Technology and Applications of iron metal melting point
Iron, with a melting point of approximately 1538°C (2800°F), is a critical material in various industries due to its abundant availability and versatile properties. The melting point of iron is significant in its applications, particularly in manufacturing and metallurgy.
Technology and Processes
1. Blast Furnace:
Iron ore is smelted in a blast furnace to produce pig iron, a key raw material for steelmaking. The process involves reducing iron ore using coke and limestone at high temperatures, reaching the melting point of iron.
2. Electric Arc Furnace (EAF):
EAFs are used to melt scrap iron and steel using electrical energy. This process is more flexible and environmentally friendly, as it recycles steel, reducing the need for raw ore and decreasing carbon emissions.
3. Induction Furnace:
Induction furnaces use electromagnetic induction to heat and melt iron. This method is efficient for melting scrap iron and allows precise control over the temperature, essential for producing high-quality steel alloys.
Applications
1. Construction:
Iron and its alloys, primarily steel, are fundamental in construction for building frameworks, bridges, and infrastructure due to their strength and durability.
2. Automotive Industry:
Steel, derived from iron, is crucial in manufacturing car bodies, engines, and other components, providing safety, strength, and longevity.
3. Machinery and Tools:
Iron-based materials are used in producing machinery, tools, and equipment essential in various industries, from agriculture to manufacturing.
4. Shipbuilding:
The shipbuilding industry relies on steel for constructing hulls and structural components, ensuring the vessels’ strength and resilience in harsh marine environments.
5. Appliances and Consumer Goods:
Iron and steel are used in household appliances, kitchenware, and other consumer goods, valued for their durability and resistance to wear.
Iron’s high melting point is integral to its role in these technologies and applications, ensuring the production of robust, high-quality materials essential to modern industry and daily life.
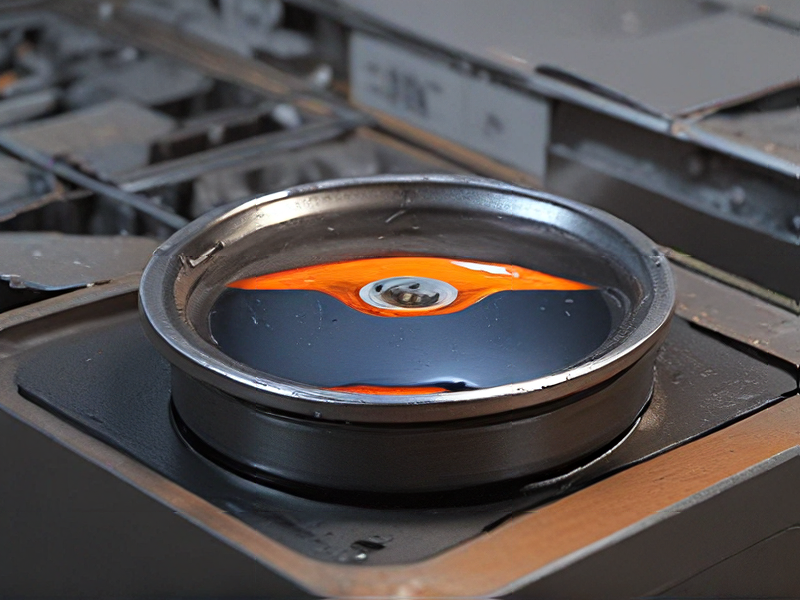
Quality Testing Methods for iron metal melting point and how to control quality
Quality Testing Methods for Iron Melting Point
1. Differential Scanning Calorimetry (DSC):
– Process: Measures heat flow into a sample as it is heated, providing precise melting point data.
– Advantages: High accuracy and sensitivity.
2. Thermal Analysis (TA):
– Process: Techniques like thermogravimetric analysis (TGA) and differential thermal analysis (DTA) monitor physical and chemical changes under controlled heating.
– Advantages: Provides comprehensive thermal properties and behavior.
3. Pyrometry:
– Process: Uses a pyrometer to measure high temperatures without contact.
– Advantages: Ideal for high-temperature processes and real-time measurements.
Quality Control Measures
1. Material Purity:
– Testing: Chemical analysis (e.g., X-ray fluorescence) to detect impurities.
– Control: Ensure raw materials meet purity standards to maintain consistent melting points.
2. Consistent Heating Rates:
– Testing: Use calibrated equipment to maintain uniform heating rates during testing.
– Control: Regular calibration and maintenance of heating equipment to avoid discrepancies.
3. Environmental Conditions:
– Testing: Monitor and control atmospheric conditions, as oxygen and humidity can affect melting points.
– Control: Conduct tests in controlled environments to ensure reliable results.
