Technology and Applications of cleaning laser machine
Cleaning laser machines employ laser ablation, a process where laser energy is used to remove contaminants, coatings, or residues from surfaces. This technology offers a non-contact, precise, and environmentally friendly cleaning solution compared to traditional methods like chemical cleaning or abrasive blasting.
Technology
1. Laser Source: The core component is a high-powered laser, usually fiber, CO2, or Nd:YAG, which emits a focused beam of light.
2. Beam Delivery: The laser beam is directed through optical fibers and lenses to the target surface.
3. Control System: Advanced software controls the laser parameters such as power, pulse duration, and frequency, allowing customization for different cleaning tasks.
4. Scanning System: Galvanometer scanners or robotic arms move the laser beam across the surface, ensuring uniform cleaning.
Applications
1. Industrial Cleaning: Removal of rust, paint, and oxides from metals without damaging the underlying material. Used in aerospace, automotive, and shipbuilding industries.
2. Conservation and Restoration: Cleaning historical artifacts and artworks by precisely removing dirt and pollutants without harming the original material.
3. Precision Cleaning: In electronics and semiconductor industries, lasers clean delicate components and circuits without leaving residues or causing damage.
4. Surface Preparation: Pre-treatment of surfaces for better adhesion of coatings or welds. This application is common in manufacturing processes.
5. Medical Device Cleaning: Sterilizing and cleaning medical instruments where precision and cleanliness are crucial.
Advantages
– Non-Contact Process: Minimizes mechanical damage to sensitive surfaces.
– Eco-Friendly: Reduces the need for harmful chemicals and produces minimal waste.
– Precision: Enables targeted cleaning without affecting surrounding areas.
– Versatility: Effective on various materials, including metals, plastics, and composites.
Conclusion
Cleaning laser machines represent a cutting-edge solution for modern cleaning challenges, offering unparalleled precision, efficiency, and environmental benefits across diverse industries.
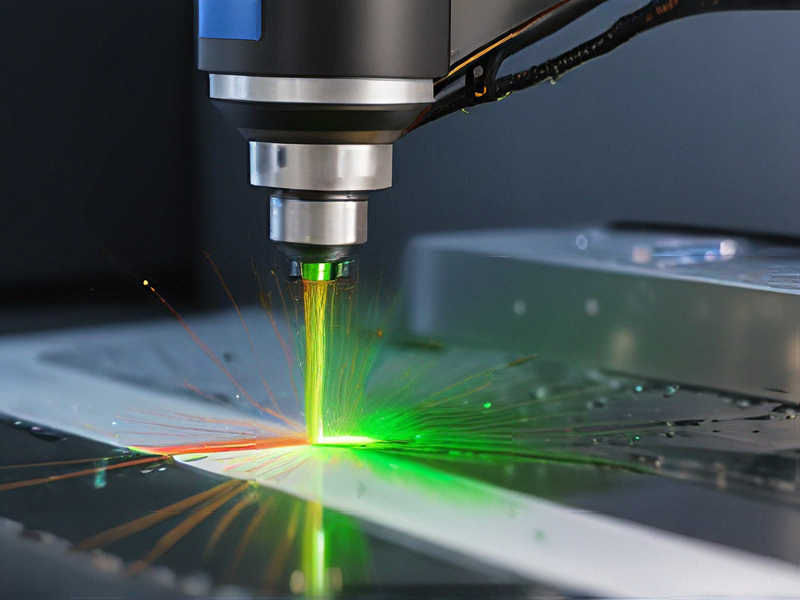
Quality Testing Methods for cleaning laser machine and how to control quality
Quality testing methods for cleaning a laser machine focus on ensuring that the equipment operates efficiently and without contamination. Here are the key methods and controls:
1. Visual Inspection
– Frequency: Before and after each cleaning.
– Purpose: Identify visible residues, dust, or damage on critical components like lenses, mirrors, and laser pathways.
– Tools: Magnifying glass, inspection lights.
2. Contamination Testing
– Swab Tests: Use sterile swabs to collect samples from various machine parts. Analyze for contaminants using microscopy or chemical assays.
– Residue Analysis: Utilize UV light to detect organic residues that are invisible to the naked eye.
3. Performance Testing
– Beam Quality Analysis: Measure the beam’s intensity and uniformity using a laser beam profiler to ensure optimal performance.
– Alignment Check: Use alignment tools to ensure the laser beam is correctly aligned with the optical path.
4. Environmental Monitoring
– Air Quality Control: Monitor the cleanliness of the air in the laser machine’s environment using air quality sensors. This prevents airborne particles from contaminating the machine.
– Humidity and Temperature Control: Ensure stable environmental conditions to prevent condensation or thermal stress on the machine components.
5. Routine Maintenance Records
– Logging Cleaning Activities: Maintain detailed logs of all cleaning activities, including dates, procedures followed, and any issues observed.
– Scheduled Maintenance: Implement a routine maintenance schedule to ensure regular inspection and cleaning.
