Technology and Applications of brackets metal
Metal brackets are fundamental components used across various industries for a wide range of applications, primarily due to their durability, strength, and versatility. Here’s a brief overview of their technology and applications:
Technology
Material Composition: Metal brackets are typically made from stainless steel, aluminum, or galvanized steel. These materials are chosen for their high tensile strength, corrosion resistance, and longevity.
Manufacturing Processes: The production of metal brackets involves several processes:
– Stamping: Sheets of metal are cut and shaped using dies to form the desired bracket shape.
– Bending: The metal is bent to specific angles and shapes, which is crucial for fitting and support applications.
– Welding: For complex designs, welding is used to join multiple pieces of metal.
– Finishing: To enhance corrosion resistance and appearance, metal brackets may undergo processes like powder coating, anodizing, or galvanizing.
Applications
Construction: Metal brackets are essential in construction for joining structural elements, supporting beams, and securing frameworks. They are used in both residential and commercial buildings for tasks such as mounting shelves, securing handrails, and supporting ceilings.
Automotive Industry: In vehicles, metal brackets are used to mount engines, secure batteries, and attach various components to the chassis. Their strength ensures that these components remain securely in place even under intense conditions.
Electronics: Metal brackets are used in electronic devices to mount circuit boards, secure components, and provide structural integrity. They help in dissipating heat and ensuring that delicate parts are protected and properly aligned.
Furniture: In furniture making, metal brackets provide structural support for items like beds, tables, and chairs. They ensure stability and durability, especially in joints and corners where stress is highest.
Aerospace: The aerospace industry uses specialized metal brackets to handle extreme conditions and stresses. They are critical for mounting instruments, securing panels, and ensuring the structural integrity of aircraft.
In summary, metal brackets are integral to various applications due to their robustness, versatility, and ability to meet specific structural and functional requirements. Their manufacturing involves advanced techniques to ensure they meet the high standards necessary for their diverse uses.
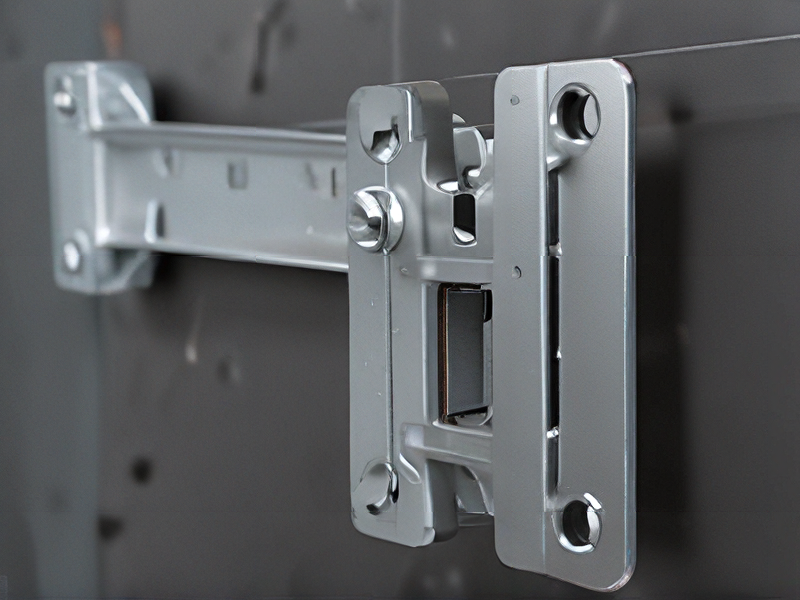
Quality Testing Methods for brackets metal and how to control quality
Quality testing methods for metal brackets involve several key procedures to ensure they meet the required standards and specifications. Here are the primary methods and control measures:
Testing Methods:
1. Tensile Testing:
– Purpose: Measures the strength and ductility of the metal.
– Procedure: A sample bracket is pulled until it breaks, recording the stress and strain.
2. Hardness Testing:
– Purpose: Determines resistance to deformation and wear.
– Procedure: Techniques like Rockwell, Vickers, or Brinell hardness tests are used to press a hard object into the metal surface and measure the indentation.
3. Impact Testing:
– Purpose: Assesses the material’s toughness and ability to absorb energy.
– Procedure: Charpy or Izod tests involve striking a notched sample with a pendulum hammer and measuring the absorbed energy.
4. Fatigue Testing:
– Purpose: Evaluates how the bracket withstands cyclic loading.
– Procedure: Samples are subjected to repeated loading cycles until failure occurs, simulating real-life stress conditions.
5. Corrosion Testing:
– Purpose: Checks resistance to corrosion and rust.
