Technology and Applications of what is cnc machines
Computer Numerical Control (CNC) machines are automated devices that control machining tools via a computer program. They are essential in manufacturing for precise, complex, and repeatable tasks. The technology behind CNC machines involves the use of digital instructions, typically created through Computer-Aided Design (CAD) and Computer-Aided Manufacturing (CAM) software, to dictate the movement and operation of machinery.
Key Technologies:
1. Controllers: The brain of CNC machines, translating code into mechanical motion.
2. Drive Systems: Include motors and actuators to move machine components precisely.
3. Feedback Systems: Sensors that ensure the machine follows programmed paths accurately.
4. Machine Interface: Software that allows operators to interact with the machine, inputting commands and monitoring operations.
Applications:
1. Automotive Industry: CNC machines produce engine parts, gears, and custom modifications.
2. Aerospace: Manufacturing of turbine blades, airframe components, and other precision parts.
3. Medical Devices: Production of implants, prosthetics, and surgical instruments.
4. Electronics: Creation of circuit boards and enclosures.
5. Prototyping: Rapid development of prototypes for product design and testing.
6. Woodworking: CNC routers carve complex designs into wood, creating furniture and cabinetry.
CNC technology revolutionizes manufacturing by enhancing precision, efficiency, and flexibility. The ability to automate complex machining tasks reduces human error, increases production speed, and allows for the manufacturing of intricate designs that would be difficult or impossible manually. As technology advances, CNC machines continue to evolve, incorporating artificial intelligence and advanced sensors, further broadening their applications and improving their capabilities.
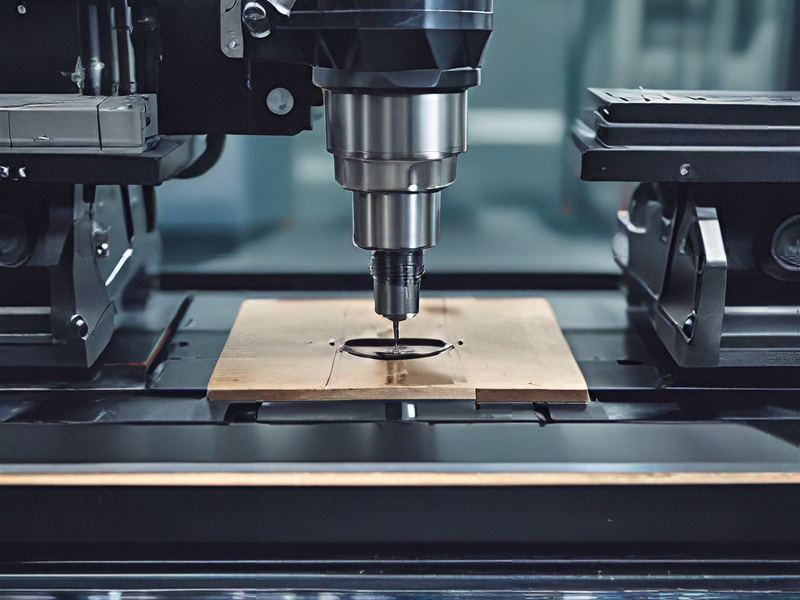
Quality Testing Methods for what is cnc machines and how to control quality
Quality Testing Methods for CNC Machines
CNC Machines Overview:
CNC (Computer Numerical Control) machines automate the control of machining tools through a computer, enabling high precision and repeatability in manufacturing processes. Common CNC machines include mills, lathes, and routers.
Quality Testing Methods:
1. Dimensional Inspection:
– Coordinate Measuring Machines (CMM): CMMs provide precise measurements of the physical geometrical characteristics of an object. They are crucial for ensuring the produced parts meet design specifications.
– Gauge Tools: Calipers, micrometers, and other gauge tools are used for quick checks and less complex parts.
2. Surface Finish Analysis:
– Profilometers: These devices measure surface roughness and texture to ensure the finished part meets the required surface quality standards.
3. Material Testing:
– Hardness Testing: Techniques like Rockwell, Brinell, or Vickers hardness tests are used to ensure the material properties of the machined parts are within specified limits.
– Tensile Testing: Ensures the material’s mechanical properties, such as strength and ductility, meet requirements.
4. Non-Destructive Testing (NDT):
– Ultrasonic Testing: Uses high-frequency sound waves to detect internal flaws or defects without damaging the part.
– X-ray Inspection: Provides detailed images of the internal structure of a part to identify defects like voids or inclusions.
5. Process Control:
– Statistical Process Control (SPC): Monitors the manufacturing process through control charts and statistical methods to detect variations and maintain consistent quality.
– Automated Inspection Systems: Integrated vision systems and sensors can inspect parts in real-time during production.
