Technology and Applications of label machinery
Label machinery encompasses a wide range of technologies designed to automate the application of labels on products, packaging, and other surfaces. These machines are crucial in various industries, including food and beverage, pharmaceuticals, cosmetics, and logistics, for enhancing productivity, accuracy, and compliance with labeling regulations.
Technologies in Label Machinery
1. Pressure-Sensitive Labeling: Utilizes adhesive-backed labels that stick to surfaces upon contact. These are versatile and widely used for various product shapes and sizes.
2. Heat-Shrink Labeling: Involves labels that shrink upon heating to conform tightly to the contours of the container, offering 360-degree coverage and tamper-evidence.
3. In-Mold Labeling (IML): Integrates labels into the molding process of containers, creating a durable and seamless label application often used in high-volume packaging.
4. RFID Labeling: Embeds Radio Frequency Identification (RFID) tags within labels for advanced tracking, inventory management, and anti-counterfeiting measures.
5. Print and Apply Systems: Combine printing and labeling functions in one machine, allowing for real-time customization and variable data printing directly on the production line.
Applications of Label Machinery
1. Product Identification and Branding: Ensures clear and attractive presentation of product information, brand logos, and marketing messages.
2. Compliance and Safety: Meets regulatory requirements for information display, such as nutritional facts, ingredients, warnings, and expiry dates.
3. Traceability and Inventory Management: Facilitates tracking of products through the supply chain, enhancing transparency and efficiency.
4. Anti-Counterfeiting: Uses advanced label technologies like holographic seals and RFID tags to protect against product falsification.
5. Automation and Efficiency: Increases production speed, reduces labor costs, and minimizes human errors in the labeling process.
In conclusion, the advancement in label machinery technology significantly boosts operational efficiency, accuracy, and regulatory compliance across various industries, making it an indispensable component of modern manufacturing and logistics operations.

Quality Testing Methods for label machinery and how to control quality
Quality testing for label machinery involves several key methods to ensure the equipment functions correctly and produces high-quality labels. Here are some common methods and control measures:
1. Visual Inspection:
– Purpose: Detects obvious defects like misalignment, smudging, or improper cutting.
– Process: Regularly check printed labels against predefined quality standards.
2. Functional Testing:
– Purpose: Ensures machinery operates as expected under various conditions.
– Process: Run the machinery at different speeds and loads to verify performance.
3. Calibration:
– Purpose: Maintains accuracy in label placement and printing.
– Process: Regularly calibrate sensors, cutters, and printers according to manufacturer guidelines.
4. Durability Testing:
– Purpose: Tests the longevity and resistance of labels to various environmental factors.
– Process: Expose labels to conditions like heat, moisture, and abrasion to assess durability.
5. Dimensional Analysis:
– Purpose: Ensures labels meet precise size specifications.
– Process: Use tools like calipers and micrometers to measure label dimensions.
Quality Control Measures
1. Standard Operating Procedures (SOPs):
– Develop and follow detailed SOPs for every stage of the labeling process to ensure consistency and quality.
2. Training and Certification:
– Regularly train operators and technicians on quality standards and new technologies to maintain high performance.
3. Preventive Maintenance:
– Schedule regular maintenance to prevent machinery breakdowns and ensure continuous quality output.
4. Automated Quality Control Systems:
– Integrate vision systems and other automated quality control technologies to detect defects in real-time and reduce human error.
5. Data Collection and Analysis:
– Collect and analyze data from production runs to identify trends, potential issues, and areas for improvement.
6. Feedback Loops:
– Establish feedback mechanisms from the end-users and the quality control team to continuously improve processes and address issues promptly.
By implementing these methods and controls, manufacturers can ensure their label machinery consistently produces high-quality labels, thereby enhancing overall efficiency and customer satisfaction.