– Procedure: Exposing samples to corrosive environments (salt spray test) and observing the degradation over time.
6. Dimensional Inspection:
– Purpose: Ensures the brackets meet design specifications.
– Procedure: Using calipers, micrometers, and coordinate measuring machines (CMM) to measure dimensions and tolerances.
Quality Control Measures:
1. Incoming Material Inspection:
– Procedure: Verify the quality and specifications of raw materials before production.
2. In-Process Inspections:
– Procedure: Regular checks during manufacturing to detect defects early. This includes visual inspections, dimensional checks, and spot testing.
3. Statistical Process Control (SPC):
– Procedure: Use of control charts to monitor production processes and maintain consistency. Analyzing data helps in identifying and addressing variations.
4. Final Inspection:
– Procedure: Comprehensive testing of finished brackets to ensure they meet all specified criteria before shipment. Includes all aforementioned tests and visual inspections for surface defects.
5. Traceability:
– Procedure: Keeping detailed records of production batches and testing results to trace back any quality issues to their source.
By implementing these testing methods and control measures, manufacturers can ensure the quality and reliability of metal brackets, meeting industry standards and customer expectations.
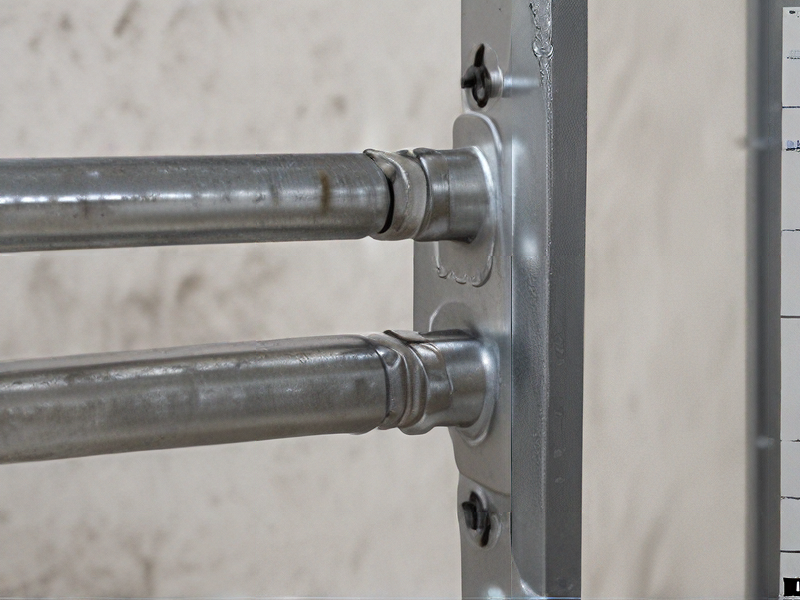
Tips for Procurement and Considerations when Purchasing from brackets metal
When procuring brackets from metal suppliers, consider these tips:
Material: Choose the right metal based on application needs:
* Steel: Strong, durable, versatile, available in various grades.
* Aluminum: Lightweight, corrosion-resistant, good for applications where weight is a factor.
* Stainless Steel: Highly corrosion-resistant, suitable for outdoor or harsh environments.
Finish:
* Galvanized: Provides corrosion protection.
* Powder Coated: Offers a durable and aesthetically pleasing finish.
* Plain: Cost-effective, but may require additional protection.
Specifications:
* Size and Shape: Ensure brackets meet your exact dimensional requirements.
* Load Capacity: Choose brackets capable of supporting the intended weight load.
* Fastening Type: Consider screw holes, slots, or other mounting methods.
Supplier Evaluation:
* Reputation: Research the supplier’s experience and reliability.
* Quality Control: Inquire about their quality assurance processes.
* Pricing and Lead Times: Compare quotes and delivery timelines from multiple suppliers.
Additional Tips:
* Request samples for testing.
* Clearly define your project specifications.
* Negotiate payment terms and warranties.
* Consider long-term supplier relationships for bulk orders.