Quality Control Strategies:
– Standard Operating Procedures (SOPs): Documented processes for machine operation and maintenance to ensure consistency.
– Regular Calibration: Periodic calibration of machines and tools to maintain accuracy.
– Training and Certification: Ensuring operators are well-trained and certified to handle CNC machines and understand quality control measures.
These methods collectively ensure the quality of parts produced by CNC machines, maintaining high standards of precision and reliability in manufacturing.
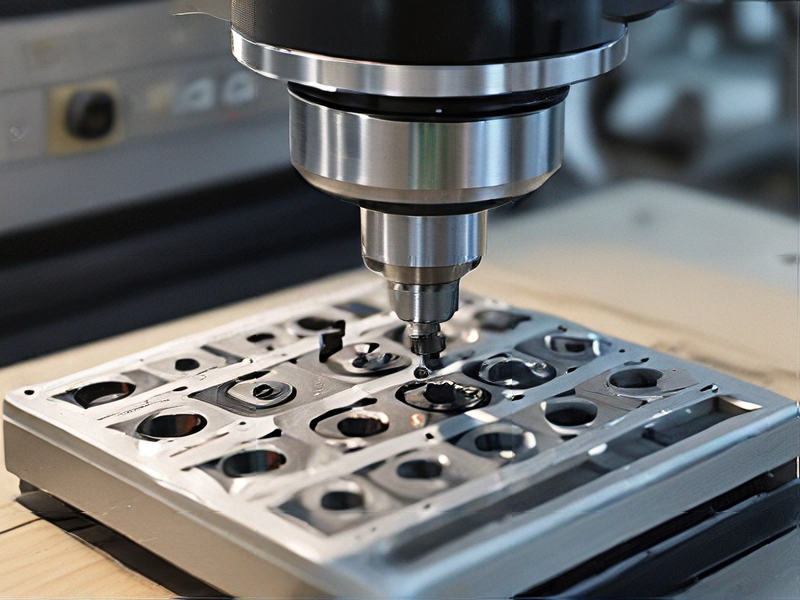
Tips for Procurement and Considerations when Purchasing from what is cnc machines
Tips for Procurement and Considerations when Purchasing CNC Machines
1. Assess Your Needs:
– Production Requirements: Identify the types of parts you need to produce, including material, complexity, and volume.
– Accuracy and Precision: Determine the required tolerances and surface finish.
2. Machine Specifications:
– Spindle Speed and Power: Ensure the machine can handle the materials you use and the required cutting speeds.
– Axis Configuration: Choose between 3, 4, or 5-axis machines based on the complexity of the parts.
– Table Size and Weight Capacity: Ensure the machine can accommodate your largest workpieces.
3. Budget Considerations:
– Initial Cost vs. Long-term Investment: Balance the upfront cost with the machine’s lifespan, maintenance, and operational costs.
– Financing Options: Explore leasing, financing, or buying used machines to manage cash flow.
4. Manufacturer and Support:
– Reputation and Reviews: Choose reputable manufacturers with good reviews and proven reliability.
– Technical Support and Training: Ensure the manufacturer provides robust after-sales support and training for your team.
5. Software and Compatibility:
– CAD/CAM Integration: Verify compatibility with your existing design and manufacturing software.
– Control System: Ensure the CNC control system is user-friendly and meets your operational needs.
6. Maintenance and Downtime:
– Maintenance Requirements: Understand the machine’s maintenance schedule and the availability of spare parts.
– Downtime Impact: Consider the machine’s reliability and the potential impact of downtime on your production schedule.
7. Safety and Compliance:
– Safety Features: Look for features like emergency stops, guards, and automatic shutdowns.
– Regulatory Compliance: Ensure the machine complies with local safety and environmental regulations.
8. Future-proofing:
– Scalability: Choose a machine that can grow with your business, handling increased production volumes or more complex parts.
– Technology Upgrades: Consider the ease of upgrading the machine with new technology or capabilities.
Careful consideration of these factors can help ensure you choose the right CNC machine for your needs, balancing performance, cost, and future growth.