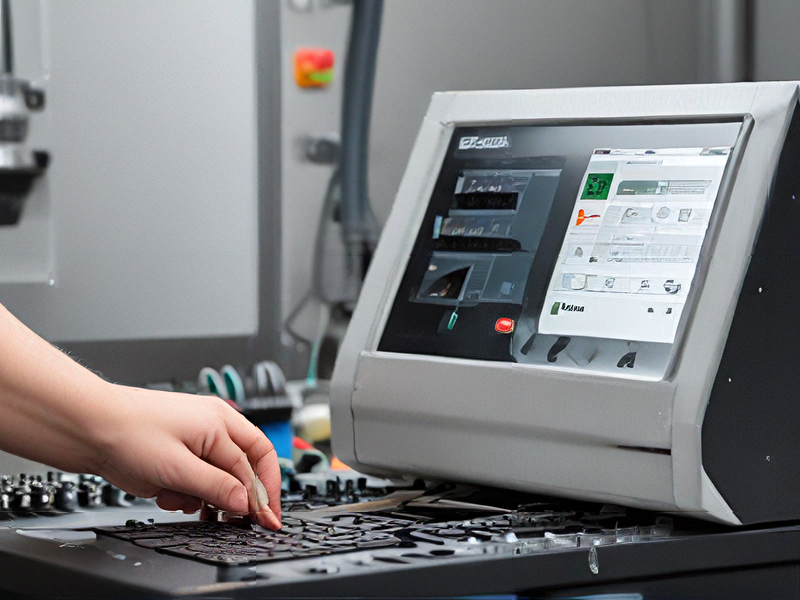
Tips for Procurement and Considerations when Purchasing from label machinery
Tips for Procurement and Considerations When Purchasing Label Machinery
1. Define Your Requirements:
– Volume and Speed: Determine the production volume and speed needed. Choose machinery that matches your production capacity to avoid bottlenecks or underutilization.
– Label Types and Sizes: Ensure the machine can handle the range of label types (e.g., pressure-sensitive, shrink sleeve) and sizes your operation requires.
2. Budget and Cost Analysis:
– Initial Investment vs. Long-Term Costs: Consider not just the upfront cost but also the long-term operational and maintenance expenses. Look for machines that offer a balance between cost and efficiency.
– Total Cost of Ownership (TCO): Factor in installation, training, consumables, and potential downtime costs.
3. Quality and Reliability:
– Brand Reputation: Opt for well-known brands with a proven track record in the industry. Check reviews and case studies.
– Warranty and Support: Ensure the manufacturer offers comprehensive warranty and reliable customer support.
4. Technology and Features:
– Automation and Integration: Look for machines with advanced automation features that can integrate with your existing systems for streamlined operations.
– Ease of Use: User-friendly interfaces and easy maintenance features can significantly reduce training time and operational errors.
5. Compliance and Safety:
– Regulatory Standards: Ensure the machinery complies with relevant industry standards and regulations to avoid legal issues and ensure safety.
– Safety Features: Prioritize machines with robust safety features to protect operators and reduce the risk of accidents.
6. Flexibility and Scalability:
– Future-Proofing: Choose machinery that can adapt to future needs, such as changes in label design or production scale.
– Modular Design: Machines with modular components allow for easy upgrades and modifications.
7. Vendor Selection:
– Supplier Reliability: Work with reputable suppliers who provide excellent after-sales service, training, and spare parts availability.
– Trial and Demos: Whenever possible, request a demonstration or trial period to evaluate the machine’s performance in your specific operational context.
By thoroughly considering these factors, you can make an informed decision that aligns with your production goals and ensures a smooth, efficient, and cost-effective labeling process.
