Technology and Applications of bore machining
Bore machining is a critical process in manufacturing, used to enlarge or finish the diameter of pre-drilled holes with high precision. This process is essential in industries such as automotive, aerospace, and heavy machinery, where precise hole dimensions are crucial for part functionality and assembly.
Technology
1. Boring Machines: Boring machines, such as horizontal and vertical boring mills, are used to perform this process. These machines are capable of handling large and heavy workpieces, offering high precision and stability.
2. Cutting Tools: Boring bars, equipped with single-point cutting tools or multiple cutting edges, are commonly used. Advanced tools include carbide or diamond tips for increased durability and precision.
3. CNC Technology: Computer Numerical Control (CNC) boring machines offer enhanced precision, repeatability, and efficiency. They allow for complex operations, such as contouring and multiple-hole boring, through automated control.
4. Measurement and Control: Advanced measurement systems, such as laser and optical sensors, are integrated into boring machines to ensure real-time monitoring and control of the machining process, reducing errors and improving quality.
Applications
1. Engine Components: Bore machining is crucial in producing engine blocks, cylinder heads, and other automotive components that require precise internal diameters for optimal performance and efficiency.
2. Aerospace Parts: Aerospace components, like turbine casings and landing gear parts, often require precision boring to meet strict safety and performance standards.
3. Heavy Machinery: Boring is used in manufacturing parts for construction equipment, mining machinery, and other heavy-duty applications where robust and precise components are necessary.
4. Hydraulic and Pneumatic Cylinders: These cylinders demand high precision to ensure proper sealing and functionality, making boring a vital process in their production.
Bore machining technologies continue to evolve, incorporating advancements in materials, automation, and measurement techniques, enhancing the precision, efficiency, and application scope of this essential manufacturing process.
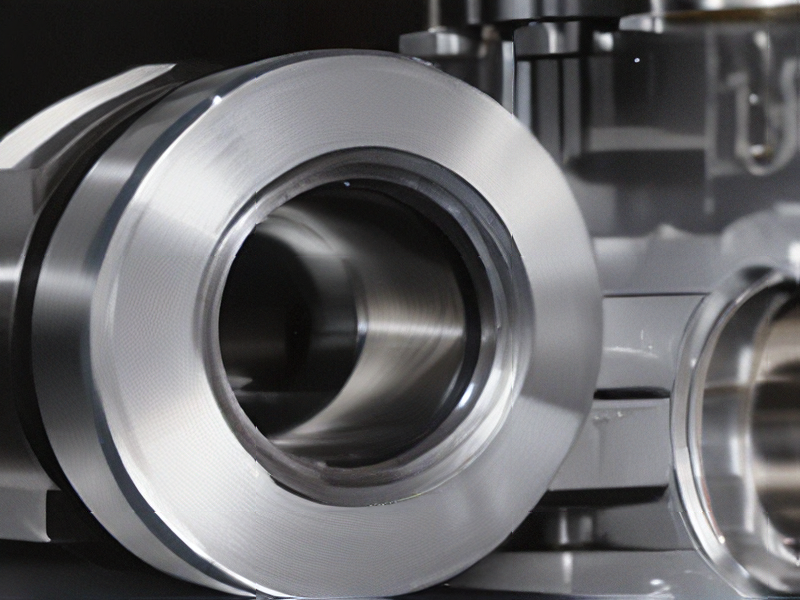
Quality Testing Methods for bore machining and how to control quality
Quality testing for bore machining involves several methods to ensure precision and reliability. Key techniques include:
1. Dimensional Inspection:
– Calipers and Micrometers: For measuring bore diameter.
– Bore Gauges: For checking internal dimensions with high accuracy.
– Coordinate Measuring Machines (CMMs): For 3D measurements and precise analysis.
2. Surface Finish Inspection:
– Profilometers: To measure surface roughness.
– Visual and Tactile Inspection: Using comparison with standard surface finish samples.
3. Roundness and Cylindricity Testing:
– Roundness Testers: To assess deviations in circularity.
– CMMs: Also used for checking cylindricity by comparing multiple cross-sections.
4. Non-Destructive Testing (NDT):
– Ultrasonic Testing: For detecting internal defects.
– Eddy Current Testing: For surface and sub-surface flaw detection.
5. Tolerances and Fit Checks:
– Go/No-Go Gauges: Simple yet effective tools to ensure the bore falls within specified limits.
To control quality, follow these steps:
1. Pre-Production Planning:
– Tool Selection: Choose appropriate tools and machines.
– Process Planning: Define machining parameters and sequences.
2. In-Process Monitoring:
– Statistical Process Control (SPC): Utilize control charts to monitor machining processes.
