Technology and Applications of plasma cutter cnc
Technology and Applications of Plasma Cutter CNC
Plasma cutter CNC (Computer Numerical Control) technology integrates plasma cutting with computer-aided control to deliver precision and efficiency in metal cutting. Utilizing a high-velocity jet of ionized gas (plasma), these cutters can slice through electrically conductive materials such as steel, aluminum, and copper with ease.
Technology:
1. Plasma Generation: A plasma cutter generates plasma by sending an electric arc through a gas, typically compressed air. This transforms the gas into plasma, which can reach temperatures up to 30,000 degrees Fahrenheit.
2. CNC Control: The CNC aspect involves using computer programming to control the cutting path with high precision. G-code, a programming language, is employed to dictate movements of the cutting head.
3. Components: Key components include the plasma torch, power supply, CNC controller, and a cutting table. The CNC controller ensures precise movement and positioning of the torch based on the programmed design.
Applications:
1. Manufacturing and Fabrication: Plasma cutter CNC machines are extensively used in manufacturing industries to cut parts for machinery, vehicles, and construction equipment. Their ability to handle thick and thin metals makes them versatile for diverse applications.
2. Automotive Industry: These machines are utilized for cutting and shaping car components, such as chassis and body panels, ensuring high precision and reducing manual labor.
3. Art and Design: Artists and designers use plasma cutter CNCs to create intricate metal artworks, decorative panels, and custom signage.
4. Shipbuilding and Aerospace: In shipbuilding, they cut large metal sheets for hulls and decks. In aerospace, they ensure the precision cutting of high-strength materials used in aircraft structures.
5. Repair and Maintenance: Plasma cutters are also valuable in maintenance and repair shops for cutting and removing worn-out metal parts.
In summary, plasma cutter CNC technology revolutionizes metal cutting by combining the high temperatures and precision of plasma cutting with the accuracy of CNC control, leading to enhanced productivity and broad applicability across various industries.
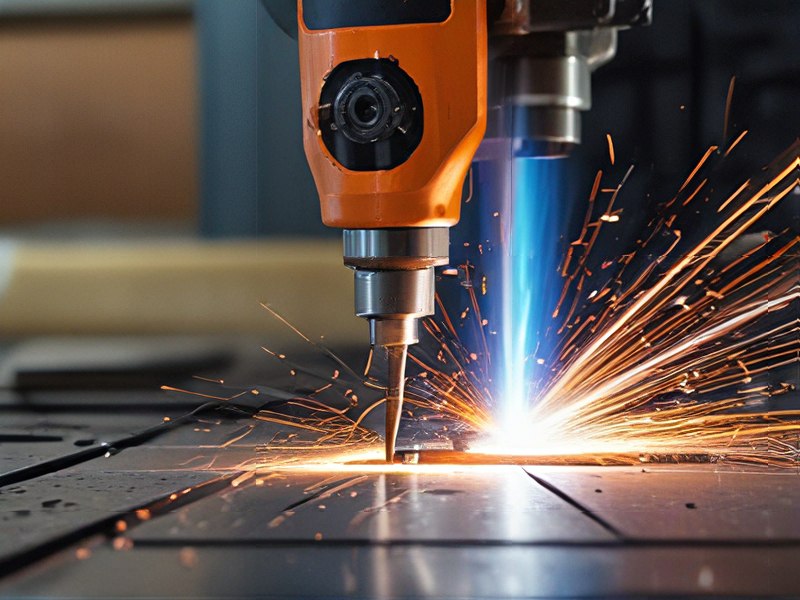
Quality Testing Methods for plasma cutter cnc and how to control quality
Quality testing for plasma cutter CNC (Computer Numerical Control) systems involves several methods to ensure precision, efficiency, and safety. Here are key testing methods and quality control measures:
Quality Testing Methods:
1. Cut Quality Inspection:
– Visual Inspection: Assess the smoothness and consistency of the cuts. Look for dross (excess material) and evaluate the squareness of edges.
– Dimensional Accuracy: Measure the dimensions of the cut parts against specifications using calipers and other measuring tools.
2. Material Testing:
– Hardness Testing: Verify the material’s hardness before and after cutting to ensure it meets required specifications.
