Technology and Applications of electrical discharge machining edm
Electrical Discharge Machining (EDM) is a non-traditional manufacturing process that uses electrical discharges to shape metal materials. It is particularly useful for machining hard materials and complex shapes that are difficult to achieve with conventional methods.
Technology
EDM works by generating a series of rapid, repetitive electrical discharges (sparks) between an electrode and the workpiece, both submerged in a dielectric fluid. The sparks erode material from the workpiece in the shape of the electrode, allowing precise and intricate machining. The two main types of EDM are:
1. Die-Sinking EDM: Uses a shaped electrode that is gradually fed into the workpiece. It’s ideal for producing complex cavities and shapes in molds and dies.
2. Wire EDM: Employs a thin, electrically charged wire as the electrode to cut contours and intricate shapes. It is especially useful for producing parts with intricate, delicate geometries.
Applications
EDM is used across various industries due to its ability to precisely machine hard and heat-treated materials. Key applications include:
1. Aerospace: Manufacturing turbine blades, jet engine components, and other high-precision parts.
2. Automotive: Producing molds, dies, and engine components.
3. Medical: Creating intricate surgical instruments and implants.
4. Tool and Die Making: Crafting complex molds and dies for plastic injection molding, die-casting, and forging.
5. Electronics: Fabricating micro-components and precision parts for electronic devices.
Advantages
– Precision: Achieves tight tolerances and fine finishes.
– Complex Shapes: Easily machines intricate geometries and hard materials.
– No Mechanical Stress: The lack of contact between tool and workpiece reduces the risk of mechanical stress and deformation.
Limitations
– Slow Material Removal Rate: EDM is slower compared to conventional machining processes.
– Electrode Wear: The electrode gradually wears out, requiring frequent replacements or redressing.
– High Costs: The process and equipment can be expensive, especially for small-scale production.
Overall, EDM is a critical technology in modern manufacturing, enabling the production of high-precision and complex components in various industries.
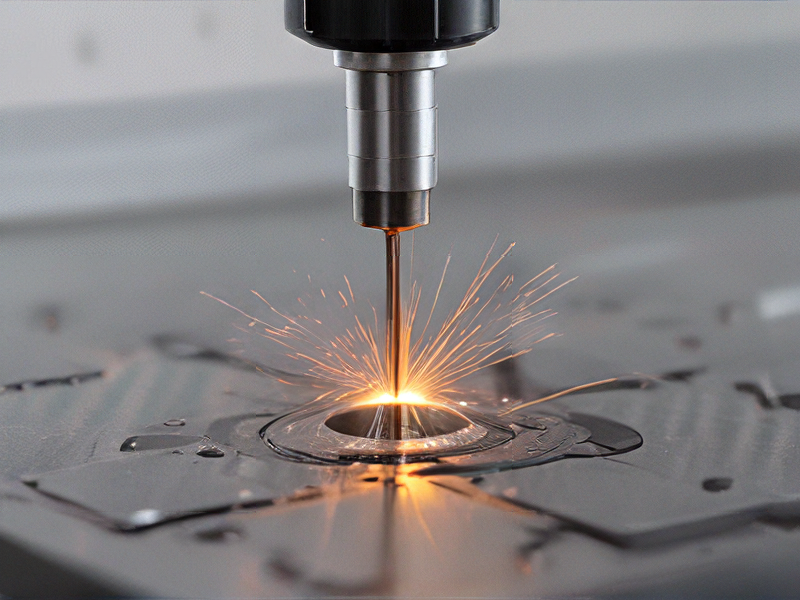
Quality Testing Methods for electrical discharge machining edm and how to control quality
Quality Testing Methods for EDM
1. Surface Roughness Measurement:
– Purpose: To assess the smoothness of the machined surface.
– Method: Tools like profilometers measure the surface texture and roughness, providing quantitative data.
2. Dimensional Accuracy:
– Purpose: Ensures the machined part meets design specifications.
– Method: Use calipers, micrometers, and coordinate measuring machines (CMM) for precise dimensional checks.
3. Microhardness Testing:
– Purpose: Determines the hardness of the machined surface, which can affect wear resistance.
– Method: Vickers or Knoop microhardness tests measure hardness on a microscopic scale.
4. Material Integrity Testing:
– Purpose: Detects defects such as cracks or residual stresses.
– Method: Techniques like X-ray diffraction (XRD) or scanning electron microscopy (SEM) analyze the material’s microstructure and identify any issues.
5. Electrical Parameters Monitoring:
– Purpose: Ensures the EDM process parameters are optimal.
– Method: Continuous monitoring of voltage, current, and pulse duration during the EDM process to maintain consistency.
Quality Control Strategies
1. Process Parameter Optimization:
– Approach: Regularly calibrate and adjust machine settings (e.g., voltage, current, pulse duration) to ensure consistent quality.
– Implementation: Use statistical process control (SPC) to monitor and control EDM parameters.
