing (UT), X-ray Computed Tomography (CT), and Magnetic Particle Inspection can detect internal and surface flaws without damaging the part.
4. Mechanical Testing: Conduct tensile, compressive, and fatigue tests to assess material strength and durability. Hardness testing using methods like Rockwell or Brinell can also be important.
5. Microstructural Analysis: Use Optical or Scanning Electron Microscopy (SEM) to examine grain structure, porosity, and inclusions, which affect mechanical properties.
To control quality, implementing a robust Quality Management System (QMS) is crucial. This includes:
– Material Verification: Ensure raw materials meet specifications through certification and testing.
– Process Monitoring: Utilize sensors and data logging to monitor printing parameters (temperature, speed, layer height) in real-time and adjust accordingly.
– Post-Processing Procedures: Standardize post-processing techniques such as heat treatment or surface finishing to improve mechanical properties.
– Regular Audits and Training: Conduct periodic quality audits and provide training for operators to maintain high standards throughout the printing process.
Combining these methods and controls fosters a culture of quality, ensuring that 3D-printed metal parts are reliable and meet industry standards.
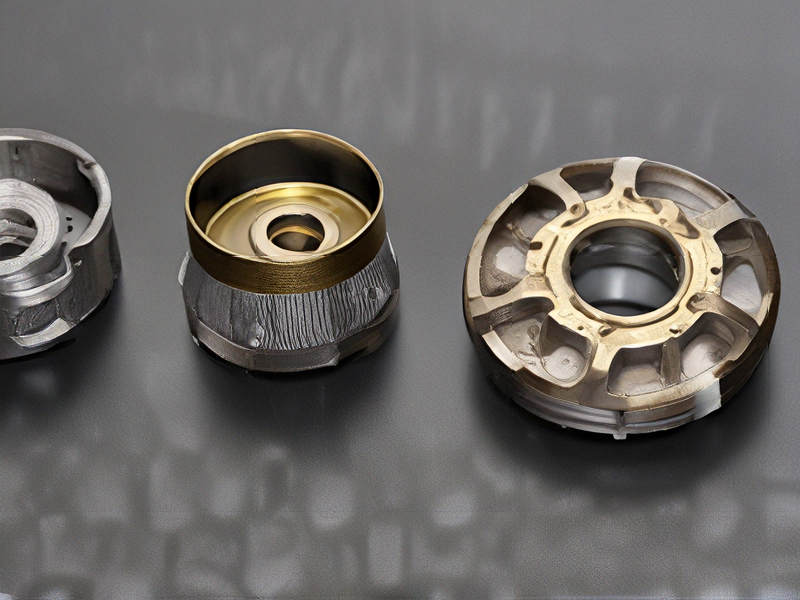
Tips for Procurement and Considerations when Purchasing from 3d print metals
When procuring 3D printed metals, several key considerations can enhance decision-making and ensure quality and cost-effectiveness:
1. Material Selection: Choose the appropriate metal for your application. Common 3D printing metals include titanium, aluminum, and stainless steel, each offering different properties such as strength, weight, and corrosion resistance.
2. Supplier Evaluation: Assess potential suppliers based on their reputation, certifications (e.g., ISO), and previous work samples. Ensure they have the capability to meet your specific requirements and industry standards.
3. Technology Choice: Familiarize yourself with the different 3D printing technologies used for metals, such as Direct Metal Laser Sintering (DMLS) or Electron Beam Melting (EBM). Each has unique advantages regarding surface finish, detail, and production speed.
4. Cost Analysis: Understand the total cost of ownership, including design, material, production processes, finishing, and post-processing. Compare quotes from multiple suppliers while considering the quality of outputs.
5. Design Optimization: Collaborate with your design team to optimize parts for 3D printing. This may involve reducing weight through lattice structures or integrating features to minimize assembly.
6. Prototype Testing: Prioritize prototyping to identify any issues in design or performance early on. Rigorous testing helps validate the functionality and durability of the printed component.
7. Lead Times: Consider the production timeline for 3D printed metal parts. Discuss lead-time expectations with your supplier to ensure alignment with your project schedule.
8. Supply Chain Considerations: Ensure your supply chain is robust, with backup suppliers and a clear plan for material sourcing to mitigate potential disruptions.
By focusing on these areas, organizations can streamline their procurement processes and achieve successful outcomes in their 3D metal printing projects.
