Technology and Applications of borer machine
A borer machine is a precision tool used for enlarging holes and ensuring they are perfectly round and straight. These machines are essential in industries such as automotive, aerospace, and manufacturing, where accuracy and surface finish are critical.
Technology
Borer machines use advanced technology to achieve high precision and efficiency:
1. CNC Control: Computer Numerical Control (CNC) systems allow for automated and highly accurate operations, reducing human error and improving consistency.
2. Advanced Materials: Modern borer machines are made from high-strength materials like carbide and high-speed steel, which enhance durability and cutting performance.
3. Precision Bearings and Guides: These components minimize vibration and ensure smooth operation, which is crucial for maintaining tight tolerances.
4. Coolant Systems: Integrated coolant systems help reduce heat and wear on the cutting tools, extending their life and maintaining accuracy.
5. Feedback Systems: Real-time monitoring systems provide feedback on tool wear and workpiece quality, allowing for immediate adjustments.
Applications
Borer machines have a wide range of applications:
1. Automotive Industry: Used for machining engine blocks, cylinder heads, and transmission parts, ensuring components meet exact specifications for performance and reliability.
2. Aerospace Industry: Essential for producing critical parts like turbine blades and fuselage components, where precision is vital for safety and functionality.
3. Manufacturing: Used in creating molds, dies, and other tools that require high accuracy and a fine surface finish.
4. Oil and Gas Industry: Employed in machining parts for drilling equipment and pipelines, which need to withstand high pressures and harsh environments.
5. Medical Devices: Precision boring is used in manufacturing components for medical devices and implants, where accuracy is critical for patient safety.
In summary, borer machines are a cornerstone of precision manufacturing, leveraging advanced technology to deliver high-quality results in various industries. Their ability to produce accurate and consistent holes makes them indispensable in applications requiring stringent quality standards.
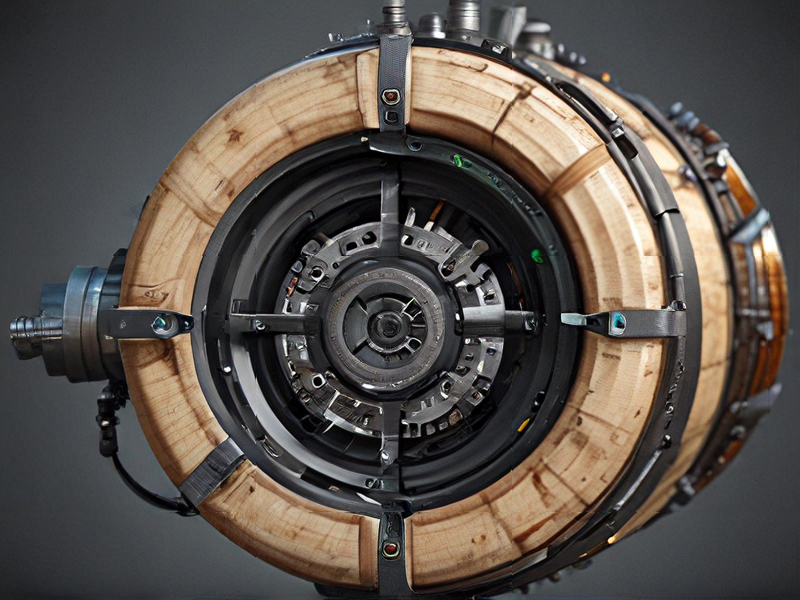
Quality Testing Methods for borer machine and how to control quality
Quality testing for borer machines involves several key methods to ensure precision, durability, and performance. These methods can be broadly categorized as follows:
1. Dimensional Inspection:
– Calipers and Micrometers: Measure the dimensions of machined parts to ensure they meet specifications.
– Coordinate Measuring Machine (CMM): Provides high-precision measurements of complex geometries.
2. Surface Finish Inspection:
– Surface Roughness Testers: Measure the texture of the machined surface to ensure it meets required smoothness.
– Visual Inspection: Identifies surface defects like scratches, burns, or tool marks.
3. Material Testing:
– Hardness Testing: Assesses the material’s resistance to deformation.
– Metallographic Analysis: Examines the material’s microstructure for any anomalies.
4. Performance Testing:
– Runout Measurement: Checks the alignment and concentricity of the spindle and tool.
– Vibration Analysis: Ensures the machine operates smoothly without excessive vibrations.
5. Non-Destructive Testing (NDT):
– Ultrasonic Testing: Detects internal defects without damaging the part.
– Magnetic Particle Testing: Identifies surface and near-surface defects in ferromagnetic materials.