6. Standard Operating Procedures (SOPs)
– Consistency: Develop and adhere to SOPs for cleaning to ensure consistency and thoroughness.
– Training: Regularly train personnel on proper cleaning techniques and SOPs to maintain high-quality standards.
Quality Control Measures
– Regular Audits: Conduct internal audits to ensure compliance with SOPs and identify areas for improvement.
– Feedback Mechanism: Implement a feedback system for operators to report any issues encountered during cleaning, enabling continuous improvement.
By integrating these methods and controls, you can maintain the cleanliness and performance of a laser machine, ensuring high-quality output and longevity of the equipment.
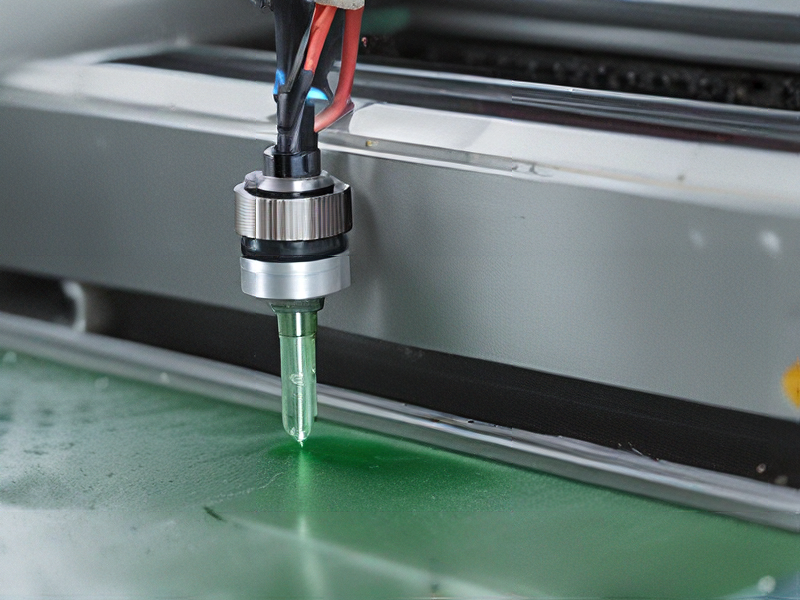
Tips for Procurement and Considerations when Purchasing from cleaning laser machine
When purchasing a cleaning laser machine, consider the following tips and factors to ensure you make an informed and effective decision:
Key Considerations
1. Application Needs:
– Identify the specific cleaning tasks you need the laser machine for (e.g., rust removal, paint stripping, surface preparation).
– Determine the types of materials you’ll be cleaning (metals, plastics, ceramics).
2. Power and Wavelength:
– Higher power lasers can clean more quickly and efficiently but may cost more.
– The wavelength of the laser affects its effectiveness on different materials. Choose accordingly.
3. Precision and Control:
– Look for machines with adjustable power settings and focus controls for precision cleaning.
– Consider machines with advanced software for better control over cleaning parameters.
4. Safety Features:
– Ensure the machine has robust safety features, including proper shielding, emergency stop functions, and safety interlocks.
– Verify compliance with local safety regulations and standards.
5. Ease of Use:
– Opt for user-friendly interfaces and controls.
– Check for features like automated cleaning modes and programmable settings.
6. Maintenance and Support:
– Investigate the maintenance requirements and the availability of spare parts.
– Ensure the manufacturer provides reliable customer support and training.
7. Portability and Size:
– Consider the size and weight of the machine, especially if you need to move it frequently.
– Some applications may benefit from portable or handheld models.
8. Cost and Budget:
– Balance the upfront cost with the machine’s long-term benefits and operational costs.
– Look for warranties and after-sales services to protect your investment.
Procurement Tips
1. Research and Reviews:
– Read reviews and case studies to understand the performance and reliability of different models.
– Engage with industry forums and peers for recommendations.
2. Supplier Reliability:
– Choose reputable suppliers with a track record of delivering high-quality machines and good customer service.
– Verify the supplier’s credentials and certifications.
3. Trials and Demonstrations:
– Request demonstrations or trial periods to test the machine’s capabilities before purchase.
– Assess the machine’s performance in your specific cleaning applications.
4. Training and Installation:
– Ensure the supplier provides adequate training for your staff.
– Confirm installation services and initial setup support are included.
By thoroughly evaluating these factors, you can make a well-informed decision that meets your operational needs and budget constraints.