2. Regular Maintenance:
– Approach: Maintain EDM equipment regularly to prevent mechanical failures and inaccuracies.
– Implementation: Schedule routine checks and servicing of the machine components.
3. Operator Training:
– Approach: Train operators on the nuances of EDM and quality standards.
– Implementation: Continuous education and certification programs to keep skills up-to-date.
4. Post-Machining Inspection:
– Approach: Conduct thorough inspections after machining.
– Implementation: Use a combination of visual inspections and advanced measurement tools to verify quality.
5. Feedback Loop:
– Approach: Implement a feedback system for continuous improvement.
– Implementation: Analyze inspection data to identify trends and areas for process improvements.
By integrating these methods and strategies, the quality of EDM machined parts can be effectively controlled and improved.
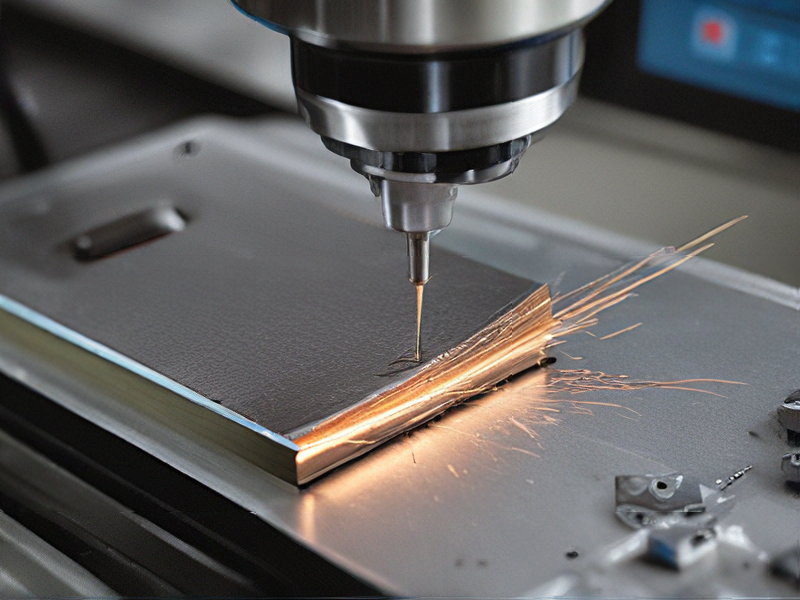
Tips for Procurement and Considerations when Purchasing from electrical discharge machining edm
When procuring Electrical Discharge Machining (EDM) equipment, several tips and considerations can ensure a successful purchase:
1. Assess Requirements:
– Define the specific needs of your operations, including the type of materials, desired precision, and production volume. Consider whether you need a sinker EDM, wire EDM, or hole drilling EDM based on your application.
2. Budget and Cost:
– Evaluate the total cost of ownership, including initial purchase price, operational costs, maintenance, and consumables like electrodes and dielectric fluids. Balance cost with the expected return on investment.
3. Machine Specifications:
– Examine critical specifications such as machining accuracy, surface finish quality, maximum workpiece size, and electrical capacity. Ensure the machine meets your precision and tolerance requirements.
4. Technology and Features:
– Look for advanced features such as CNC controls, automation capabilities, and software compatibility for better productivity and ease of use. Modern machines may offer improved energy efficiency and better ergonomic designs.
5. Supplier Reputation:
– Choose reputable suppliers with a proven track record in the industry. Consider the availability of after-sales support, training, and technical assistance. Read reviews and seek recommendations from other users.
6. Maintenance and Downtime:
– Investigate the maintenance requirements and availability of spare parts. Machines with easy maintenance protocols and readily available parts reduce downtime and increase productivity.
7. Compliance and Safety:
– Ensure the equipment complies with industry standards and safety regulations. Proper safety features, such as automatic shut-offs and protective enclosures, are crucial for safe operation.
8. Training and Support:
– Verify if the supplier provides comprehensive training for your operators. Proper training ensures optimal use of the machine and reduces the risk of operational errors.
9. Trial and Demonstration:
– Request a demonstration or trial run to assess the machine’s performance in real-world conditions. This helps verify the machine’s capabilities and suitability for your specific applications.
10. Long-term Viability:
– Consider the long-term support and potential for future upgrades. Machines with modular designs and upgrade paths can extend the lifespan of your investment.
By carefully evaluating these factors, you can make an informed decision and select the EDM equipment that best suits your operational needs and budget.
