Technology and Applications of labelling machinery
Technology and Applications of Labelling Machinery
Labelling machinery employs advanced technology to automate the process of attaching labels to products, containers, and packages. These machines are crucial in various industries, including food and beverage, pharmaceuticals, cosmetics, and logistics, ensuring efficiency, accuracy, and consistency in product labeling.
Technologies Used in Labelling Machinery:
1. Automated Systems: These systems use sensors, robotics, and computer controls to precisely place labels on products. They offer high-speed operations and minimize human error.
2. Print and Apply: This technology combines printing and labeling in a single machine. It prints labels on demand and applies them directly to products, suitable for dynamic and variable data labeling.
3. RFID and Barcode Integration: Modern labelling machines incorporate RFID and barcode technologies for track-and-trace capabilities, enhancing supply chain visibility and inventory management.
4. Vision Systems: Integrated cameras and vision systems ensure proper label placement and quality by detecting defects or misalignments.
5. Pressure-Sensitive Labeling: This method uses pressure to apply labels, suitable for various surfaces, including bottles, jars, and cartons.
Applications of Labelling Machinery:
1. Food and Beverage Industry: Labels provide nutritional information, ingredients, barcodes, and branding. Labelling machines handle various packaging types, ensuring compliance with regulations.
2. Pharmaceuticals: Precision is critical for safety and compliance. Labelling machinery ensures accurate placement of labels with dosage information, batch numbers, and expiration dates.
3. Cosmetics: Machines handle different container shapes and sizes, applying labels that convey brand identity and product information.
4. Logistics and Warehousing: Labelling machines are used for shipping labels, barcodes, and RFID tags, facilitating efficient tracking and management of inventory.
In summary, labelling machinery integrates advanced technologies to automate the labeling process across multiple industries, enhancing efficiency, accuracy, and regulatory compliance.
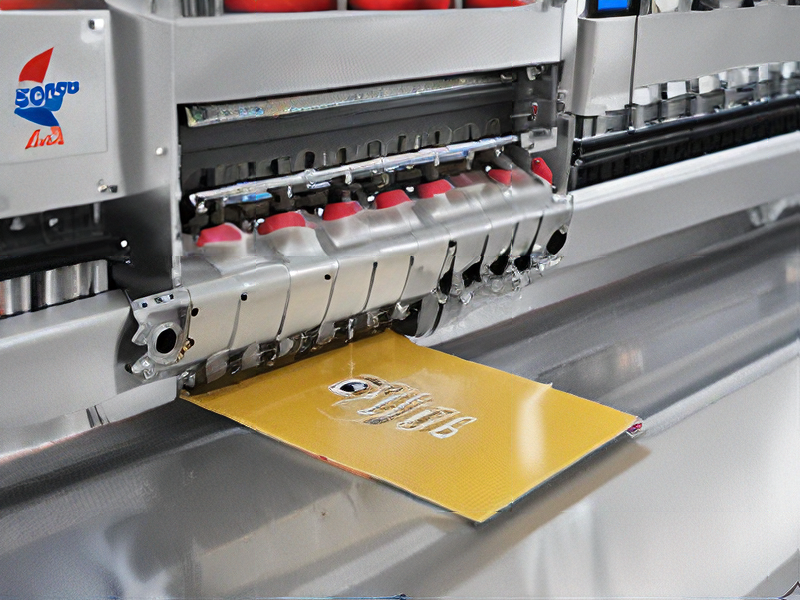
Quality Testing Methods for labelling machinery and how to control quality
Quality testing methods for labeling machinery ensure that labels are correctly applied, durable, and compliant with standards. Here are the primary methods and controls:
1. Visual Inspection: Regularly check for alignment, placement, and legibility of labels. Inspect for defects such as smudging, tearing, or misprints.
2. Adhesion Testing: Assess the adhesive quality by applying and removing the label from various surfaces. Peel tests can quantify the force required to remove the label, ensuring consistent adhesion.
3. Durability Testing: Expose labels to environmental conditions (humidity, temperature, abrasion) to simulate real-world usage. Evaluate any changes in color, readability, or adhesion.