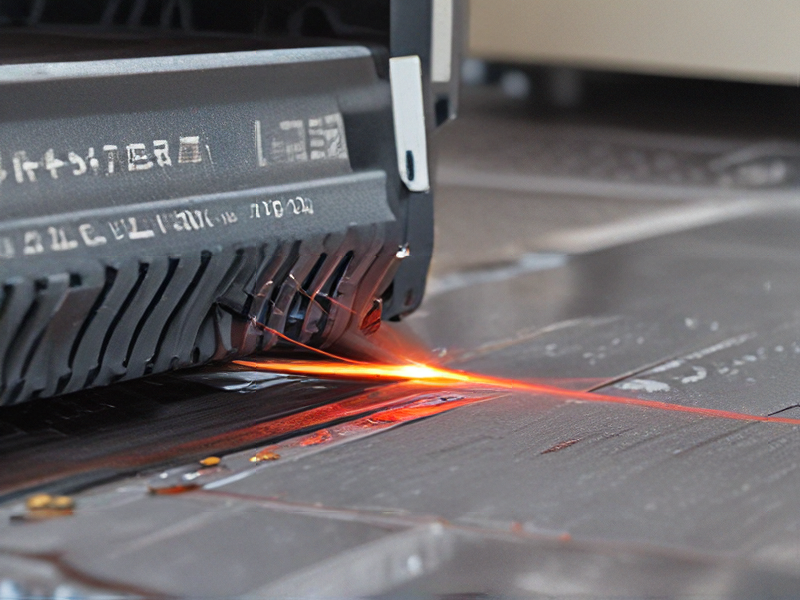
FAQs on Sourcing and Manufacturing from cleaning laser machine in China
FAQs on Sourcing and Manufacturing Cleaning Laser Machines in China
1. Why should I source cleaning laser machines from China?
China offers competitive pricing, a wide range of manufacturers, and advanced technology in laser cleaning machines. The country’s robust manufacturing infrastructure and extensive experience make it a cost-effective option.
2. How do I find reliable manufacturers in China?
Utilize online platforms like Alibaba, Made-in-China, and Global Sources. Look for suppliers with high ratings, positive reviews, and verified status. Attending trade shows and using sourcing agents can also help identify reliable manufacturers.
3. What should I consider when choosing a supplier?
Assess the supplier’s experience, quality certifications (e.g., ISO, CE), production capacity, and ability to provide after-sales support. Request samples and visit their facilities if possible to ensure they meet your quality standards.
4. What is the typical lead time for manufacturing?
Lead times can vary, but generally, it takes 30-60 days from order placement to shipment. This includes production, quality checks, and packaging. Custom orders may take longer.
5. How can I ensure the quality of the machines?
Implement strict quality control measures. This can include pre-production samples, regular inspections during manufacturing, and third-party quality assurance checks. Specify detailed product requirements and standards in your contract.
6. What are the shipping options and costs?
Shipping options include sea freight (most economical for large orders), air freight (faster but costlier), and express courier services (for smaller quantities). Shipping costs depend on the machine size, weight, and destination. Work with freight forwarders to manage logistics.
7. Are there import duties and taxes?
Yes, import duties and taxes apply and vary by country. Consult with customs brokers to understand the applicable fees and ensure compliance with import regulations.
8. How can I handle after-sales service and maintenance?
Choose suppliers that offer comprehensive after-sales support, including warranties, spare parts, and technical assistance. Some suppliers may have local service centers or partners to facilitate maintenance and repairs.
9. What payment terms are typically offered?
Common payment terms include a 30% deposit upon order confirmation and the remaining 70% before shipment. Letters of credit and escrow services can provide additional payment security.
10. How do I protect my intellectual property?
Use non-disclosure agreements (NDAs) and non-compete clauses in your contracts. Register your patents and trademarks in China to safeguard your intellectual property rights.
By considering these aspects, you can effectively source and manufacture cleaning laser machines from China, ensuring quality and reliability in your procurement process.
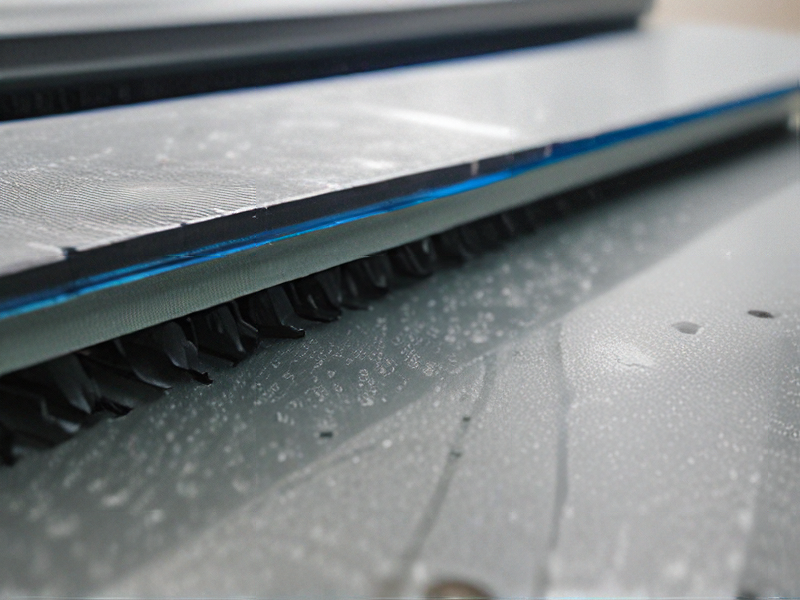