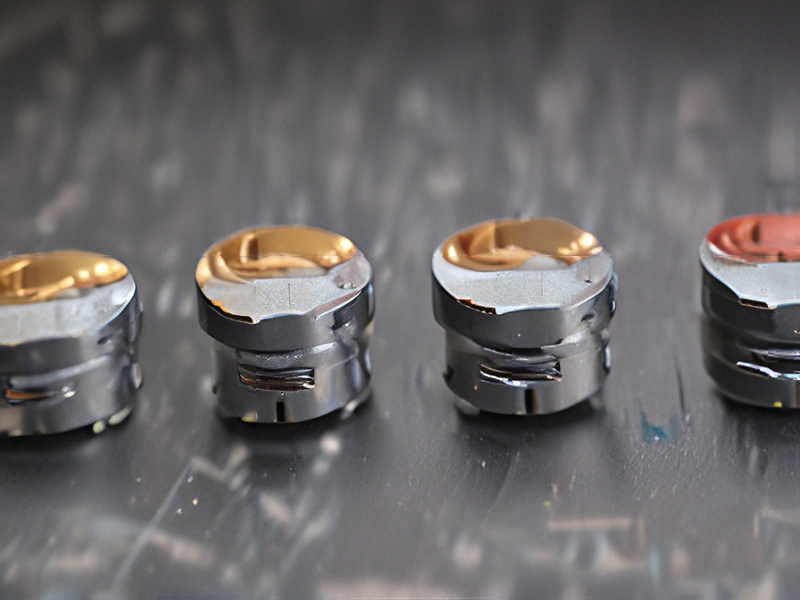
FAQs on Sourcing and Manufacturing from electrical discharge machining edm in China
FAQs on Sourcing and Manufacturing Electrical Discharge Machining (EDM) in China
1. What is EDM?
Electrical Discharge Machining (EDM) is a manufacturing process where material is removed from a workpiece using electrical discharges (sparks). It is particularly useful for creating intricate shapes and working with hard materials.
2. Why source EDM services from China?
China offers competitive pricing, advanced technology, skilled labor, and a wide range of suppliers capable of handling complex EDM projects. The country’s extensive manufacturing infrastructure supports efficient and large-scale production.
3. How do I find reliable EDM suppliers in China?
Utilize online platforms like Alibaba, Made-in-China, and Global Sources to identify potential suppliers. Additionally, attend trade shows like the China International Machine Tool Show (CIMT) to meet suppliers in person.
4. What should I look for in a supplier?
Consider factors such as the supplier’s experience, certifications (ISO 9001), capacity, quality control processes, and previous client reviews. Request samples to assess quality firsthand.
5. How can I ensure quality control?
Implement a stringent quality control process, including defining clear specifications, conducting regular inspections, and employing third-party quality control services. Communication and detailed contracts are crucial.
6. What are the typical lead times for EDM projects in China?
Lead times can vary based on the project’s complexity and the supplier’s capacity, typically ranging from a few weeks to a few months. Clear communication and planning can help manage timelines effectively.
7. What are the payment terms usually required by Chinese suppliers?
Common payment terms include a 30% deposit upfront, with the remaining 70% paid upon completion or before shipment. Letters of credit and other secure payment methods can be negotiated.
8. Are there any risks involved?
Risks include potential communication barriers, quality issues, and intellectual property concerns. Mitigate these risks through thorough vetting, detailed contracts, regular monitoring, and possibly hiring a local agent.
9. How can I handle shipping and logistics?
Collaborate with experienced freight forwarders to handle shipping and customs. Ensure proper documentation and consider incoterms (FOB, CIF) that best suit your needs.
10. What are the benefits of long-term partnerships with Chinese suppliers?
Long-term partnerships can lead to better pricing, improved communication, higher priority for your orders, and a deeper understanding of each other’s processes and standards, enhancing overall efficiency and quality.
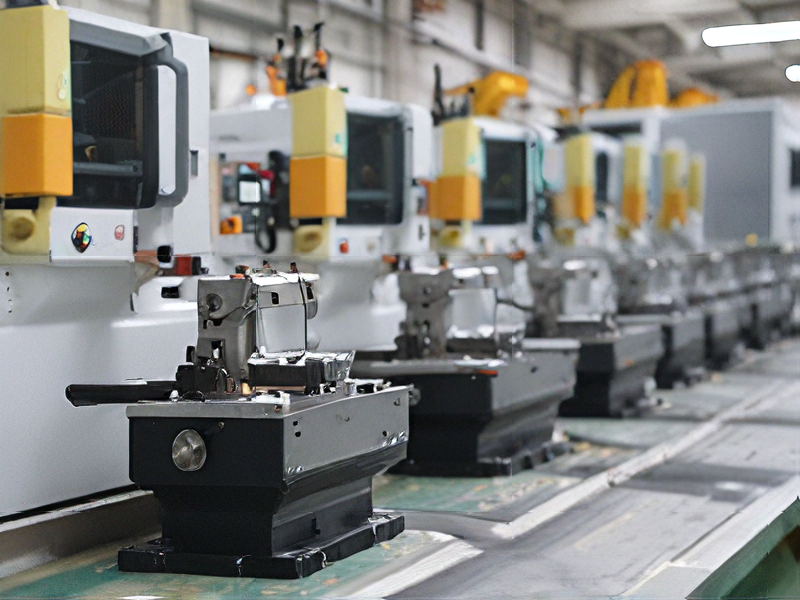