Controlling Quality
1. Standard Operating Procedures (SOPs): Establish clear guidelines for machine operation and maintenance.
2. Regular Calibration: Ensure all measuring instruments and the borer machine itself are regularly calibrated to maintain accuracy.
3. Training Programs: Continuously train operators and inspectors on the latest techniques and standards.
4. Preventive Maintenance: Schedule regular maintenance to prevent unexpected breakdowns and ensure consistent performance.
5. Statistical Process Control (SPC): Use statistical methods to monitor and control the machining process, identifying any variations that could lead to defects.
6. Quality Audits: Conduct periodic audits to ensure compliance with quality standards and identify areas for improvement.
By implementing these testing methods and control measures, manufacturers can ensure that borer machines produce high-quality, precise, and reliable parts.
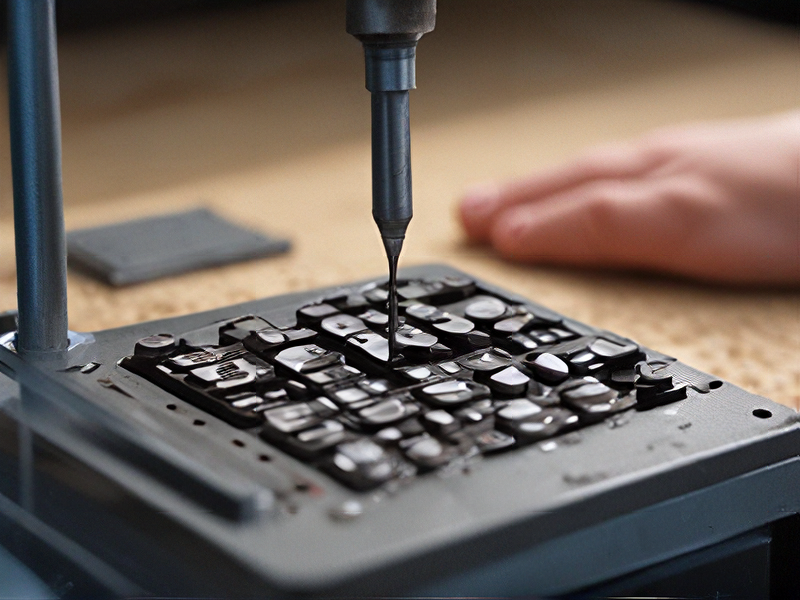
Tips for Procurement and Considerations when Purchasing from borer machine
When procuring a borer machine, consider these key tips and factors:
1. Define Requirements:
– Application Needs: Understand the specific tasks the borer machine will perform, including the materials to be drilled and required precision.
– Specifications: Determine the necessary machine specifications like drilling depth, diameter range, and spindle speed.
2. Quality and Durability:
– Build Quality: Choose a machine with a robust build to ensure longevity and reliable performance.
– Reputable Brands: Opt for machines from reputable manufacturers known for quality and after-sales support.
3. Technological Features:
– Automation and Controls: Consider machines with advanced control systems and automation features for enhanced efficiency and precision.
– Software Integration: Ensure compatibility with existing software and systems for streamlined operations.
4. Cost and Budgeting:
– Total Cost of Ownership: Factor in not just the purchase price but also maintenance, spare parts, and operational costs.
– Financing Options: Explore leasing or financing options if capital expenditure is a concern.
5. Vendor Selection:
– Reputation and Reviews: Check reviews and ask for references to gauge vendor reliability and service quality.
– After-Sales Service: Ensure the vendor provides robust after-sales support, including training, maintenance, and quick response to issues.
6. Compliance and Safety:
– Regulatory Standards: Ensure the machine meets all relevant safety and regulatory standards.
– Safety Features: Look for machines with built-in safety features to protect operators and enhance workplace safety.
7. Training and Support:
– Operator Training: Ensure comprehensive training programs are available for operators to maximize the machine’s capabilities.
– Technical Support: Confirm the availability of technical support for troubleshooting and maintenance.
8. Trial and Demonstration:
– Machine Demonstration: Whenever possible, arrange for a demonstration to see the machine in action and evaluate its performance.
By carefully considering these factors, you can ensure a successful procurement process and optimal long-term use of your borer machine.
