Technology and Applications of laser cutting machine tube
Laser cutting technology uses a focused laser beam to cut materials with high precision. It is widely applied in various industries due to its efficiency and versatility. The technology for cutting tubes, specifically, involves specialized machines capable of handling the unique challenges posed by the tubular structure.
Technology of Laser Tube Cutting
Laser Source: Fiber lasers are commonly used due to their high power and efficiency. They provide a concentrated beam that can cut through various materials, including metals, plastics, and composites.
Beam Delivery: The laser beam is directed through optics and focused onto the tube’s surface. Advanced systems use automatic focus adjustment to ensure consistent cutting quality across different tube diameters and thicknesses.
Cutting Head: Equipped with sensors, the cutting head follows the programmed path precisely. It often includes features like automatic nozzle cleaning and collision detection to maintain performance and safety.
Tube Handling: Modern machines have automated systems for feeding, rotating, and positioning tubes. This automation minimizes manual intervention, reducing errors and increasing productivity.
Control Software: Sophisticated software allows for precise control over cutting parameters and path optimization. CAD/CAM integration enables the direct use of design files, streamlining the production process.
Applications of Laser Tube Cutting
Automotive: Used for creating complex exhaust systems, chassis components, and structural parts with high precision and repeatability.
Aerospace: Ideal for cutting lightweight yet strong components required in aircraft structures, where precision is critical.
Furniture Manufacturing: Enables intricate designs and efficient production of metal and plastic furniture frames.
Construction: Used in cutting structural tubes for buildings, bridges, and other infrastructure, providing accurate and clean cuts that facilitate assembly.
Medical Devices: Precision cutting is crucial for manufacturing various medical instruments and devices, ensuring compliance with strict industry standards.
Advantages
Laser tube cutting offers numerous benefits, including high precision, reduced waste, minimal thermal distortion, and the ability to create complex geometries that traditional methods cannot achieve. It significantly enhances productivity and product quality across various industries.

Quality Testing Methods for laser cutting machine tube and how to control quality
Quality Testing Methods for Laser Cutting Machine Tubes
1. Dimensional Accuracy:
– Method: Use calipers and micrometers to measure the tube’s dimensions and ensure they meet specified tolerances.
– Control: Regular calibration of measuring instruments and routine checks against standards.
2. Edge Quality:
– Method: Visual inspection and surface roughness testers can assess the smoothness and finish of cut edges.
– Control: Optimize cutting parameters (speed, power, focus) and maintain clean optics and nozzles.
3. Cut Surface Integrity:
– Method: Use non-destructive testing (NDT) techniques like ultrasonic testing to check for internal flaws or inconsistencies.
– Control: Regularly inspect and replace worn or damaged cutting components.
4. Consistency:
– Method: Statistical Process Control (SPC) to monitor and analyze cutting data over time.
– Control: Implement process control charts and conduct regular machine maintenance.
5. Material Compatibility:
– Method: Test cuts on different materials to ensure the machine performs well across various substrates.
– Control: Use material-specific settings and regularly update them based on performance feedback.
6. Burr Formation:
– Method: Visual and tactile inspection to detect any burrs or rough edges.
– Control: Adjust cutting parameters and maintain proper nozzle alignment.
7. Heat Affected Zone (HAZ):
– Method: Inspect for discoloration or structural changes using metallographic analysis.
– Control: Optimize cooling strategies and cutting speed to minimize HAZ.
Controlling Quality:
– Preventive Maintenance: Regularly service the laser cutting machine to ensure all parts function correctly.
– Operator Training: Ensure operators are well-trained in using the machine and understanding the parameters affecting cut quality.
– Standard Operating Procedures (SOPs): Develop and adhere to SOPs for machine operation and quality checks.
– Software Updates: Regularly update the machine’s software to incorporate the latest improvements and bug fixes.
– Documentation and Records: Keep detailed records of cutting conditions, maintenance, and quality checks for traceability and continuous improvement.
