Technology and Applications of labeling machinery
Labeling machinery technology has advanced significantly, offering diverse applications across various industries. These machines are designed to apply labels to products, containers, or packages efficiently and accurately. Here’s an overview of the technology and its applications:
Technology:
1. Automation: Modern labeling machines often feature automation for enhanced speed and precision. This includes automated adjustments for different label sizes and shapes, reducing manual intervention.
2. Sensors and Vision Systems: These components ensure labels are placed accurately. Vision systems can inspect labels for correct placement, orientation, and quality, minimizing errors.
3. Versatile Designs: Machines are designed to handle various label types, such as pressure-sensitive, shrink-sleeve, and in-mold labels. They can also accommodate different container shapes and sizes, from bottles to boxes.
4. High-Speed Capabilities: Advanced labeling machinery can process thousands of units per hour, essential for large-scale manufacturing operations.
5. Integration with Production Lines: Labeling machines can be integrated into existing production lines, working seamlessly with other equipment like filling, capping, and packaging machines.
Applications:
1. Food and Beverage Industry: Labeling machinery is used to apply labels to bottles, cans, and jars, providing essential information like ingredients, nutritional facts, and branding.
2. Pharmaceuticals: Ensuring compliance with regulations, these machines apply labels with dosage instructions, expiry dates, and batch numbers.
3. Cosmetics and Personal Care: Precision labeling enhances the appearance and branding of products like lotions, shampoos, and perfumes.
4. Logistics and Shipping: Labeling machines are crucial for applying shipping labels and barcodes, aiding in tracking and inventory management.
5. Automotive: Labels are used for parts identification, safety warnings, and compliance information.
6. Chemical and Industrial Products: Labels provide handling instructions, safety data, and product specifications.
In summary, labeling machinery technology integrates automation, sensors, and high-speed capabilities to cater to various industries’ needs, enhancing efficiency, accuracy, and compliance.
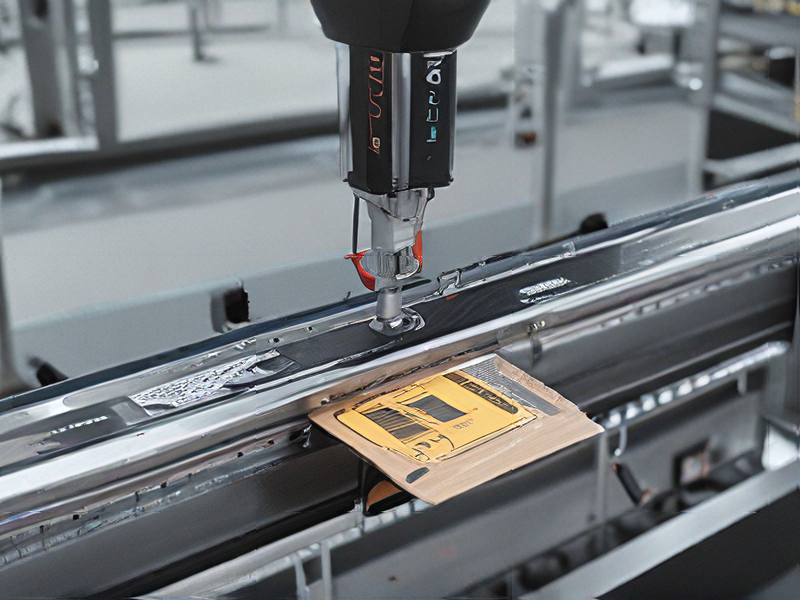
Quality Testing Methods for labeling machinery and how to control quality
Quality testing methods for labeling machinery ensure that labels are applied accurately, securely, and consistently. Key methods and controls include:
Visual Inspection
Regularly check the labels for proper alignment, placement, and legibility. Inspect for any misprints, skewing, or wrinkles.
Functional Testing
Conduct tests to ensure labels adhere properly under various conditions. This includes adhesion tests where labels are exposed to temperature changes, moisture, and friction to verify durability.
Measurement Tools
Use precision measurement tools like calipers and alignment gauges to verify the exact positioning and dimensions of labels.
Automation and Sensors
Implement automated vision systems and sensors to detect and reject improperly labeled products in real-time. These systems can check for correct label application and read barcodes or QR codes for verification.
Consistency Checks
Regularly test the machinery’s consistency in label application over prolonged periods. This involves running sample batches and checking for any deviations.
Adhesion Testing
Perform peel tests to measure the force required to remove labels, ensuring they remain affixed during the product’s life cycle.
Regular Maintenance
Schedule routine maintenance to prevent wear and tear of machinery parts that could affect labeling accuracy. This includes checking the tension of belts, rollers, and other moving parts.