4. Barcode Verification: Use barcode scanners to ensure barcodes are readable and correctly formatted. Verification systems can measure barcode quality against standards like ANSI or ISO.
5. Print Quality Assessment: Analyze print clarity, contrast, and color accuracy using digital imaging systems. Ensure text and graphics meet specified resolutions.
6. Label Placement Accuracy: Use automated vision systems to measure the exact position of labels. These systems detect misalignments and trigger alerts for corrective action.
7. Material Compatibility Testing: Ensure label materials are compatible with the surfaces they are applied to, preventing issues like bubbling or peeling.
Controlling Quality:
– Standard Operating Procedures (SOPs): Establish clear guidelines for labeling processes, including machine setup, maintenance, and inspection routines.
– Regular Calibration: Periodically calibrate machinery to maintain accuracy and consistency in label application.
– Training: Train operators on proper machine use, troubleshooting, and quality inspection techniques.
– Statistical Process Control (SPC): Use SPC to monitor labeling process performance. Analyze data trends to detect and correct deviations promptly.
– Audit and Feedback Loops: Conduct regular audits and use feedback from inspections to improve processes. Implement corrective actions for identified issues.
By employing these methods and controls, companies can maintain high-quality labeling standards, ensuring product integrity and customer satisfaction.
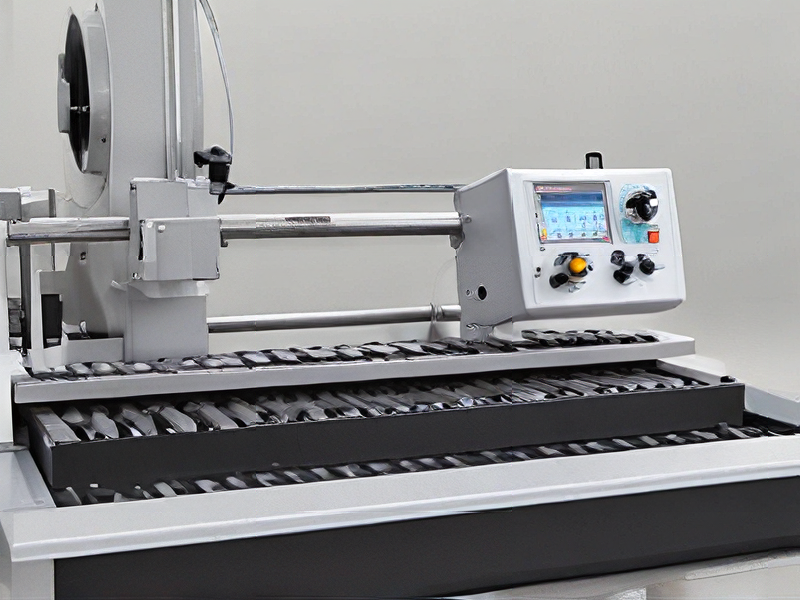
Tips for Procurement and Considerations when Purchasing from labelling machinery
When procuring labeling machinery, careful consideration and strategic planning are essential to ensure you get the best equipment suited to your needs. Here are some key tips and considerations:
1. Define Requirements: Identify the specific needs of your operation. Consider the types of products you’ll label, the production volume, and the labeling speed required. Determine whether you need automatic, semi-automatic, or manual machinery.
2. Quality and Reliability: Invest in high-quality, durable machinery from reputable manufacturers. Check reviews and ask for references to ensure reliability and longevity, minimizing downtime and maintenance costs.
3. Flexibility and Scalability: Choose machines that can handle different label sizes and types. Equipment that can be easily upgraded or modified will accommodate future growth and changes in product lines.
4. Compliance and Standards: Ensure the machinery complies with industry standards and regulations, particularly if you operate in sectors with stringent labeling requirements like food, pharmaceuticals, or chemicals.
5. Total Cost of Ownership: Look beyond the initial purchase price. Consider the total cost of ownership, including maintenance, spare parts, energy consumption, and potential downtime. Opt for machines with a good balance of upfront cost and long-term operational efficiency.
6. Supplier Support and Training: Select a supplier that offers comprehensive support and training. Proper training for your staff will maximize the machine’s efficiency and lifespan. Good customer service can assist with troubleshooting and maintenance.
