Technology and Applications of metal injection
Metal Injection Molding (MIM) is an advanced manufacturing process that combines the principles of traditional injection molding with powder metallurgy. This technique allows for the production of complex metal parts with high precision and efficiency, making it suitable for a wide range of applications.
In MIM, metal powders are mixed with a binder material to form a feedstock that can be injected into molds. After injection, the part undergoes debinding to remove the binder, followed by sintering to achieve the final desired properties. This process enables the production of intricate geometries that are difficult to achieve with conventional machining methods.
The applications of MIM span various industries, including:
1. Automotive: Components such as gearbox parts, fuel injectors, and valve seats are produced using MIM, benefitting from the process’s ability to reduce weight while maintaining strength.
2. Aerospace: MIM is utilized for components requiring tight tolerances and complex shapes, such as brackets, fittings, and turbine parts.
3. Medical Devices: Surgical instruments, dental implants, and various medical devices benefit from MIM’s precision and the ability to produce biocompatible materials.
4. Consumer Electronics: The production of small, intricate parts for devices like smartphones and wearables has been enhanced through MIM, improving performance and aesthetics.
5. Industrial Equipment: MIM is employed for producing durable components that withstand harsh conditions, ensuring longevity and reliability in machinery.
Overall, MIM presents significant advantages, including reduced waste, lower production costs for complex parts, and the ability to create high-performance materials, making it a vital technology in modern manufacturing.

Quality Testing Methods for metal injection and how to control quality
Quality testing for metal injection molding (MIM) is essential to ensure the mechanical properties and integrity of components. Effective quality control methods include:
1. Material Characterization: Initial analysis involves verifying the chemical composition of the powdered metal using techniques like X-ray fluorescence (XRF) or inductively coupled plasma (ICP) spectrometry. This ensures that the raw materials meet specified standards.
2. Green Part Evaluation: Testing green parts for dimensional accuracy and surface quality is crucial. Techniques like calipers and coordinate measuring machines (CMM) assess the physical dimensions before sintering.
3. Sintering Analysis: Post-sintering, evaluate density and microstructural features using techniques such as scanning electron microscopy (SEM) and optical microscopy. This ensures the material achieves the desired mechanical properties, including hardness and tensile strength.
4. Mechanical Testing: Conduct standardized tests like tensile, fatigue, and impact tests to verify the strength and durability of the final product. These tests are often performed according to ASTM or ISO standards.
5. Non-Destructive Testing (NDT): Techniques like ultrasonic testing and X-ray inspection can help identify internal flaws or porosity without damaging the parts.
6. Surface Quality Inspection: Methods such as visual inspection and roughness measurements ensure the surface integrity of the parts.
7. Traceability and Documentation: Maintaining detailed records of processes, tests, and results ensures traceability and facilitates continuous improvement.
Implementing these quality control methods requires a well-defined quality management system that includes training, process audits, and continuous feedback loops to refine manufacturing processes and meet customer specifications effectively. By adhering to these practices, MIM manufacturers can enhance product reliability and customer satisfaction.

Tips for Procurement and Considerations when Purchasing from metal injection
When considering procurement for Metal Injection Molding (MIM) processes, here are key tips and considerations:
1. Material Selection: Identify the specific metal alloys suitable for your application. MIM works best with materials such as stainless steel, titanium, and certain nickel alloys. Ensure the chosen material meets the necessary mechanical, thermal, and corrosion resistance properties.
2. Supplier Evaluation: Research and evaluate potential suppliers. Look for established companies with a proven track record in MIM. Check for certifications such as ISO or AS9100, which indicate compliance with industry standards.
3. Quality Assurance: Inquire about the supplier’s quality control processes. Ensure they have stringent inspection methods and testing protocols to guarantee the integrity of the final product. Request documentation of past performance and client references.
4. Design Compatibility: Consider the design complexity and precision requirements of your components. MIM can produce intricate shapes, but ensure your designs are optimized for the process to minimize material waste and production costs.
5. Production Volume: Determine your expected production volume. MIM is cost-effective for high-volume runs but may not be suitable for low-volume projects. Discuss minimum order quantities and scalability options with suppliers.
6. Lead Time and Logistics: Evaluate lead times for tooling, production, and delivery. Understand your supplier’s schedule and their ability to meet your project’s timelines.
7. Cost Analysis: Analyze total procurement costs, including tooling, production, and post-processing. Compare quotes from multiple suppliers to ensure you’re getting competitive pricing, but don’t compromise on quality for cost.
By considering these factors, you can enhance your procurement strategy for MIM, ensuring quality, efficiency, and optimal cost management.