Operator Training
Ensure operators are well-trained to handle machinery, conduct inspections, and identify potential issues. Regular training updates keep staff informed about best practices and new technologies.
Calibration
Regularly calibrate machinery to maintain accuracy in label placement. Calibration ensures that mechanical components are aligned and functioning correctly.
Documentation and Audits
Maintain detailed records of testing procedures, results, and maintenance activities. Conduct regular audits to ensure compliance with quality standards and identify areas for improvement.
By combining these methods, manufacturers can maintain high labeling quality, minimize errors, and ensure compliance with industry standards.
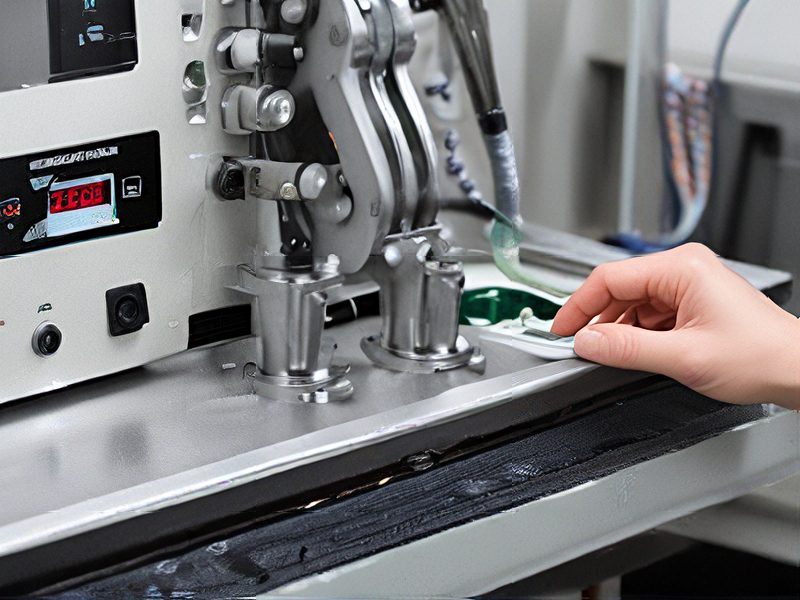
Tips for Procurement and Considerations when Purchasing from labeling machinery
When procuring labeling machinery, several key factors should be considered to ensure an optimal purchase that meets your operational needs:
1. Define Requirements: Identify your labeling needs, including the type of products, production volume, and specific labeling formats. Consider future growth and scalability.
2. Research and Compare: Investigate different manufacturers and models. Compare features, durability, and compatibility with your existing systems. Read reviews and seek recommendations from industry peers.
3. Budget Considerations: Establish a clear budget but remain flexible for quality and reliability. Remember that lower upfront costs may lead to higher maintenance expenses later.
4. Quality and Reliability: Opt for machines from reputable manufacturers known for quality and durability. Reliable machines reduce downtime and increase productivity.
5. Technology and Integration: Ensure the machine’s technology is up-to-date and can integrate seamlessly with your current production line. Look for features like ease of operation, flexibility in label sizes, and automation capabilities.
6. After-Sales Support: Choose suppliers that offer robust after-sales support, including training, maintenance, and readily available spare parts. Reliable technical support can minimize downtime and operational disruptions.
7. Compliance and Standards: Ensure the machinery complies with industry standards and regulations. This is critical for food, pharmaceuticals, and other sectors with stringent labeling requirements.
8. Test and Validate: If possible, conduct trials to test the machine’s performance in real-world conditions. Validate its speed, accuracy, and reliability before making a final decision.
9. Warranty and Service Agreements: Evaluate the warranty terms and consider service agreements that cover regular maintenance and unforeseen repairs.
10. Training and Usability: Ensure your staff can operate the machinery efficiently. User-friendly machines with comprehensive training programs can significantly enhance productivity.
By carefully considering these factors, you can make a well-informed decision, ensuring that the labeling machinery you purchase will meet your needs effectively and provide a good return on investment.
