Technology and Applications of drill bit for metal
Technology and Applications of Drill Bits for Metal
Drill bits for metal are specialized cutting tools designed to create precise holes in various types of metal. The technology behind these bits focuses on durability, precision, and efficiency.
#### Technology
1. Materials:
– High-Speed Steel (HSS): Commonly used for general-purpose drilling due to its hardness and heat resistance.
– Cobalt Steel Alloys: Enhanced HSS with cobalt, offering greater heat resistance and durability, suitable for harder metals.
– Carbide: Extremely hard and wear-resistant, ideal for high-speed applications and drilling very hard metals.
2. Coatings:
– Titanium Nitride (TiN): Increases hardness and reduces friction.
– Black Oxide: Provides corrosion resistance and reduces friction.
– Diamond and Carbon Coatings: Enhance cutting efficiency and tool life.
3. Design:
– Twist Drill Bits: The most common type, featuring helical flutes to remove chips efficiently.
– Step Drill Bits: Conical shape for drilling holes of various diameters.
– Center Drill Bits: Used for creating a starting point to prevent drill wandering.
– Reduced Shank Bits: Allows larger diameter bits to fit into standard-sized chucks.
#### Applications
1. Manufacturing:
– Used in CNC machines for producing components with high precision.
– Essential in automotive, aerospace, and heavy machinery industries for fabricating parts.
2. Construction:
– Vital for installing metal frameworks, beams, and structural components.
– Used in drilling pilot holes for screws and bolts in metal fabrication.
3. Maintenance and Repair:
– Employed in workshops and repair facilities for refurbishing equipment.
– Utilized in on-site repairs for drilling out damaged bolts or creating new holes for repairs.
4. Hobby and DIY Projects:
– Popular among hobbyists for crafting metalwork projects.
– Used in home improvement tasks that involve metal fittings and installations.
The continuous advancement in drill bit technology ensures greater efficiency, precision, and versatility, catering to the diverse needs of industries and individual users.
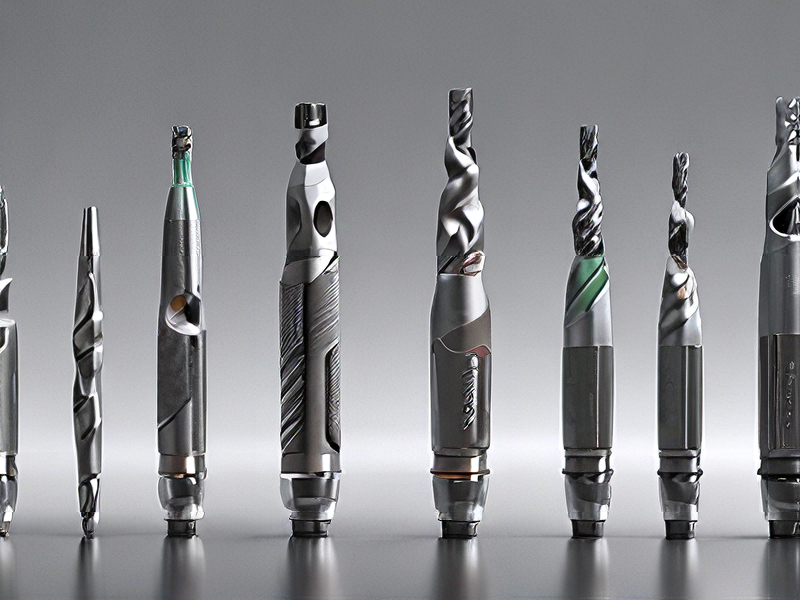
Quality Testing Methods for drill bit for metal and how to control quality
Quality Testing Methods for Metal Drill Bits
1. Material Composition Analysis: Ensure the drill bit is made from the correct alloy (e.g., high-speed steel, cobalt steel, carbide). Use spectrometry or X-ray fluorescence (XRF) for accurate composition analysis.
2. Hardness Testing: Check the drill bit’s hardness using Rockwell or Vickers hardness tests. This ensures the bit can withstand high temperatures and maintain sharpness.
3. Dimensional Accuracy: Use micrometers, calipers, and optical comparators to measure the drill bit’s dimensions, including diameter, length, and helix angle, ensuring they meet specified tolerances.
4. Coating Thickness and Adherence: For coated drill bits, use methods like X-ray fluorescence (XRF) to measure coating thickness. Adhesion tests (scratch test) ensure the coating will not peel off during use.
5. Torsional Strength Test: This test assesses the drill bit’s resistance to twisting forces, ensuring it won’t break under load.
6. Cutting Performance Test: Conduct practical drilling tests on standardized metal pieces to evaluate cutting efficiency, heat resistance, and wear.
