Technology and Applications of machining boring
Technology and Applications of Machining Boring
Machining Boring:
Machining boring is a precision technique used to enlarge and finish the inside diameter of a pre-existing hole. This process enhances the dimensional accuracy and surface finish of cylindrical parts, making it essential in manufacturing industries requiring high precision.
Technology:
1. Boring Machines: There are different types of boring machines, including horizontal boring machines, vertical boring machines, and jig borers. Each type is suited to specific applications and materials.
2. Tooling: Boring bars, with adjustable cutting heads and insert holders, are the primary tools used. They ensure precision and flexibility in achieving the desired hole dimensions.
3. Computer Numerical Control (CNC): Modern boring operations often use CNC machines, allowing for automated, highly accurate, and repeatable processes. CNC technology integrates CAD/CAM software for designing and programming boring operations.
4. Boring Heads: These can be adjusted to achieve specific diameters and surface finishes. Advanced heads use digital readouts and control systems to maintain precision.
5. Coolants and Lubricants: Proper coolant application is critical to remove heat, prolong tool life, and ensure a smooth finish.
Applications:
1. Automotive Industry: Boring is used in manufacturing engine cylinders, gearbox housings, and other components requiring precise internal dimensions.
2. Aerospace Industry: Aircraft components, such as landing gear and engine parts, often require boring to ensure exact tolerances and structural integrity.
3. Heavy Machinery: Boring is essential in producing parts for construction and mining equipment, where durability and precision are paramount.
4. Medical Devices: Precision boring is used in creating surgical instruments and implants that require high accuracy and smooth finishes.
5. Energy Sector: Boring is applied in manufacturing components for power generation, including turbines and nuclear reactors, where precision is critical.
Machining boring is a vital process across various industries, enabling the production of high-precision components essential for modern technology and engineering applications.
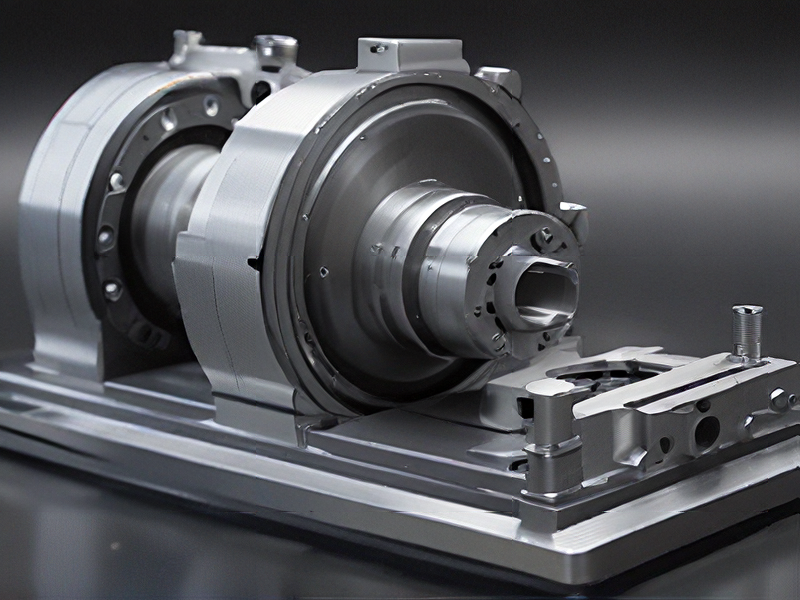
Quality Testing Methods for machining boring and how to control quality
Quality Testing Methods for Machining Boring
1. Dimensional Inspection:
– Micrometers and Calipers: Used to measure the diameter and depth of the bore with high precision.
– Bore Gauges: Specifically designed for internal diameter measurements.
– Coordinate Measuring Machines (CMM): Provide highly accurate 3D measurements.
2. Surface Finish Inspection:
– Surface Roughness Testers: Measure the surface texture and ensure it meets the specified Ra value.
– Visual Inspection: Detects obvious surface defects like scratches or tool marks.
3. Roundness and Cylindricity:
– Roundness Testers: Evaluate the roundness of the bore.
– Form Testers: Assess the cylindricity to ensure the bore is consistent throughout its length.
4. Concentricity and Alignment:
– Dial Indicators: Check the concentricity of the bore relative to other features.
– Laser Alignment Tools: Ensure the bore is aligned correctly within the assembly.
5. Material Integrity:
– Ultrasonic Testing: Detects internal defects and inconsistencies within the material.
– Hardness Testing: Verifies the material hardness to ensure it meets specifications.
Quality Control Methods
1. Statistical Process Control (SPC):
– Control Charts: Monitor process stability and variation.
– Capability Analysis: Assess the process capability (Cp and Cpk) to ensure consistent quality.
2. Standard Operating Procedures (SOPs):
– Define detailed machining processes and inspection routines to maintain consistency.