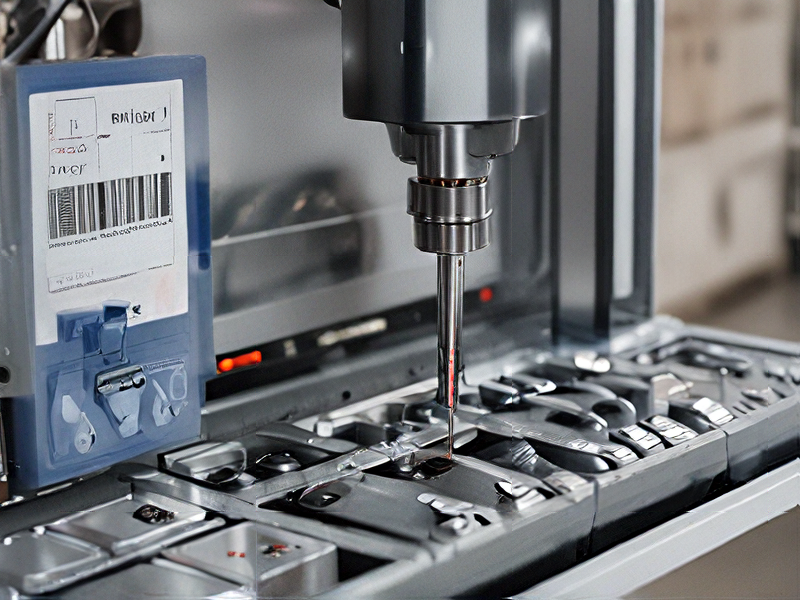
FAQs on Sourcing and Manufacturing from labeling machinery in China
FAQs on Sourcing and Manufacturing Labeling Machinery in China
#### 1. Why source labeling machinery from China?
China is known for its competitive pricing, diverse manufacturing capabilities, and extensive experience in producing labeling machinery. Manufacturers often provide customization options and can handle large volume orders efficiently.
#### 2. How do I find reliable manufacturers?
Use platforms like Alibaba, Global Sources, and Made-in-China. Check reviews, request references, and verify certifications. Visiting trade shows or conducting factory visits can also help establish reliability.
#### 3. What are the key factors to consider when selecting a manufacturer?
Evaluate the manufacturer’s experience, production capacity, quality control processes, and ability to meet international standards. Assess their responsiveness, communication skills, and willingness to provide samples or prototypes.
#### 4. How can I ensure the quality of the labeling machinery?
Request detailed specifications and conduct third-party inspections. Consider working with local agents or consultants to oversee quality control and factory audits. Ensure the machinery complies with relevant certifications such as CE, ISO, or UL.
#### 5. What is the typical lead time for manufacturing and delivery?
Lead times vary but generally range from 30 to 90 days, depending on the complexity and quantity of the order. Factor in additional time for shipping and potential customs clearance delays.
#### 6. What are the payment terms usually offered?
Common payment terms include a 30% deposit before production and the remaining 70% before shipment. Letters of credit and escrow services can offer additional security.
#### 7. How do I handle shipping and logistics?
Work with experienced freight forwarders familiar with importing from China. They can assist with customs documentation, insurance, and choosing the most efficient shipping methods, whether by sea or air.
#### 8. Are there any risks involved in sourcing from China?
Risks include quality inconsistencies, communication barriers, and intellectual property concerns. Mitigate these by conducting thorough due diligence, maintaining clear contracts, and considering legal protections for your designs and patents.
#### 9. Can I get after-sales support and training?
Many Chinese manufacturers offer after-sales support, including installation, training, and maintenance services. Confirm these provisions before finalizing your order and ensure they are documented in your contract.
#### 10. What about warranty and spare parts?
Ensure the manufacturer provides a warranty, typically ranging from 1 to 2 years. Discuss the availability of spare parts and their delivery times to minimize downtime in case of machinery breakdowns.
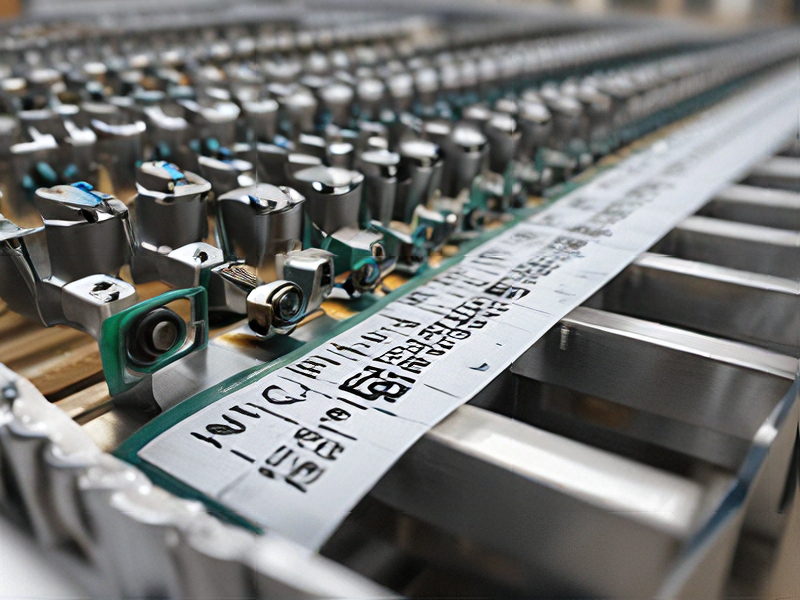