7. Flaw Detection: Use non-destructive testing methods such as ultrasonic testing or magnetic particle inspection to detect internal flaws or cracks.
Quality Control Measures
1. Incoming Material Inspection: Verify raw materials before production using composition analysis and hardness tests.
2. Process Control: Implement Statistical Process Control (SPC) during manufacturing to monitor and control critical dimensions and properties.
3. Regular Calibration: Ensure measuring and testing equipment are regularly calibrated to maintain accuracy.
4. In-process Inspection: Conduct inspections at various stages of production to identify defects early.
5. Final Inspection: Perform a comprehensive inspection of the finished drill bits to ensure they meet all specifications.
6. Batch Testing: Test samples from each production batch to ensure consistent quality.
7. Documentation and Traceability: Maintain detailed records of materials, processes, and inspections to trace any issues back to their source.
These methods and controls ensure drill bits meet the required quality standards, providing reliable performance in metal drilling applications.
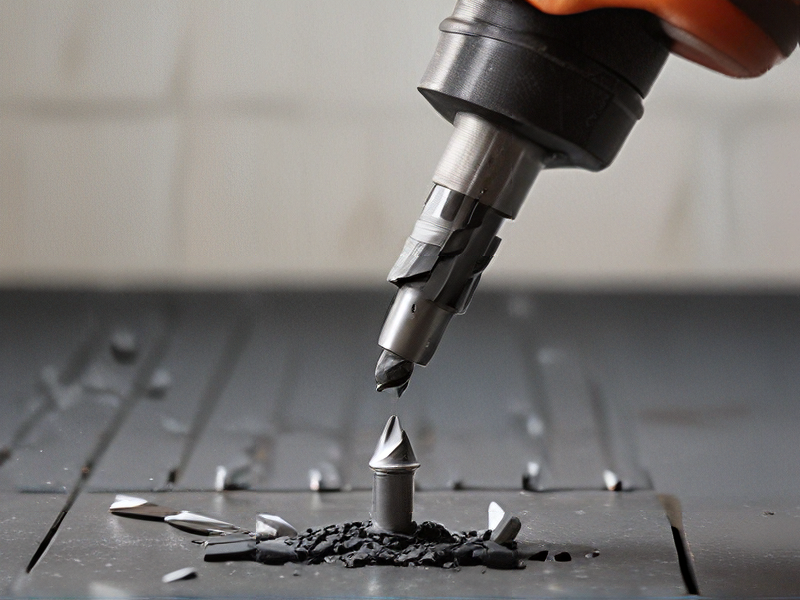
Tips for Procurement and Considerations when Purchasing from drill bit for metal
When procuring drill bits for metal, consider the following tips and factors:
1. Material Compatibility:
– Ensure the drill bit material is suitable for the type of metal you will be drilling. High-speed steel (HSS) is common for general purposes, while cobalt or carbide bits are ideal for harder metals.
2. Bit Type:
– Choose the right bit type for your application. Twist bits are versatile, step bits are excellent for enlarging holes, and unibit or step drill bits are perfect for thin metals.
3. Coating:
– Look for coated drill bits. Titanium-coated bits reduce friction and extend lifespan, while black oxide offers corrosion resistance and durability.
4. Size and Precision:
– Verify the size range available and the precision required. Ensure the bits can create holes of the exact diameter needed for your projects.
5. Durability and Quality:
– Invest in high-quality, durable drill bits from reputable manufacturers to avoid frequent replacements and ensure efficient performance.
6. Shank Type:
– Consider the shank type that matches your drill. Common types include round, hex, and reduced shank, each offering different levels of grip and compatibility.
7. Usage Frequency:
– Determine the frequency of use. For heavy-duty, regular usage, opting for premium, industrial-grade bits will be more cost-effective in the long run.
8. Price and Budget:
– Balance cost with quality. Cheaper bits may save money upfront but often wear out faster, leading to higher long-term costs.
9. Vendor Reliability:
– Purchase from reliable vendors with good after-sales support. Ensure they offer warranties or guarantees for their products.
10. Customer Reviews:
– Check customer reviews and ratings to gauge performance and reliability. Reviews can provide insights into real-world use cases and potential issues.
By considering these factors, you can select the most appropriate and cost-effective drill bits for your metalworking needs.
