Technology and Applications of metal 3d prints
Metal 3D printing, or additive manufacturing, is revolutionizing various industries by enabling the production of complex geometries, reducing material waste, and significantly shortening lead times. The technology primarily employs methods such as Selective Laser Melting (SLM), Electron Beam Melting (EBM), and Binder Jetting. These processes allow for precise layering of metal powders to create intricate parts that are often impossible to achieve through traditional manufacturing methods.
Applications of metal 3D printing span across multiple sectors, including aerospace, automotive, medical, and tooling. In aerospace, for instance, lightweight components with complex structures can enhance fuel efficiency and performance. In the automotive industry, manufacturers use 3D printing for prototyping and producing custom parts, reducing costs and time-to-market.
The medical field benefits significantly from metal 3D printing by enabling the creation of tailored implants and prosthetics that fit patients’ specific anatomical requirements. Furthermore, the technology facilitates rapid prototyping in tooling, allowing for the quick iteration of designs, which is crucial for maintaining a competitive edge.
Additionally, advancements in materials science are expanding the range of metals available for 3D printing. Alloys such as titanium, aluminum, and cobalt-chrome are commonly used, each offering unique properties for different applications. The combination of flexibility in design, customization capabilities, and the potential for lightweight construction positions metal 3D printing as a transformative force in manufacturing. As technology continues to advance, it is poised to further enhance efficiency, sustainability, and innovation across various industries.
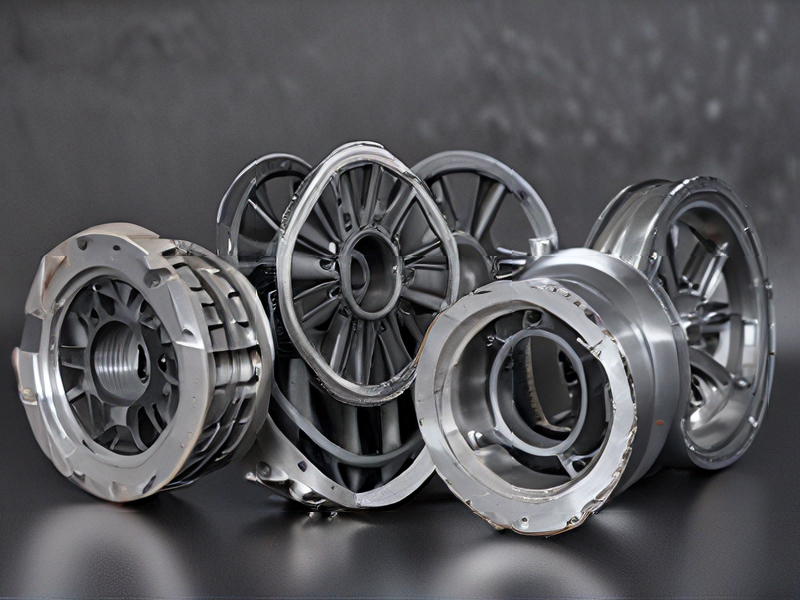
Quality Testing Methods for metal 3d prints and how to control quality
Quality testing for metal 3D prints is critical to ensure part integrity and performance. Here are key methods and control measures:
1. Visual Inspection: A preliminary check for surface defects, layer inconsistencies, and overall dimensional accuracy. High-quality prints should have minimal visible flaws.
2. Dimensional Accuracy Testing: Using calipers, gauges, or coordinate measuring machines (CMM) to assess whether the printed part meets specified tolerances.
3. Non-Destructive Testing (NDT): Techniques like X-ray or ultrasound scanning evaluate the internal structure without damaging the part. These methods can detect voids, inclusions, or other internal defects.
4. Mechanical Testing: Assessing material properties through tensile, fatigue, and hardness tests. This helps determine if the print meets the necessary strength and durability criteria.
5. Microstructure Analysis: Using microscopy to examine grain structure and phase distribution. This analysis helps in understanding the material properties derived from the printing process.
6. Porosity Measurement: Quantifying porosity using methods like Archimedes’ principle or image analysis. Controlling pore sizes is essential for the mechanical performance of the final part.