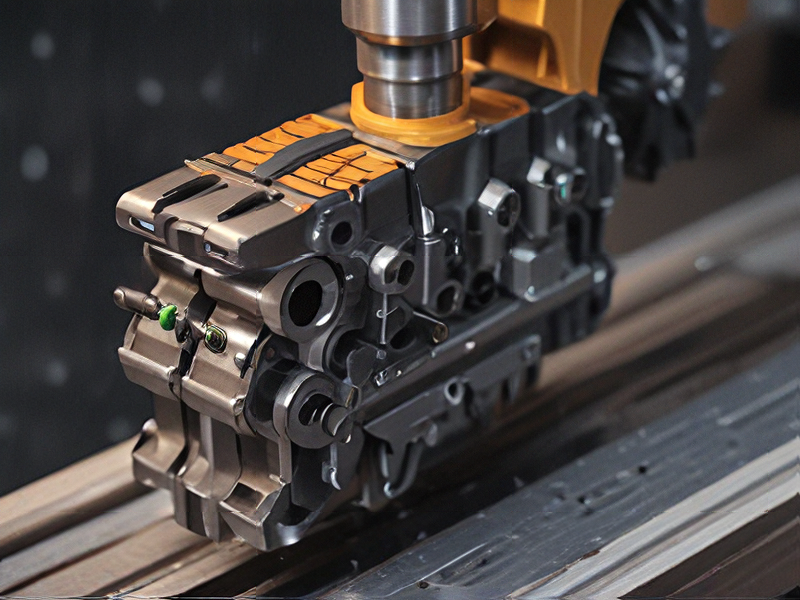
FAQs on Sourcing and Manufacturing from borer machine in China
FAQs on Sourcing and Manufacturing Borer Machines in China
#### 1. Why source borer machines from China?
China offers competitive pricing, diverse manufacturers, and high production capacity, making it a cost-effective option for sourcing borer machines.
#### 2. How to find reliable manufacturers?
Utilize online platforms like Alibaba, Global Sources, and Made-in-China. Verify manufacturers’ credentials through customer reviews, certifications, and site visits if possible.
#### 3. What certifications should I look for?
Ensure manufacturers comply with international standards such as ISO 9001 for quality management, CE marking for European safety, and other relevant industry-specific certifications.
#### 4. What is the typical lead time for production?
Lead times vary but generally range from 30 to 90 days depending on order size, customization requirements, and the manufacturer’s schedule.
#### 5. How can I ensure the quality of the machines?
Conduct thorough inspections, request pre-shipment samples, and hire third-party quality inspection services to assess product quality before shipping.
#### 6. What are the payment terms?
Common payment terms include 30% upfront and 70% before shipment, but terms can be negotiated based on the relationship and order size.
#### 7. What shipping methods are available?
Options include sea freight, air freight, and express shipping (e.g., DHL, FedEx). Sea freight is typically the most cost-effective for large orders.
#### 8. How to handle customs and import duties?
Work with freight forwarders and customs brokers to navigate import regulations, handle documentation, and ensure compliance with local laws.
#### 9. Are there risks involved?
Risks include quality issues, delays, and communication barriers. Mitigate these by thorough vetting of suppliers, clear contracts, and regular communication.
#### 10. Can I visit the factories?
Yes, visiting factories is recommended to verify capabilities, meet the team, and build stronger relationships with manufacturers.
By following these guidelines, you can streamline the process of sourcing and manufacturing borer machines in China, ensuring quality and efficiency.
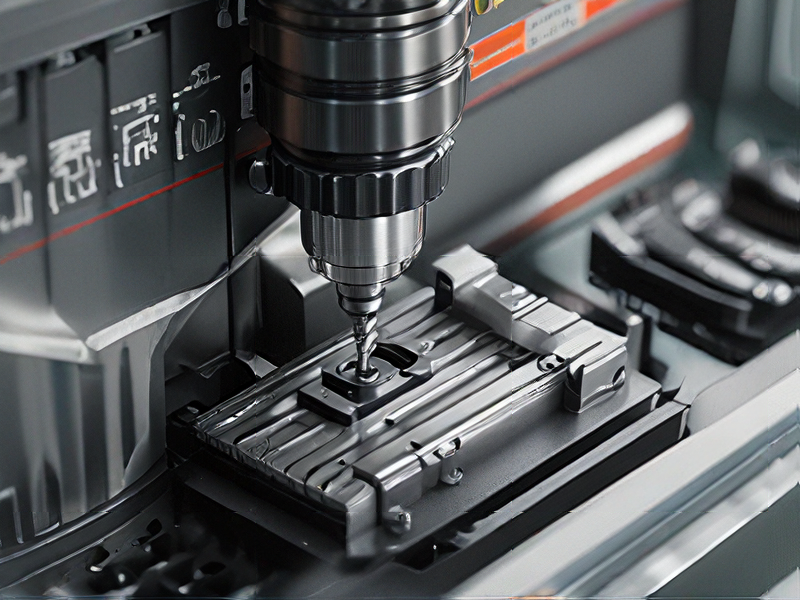