Technology and Applications of mill machine
Mill machines, integral to the manufacturing and processing sectors, utilize advanced technology to perform various tasks such as milling, grinding, and drilling. These machines operate on principles of material removal using rotary cutters, impacting both efficiency and precision in production.
Key Technologies:
1. CNC Milling: Computer Numerical Control (CNC) technology allows for automated and highly precise milling operations. CNC mills can produce complex shapes and designs, significantly reducing human error and increasing production speed.
2. Vertical & Horizontal Milling Machines: Vertical mills have a vertically oriented spindle, ideal for tasks requiring precision, such as slotting and drilling. Horizontal mills, with horizontal spindles, are better suited for heavy-duty tasks and large workpieces.
3. 3D Printing Integration: Some modern mills integrate additive manufacturing processes, allowing for rapid prototyping and the production of intricate geometries that traditional methods may find challenging.
Applications:
1. Manufacturing: Mills are essential in producing parts for industries like aerospace, automotive, and medical devices, ensuring high tolerance and durability in components.
2. Woodworking: In the woodworking sector, milling machines shape and finish wood pieces, enhancing aesthetics and usability in furniture design and construction.
3. Metalworking: Milling machines are crucial for shaping metal parts, providing the necessary finish for machine components in various heavy machinery and equipment.
In summary, the technology and applications of mill machines are diverse and vital to numerous industries, driving innovation and efficiency in manufacturing processes. Their adaptability continues to enhance operational capabilities across various sectors.
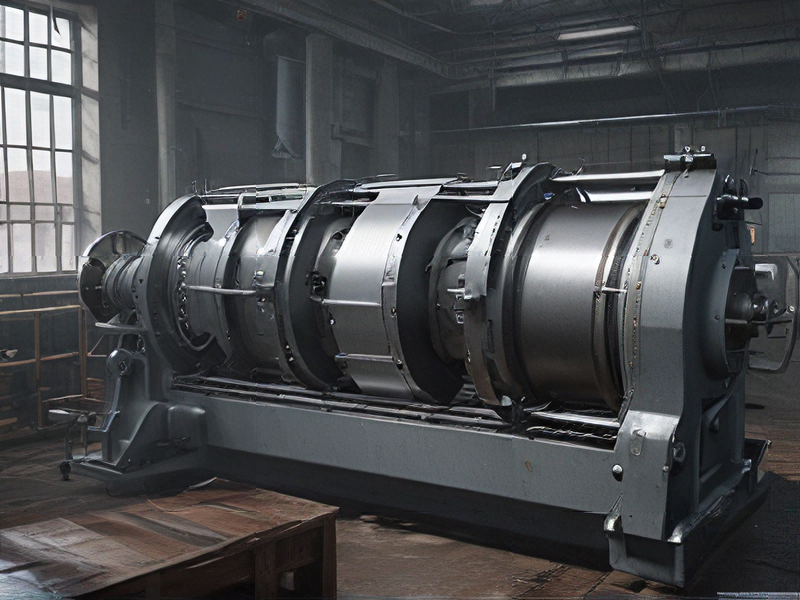
Quality Testing Methods for mill machine and how to control quality
Quality testing methods for milling machines are essential for ensuring optimal performance, safety, and reliability. Here are some effective methods and strategies for controlling quality:
1. Dimensional Inspection: Use calipers and micrometers to measure the dimensions of machined parts against specified tolerances. This ensures that each part meets manufacturing standards.
2. Visual Inspection: Perform thorough visual checks for surface defects, tool wear, and alignment issues. Regularly inspecting machine components helps in early detection of wear and prevents defects.
3. Runout Testing: Measure the runout (the deviation from perfect roundness) of rotating parts to ensure accurate machining. Tools like dial indicators can be used to assess alignment and precision.
4. Hardness Testing: Utilize hardness testers to ensure that the material used for parts is within specified hardness ranges, which affects durability and performance.
5. Operational Tests: Conduct operational trials under varied conditions to evaluate the machine’s performance, including cutting speed, feed rate, and load capacity.
6. Statistical Process Control (SPC): Employ SPC techniques to monitor and analyze production processes. Control charts can help identify trends and variations in production quality.
