Technology and Applications of laser metal cutters
Laser metal cutters employ concentrated beams of light to precisely and efficiently cut through various metals. This technology finds extensive applications across industries such as manufacturing, automotive, aerospace, and electronics due to its versatility and accuracy.
The key components of a laser metal cutter include the laser source (typically CO2 or fiber lasers), focusing optics, CNC (Computer Numerical Control) system, and a cutting bed. These systems can cut through metals ranging from thin sheets to thick plates with high precision and minimal heat-affected zones, reducing material wastage and post-processing requirements.
Applications of laser metal cutters include:
1. Sheet Metal Fabrication: Used extensively in manufacturing for cutting intricate shapes in sheet metal used in construction, appliances, and consumer goods.
2. Automotive Industry: Laser cutters are vital for producing precise components such as chassis parts, exhaust pipes, and panels.
3. Aerospace: Critical for manufacturing aerospace components where precision, reliability, and material integrity are paramount.
4. Electronics: Used in cutting metal parts for devices like smartphones, computers, and other electronics.
5. Prototyping and Rapid Manufacturing: Enables quick iteration and production of prototypes and small batches of custom parts.
Advantages of laser metal cutters include high speed, accuracy, and the ability to cut complex shapes with tight tolerances. However, they require skilled operators to optimize settings and ensure safety due to the high-powered lasers involved. As technology advances, laser metal cutters continue to evolve, offering improved efficiency and expanding their applications in various industries worldwide.
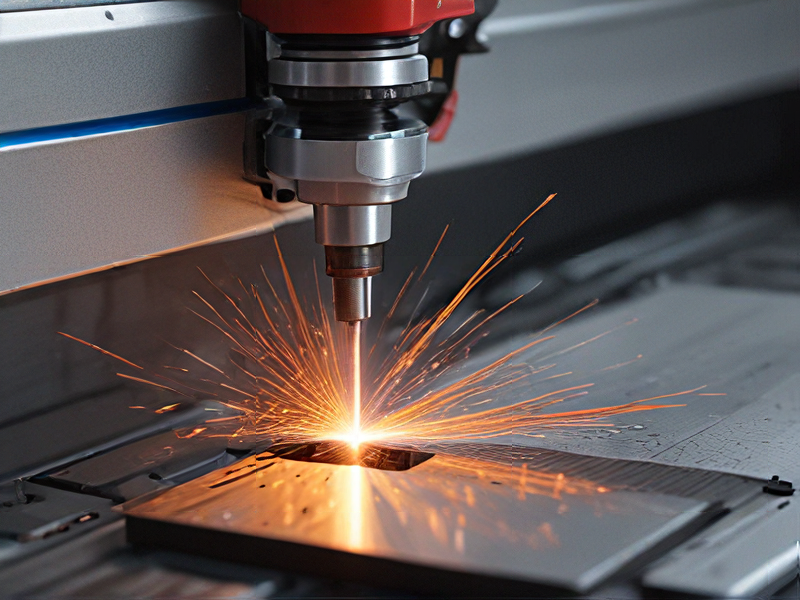
Quality Testing Methods for laser metal cutters and how to control quality
Quality testing methods for laser metal cutters typically involve several key approaches to ensure precision and reliability in the cutting process.
1. Dimensional Accuracy: Utilize precision measuring tools such as calipers or coordinate measuring machines (CMM) to verify that cut parts conform to specified dimensional tolerances.
2. Surface Quality: Visual inspection and tactile methods can assess the smoothness and finish of cut surfaces. Optical profilometers or surface roughness testers can provide quantitative data on surface roughness.
3. Edge Quality: Inspect the edges of cut parts for burrs, dross, and sharpness using methods such as microscopy or edge quality gauges.
4. Material Integrity: Non-destructive testing methods like ultrasonic testing or dye penetrant inspection can detect defects like cracks or voids in the material caused by the cutting process.
5. Accuracy of Features: Use optical comparators or vision systems to verify the accuracy of features such as holes, slots, or other geometric shapes cut into the metal.
To control quality effectively:
– Regular Calibration: Ensure laser cutter components are calibrated regularly to maintain accuracy.
– Process Monitoring: Implement real-time monitoring of cutting parameters (e.g., power, speed) to detect deviations that could affect quality.
– Operator Training: Train operators in proper machine operation, maintenance, and quality inspection techniques to minimize errors.
– Quality Assurance Procedures: Establish comprehensive quality assurance procedures that include periodic audits and checks to ensure adherence to quality standards.
By combining these testing methods with rigorous quality control measures, manufacturers can ensure consistent and high-quality output from laser metal cutters, meeting stringent industry requirements.

Tips for Procurement and Considerations when Purchasing from laser metal cutters
When purchasing from laser metal cutters, consider several key factors to ensure you get the best equipment for your needs:
1. Precision and Performance: Evaluate the laser cutter’s cutting precision, speed, and overall performance. Look for machines with high cutting accuracy and speed suitable for your intended materials and thicknesses.