Quality Control Measures:
– Process Monitoring: Implement sensors and monitoring systems during printing to track parameters like temperature, laser power, and feed rates, ensuring they stay within specified ranges.
– Standard Operating Procedures (SOPs): Establish robust SOPs for preparation, printing, and post-processing to minimize variations.
– Material Traceability: Maintain records of material batches to ensure consistency across prints.
By employing these testing methods and control measures, manufacturers can effectively ensure the quality and reliability of metal 3D printed components.
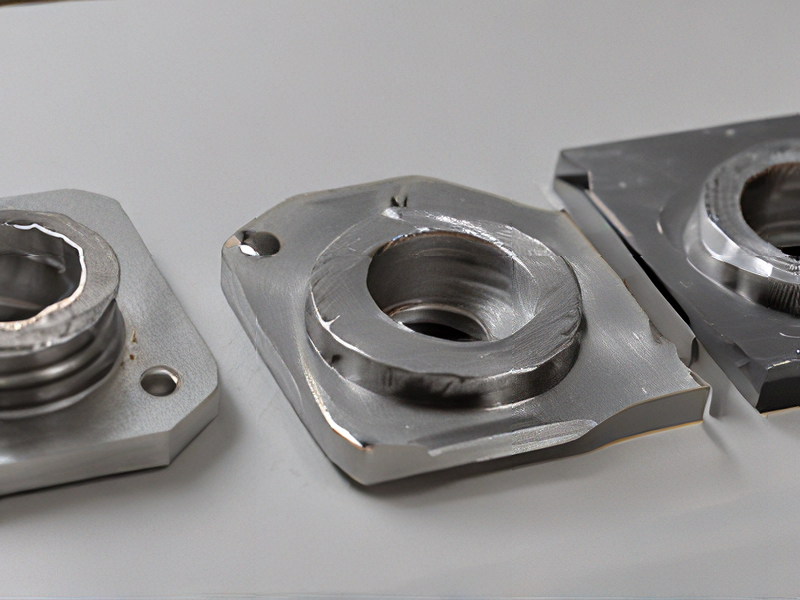
Tips for Procurement and Considerations when Purchasing from metal 3d prints
When procuring metal 3D prints, several key tips and considerations can help ensure a successful purchase:
1. Material Selection: Identify the specific metal alloy required for your application, considering properties like strength, weight, corrosion resistance, and temperature tolerance. Popular choices include titanium, aluminum, and stainless steel.
2. Supplier Credibility: Research potential suppliers thoroughly. Look for those with a proven track record in metal 3D printing, certifications (like ISO standards), and positive customer testimonials.
3. Technology Used: Understand the printing technology employed by the supplier (e.g., Electron Beam Melting, Selective Laser Melting). Each method has different capabilities, surface finishes, and tolerances.
4. Design Constraints: Ensure your design is optimized for metal 3D printing. Some geometries may be difficult or costly to produce. Engage with the supplier for design feedback early in the process.
5. Post-Processing Requirements: Determine if post-printing processes like heat treatment, machining, or surface finishing are needed. Clarify these costs and timelines with the supplier.
6. Quality Assurance: Inquire about the supplier’s quality control measures, including inspections and testing procedures. Ensure they can provide necessary certifications for the printed parts.
7. Lead Time and Scalability: Confirm the expected lead time for your order and the supplier’s capability to scale production if required in the future.
8. Cost Transparency: Seek detailed pricing that includes all aspects of production, from design to delivery. Be wary of hidden costs that might arise during the process.
By considering these factors, you can ensure a well-informed procurement process for metal 3D prints that meets your specific needs and requirements.
