Technology and Applications of boring machining
Technology and Applications of Boring Machining
Technology:
Boring is a machining process used to enlarge holes or cylindrical cavities that have already been drilled, cast, or forged. The process involves a single-point cutting tool or boring head that removes material to achieve precise dimensions, improved surface finish, and accurate geometrical shapes. Boring machines can be horizontal or vertical, with CNC (Computer Numerical Control) technology being commonly integrated for enhanced precision and automation.
Key components of boring technology include:
1. Boring Bars and Heads: Tools that hold the cutting insert and are designed to minimize deflection and vibration.
2. Cutting Inserts: Replaceable tools made from high-speed steel, carbide, or other materials to ensure efficient cutting.
3. Machine Tools: CNC boring mills and jig borers that offer high accuracy and repeatability.
Applications:
Boring machining is widely used across various industries due to its ability to produce high-precision internal diameters and surface finishes. Key applications include:
1. Automotive Industry: Boring is used to finish engine cylinders, crankshaft bearing holes, and other critical components requiring tight tolerances.
2. Aerospace Industry: The process is essential for creating precise components in jet engines, landing gear, and structural parts that demand high accuracy and surface quality.
3. Heavy Machinery: Large-scale boring machines are employed in the production of hydraulic cylinders, gearboxes, and other heavy equipment components.
4. Oil and Gas: Boring is critical in manufacturing pipeline valves, pump housings, and drill collars where precise internal dimensions are crucial for operational efficiency.
5. Tool and Die Making: Precision boring ensures the accurate production of molds and dies, which are foundational in manufacturing industries.
By integrating advanced technologies like CNC and high-performance cutting materials, boring machining continues to evolve, offering greater precision, efficiency, and application versatility.
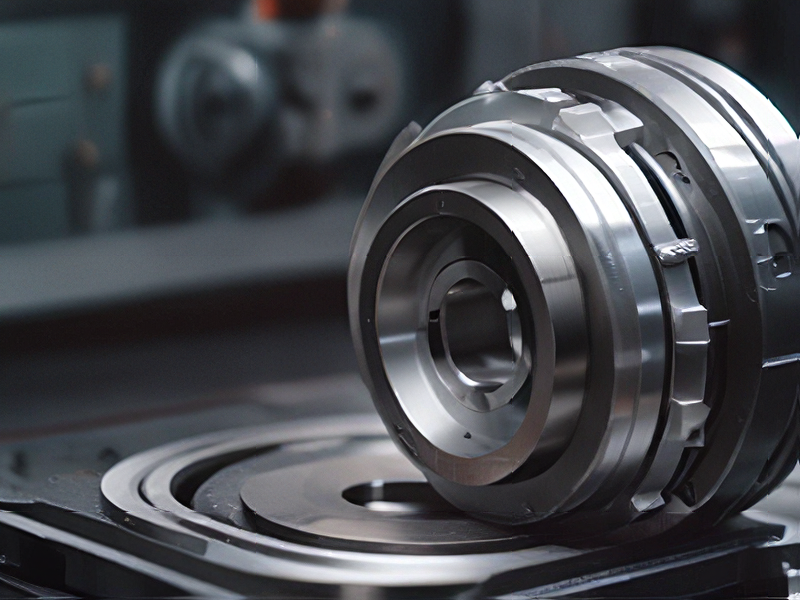
Quality Testing Methods for boring machining and how to control quality
Quality testing for boring machining involves several methods to ensure precision, surface finish, and dimensional accuracy. Here are key methods and control measures:
Methods:
1. Dimensional Inspection:
– Vernier Calipers and Micrometers: Measure bore diameter and length.
– Bore Gauges: Check internal diameter with high accuracy.
2. Surface Finish Inspection:
– Surface Roughness Testers: Evaluate the texture and smoothness of the bore surface.
3. Roundness and Cylindricity:
– Roundness Testers: Ensure the bore is perfectly round.
– Cylindricity Gauges: Measure the overall cylindrical shape consistency.
4. Concentricity Check:
– Coordinate Measuring Machines (CMMs): Assess the alignment of the bore center with other features.
Quality Control Measures:
1. Tool Selection and Maintenance:
– Use high-quality boring tools suitable for the material.
– Regularly inspect and replace worn-out tools to maintain cutting precision.
2. Machining Parameters:
– Optimize cutting speed, feed rate, and depth of cut based on material properties to avoid excessive tool wear and ensure a smooth finish.
3. Calibration of Equipment:
– Regularly calibrate measurement tools and machines to ensure accuracy in readings.