7. Material Traceability: Implement systems for tracking materials used in production to ensure compliance with specifications, allowing for recalls if defects are discovered.
8. Preventive Maintenance: Establish a routine maintenance schedule to keep the milling machine in optimal condition, minimizing the risk of breakdowns and defects.
By combining these methods, manufacturers can effectively control the quality of milling machines, ensuring they meet industry standards and customer expectations.
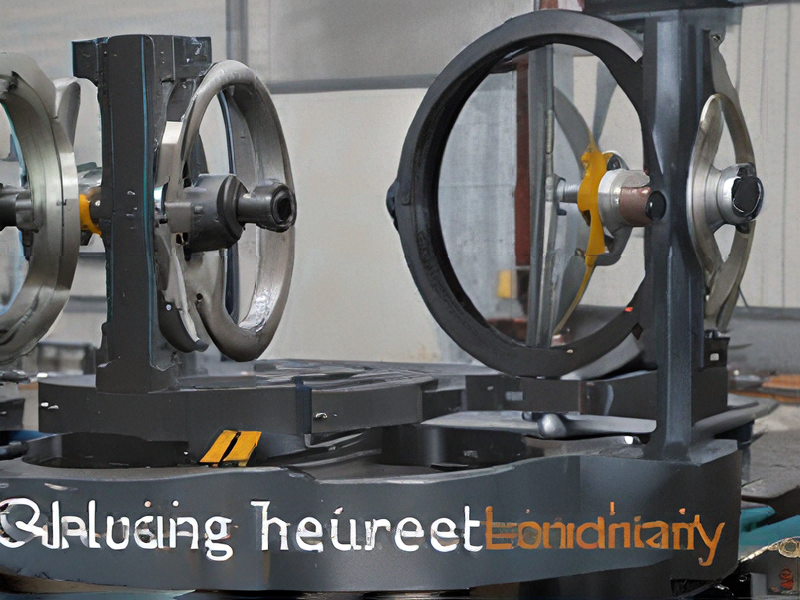
Tips for Procurement and Considerations when Purchasing from mill machine
When purchasing a mill machine, careful planning and consideration are crucial to ensure you make the right investment. Here are essential tips and considerations:
1. Define Requirements: Clearly outline your production needs, such as the type of materials you will process, the required capacity, and the desired output quality. This will help in selecting a machine that fits your specifications.
2. Budget and Total Cost of Ownership: Establish a budget that encompasses not just the initial purchase price but also operational costs, maintenance, energy consumption, and potential downtime.
3. Supplier Reputation: Research potential suppliers. Look for reviews, testimonials, and case studies to understand their reliability, after-sales service, and customer support. A reputable supplier often provides better pre- and post-purchase assistance.
4. Technology and Features: Evaluate the technology incorporated in the mill machine. Modern machines may offer automation, energy efficiency, and superior performance features, which can enhance productivity.
5. Compliance and Standards: Ensure the mill machine meets industry standards and regulations. This includes safety certifications and environmental regulations specific to your region.
6. Customization Options: Consider if the supplier offers customization to meet your specific needs or if they can provide accessories and upgrades in the future.
7. Warranty and Support: Investigate the warranty terms and the availability of technical support. A good warranty can protect your investment and guarantee assistance in maintaining the machine.
8. Demo and Testing: If possible, request a demonstration or trial period to assess the machine’s performance in your specific operating environment.
By taking these considerations into account, you can make an informed decision that aligns with your operational goals and budget.