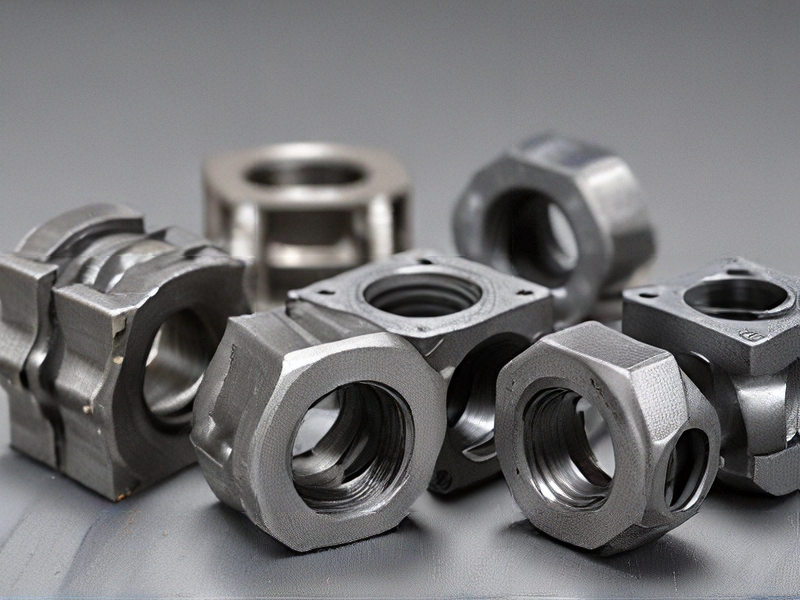
FAQs on Sourcing and Manufacturing from metal 3d prints in China
FAQs on Sourcing and Manufacturing Metal 3D Prints in China
1. What are the advantages of sourcing metal 3D printing in China?
China offers competitive pricing, a skilled workforce, and advanced technology. With a robust manufacturing ecosystem, businesses can access high-quality materials and rapid prototyping services.
2. What materials are commonly used for metal 3D printing?
Common materials include stainless steel, titanium, aluminum, and cobalt-chrome alloys. Each material has unique properties suited for different applications.
3. How does the metal 3D printing process work?
Metal 3D printing typically involves methods like Selective Laser Melting (SLM) and Direct Metal Laser Sintering (DMLS). These processes layer fine metal powders which are melted and fused with a laser to create parts.
4. What are the typical lead times for production?
Lead times vary based on part complexity and quantity but generally range from a few weeks to several months, including design, printing, post-processing, and shipping.
5. How do I ensure quality in my metal 3D prints?
Collaborate with reputable suppliers who have quality certifications (ISO 9001, etc.). Request samples and conduct audits to evaluate their processes and quality control measures.
6. What is the cost structure for metal 3D printing?
Costs can vary based on material, complexity, and quantity. Pricing typically includes the cost of materials, printing, post-processing, and shipping.
7. Are there regulations I should be aware of?
Be mindful of export regulations and intellectual property rights when sourcing from China. Thoroughly review contracts and seek legal guidance if necessary.
8. What industries benefit from metal 3D printing?
Key industries include aerospace, automotive, healthcare, and manufacturing, where lightweight and complex designs are essential.
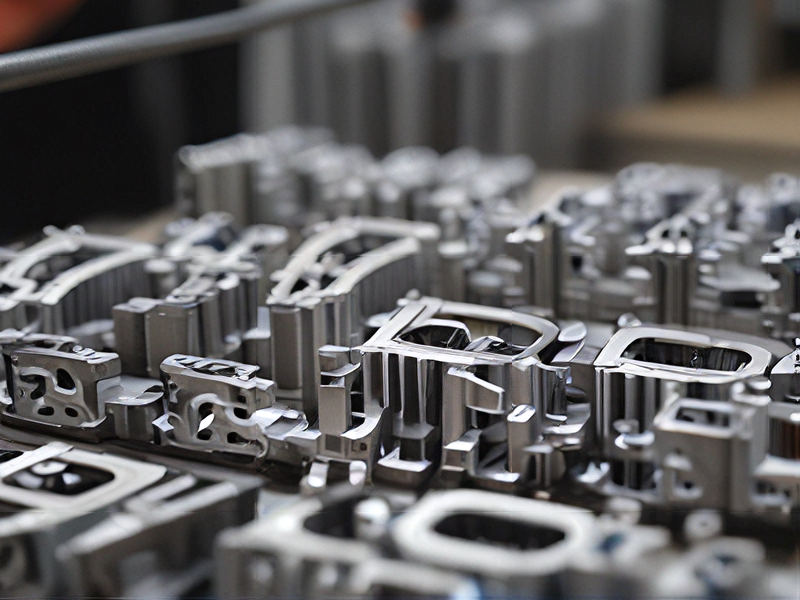