4. Sample Preparation:
– Testing: Standardize sample size and shape for uniformity.
– Control: Implement strict protocols for sample preparation to reduce variability.
5. Repeatability and Reproducibility:
– Testing: Perform multiple tests to confirm consistency.
– Control: Use statistical process control (SPC) to monitor and maintain quality standards.
By implementing these methods and controls, you can ensure the accurate determination of iron’s melting point and maintain high-quality standards in production and testing processes.
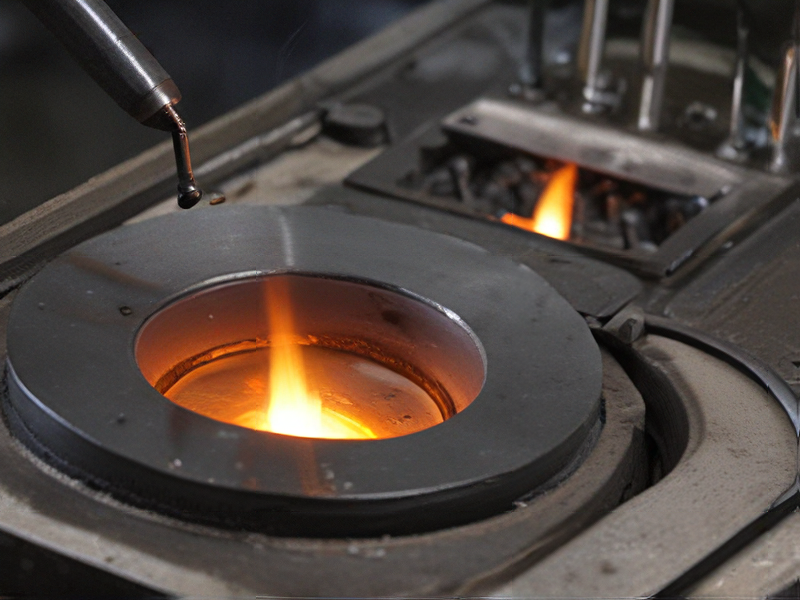
Tips for Procurement and Considerations when Purchasing from iron metal melting point
When procuring iron metal, particularly for applications involving its melting point (1538°C or 2800°F), several considerations are crucial to ensure quality and efficiency:
Tips for Procurement
1. Supplier Reliability: Choose reputable suppliers with a track record of delivering high-quality iron. Verify their certifications and industry standards compliance.
2. Material Specifications: Clearly define the required iron specifications, including purity levels, alloy content, and physical properties. Ensure these align with your application needs.
3. Volume Requirements: Assess your volume needs accurately. Bulk purchasing can often lead to cost savings, but ensure storage and handling capabilities are in place.
4. Quality Assurance: Implement strict quality control measures. Request sample testing and quality certifications to ensure the iron meets your standards.
5. Logistics and Lead Time: Consider the supplier’s location and their delivery timelines. Factor in potential delays and ensure they can meet your production schedules.
6. Cost Analysis: Perform a thorough cost-benefit analysis, including base material cost, shipping, handling, and potential wastage. Compare multiple suppliers to get the best value.
Considerations for Iron Melting Point
1. Furnace Capability: Ensure your melting furnace can achieve and sustain the iron melting point of 1538°C. The furnace should have adequate capacity and control systems for consistent performance.
2. Energy Consumption: High temperatures required for melting iron demand substantial energy. Evaluate the energy efficiency of your furnace and consider options for reducing consumption to lower operational costs.
3. Safety Measures: High-temperature operations pose significant safety risks. Implement rigorous safety protocols, including protective equipment for workers, emergency procedures, and regular equipment maintenance.
4. Environmental Impact: Melting iron can produce significant emissions. Consider environmental regulations and implement measures to minimize your ecological footprint, such as emission control systems and recycling waste materials.
5. Material Handling: Proper handling of molten iron is critical. Use high-quality crucibles and molds that can withstand extreme temperatures without degrading.
By focusing on these procurement tips and melting point considerations, you can ensure a successful and efficient iron procurement and melting process.
