Technology and Applications of laser marking on metals
Laser marking on metals involves using a concentrated beam of light to create permanent marks or designs on metal surfaces. This technology leverages various laser types, such as fiber lasers, CO2 lasers, and UV lasers, each suited for different metal types and applications.
Technology
– Fiber Lasers: These use optical fibers doped with rare-earth elements. They are ideal for marking metals like stainless steel, aluminum, and brass due to their high precision and speed.
– CO2 Lasers: Typically used for non-metal materials, they can also mark certain metals with appropriate coatings or treatments.
– UV Lasers: They operate at shorter wavelengths, providing high precision and minimal thermal damage, making them suitable for marking delicate or heat-sensitive metals.
Applications
– Identification and Traceability: Laser marking is widely used for serial numbers, barcodes, and QR codes on industrial parts, ensuring traceability and compliance with regulatory standards.
– Branding and Customization: Manufacturers use laser marking to add logos, product information, and custom designs to metal products, enhancing brand recognition and product aesthetics.
– Jewelry and Decorative Items: Precision and high-quality marks make laser marking ideal for engraving intricate designs on jewelry and luxury items.
– Medical Devices: Laser marking ensures biocompatibility and sterilization compliance by marking surgical instruments and implants without affecting their integrity.
Advantages
– Durability: Laser marks are resistant to wear, corrosion, and high temperatures.
– Precision: Capable of creating intricate and detailed marks with high accuracy.
– Speed and Efficiency: Fast marking process suitable for high-volume production.
– Non-Contact Process: Reduces the risk of damaging delicate components.
Overall, laser marking on metals provides a versatile and reliable method for permanent marking across various industries, ensuring both functional and aesthetic benefits.
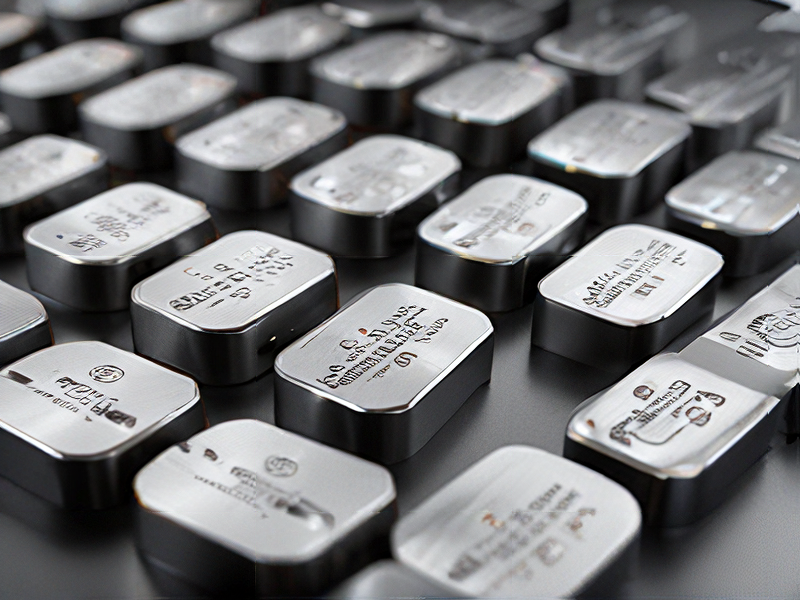
Quality Testing Methods for laser marking on metals and how to control quality
Quality testing for laser marking on metals involves several methods to ensure the markings are clear, durable, and accurate. Here are key methods and controls:
Testing Methods:
1. Visual Inspection:
– Microscopic Examination: Inspect under a microscope to check the clarity, precision, and edge quality of the markings.
– Color and Contrast: Evaluate the contrast between the mark and the substrate to ensure readability.
2. Durability Tests:
– Abrasion Resistance: Subject the marked surface to abrasive materials to test the mark’s resistance to wear.
– Chemical Resistance: Expose the marked area to various chemicals to assess its resistance.
3. Dimensional Accuracy:
– Coordinate Measuring Machines (CMM): Measure the dimensions of the marks to ensure they meet specified tolerances.
– Optical Comparators: Compare the marked patterns with a standard template.