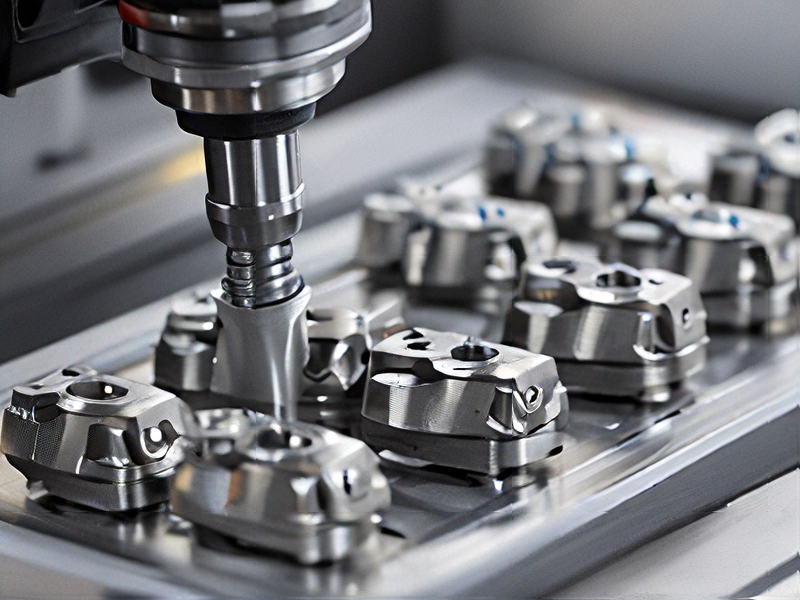
FAQs on Sourcing and Manufacturing from what is cnc machines in China
FAQs on Sourcing and Manufacturing CNC Machines in China
1. What are CNC machines?
CNC (Computer Numerical Control) machines are automated tools controlled by a computer, which precisely manipulate tools like drills, lathes, and mills to create parts from raw materials. They are widely used in manufacturing for their accuracy and efficiency.
2. Why source CNC machines from China?
China is a leading producer of CNC machines due to its large-scale manufacturing capabilities, cost-effective production, and advancements in technology. Sourcing from China can result in significant cost savings without compromising on quality.
3. How to find reliable CNC machine manufacturers in China?
– Online Platforms: Websites like Alibaba, Made-in-China, and Global Sources list numerous manufacturers.
– Trade Shows: Attending trade shows such as the China International Machine Tool Show (CIMT) can provide direct interaction with manufacturers.
– Referrals and Reviews: Checking reviews, asking for referrals, and conducting thorough background checks can ensure reliability.
4. What factors should be considered when selecting a manufacturer?
– Quality Standards: Ensure the manufacturer adheres to international quality standards such as ISO 9001.
– Customization: Check if they offer customization to meet specific requirements.
– After-Sales Support: Reliable after-sales service is crucial for maintenance and troubleshooting.
– Lead Time: Confirm the production and delivery timelines to match your schedule.
– Cost: Evaluate the total cost, including shipping, tariffs, and taxes.
5. What are the common challenges in sourcing from China?
– Communication: Language barriers can lead to misunderstandings; using clear and precise communication is essential.
– Quality Control: Regular inspections and third-party quality checks can help maintain product standards.
– Logistics: Navigating shipping and customs can be complex; using experienced freight forwarders can mitigate risks.
6. How to ensure quality and compliance?
– Factory Audits: Conducting factory audits ensures the manufacturer’s capabilities.
– Quality Inspections: Implementing pre-shipment inspections helps verify product quality before dispatch.
– Compliance Certifications: Verify that the manufacturer’s products meet relevant safety and quality certifications.
Sourcing CNC machines from China can be highly beneficial if due diligence is performed to ensure quality, reliability, and compliance with standards.
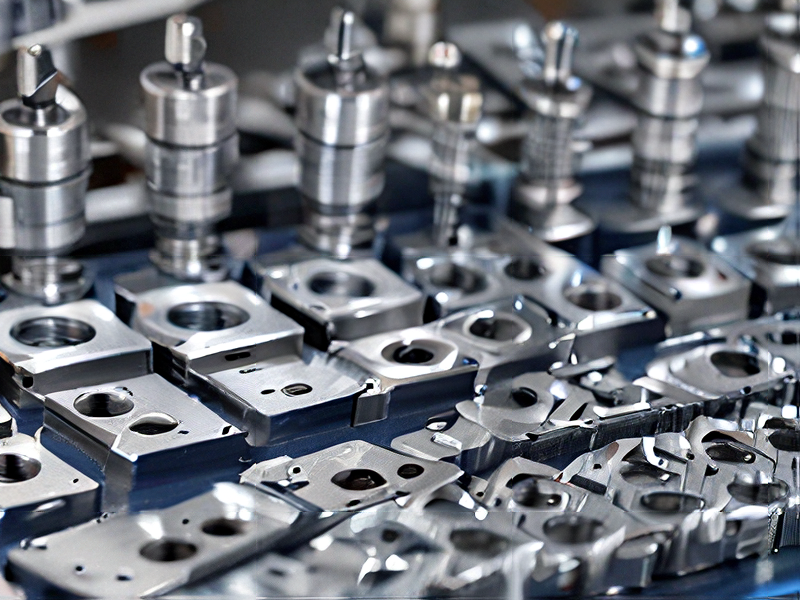