7. Integration with Existing Systems: Ensure the new machinery can integrate seamlessly with your current production line and software systems. Compatibility with your existing infrastructure will reduce implementation time and costs.
8. Test Before Purchase: If possible, arrange for a trial or demonstration to see the machinery in action. This helps verify performance and suitability for your specific requirements.
9. Warranty and After-Sales Service: Check the warranty terms and ensure robust after-sales service. A good warranty and reliable service will protect your investment and ensure continuous operation.
By considering these factors, you can make an informed decision and select labeling machinery that will enhance your production efficiency and meet your long-term needs.

FAQs on Sourcing and Manufacturing from labelling machinery in China
FAQs on Sourcing and Manufacturing Labelling Machinery in China
1. Why source labelling machinery from China?
China offers competitive pricing, a wide range of options, advanced technology, and established manufacturing expertise. These factors make it a cost-effective choice without compromising on quality.
2. How do I find reliable manufacturers?
Use platforms like Alibaba, Global Sources, and Made-in-China. Attend trade shows like the Canton Fair. Verify manufacturers through third-party inspection companies and request references.
3. What certifications should I look for?
Ensure the manufacturer complies with international standards such as ISO 9001 for quality management, CE marking for safety compliance in Europe, and other specific certifications relevant to your industry.
4. How can I ensure the quality of machinery?
Conduct factory audits, request samples, and use third-party inspection services. Clearly define your quality requirements and include them in the purchase contract.
5. What are the payment terms?
Common terms include a 30% deposit before production and 70% balance before shipment. Use secure payment methods like letters of credit or escrow services to mitigate risk.
6. What about lead times?
Lead times vary depending on the complexity of the machinery and order size but generally range from 30 to 60 days. Confirm this with your supplier and include it in your contract.
7. How is shipping handled?
Manufacturers typically handle shipping arrangements. Choose between FOB (Free on Board) or CIF (Cost, Insurance, and Freight) terms. Consider using a freight forwarder for logistics management.
8. Are after-sales services available?
Reputable manufacturers offer after-sales services, including installation, training, and maintenance support. Verify the availability and terms of these services before finalizing your purchase.
9. What are the common challenges?
Common challenges include communication barriers, quality control issues, and intellectual property concerns. Mitigate these by maintaining clear communication, using contracts, and protecting your IP rights.
10. How do I handle potential disputes?
Clearly outline dispute resolution mechanisms in your contract. This might include arbitration in a neutral location or litigation in a mutually agreed-upon jurisdiction.
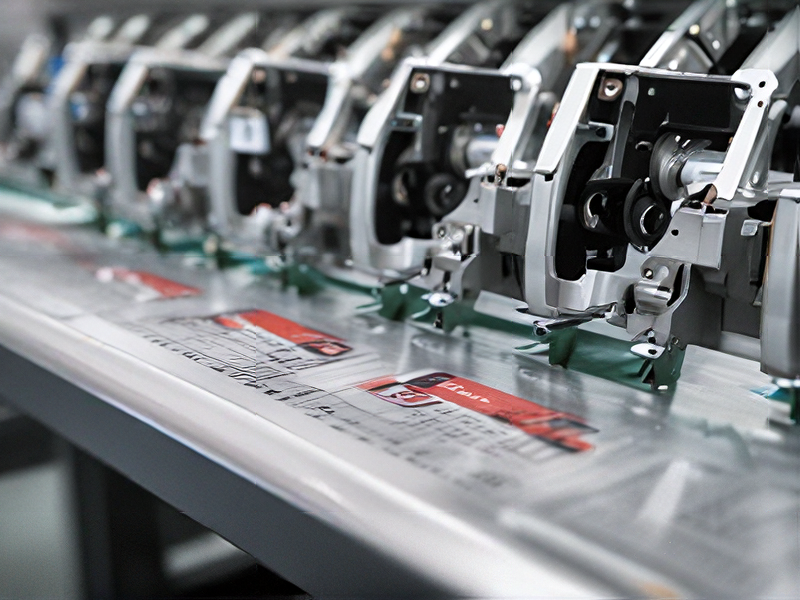