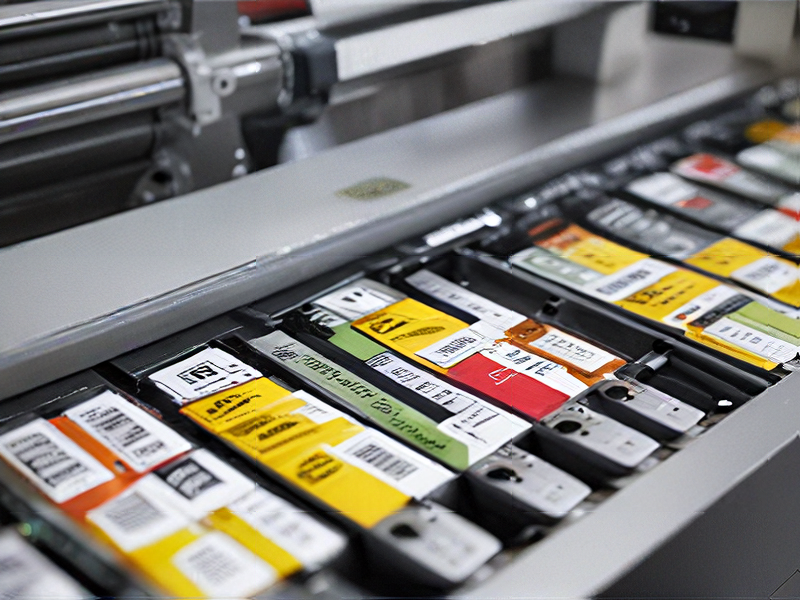
FAQs on Sourcing and Manufacturing from label machinery in China
FAQs on Sourcing and Manufacturing Label Machinery in China
1. Why source label machinery from China?
– Cost-Effective: Lower manufacturing and labor costs.
– Advanced Technology: Access to the latest technology and innovations.
– Diverse Options: Wide range of machinery to meet different needs.
2. How do I find reliable suppliers?
– Online Marketplaces: Use platforms like Alibaba, Made-in-China, and Global Sources.
– Trade Shows: Attend trade fairs such as Canton Fair or China International Label Printing Technology Exhibition.
– Referrals: Seek recommendations from industry peers.
3. What should I consider when evaluating suppliers?
– Reputation: Check reviews, ratings, and certifications.
– Experience: Look for suppliers with a proven track record in label machinery.
– Quality Control: Assess their quality assurance processes and after-sales service.
4. How can I ensure product quality?
– Factory Audits: Conduct on-site inspections or hire third-party audit services.
– Sample Testing: Request and test samples before full-scale production.
– Contracts: Clearly outline quality standards and penalties for non-compliance in contracts.
5. What are the common payment terms?
– Initial Deposit: Typically, 30% upfront.
– Balance Payment: 70% upon completion or before shipment.
– Letter of Credit: Secure payment method for larger transactions.
6. How do I handle shipping and logistics?
– Freight Forwarders: Use experienced freight forwarders for smoother logistics.
– Incoterms: Familiarize yourself with international commercial terms (e.g., FOB, CIF).
– Customs: Ensure all necessary documentation and compliance with import regulations.
7. What are the potential risks and how to mitigate them?
– Communication Barriers: Use clear, concise communication; consider hiring a translator if necessary.
– Cultural Differences: Understand business etiquette and practices in China.
– Intellectual Property (IP): Register your IP in China and use Non-Disclosure Agreements (NDAs).
8. What support is available post-purchase?
– Technical Support: Many suppliers offer remote or on-site technical support.
– Training: Some suppliers provide training for your staff on using the machinery.
– Spare Parts: Ensure the availability of spare parts and after-sales service.
Sourcing and manufacturing label machinery in China can be highly beneficial if approached with due diligence and thorough planning.
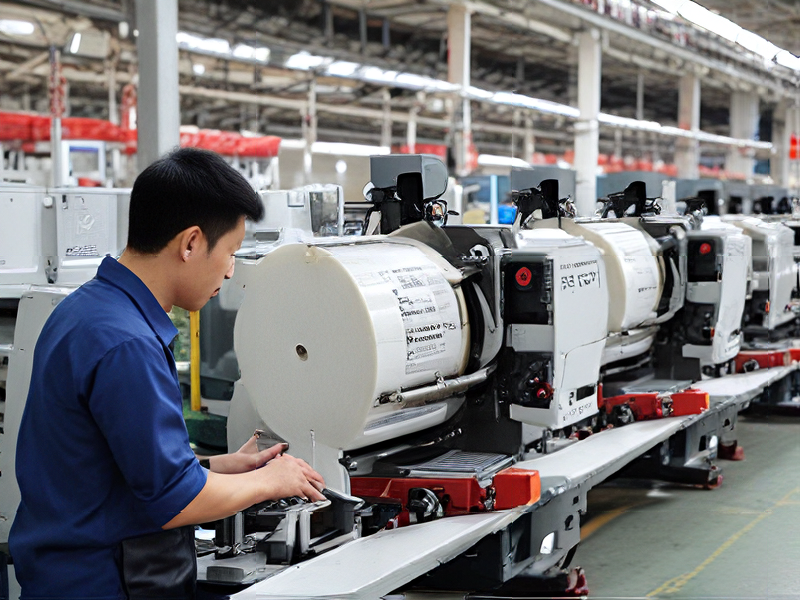