– Metallurgical Analysis: Check for changes in the material’s structure due to the cutting process.
3. Thermal Imaging:
– Use thermal cameras to detect hot spots and ensure even heat distribution, preventing warping and structural weaknesses.
4. Surface Finish Testing:
– Measure the surface roughness of the cut edges using profilometers to ensure smoothness and quality.
5. Destructive Testing:
– Perform tensile tests or bend tests on sample cuts to check for strength and durability.
Quality Control Measures:
1. Calibration and Maintenance:
– Regularly calibrate the CNC machine and maintain plasma torches to ensure consistent performance.
– Replace worn parts to maintain cutting precision.
2. Software Verification:
– Use updated and verified software for programming cuts, ensuring accurate control over the cutting process.
3. Operator Training:
– Ensure operators are well-trained in using the CNC machine and understanding quality standards.
4. Standard Operating Procedures (SOPs):
– Implement SOPs for machine setup, operation, and maintenance to standardize quality control practices.
5. Documentation and Audits:
– Keep detailed records of cutting operations, inspections, and maintenance activities.
– Conduct regular internal audits to identify and address quality issues proactively.
By combining these testing methods and quality control measures, you can ensure high-quality outputs from plasma cutter CNC systems, enhancing both product reliability and customer satisfaction.
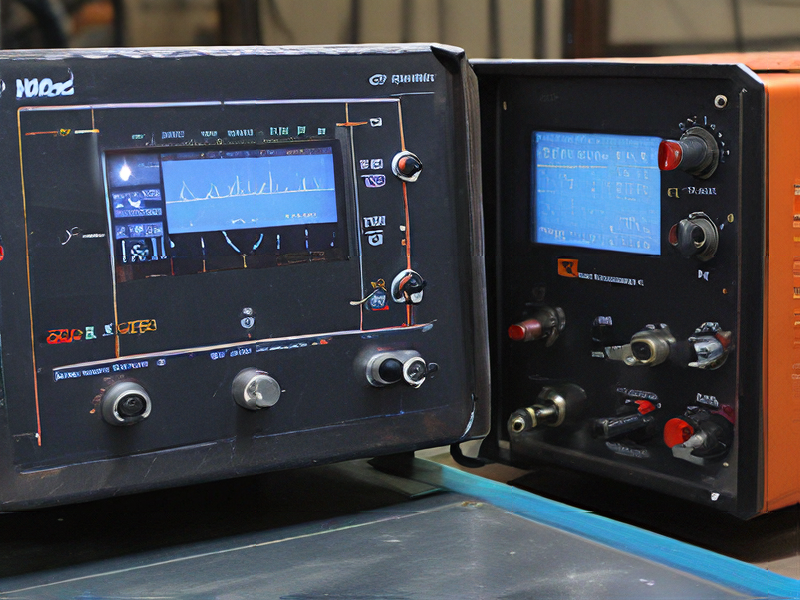
Tips for Procurement and Considerations when Purchasing from plasma cutter cnc
When procuring a plasma cutter CNC (Computer Numerical Control), consider the following tips and key considerations to ensure you select the right equipment for your needs:
1. Understand Your Needs: Determine the specific applications and materials you’ll be working with. This will influence the type and power of the plasma cutter you need.
2. Cutting Capacity: Choose a plasma cutter that can handle the thickness of the materials you typically work with. Ensure the machine has sufficient amperage to cut through your materials efficiently.
3. Table Size and Gantry Configuration: The size of the CNC table should accommodate your largest workpieces. Additionally, check the gantry configuration for stability and precision during operation.
4. Precision and Accuracy: Look for machines with high precision and repeatability. This is crucial for producing consistent, high-quality cuts.
5. Software Compatibility: Ensure the CNC machine’s software is compatible with your existing design software and easy to use. User-friendly software can save time and reduce errors.
6. Maintenance and Support: Opt for a machine from a reputable manufacturer that offers robust customer support and readily available replacement parts. Regular maintenance is essential to keep the machine running smoothly.
7. Cost of Ownership: Consider not only the initial purchase price but also the long-term costs, including consumables (like electrodes and nozzles), maintenance, and energy consumption.