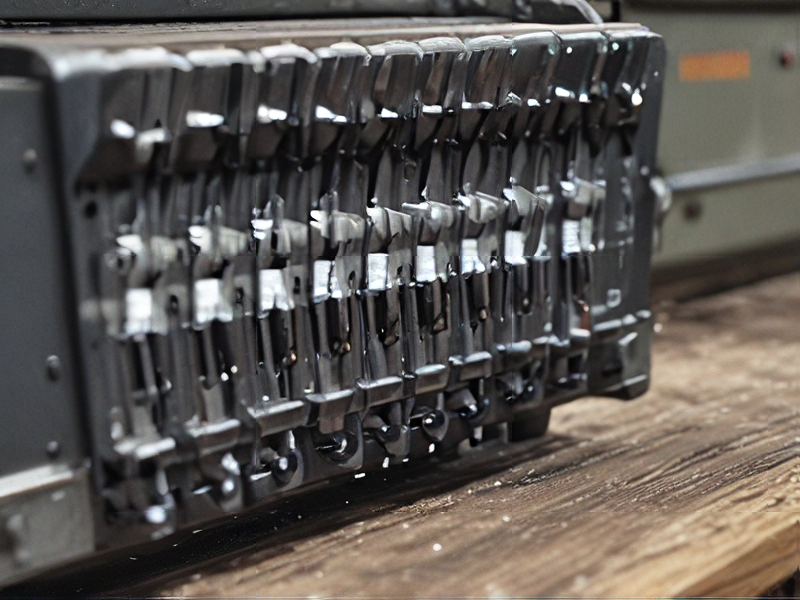
FAQs on Sourcing and Manufacturing from mill machine in China
FAQs on Sourcing and Manufacturing Mill Machines in China
1. Why source mill machines from China?
China is known for its competitive pricing, advanced manufacturing technology, and a vast range of suppliers. This makes it an attractive option for high-quality mill machines at lower costs.
2. How do I find reliable suppliers?
Research is key. Use platforms like Alibaba, Made-in-China, or Global Sources. Check supplier ratings, read reviews, and verify their certifications. Attending trade shows in China or industry expos can also help you meet suppliers face-to-face.
3. What should I consider when assessing quality?
Request samples and conduct inspections during production. Look for ISO certifications and ask for material specifications. Engaging third-party inspection services can also help ensure adherence to quality standards.
4. What are the shipping options?
Common shipping methods include sea freight, air freight, and express shipping. Sea freight is cost-effective for bulk orders, while air freight is faster but more expensive. Consider using a freight forwarder to manage logistics efficiently.
5. How do I handle customs and duties?
Familiarize yourself with local import regulations and customs duties for mill machines. Ensure all paperwork, including invoices and bills of lading, is in order to avoid delays.
6. Can I customize my mill machine?
Most manufacturers offer customization options. Communicate your specific requirements, including size, features, and materials, to ensure the final product meets your needs.
7. What are the payment terms?
Payment terms can vary. Common methods include a deposit upfront (30-50%) and the balance upon shipment. Using secure payment methods like PayPal or a letter of credit can provide added protection.
8. What are the lead times?
Lead times can vary depending on the complexity of the machine and order size. Typically, expect 30 to 90 days from order confirmation to delivery. Always confirm with your supplier.
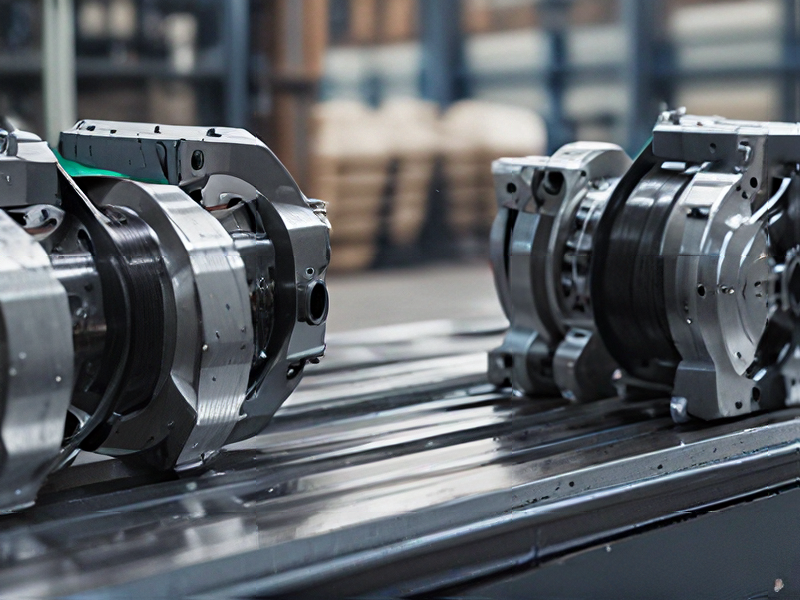