4. Process Monitoring:
– Implement real-time monitoring systems to track machining conditions and detect any anomalies early.
5. Operator Training:
– Ensure that operators are well-trained in using the machinery and measurement tools correctly.
6. Environmental Control:
– Maintain a controlled environment (temperature and humidity) to prevent material expansion or contraction, which can affect machining precision.
By combining precise measurement techniques and robust quality control measures, boring machining processes can achieve high levels of accuracy and consistency, ensuring the final product meets the desired specifications.
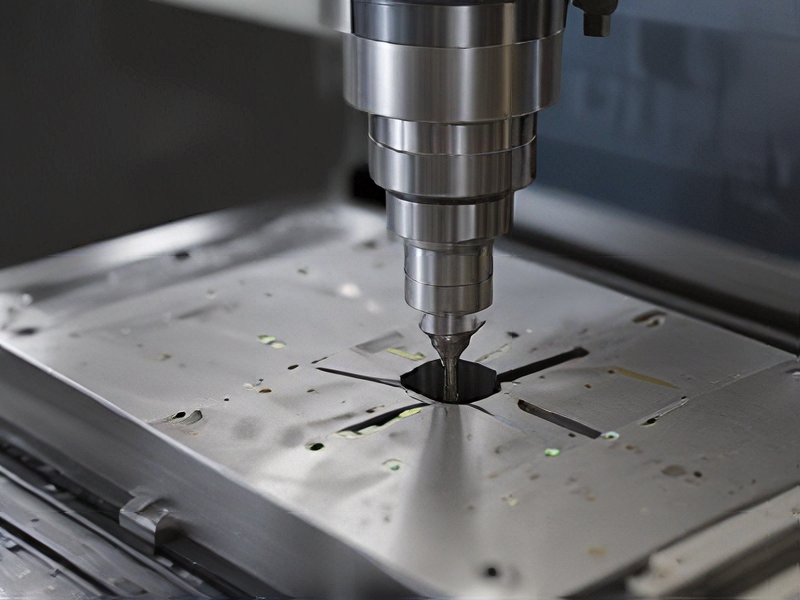
Tips for Procurement and Considerations when Purchasing from boring machining
When procuring boring machining services, consider the following tips to ensure a successful purchase:
1. Understand Requirements:
Clearly define the specifications, including dimensions, tolerances, materials, and surface finish requirements. Detailed blueprints and technical drawings can help avoid misunderstandings.
2. Vendor Selection:
Choose vendors with proven experience in boring machining. Check their reputation, certifications, and past project quality. It’s crucial they have expertise with the specific materials and tolerances your project demands.
3. Equipment Capabilities:
Ensure the vendor’s machinery can handle your project’s complexity. Advanced CNC boring machines offer higher precision and efficiency. Verify their maintenance and calibration schedules to guarantee accuracy.
4. Material Quality:
Specify the material grade and ensure it meets industry standards. Subpar material can lead to defects and failure in the final product. Request material certificates and perform quality checks if necessary.
5. Quality Control:
Implement stringent quality control measures. Insist on inspection reports and adherence to ISO or other relevant standards. Regular audits and in-process inspections help maintain high-quality output.
6. Lead Times and Production Capacity:
Confirm the vendor’s capacity to meet your delivery schedule. Delays can disrupt production timelines and incur additional costs. A vendor with flexible capacity can accommodate urgent orders.
7. Cost and Payment Terms:
Obtain detailed quotes and compare costs across multiple vendors. Ensure the quote includes all aspects of production, including setup and tooling. Negotiate favorable payment terms, considering cash flow and project milestones.
8. Communication:
Maintain clear and constant communication with the vendor. Regular updates on production status, potential issues, and changes in requirements help avoid surprises and ensure timely delivery.
9. Post-Purchase Support:
Choose vendors offering post-purchase support, including adjustments, repairs, and technical advice. This ensures long-term reliability and performance of the machined parts.
By focusing on these considerations, you can optimize the procurement process for boring machining services, ensuring high-quality, cost-effective, and timely delivery of machined parts.