– Tool Condition Monitoring: Regularly check tool wear and replace when necessary.
3. Post-Production Inspection:
– Regular Quality Audits: Conduct systematic checks on finished products.
– Calibration of Instruments: Ensure measuring instruments are regularly calibrated.
4. Documentation and Feedback:
– Record Keeping: Maintain detailed records of inspections and deviations.
– Continuous Improvement: Use feedback to refine processes and tools.
By integrating these methods and controls, bore machining can achieve high precision and consistency, meeting the required quality standards.
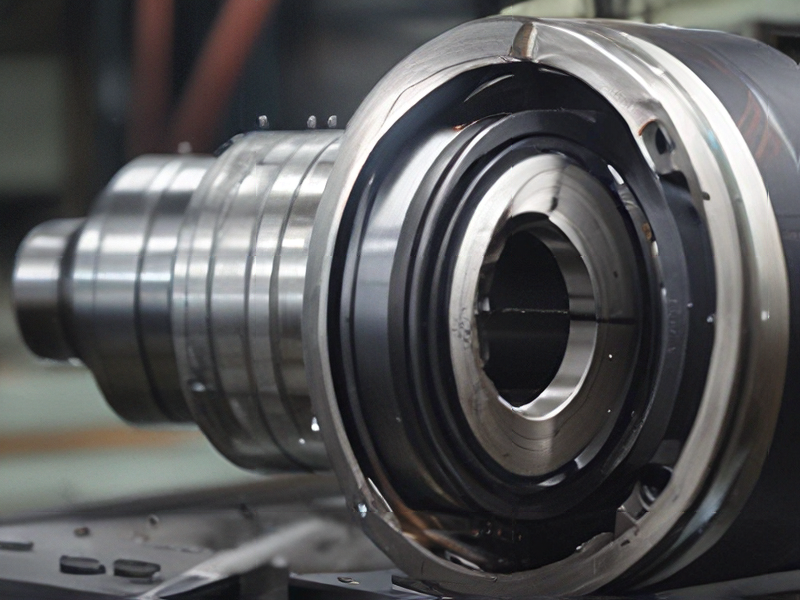
Tips for Procurement and Considerations when Purchasing from bore machining
When procuring bore machining services, several key tips and considerations can help ensure successful outcomes:
1. Define Requirements Clearly:
– Specify the material type, dimensions, tolerances, and surface finish required.
– Include any special requirements, such as heat treatment or coating.
2. Supplier Evaluation:
– Assess the supplier’s technical capabilities and machinery to ensure they can meet your specifications.
– Check the supplier’s experience in bore machining, especially with similar projects.
3. Quality Assurance:
– Ensure the supplier has a robust quality management system in place, preferably certified by ISO standards.
– Request inspection reports and quality certificates for the materials and finished parts.
4. Lead Time and Capacity:
– Confirm the supplier’s production capacity to handle your order volume within the required timeframe.
– Consider potential delays and their impact on your project timeline.
5. Cost Considerations:
– Obtain detailed quotes, including setup costs, unit prices, and any additional charges.
– Compare costs from multiple suppliers to get a competitive rate without compromising on quality.
6. Sample Testing:
– Request sample parts before committing to full production to verify quality and adherence to specifications.
– Use samples to test fit, function, and finish.
7. Communication and Support:
– Establish clear lines of communication with the supplier for project updates and issue resolution.
– Ensure the supplier provides technical support and after-sales service.
8. Logistics and Shipping:
– Discuss packaging requirements to protect parts during transit.
– Consider shipping times and costs, especially if the supplier is overseas.
9. Sustainability and Compliance:
– Verify that the supplier complies with environmental and safety regulations.
– Opt for suppliers with sustainable practices to align with corporate social responsibility goals.
10. Risk Management:
– Assess potential risks, such as supply chain disruptions, and have contingency plans in place.
– Consider supplier location and political or economic stability in that region.
By carefully considering these factors, you can optimize procurement from bore machining services, ensuring high-quality parts delivered on time and within budget.