2. Laser Power and Type: Different materials and thicknesses require specific laser powers (measured in watts). CO2 lasers are versatile for various materials, while fiber lasers excel in cutting metals. Choose based on your material requirements.
3. Bed Size and Capacity: The size of the cutting bed determines the maximum sheet size you can work with. Ensure it accommodates your typical sheet dimensions to avoid limitations in your projects.
4. Ease of Use and Software: User-friendly interfaces and intuitive software enhance productivity. Check for compatibility with your existing workflow and ease of programming.
5. Maintenance and Support: Understand the maintenance requirements and availability of technical support. Reliable after-sales service ensures minimal downtime and long-term usability.
6. Safety Features: Laser cutters involve high-power lasers and moving parts. Ensure the machine complies with safety standards and has features like emergency stop buttons and enclosed cutting areas.
7. Reviews and References: Research customer reviews and ask for references from the manufacturer. Insights from other users can provide valuable information about reliability and performance.
8. Price and Value: Compare prices across different manufacturers while considering long-term value. Cheaper options may cost more in maintenance and downtime over time.
9. Training and Skill Requirements: Assess the training needed for operators. Some machines may require specialized skills or certifications.
10. Future Expansion: Consider your future needs. Choose a machine that allows for upgrades or additional features as your business grows.
By carefully considering these factors, you can make an informed decision when purchasing a laser metal cutter that meets your specific procurement needs and operational requirements.
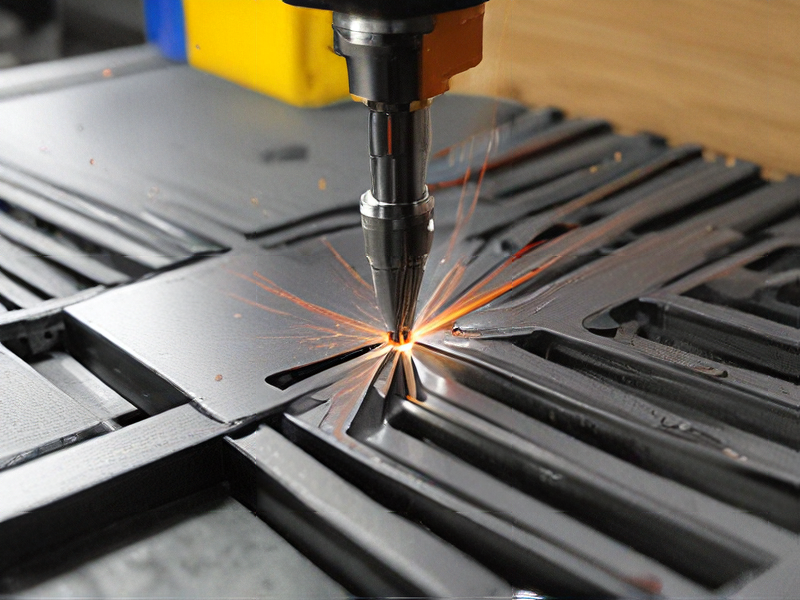
FAQs on Sourcing and Manufacturing from laser metal cutters in China
Certainly! Here are some FAQs on sourcing and manufacturing from laser metal cutters in China:
1. What are the advantages of sourcing laser metal cutters from China?
China offers cost-effective manufacturing due to lower labor and production costs. The country has a robust industrial infrastructure supporting advanced technologies like laser cutting.
2. How can I ensure quality when sourcing from China?
Conduct thorough supplier audits and request samples before bulk orders. Implement quality control measures and consider using a reputable sourcing agent to oversee production.
3. What are common challenges when sourcing laser metal cutters from China?
Challenges include language barriers, cultural differences, and potential logistics issues. Intellectual property protection is also a concern; hence, it’s crucial to have legal agreements in place.
4. Are there specific regions in China known for laser cutting expertise?
Coastal regions such as Guangdong and Jiangsu are known for their advanced manufacturing capabilities, including laser cutting technologies.
5. What certifications should I look for in Chinese laser cutter manufacturers?
Look for ISO certifications (e.g., ISO 9001 for quality management) and compliance with international standards for laser equipment (e.g., CE certification for European markets).
6. How can I manage logistics and shipping from China?
Partner with reliable freight forwarders who specialize in international shipments. Plan for lead times and consider shipping methods based on cost and urgency.
7. What are typical payment terms when sourcing from Chinese manufacturers?
Payment terms often involve an initial deposit (e.g., 30%) with the balance due upon completion or shipment. Negotiate terms that align with your cash flow and risk management strategies.
8. How do I protect my intellectual property (IP) when manufacturing in China?
Use non-disclosure agreements (NDAs) and ensure clear contracts that specify IP ownership. Consider registering patents and trademarks both locally and internationally.
By addressing these FAQs, businesses can navigate the complexities of sourcing and manufacturing laser metal cutters from China effectively.