4. Surface Roughness:
– Profilometry: Use a profilometer to measure the surface roughness of the marked area, ensuring it meets required smoothness standards.
5. Adhesion Tests:
– Tape Test: Apply and remove adhesive tape to see if the mark comes off, testing the adhesion strength of the marking.
Quality Control Measures:
1. Laser Calibration:
– Regularly calibrate the laser equipment to maintain precision and consistency in marking.
2. Environmental Control:
– Maintain consistent environmental conditions (temperature, humidity) in the marking area to avoid variations in marking quality.
3. Material Consistency:
– Ensure uniformity in the metal substrates being used, as variations can affect marking quality.
4. Process Documentation:
– Keep detailed records of marking parameters (laser power, speed, frequency) to replicate successful results and troubleshoot issues.
5. Training and Certification:
– Train operators on best practices and maintain certifications for handling and operating laser marking equipment.
Implementing these methods and controls helps achieve high-quality, durable laser markings on metals, ensuring they meet industry standards and customer expectations.
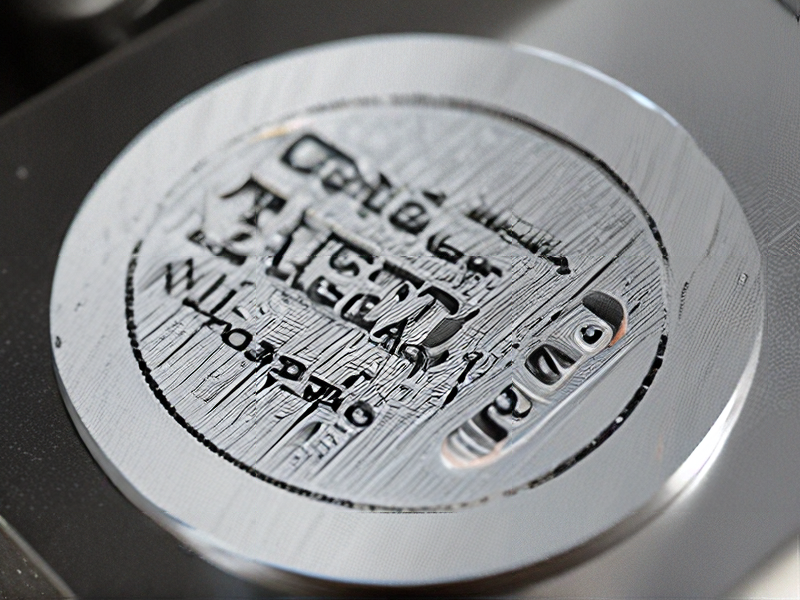
Tips for Procurement and Considerations when Purchasing from laser marking on metals
Tips for Procurement and Considerations when Purchasing Laser Marking Systems for Metals
1. Define Requirements: Clearly outline your marking needs, including the types of metals, marking depth, precision, and production volume. Different metals like stainless steel, aluminum, and titanium may require specific laser types and settings.
2. Laser Type: Choose the appropriate laser technology. Fiber lasers are typically preferred for metal marking due to their efficiency, durability, and ability to produce high-contrast marks without damaging the material.
3. System Capabilities: Ensure the laser marking system can handle the required range of metal types and thicknesses. Consider if the system allows for adjustments in power and speed to accommodate various applications.
4. Software Integration: Look for systems with user-friendly software that supports various file formats (e.g., DXF, SVG, AI) and offers features like batch processing, serial number generation, and barcode/QR code marking.
5. Precision and Quality: Evaluate the marking precision and quality. High-resolution marks are crucial for traceability, branding, and compliance with industry standards.
6. Speed and Efficiency: Consider the marking speed, especially if high throughput is necessary. Balance speed with marking quality to avoid sacrificing precision.
7. Cost: Factor in the total cost of ownership, including initial investment, maintenance, and operational costs. Higher upfront costs might be justified by long-term savings in durability and efficiency.
8. Safety Features: Ensure the system complies with safety standards, such as enclosed work areas, fume extraction, and interlock mechanisms, to protect operators from laser exposure and harmful fumes.