3. In-process Inspection:
– Tool Wear Monitoring: Regularly check and replace worn-out tools to maintain precision.
– On-machine Probing: Automated probing systems for real-time measurement and adjustments.
4. Calibration and Maintenance:
– Regular calibration of measuring instruments and maintenance of machines to ensure accuracy.
5. Employee Training:
– Continuous training programs for operators on quality standards and inspection techniques.
By integrating these methods, machining boring processes can achieve high precision and maintain consistent quality.
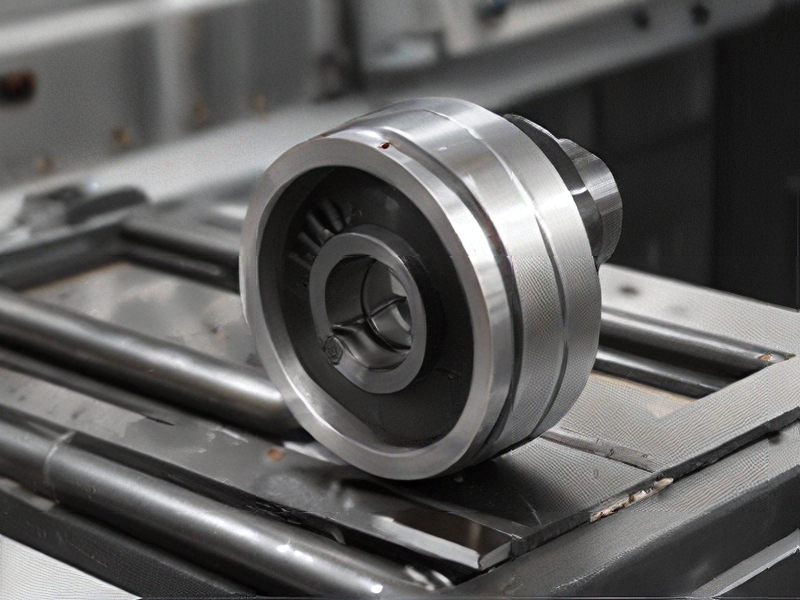
Tips for Procurement and Considerations when Purchasing from machining boring
When procuring machining and boring services, there are several key considerations to ensure quality, efficiency, and cost-effectiveness:
1. Vendor Evaluation:
– Experience and Expertise: Assess the vendor’s experience in machining and boring. Check their portfolio and client testimonials.
– Certifications: Ensure the vendor has necessary certifications like ISO 9001, indicating a commitment to quality management systems.
– Technology and Equipment: Verify that the vendor uses advanced, well-maintained machinery, which can impact the precision and quality of the work.
2. Quality Assurance:
– Inspection Processes: Inquire about their quality control measures, such as in-process inspections and final quality checks.
– Tolerance and Precision: Confirm that the vendor can meet your required tolerances and precision levels, which are critical in machining and boring operations.
3. Cost Considerations:
– Quotation and Pricing: Obtain detailed quotes, including any hidden costs. Compare prices but balance cost against quality and reliability.
– Value-added Services: Look for vendors offering additional services like design support, prototyping, or logistics, which can save costs and streamline processes.
4. Lead Time and Delivery:
– Turnaround Time: Check the vendor’s lead time for project completion. Ensure they can meet your deadlines without compromising quality.
– Logistics: Evaluate their delivery process and costs, ensuring timely and secure transportation of your components.
5. Material and Specifications:
– Material Expertise: Ensure the vendor has experience with the materials you require. Different materials may need different machining techniques.
– Specification Compliance: Make sure they can adhere to your detailed specifications, including dimensions, finishes, and material properties.
6. Communication and Support:
– Responsiveness: Choose a vendor with good communication skills who is responsive to your queries and updates.
– Technical Support: Ensure they provide technical support during and after the machining process to address any issues that may arise.
By considering these factors, you can select a reliable machining and boring vendor that delivers high-quality products, meets deadlines, and stays within budget.