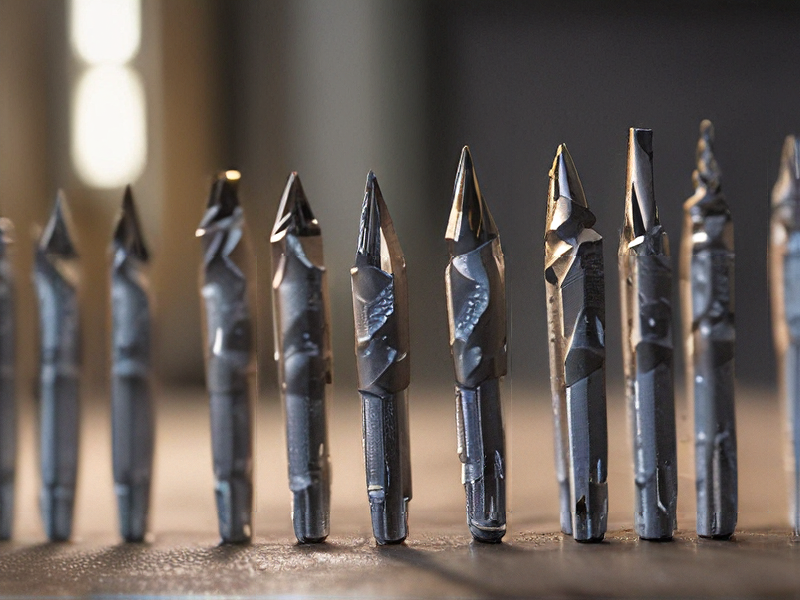
FAQs on Sourcing and Manufacturing from drill bit for metal in China
FAQs on Sourcing and Manufacturing Drill Bits for Metal in China
1. Why source drill bits for metal from China?
China offers a vast manufacturing base with competitive pricing, advanced technology, and a wide range of suppliers. This can lead to cost savings and access to high-quality products.
2. How to find reliable suppliers?
Use platforms like Alibaba, Made-in-China, and Global Sources. Verify suppliers’ credentials, request samples, and check for certifications like ISO and CE.
3. What are the key considerations when selecting a supplier?
Look for experience in producing drill bits, quality control processes, production capacity, and customer feedback. Ensure they have the necessary certifications and can meet your specifications.
4. How to ensure product quality?
Conduct factory audits, request samples for testing, and use third-party inspection services to verify quality before shipment. Regularly monitor production and maintain open communication with suppliers.
5. What are the common types of drill bits for metal available?
Twist drill bits, cobalt drill bits, carbide drill bits, and titanium-coated drill bits are commonly manufactured in China. Each type has specific applications based on the metal being drilled.
6. What is the typical lead time for manufacturing?
Lead times vary based on order size and complexity, ranging from 30 to 60 days. Confirm lead times with your supplier during the negotiation phase.
7. How to manage logistics and shipping?
Work with experienced freight forwarders and understand Incoterms. Choose between air, sea, or rail based on cost and urgency. Ensure proper documentation and customs clearance processes are followed.
8. Are there risks involved?
Risks include quality inconsistencies, communication barriers, and intellectual property concerns. Mitigate these by thorough vetting, clear contracts, and regular monitoring.
9. How to handle intellectual property (IP) protection?
Sign Non-Disclosure Agreements (NDAs) and ensure contracts include IP protection clauses. Register patents and trademarks in China to safeguard your designs.
10. What payment terms are commonly used?
Common terms include T/T (telegraphic transfer), L/C (letter of credit), and D/P (documents against payment). Negotiate terms that balance risk and cash flow.
By addressing these FAQs, you can effectively navigate the sourcing and manufacturing process for drill bits for metal in China.
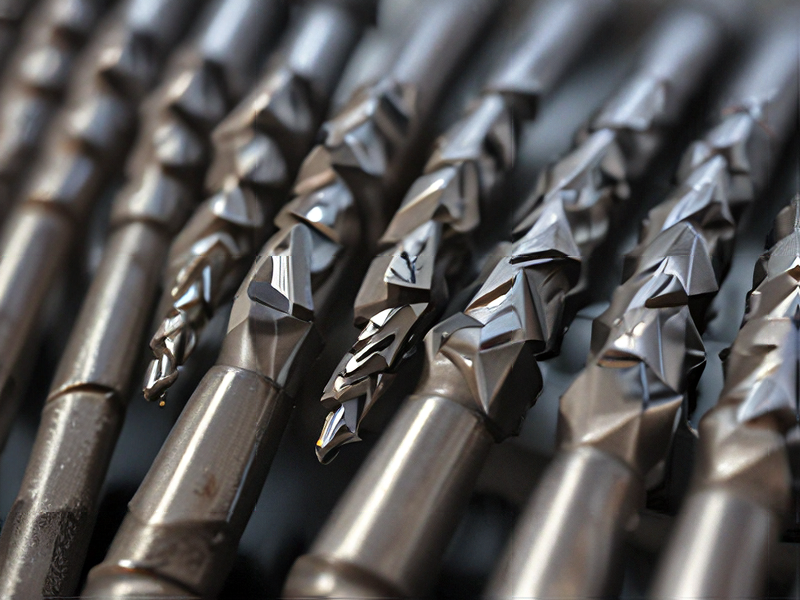