By combining these testing methods and control measures, the quality of laser-cut tubes can be effectively managed, ensuring precision and consistency in production.
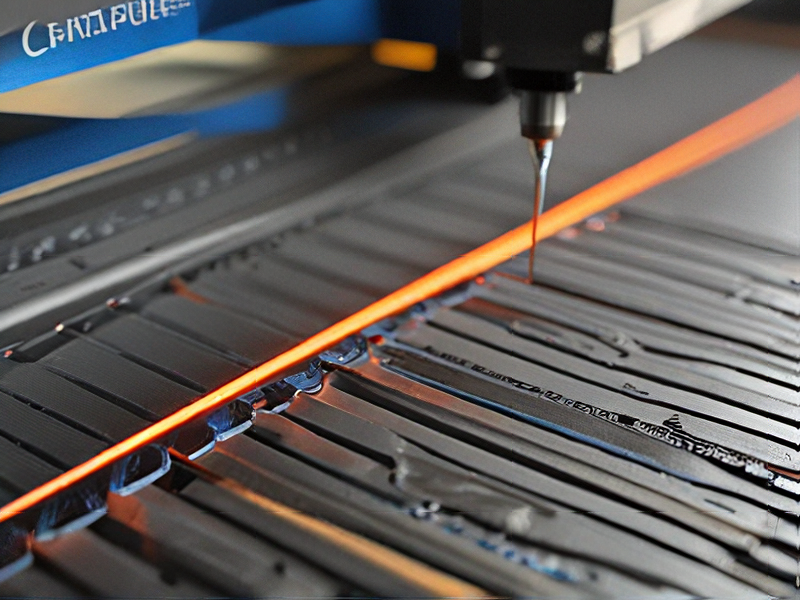
Tips for Procurement and Considerations when Purchasing from laser cutting machine tube
When procuring a laser cutting machine for tubes, several critical factors should guide your decision-making to ensure optimal performance and value:
1. Machine Specifications
– Laser Power: Choose a machine with sufficient laser power (measured in watts) to cut through the materials you typically use. Higher power levels enable faster cutting and can handle thicker materials.
– Cutting Speed: Higher cutting speeds improve productivity. Ensure the machine offers the speed needed for your production requirements.
– Accuracy and Precision: Look for machines with high precision to ensure clean cuts and minimal waste, which is crucial for complex designs.
2. Material Compatibility
– Verify that the machine can handle the types of materials you work with, such as steel, aluminum, or copper. Some lasers are better suited for specific materials.
3. Tube Size and Shape
– Ensure the machine accommodates the range of tube sizes (diameter and length) and shapes (round, square, rectangular) you use in your operations.
4. Software and Control Systems
– The machine should come with user-friendly software that supports your design and production needs. Look for features like CAD/CAM compatibility and easy integration with existing systems.
5. Automation and Versatility
– Consider machines with automated loading and unloading systems to reduce labor costs and improve efficiency. Versatile machines that can switch between different tasks or tube shapes can enhance productivity.
6. After-Sales Support and Maintenance
– Reliable after-sales support is crucial for troubleshooting and maintenance. Check for the availability of spare parts, service centers, and technician support.
7. Total Cost of Ownership
– Evaluate the initial purchase price, operating costs (energy consumption, maintenance), and potential downtime costs. Sometimes, a higher upfront cost can result in lower long-term expenses.
8. Safety Features
– Ensure the machine has robust safety features to protect operators, including proper enclosures, emergency stop buttons, and safety interlocks.
9. Vendor Reputation
– Research the vendor’s reputation for reliability, customer service, and support. Read reviews and seek references to gauge satisfaction from other customers.
10. Warranty and Training
– Look for comprehensive warranties and training programs to ensure your team can operate the machine efficiently and safely.
By considering these factors, you can make an informed decision that aligns with your production needs and budget, ensuring a worthwhile investment in a laser cutting machine for tubes.