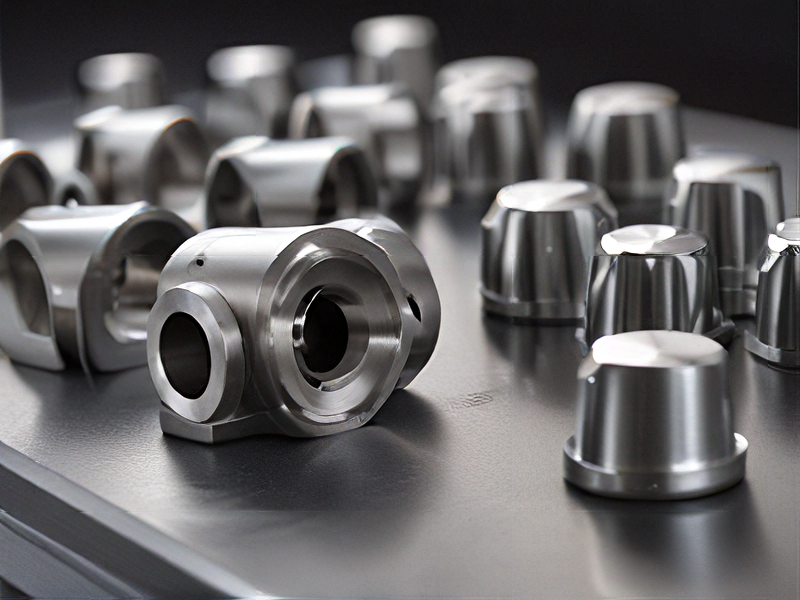
FAQs on Sourcing and Manufacturing from bore machining in China
FAQs on Sourcing and Manufacturing Bore Machining in China
1. Why source bore machining from China?
China offers cost-effective manufacturing with advanced technological capabilities and a large, skilled workforce. Chinese manufacturers can provide competitive pricing without compromising quality.
2. What should I look for in a Chinese bore machining supplier?
Key factors include:
– Experience and expertise: Choose suppliers with a proven track record in bore machining.
– Certifications: Ensure they have ISO 9001 or other relevant quality certifications.
– Capacity and technology: Verify they have the necessary equipment and capacity to meet your needs.
– Communication: Strong English skills and responsive communication are essential.
3. How can I verify the quality of a Chinese supplier?
– Factory visits: Conduct on-site inspections.
– Third-party audits: Hire independent auditors to assess their facilities and processes.
– Samples and prototypes: Request samples to evaluate quality before large-scale production.
4. What are the common challenges when sourcing from China?
– Quality control: Ensuring consistent product quality can be challenging.
– Communication barriers: Language differences may lead to misunderstandings.
– Intellectual property protection: Safeguarding your designs and technologies requires diligence.
5. How can I mitigate risks in bore machining projects?
– Clear contracts: Define specifications, timelines, and quality standards in contracts.
– Regular monitoring: Maintain frequent communication and conduct regular quality checks.
– Diversification: Avoid relying on a single supplier to reduce risk.
6. What are the lead times for bore machining in China?
Lead times vary based on order size, complexity, and supplier capabilities, typically ranging from a few weeks to several months.
7. How do I handle logistics and shipping?
– Freight forwarders: Use experienced freight forwarders to manage shipping.
– Incoterms: Understand Incoterms (e.g., FOB, CIF) to clarify responsibilities.
– Customs clearance: Ensure proper documentation to facilitate smooth customs processing.
8. What are the cost considerations?
– Production costs: Include material, labor, and overhead.
– Shipping and tariffs: Account for international shipping fees and potential tariffs.
By addressing these FAQs, you can effectively source and manage bore machining projects in China, ensuring quality and cost-efficiency.
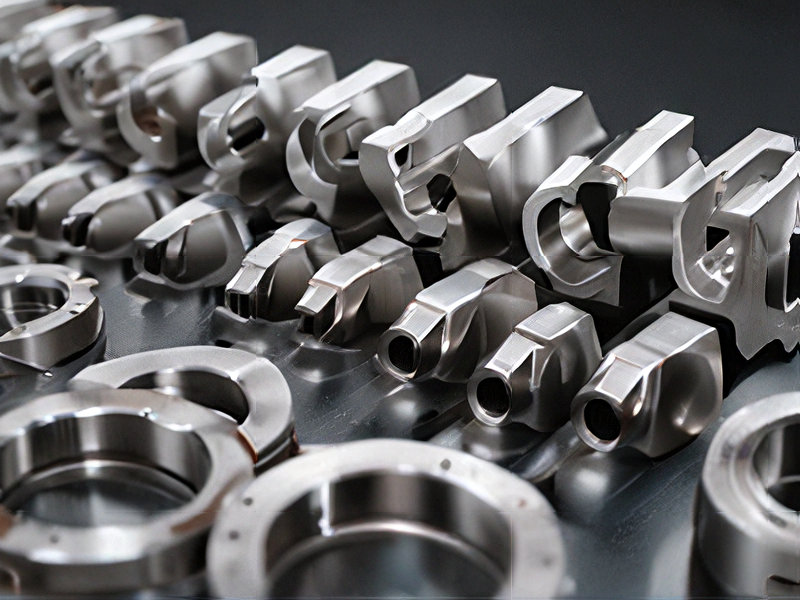