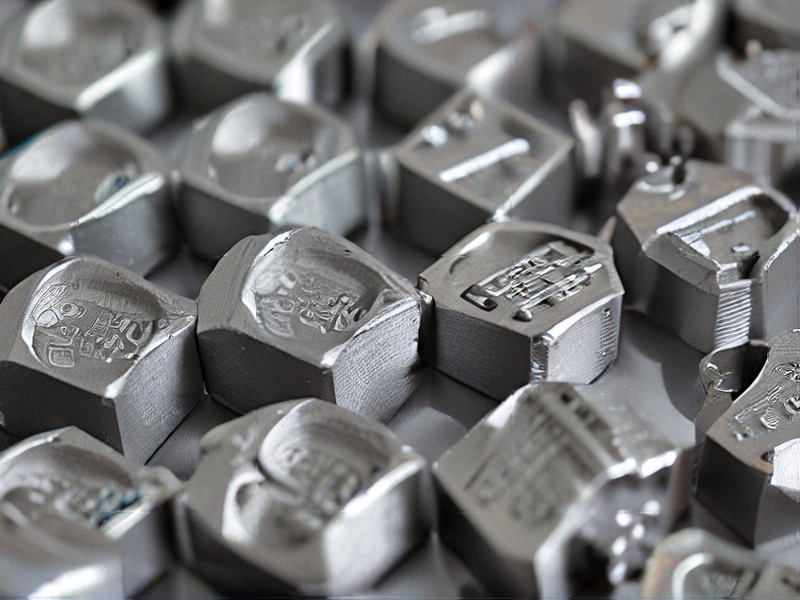
FAQs on Sourcing and Manufacturing from 3d print metals in China
FAQs on Sourcing and Manufacturing 3D Print Metals in China
1. What materials are commonly used for 3D printing metals in China?
China primarily uses stainless steel, titanium alloys, aluminum alloys, and nickel-based superalloys for 3D printing. These materials offer a balance of strength and flexibility, suitable for various applications.
2. What are the advantages of sourcing from China?
China boasts advanced manufacturing technologies, a skilled workforce, and competitive pricing. Additionally, the availability of various suppliers allows for flexibility in sourcing specific materials and processes.
3. How do I ensure quality control during manufacturing?
Establish clear specifications and standards upfront. Request certifications like ISO 9001 or AS9100, and consider hiring third-party inspection services to monitor the production process and final products.
4. What are typical lead times for 3D printed metal parts?
Lead times can vary depending on complexity, quantity, and production schedules. Generally, expect a timeline of 4 to 8 weeks, but this can be shorter with expedited services.
5. What is the minimum order quantity (MOQ)
MOQs can vary significantly based on the manufacturer, part complexity, and production capabilities. It’s essential to discuss your specific needs with potential suppliers.
6. Are there any language barriers when sourcing from China?
While many manufacturers employ English-speaking staff, some communication challenges may persist. It is advisable to work with suppliers who have experience in international business.
7. How do I protect my intellectual property (IP)?
Implement Non-Disclosure Agreements (NDAs) with suppliers and consider registering patents in China. Conduct thorough due diligence before sharing sensitive designs or data.
8. What are the payment terms typically offered?
Payment terms can vary; however, common practices include a 30-50% upfront deposit with the balance due upon completion or before shipment. Always negotiate and document terms clearly.
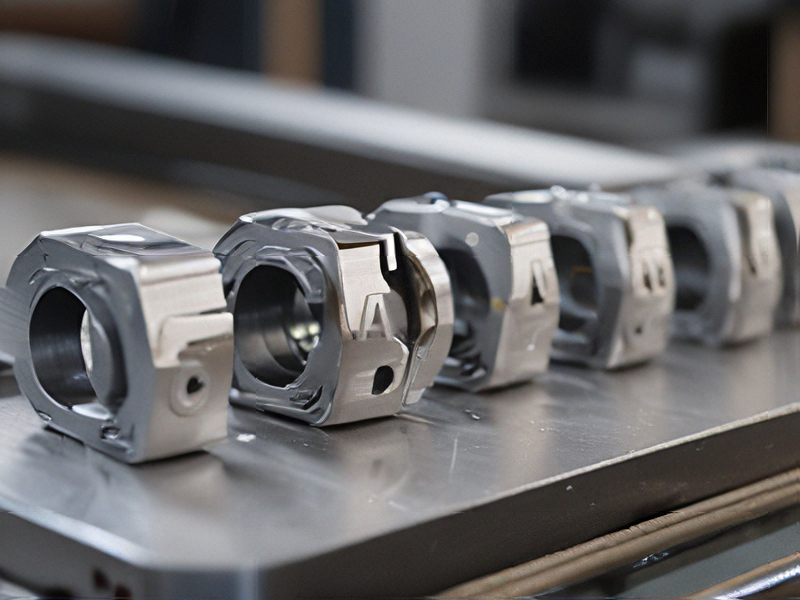