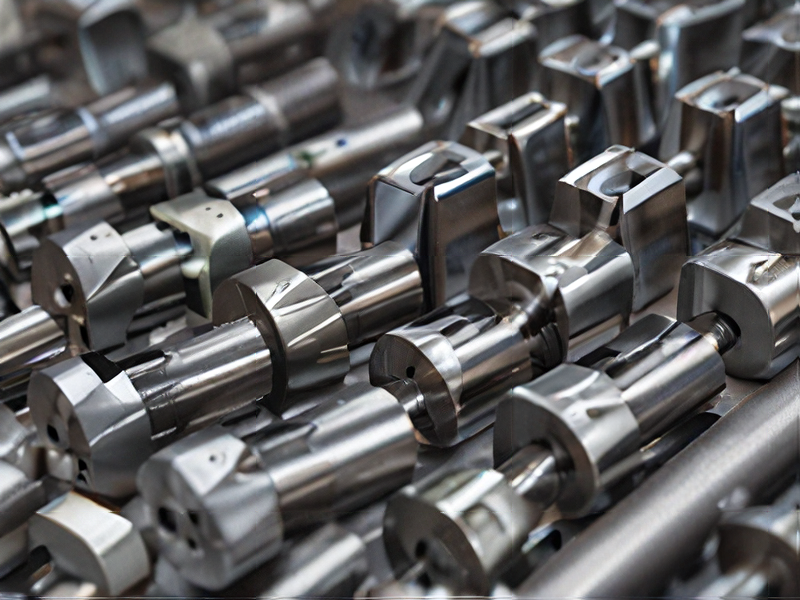
FAQs on Sourcing and Manufacturing from machining boring in China
FAQs on Sourcing and Manufacturing from Machining Boring in China
1. Why should I consider sourcing machining boring services from China?
– China offers cost-effective manufacturing solutions due to lower labor costs and economies of scale. The country also has a well-developed supply chain and advanced manufacturing technologies, ensuring high-quality production.
2. What are the main advantages of machining boring in China?
– The primary advantages include cost savings, access to advanced technology, a wide range of material options, and experienced manufacturers capable of producing complex and precise components.
3. How can I ensure the quality of machining boring services in China?
– Partner with reputable suppliers who have certifications such as ISO 9001. Conduct audits and inspections, request samples, and implement quality control measures like first article inspection (FAI) and in-process quality checks.
4. What materials are commonly used in machining boring in China?
– Common materials include various grades of steel, aluminum, brass, bronze, and other alloys. The choice of material depends on the specific requirements of the project, such as strength, weight, and corrosion resistance.
5. How do I find reliable machining boring suppliers in China?
– Utilize online platforms like Alibaba, Made-in-China, and Global Sources. Attend trade shows like the China International Machine Tool Show (CIMT). Seek recommendations from industry contacts and consider engaging sourcing agents.
6. What are the typical lead times for machining boring projects in China?
– Lead times vary based on the complexity and quantity of the order but typically range from a few weeks to several months. Clear communication and detailed specifications can help expedite the process.
7. Are there any risks involved in sourcing from China, and how can they be mitigated?
– Risks include potential quality issues, communication barriers, and intellectual property concerns. Mitigate these by performing due diligence, using contracts that protect IP, and maintaining regular communication with suppliers.
8. What are the payment terms usually offered by Chinese suppliers?
– Common payment terms include a 30% deposit upfront with the remaining 70% paid upon completion or before shipment. Letter of Credit (LC) and escrow services are also used to protect both parties.
9. How does shipping and logistics work when sourcing from China?
– Shipping options include air freight for urgent orders and sea freight for larger, less time-sensitive shipments. Work with experienced logistics providers to manage customs clearance, tariffs, and transportation.
10. Can I visit the manufacturing facilities in China?
– Yes, visiting facilities can provide valuable insights into the supplier’s capabilities and quality control processes. It is advisable to schedule visits to multiple suppliers to compare their offerings and operations.
By addressing these common questions, you can better navigate the process of sourcing and manufacturing machining boring services from China.
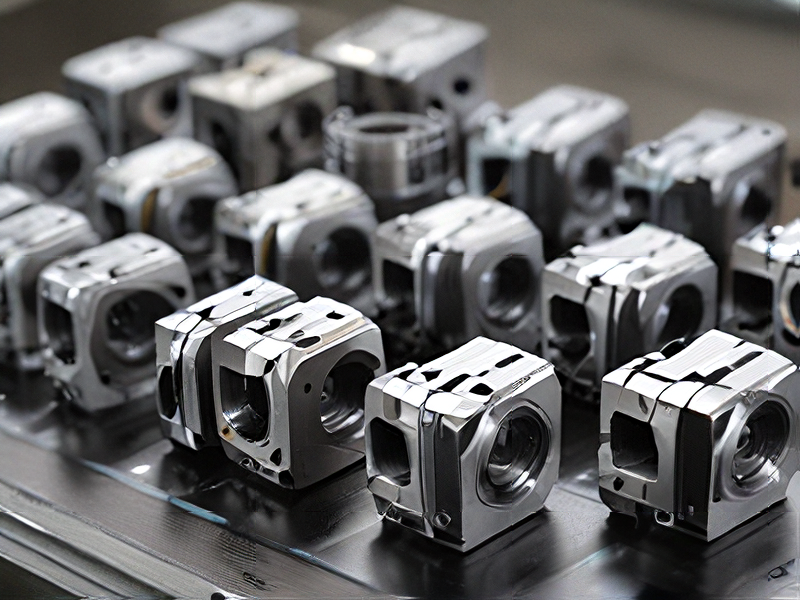