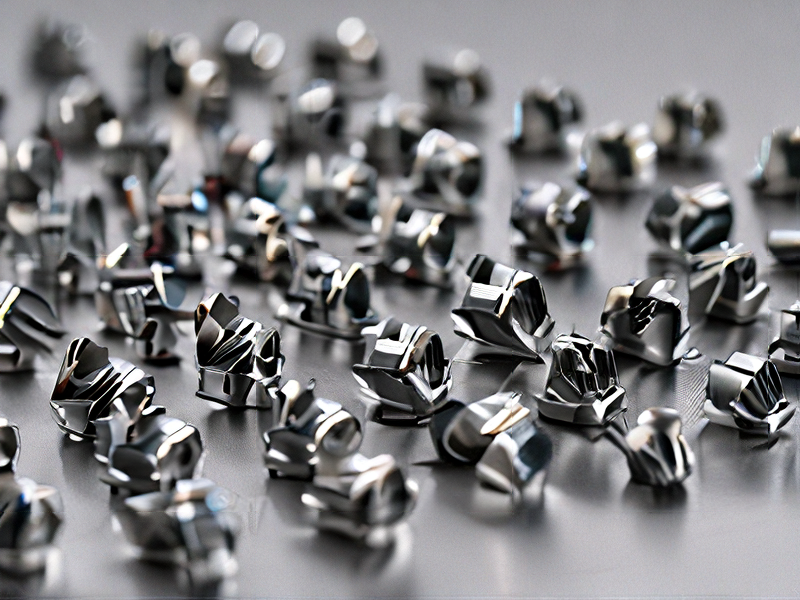
FAQs on Sourcing and Manufacturing from metal injection in China
FAQs on Sourcing and Manufacturing Metal Injection in China
1. What is Metal Injection Molding (MIM)?
Metal Injection Molding is a manufacturing process that combines fine metal powders and binding agents to create complex metal parts. After injection, the parts are debound and sintered, resulting in high-density components.
2. Why choose China for MIM?
China offers competitive pricing, advanced manufacturing technologies, and a vast network of suppliers. The country has vast experience in metalworking, making it a leading destination for MIM.
3. What materials are commonly used in MIM?
Common materials include stainless steel, titanium, copper, and various alloys. The choice of material depends on the application and required properties like strength and corrosion resistance.
4. How do I ensure quality in MIM products?
Selecting a reputable supplier is crucial. Look for manufacturers with ISO certifications and a track record in quality control, including pre-production testing and post-production inspections.
5. What are the typical lead times for MIM projects?
Lead times can vary but generally range from 8 to 16 weeks, depending on the complexity of the design, tooling requirements, and production volumes.
6. What are the costs involved in MIM?
Costs depend on several factors, including material, part complexity, production volume, and tooling. It’s advisable to request detailed quotes from multiple suppliers.
7. What are the environmental regulations in China for metal manufacturing?
China has been improving environmental regulations. Ensure your supplier complies with local environmental laws and standards to avoid potential disruptions.
8. How do I protect my intellectual property?
Use Non-Disclosure Agreements (NDAs) and consider registering your patents in China. Work with legal experts to safeguard your designs and proprietary information.
For further inquiries, it’s beneficial to consult with industry experts or sourcing agents in China.
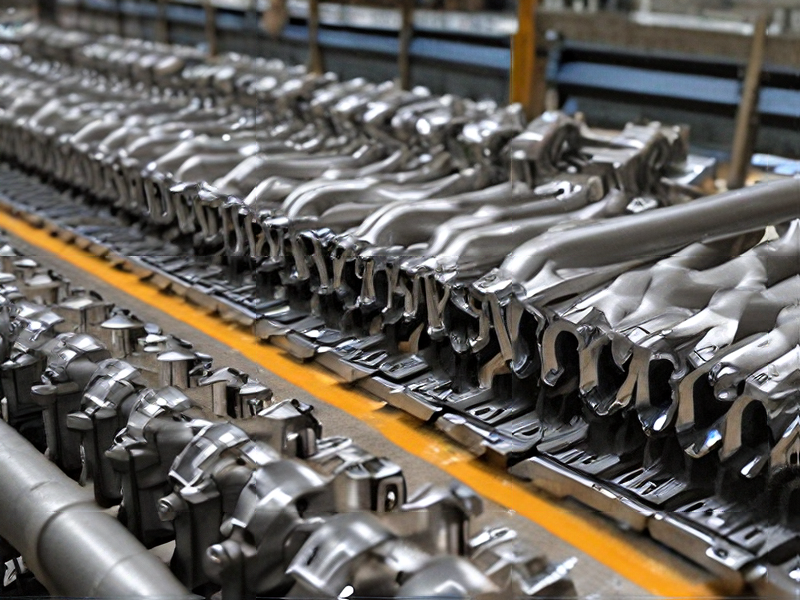