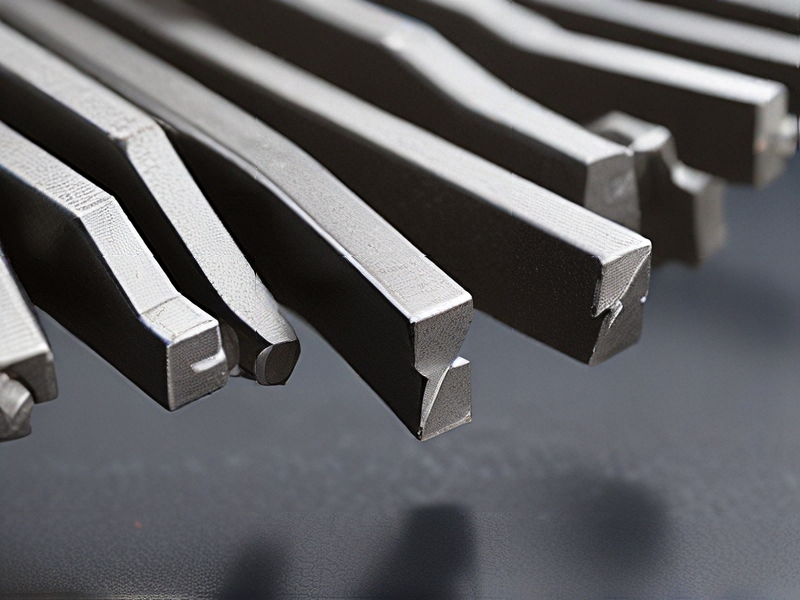
FAQs on Sourcing and Manufacturing from brackets metal in China
FAQs on Sourcing and Manufacturing Brackets Metal in China
1. Why source metal brackets from China?
– China offers competitive pricing, a wide range of manufacturers, and extensive experience in metal fabrication. The large-scale production capabilities often result in cost savings and high-quality products.
2. How do I find a reliable manufacturer?
– Use platforms like Alibaba, Made-in-China, and Global Sources. Verify manufacturers by checking reviews, requesting samples, and conducting factory audits, either in person or through third-party inspection services.
3. What are the key considerations when selecting a manufacturer?
– Consider the manufacturer’s experience, production capacity, quality control processes, and compliance with international standards. It’s also important to assess communication skills and responsiveness.
4. What are the common materials used for metal brackets in China?
– Common materials include stainless steel, aluminum, brass, and carbon steel. Each material offers different properties like corrosion resistance, strength, and cost.
5. What is the typical lead time for production?
– Lead times vary but generally range from 2 to 6 weeks, depending on the complexity of the design, order size, and the manufacturer’s current workload.
6. How can I ensure product quality?
– Specify clear product requirements and standards in your contract. Use quality assurance measures like pre-production samples, in-process inspections, and final product inspections before shipment.
7. What are the common payment terms?
– Payment terms typically include a 30% deposit upon order confirmation and the remaining 70% before shipment. Some manufacturers may offer terms like letters of credit for larger orders.
8. How are shipping and logistics handled?
– Manufacturers can handle shipping arrangements or you can use a freight forwarder. Common shipping methods include sea freight for large orders and air freight for smaller, urgent orders.
9. Are there any risks involved?
– Risks include communication barriers, quality inconsistencies, and delays. Mitigate these by working with reputable manufacturers, using contracts, and maintaining regular communication.
10. Do I need to handle import duties and customs?
– Yes, you will need to handle import duties, taxes, and customs clearance. It’s advisable to work with a customs broker to navigate these processes efficiently.
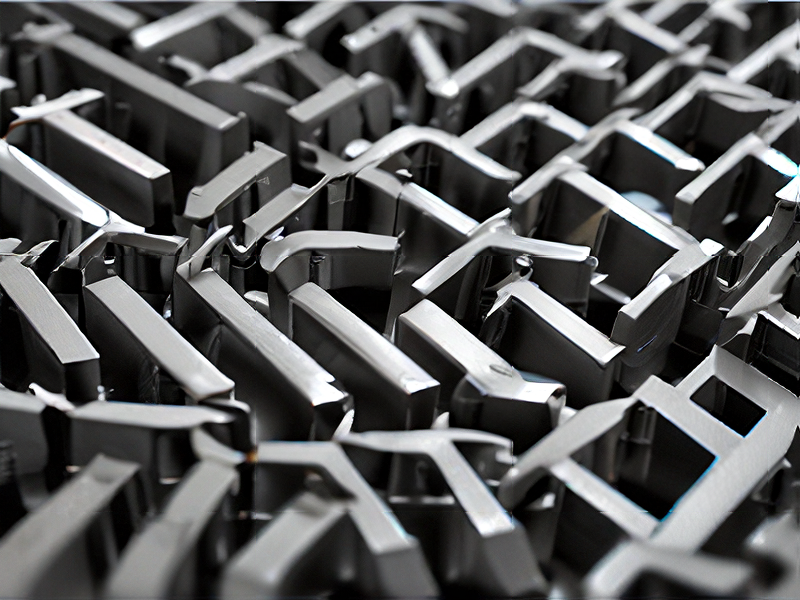