FAQs on Sourcing and Manufacturing from laser cutting machine tube in China
FAQs on Sourcing and Manufacturing Laser Cutting Machine Tubes in China
1. Why source laser cutting machine tubes from China?
China is a global leader in manufacturing, offering advanced technology, cost-effective production, and a large selection of suppliers, making it a prime destination for sourcing laser cutting machine tubes.
2. How do I find reliable suppliers?
Utilize platforms like Alibaba, Made-in-China, and Global Sources. Look for verified suppliers with positive reviews and request samples before committing to large orders.
3. What should I consider when selecting a supplier?
Evaluate their manufacturing capabilities, quality control processes, certifications (like ISO), and experience in exporting. Communication efficiency and responsiveness are also key.
4. What are the common materials used in laser cutting machine tubes?
Common materials include stainless steel, carbon steel, aluminum, and other alloys, each offering different benefits based on the application.
5. What are the quality standards for these products?
Ensure suppliers adhere to international standards such as ISO 9001 for quality management and CE marking for safety compliance in the European market.
6. How can I ensure the quality of the products?
Request third-party inspections, visit the factory if possible, and ask for detailed test reports. Regular audits and quality agreements can also help maintain standards.
7. What is the typical lead time for manufacturing?
Lead times can vary, but typically range from 30 to 60 days depending on the order size and complexity. Custom designs may take longer.
8. How do I handle shipping and logistics?
Work with a reliable freight forwarder who can manage customs clearance, shipping, and delivery. Consider Incoterms like FOB (Free on Board) or CIF (Cost, Insurance, and Freight) to define responsibilities.
9. What are the payment terms usually offered?
Common payment terms include T/T (Telegraphic Transfer) with a deposit (30% upfront and 70% before shipment), L/C (Letter of Credit), and sometimes PayPal for smaller transactions.
10. How do I handle intellectual property protection?
Use Non-Disclosure Agreements (NDAs) and ensure your designs are patented in China if applicable. Partnering with reputable suppliers reduces the risk of IP theft.
11. What are the potential risks and how can I mitigate them?
Risks include quality issues, delays, and communication barriers. Mitigate these by building strong relationships, setting clear expectations, and maintaining regular oversight.
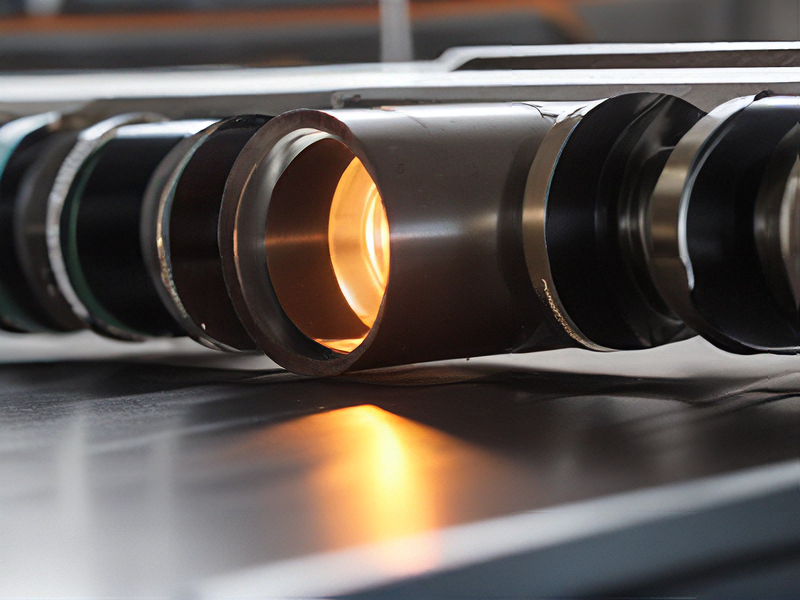