8. Safety Features: Ensure the machine has adequate safety features, such as emergency stop buttons and proper ventilation systems to manage fumes and particulates.
9. Training and Documentation: Access to comprehensive training and clear documentation can enhance operator proficiency and machine longevity.
10. Warranty and Return Policy: Review the warranty terms and return policy. A good warranty can provide peace of mind and protect your investment.
By carefully considering these factors, you can select a plasma cutter CNC that meets your operational needs and delivers reliable performance.

FAQs on Sourcing and Manufacturing from plasma cutter cnc in China
FAQs on Sourcing and Manufacturing from Plasma Cutter CNC in China
1. Why source plasma cutter CNC machines from China?
China offers competitive pricing, advanced technology, and a wide range of suppliers, making it a popular choice for plasma cutter CNC machines. The manufacturing infrastructure in China supports high production volumes and customization.
2. How do I find a reliable supplier?
Use platforms like Alibaba, Global Sources, and Made-in-China. Look for suppliers with good ratings, reviews, and verified certifications. Visiting trade shows and conducting factory audits can also help ensure reliability.
3. What certifications should I look for?
Ensure the supplier has ISO 9001 for quality management and CE or UL certifications for product safety standards, especially if exporting to Europe or North America.
4. What are the typical lead times?
Lead times vary but generally range from 30 to 60 days, depending on customization and order size. It’s crucial to confirm lead times upfront and include them in the contract.
5. How do I ensure quality control?
Implement quality control checks throughout the manufacturing process. Hiring third-party inspection services can help verify quality before shipment. Requesting samples before placing a large order is also advisable.
6. What about payment terms?
Common payment terms include 30% deposit upfront and 70% balance before shipment. Using secure payment methods like letters of credit or trade assurance can mitigate risks.
7. What are the shipping options?
Shipping can be done via sea or air, with sea freight being more cost-effective for large orders. Ensure your supplier handles export documentation and complies with international shipping regulations.
8. How do I handle customs and import duties?
Familiarize yourself with your country’s import regulations and duties. Hiring a customs broker can simplify the process and ensure compliance.
9. Can I get after-sales support and spare parts?
Reputable suppliers typically offer after-sales support, including technical assistance and spare parts. Confirm the availability and terms of after-sales services before finalizing the purchase.
10. What should be included in the contract?
Include product specifications, quality standards, lead times, payment terms, warranty, after-sales support, and penalties for non-compliance to protect your interests.
Sourcing plasma cutter CNC machines from China can be beneficial if you carefully select a reliable supplier and ensure proper quality control and contractual agreements.
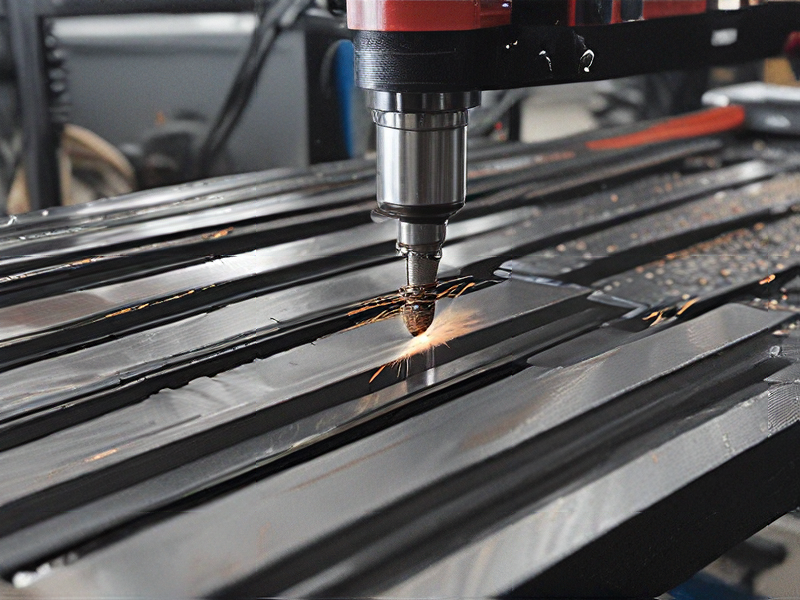