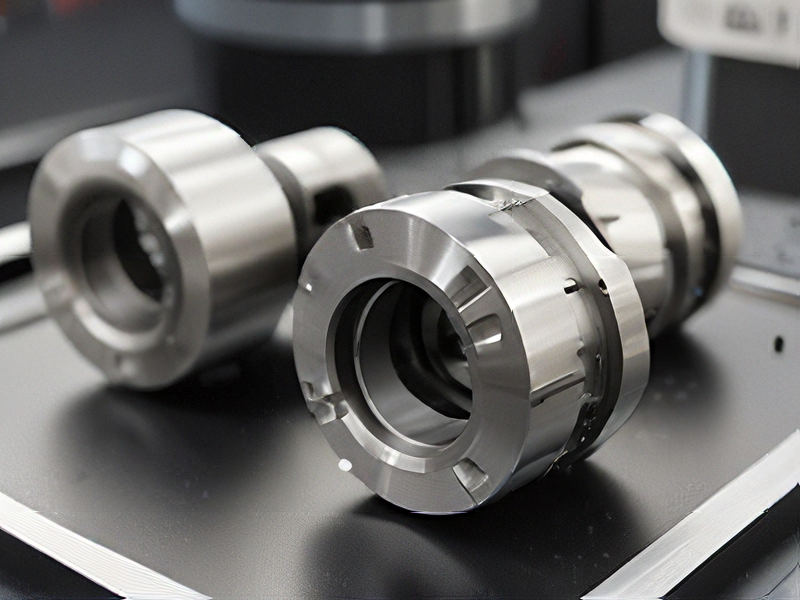
FAQs on Sourcing and Manufacturing from boring machining in China
FAQs on Sourcing and Manufacturing Boring Machining in China
1. Why source boring machining from China?
China offers cost-effective solutions, advanced technology, and skilled labor, making it an attractive option for boring machining services.
2. How do I find reliable manufacturers?
Use online platforms like Alibaba, Global Sources, and Made-in-China. Verify credentials through third-party audits and reviews, and request samples before committing.
3. What are the quality standards?
Ensure manufacturers comply with ISO 9001 and other relevant industry certifications. Regular inspections and quality checks are essential to maintain standards.
4. How can I communicate effectively?
Many manufacturers have English-speaking staff. Use clear, detailed specifications and consider hiring a local agent or translator to bridge communication gaps.
5. What is the typical lead time?
Lead times vary based on the complexity of the project and the manufacturer’s capacity. Generally, expect 4-8 weeks from order confirmation to delivery.
6. How do I handle intellectual property concerns?
Sign non-disclosure agreements (NDAs) and work with manufacturers who respect IP laws. Register patents and trademarks in China to enhance protection.
7. What are the payment terms?
Common terms include a 30% deposit upfront and the balance upon completion. Letters of credit (L/C) and escrow services can also be used for added security.
8. How do I manage logistics?
Work with experienced freight forwarders familiar with Chinese exports. They can assist with shipping, customs clearance, and ensuring timely delivery.
9. Are there cultural considerations?
Building relationships is crucial. Respect local customs and holidays, and practice patience and understanding during negotiations.
10. What are the common challenges?
Potential challenges include language barriers, quality control, and logistical issues. Mitigate risks through thorough research, clear contracts, and regular communication.
Sourcing boring machining from China can be highly beneficial if approached strategically, ensuring quality, cost savings, and efficient production timelines.
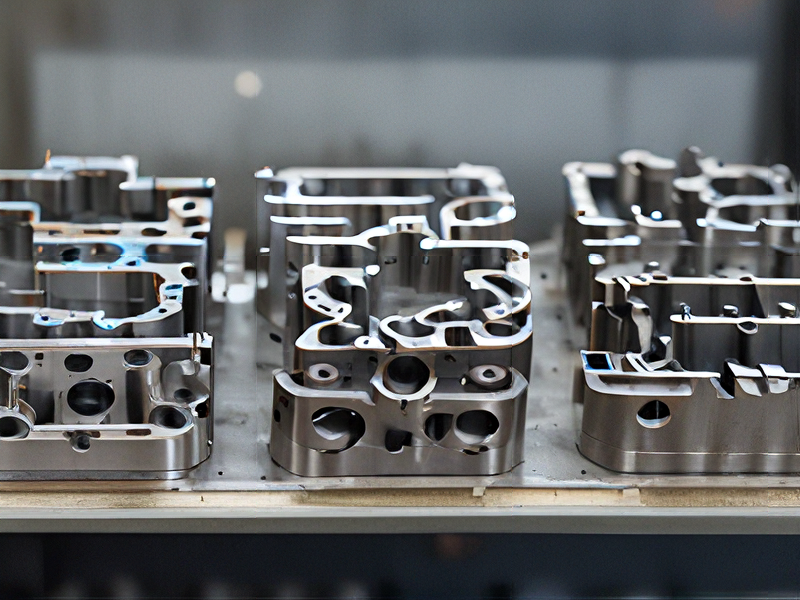