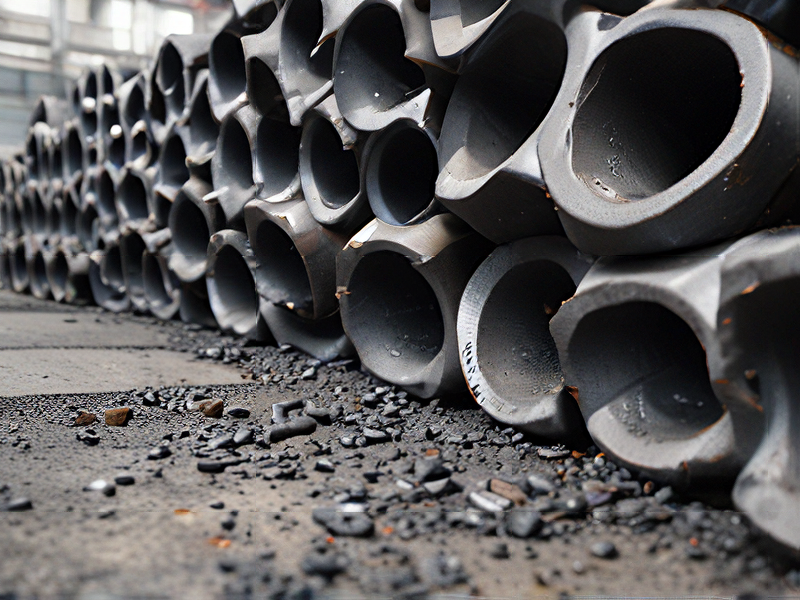
FAQs on Sourcing and Manufacturing from iron metal melting point in China
FAQs on Sourcing and Manufacturing Iron Metal from China
1. What is the melting point of iron?
The melting point of iron is approximately 1,538 degrees Celsius (2,800 degrees Fahrenheit).
2. Why source iron metal from China?
China is one of the largest producers of iron and steel, offering competitive prices, a wide range of suppliers, and advanced manufacturing capabilities. This makes China an attractive option for sourcing high-quality iron metal.
3. What are the quality standards for iron in China?
Chinese manufacturers adhere to various international quality standards, including ISO, ASTM, and GB (Chinese National Standards). It is crucial to specify the required standards when placing orders.
4. How to find reliable iron metal suppliers in China?
Researching through trade platforms like Alibaba, Made-in-China, and Global Sources, attending trade fairs, and seeking recommendations from industry contacts can help in identifying reliable suppliers. Verifying credentials, certifications, and conducting factory audits are also important steps.
5. What are the common methods of iron production in China?
The primary methods include blast furnace production and electric arc furnace (EAF) production. Blast furnaces are commonly used for large-scale production, while EAFs are utilized for more specialized or recycled iron production.
6. How to ensure the quality of iron metal sourced from China?
Quality assurance can be achieved by:
– Specifying detailed material and quality requirements.
– Requesting samples before full production.
– Conducting third-party inspections.
– Establishing clear terms in contracts regarding quality control and penalties for non-compliance.
7. What are the logistics involved in importing iron metal from China?
Key considerations include:
– Choosing reliable freight forwarders.
– Understanding shipping terms (FOB, CIF, etc.).
– Ensuring proper documentation (Bill of Lading, Packing List, Certificate of Origin, etc.).
– Complying with import regulations and duties of the destination country.
8. How to address language and cultural barriers?
Hiring bilingual staff, using professional translation services, and understanding Chinese business etiquette can facilitate smoother communication and negotiations.
By addressing these FAQs, businesses can effectively navigate the complexities of sourcing and manufacturing iron metal from China.
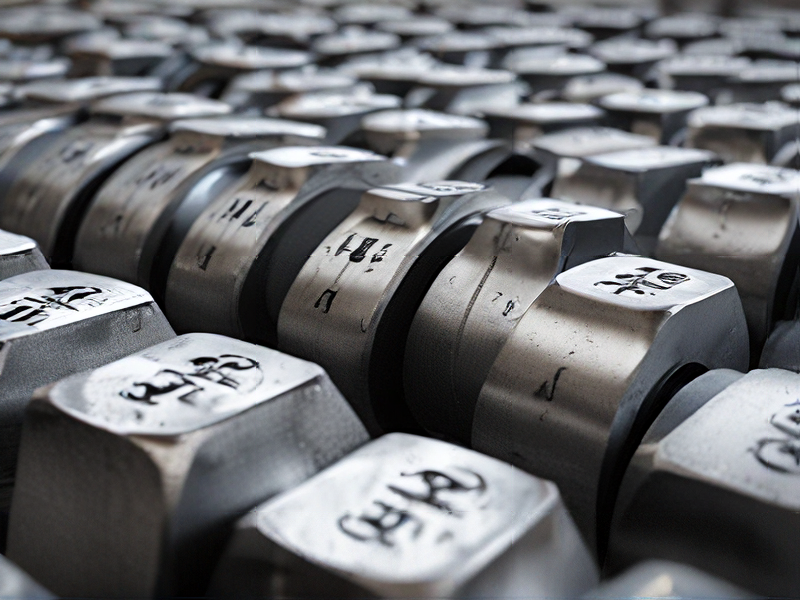