9. Vendor Support and Training: Choose a reputable vendor offering comprehensive support, including installation, training, and after-sales service. Proper training ensures efficient and safe use of the equipment.
10. Scalability and Upgrades: Select a system that allows for future upgrades and scalability to accommodate evolving marking needs and technological advancements.
11. Environmental Considerations: Evaluate the environmental impact, including energy consumption and waste management. Opt for energy-efficient systems that minimize waste.
By addressing these factors, you can make a well-informed decision, ensuring the laser marking system meets your specific needs and offers long-term value.
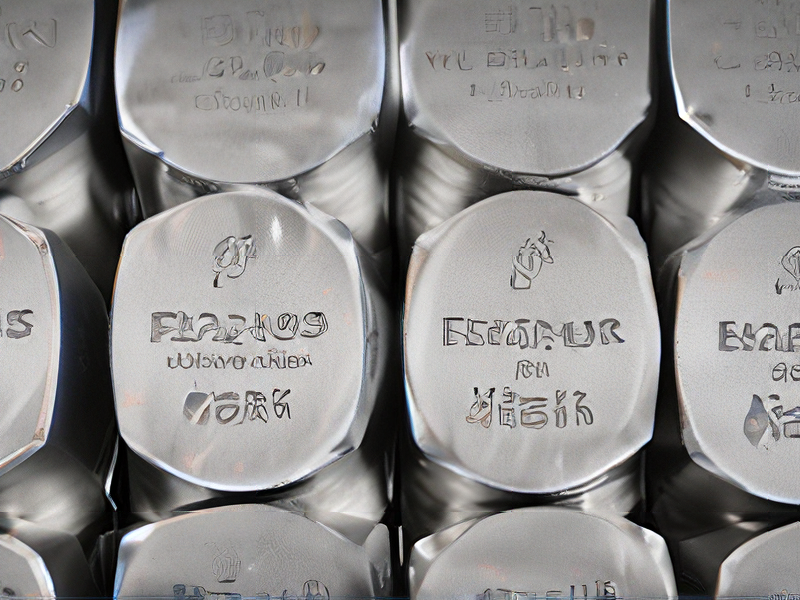
FAQs on Sourcing and Manufacturing from laser marking on metals in China
FAQs on Sourcing and Manufacturing for Laser Marking on Metals in China
#### 1. What is laser marking on metals?
Laser marking on metals involves using a focused laser beam to alter the surface of a metal, creating permanent marks such as logos, serial numbers, or barcodes. This process can include engraving, etching, or annealing.
#### 2. Why source laser marking services from China?
China is renowned for its manufacturing capabilities, offering cost-effective solutions, advanced technology, and a broad range of services. The competitive pricing, coupled with skilled labor and rapid production times, makes China a favorable destination for laser marking services.
#### 3. What metals can be laser marked?
Laser marking can be performed on various metals, including stainless steel, aluminum, brass, copper, and titanium. Each metal may require different laser settings for optimal results.
#### 4. How to ensure quality when sourcing from China?
To ensure quality:
– Research thoroughly: Choose reputable suppliers with good reviews and verified credentials.
– Request samples: Assess the quality of marking on sample products before placing large orders.
– Conduct audits: If possible, visit the manufacturing site or hire third-party inspectors.
#### 5. What are the typical lead times?
Lead times can vary based on the complexity and volume of the order. Typically, it ranges from a few days for small orders to several weeks for larger, more intricate projects.
#### 6. What are the cost factors?
Costs depend on the type of metal, the complexity of the design, the quantity ordered, and the precision required. Other factors include setup fees, shipping, and any additional finishing processes.
#### 7. Are there any legal considerations?
Ensure compliance with international trade regulations, intellectual property rights, and any specific standards required by your country or industry. It’s advisable to have clear contracts outlining terms and quality standards.
#### 8. How to handle shipping and logistics?
Partner with reliable logistics providers. Consider shipping costs, delivery times, and customs clearance. Many suppliers offer shipping services as part of their package, simplifying the process for buyers.
By addressing these FAQs, businesses can effectively navigate the process of sourcing and manufacturing laser marking on metals in China, ensuring quality and efficiency.
