Technology and Applications of 4×8 sheets plastic
4×8 sheets of plastic, typically made from materials like acrylic, polycarbonate, or PVC, find widespread application across various industries due to their versatility and durability. These sheets are commonly used in construction, signage, automotive, and DIY projects.
In construction, plastic sheets are favored for their lightweight nature, resistance to moisture and chemicals, and ease of installation. They are employed for glazing windows, skylights, and protective barriers. In signage, these sheets provide a durable substrate for outdoor and indoor signs, offering excellent clarity and weather resistance.
Automotive applications include interior trim components, dashboard covers, and protective shields due to their impact resistance and ability to be molded into complex shapes. DIY enthusiasts use them for projects such as greenhouse panels, shelving, and home improvement tasks like bathroom splash guards and decorative elements.
The technology behind these sheets involves advanced manufacturing processes such as extrusion, where molten plastic is forced through a die to create continuous sheets of uniform thickness. Injection molding is also utilized for producing specific shapes and components.
Advancements in plastic sheet technology have led to improvements in strength, UV resistance, and fire retardancy, expanding their applications even further. For instance, UV-stabilized sheets are suitable for outdoor use without yellowing or becoming brittle over time.
In conclusion, 4×8 plastic sheets play a crucial role across diverse industries and applications, offering a balance of affordability, durability, and versatility. Ongoing innovations continue to enhance their performance characteristics, ensuring they remain indispensable in modern manufacturing and construction practices.
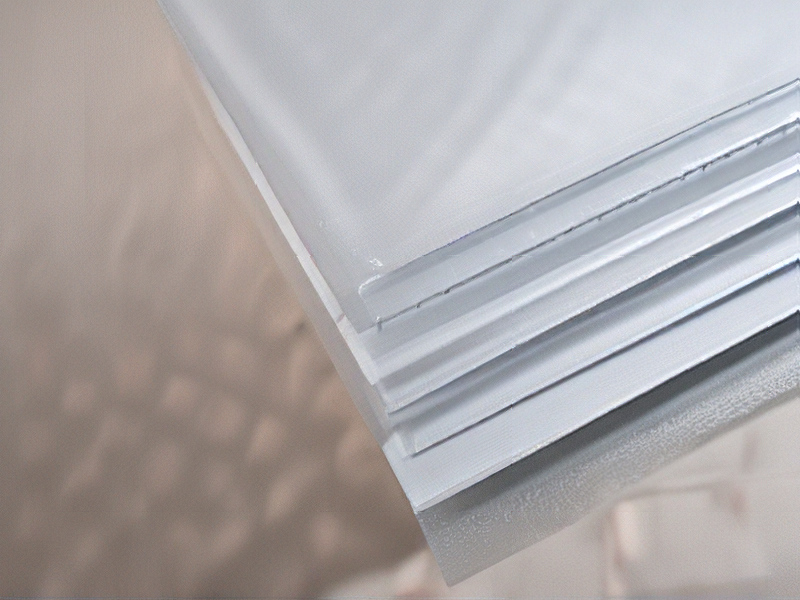
Quality Testing Methods for 4×8 sheets plastic and how to control quality
To ensure the quality of 4×8 sheets of plastic, several testing methods and quality control measures can be implemented:
1. Dimensional Accuracy: Measure dimensions using calibrated tools to ensure sheets meet specified tolerances.
2. Visual Inspection: Check for surface defects such as scratches, bubbles, or discoloration under proper lighting.
3. Weight and Thickness Measurement: Use scales and micrometers to verify weight consistency and thickness across the sheet.
4. Mechanical Properties Testing: Conduct tests like tensile strength, flexural modulus, and impact resistance to ensure sheets meet performance requirements.
5. Chemical Resistance: Assess resistance to chemicals by exposing samples to relevant substances and evaluating changes.
6. UV Stability: Expose samples to UV light and assess color stability and degradation resistance.
7. Heat Resistance: Perform tests to determine the sheets’ performance under high temperatures.
Quality control involves:
– Process Control: Regularly monitor manufacturing processes to identify and rectify deviations.
– Sampling and Testing: Implement sampling plans to ensure representative testing of each batch.
– Supplier Evaluation: Assess suppliers based on quality standards, consistency, and reliability.
– Documentation and Traceability: Maintain records of tests, inspections, and materials used for traceability and quality assurance.
By integrating these methods and controls, manufacturers can ensure that 4×8 plastic sheets meet rigorous quality standards, enhancing customer satisfaction and product reliability.
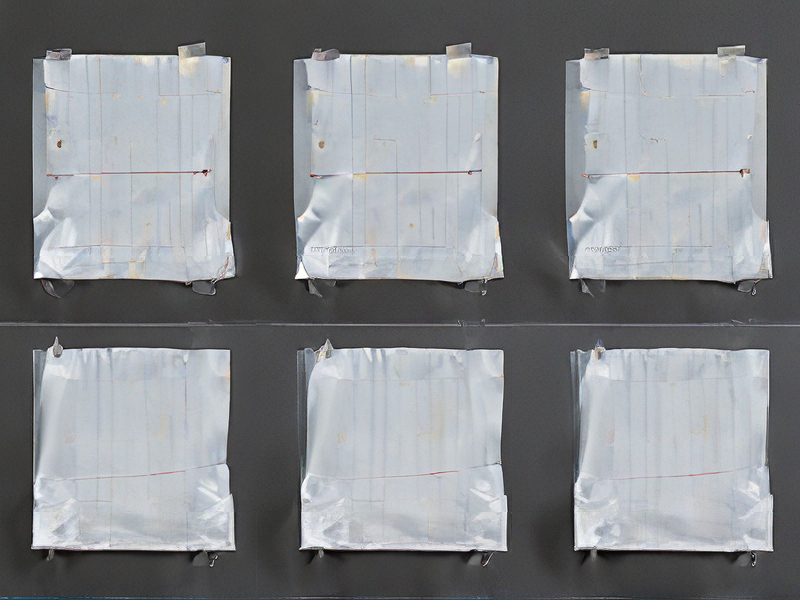
Tips for Procurement and Considerations when Purchasing from 4×8 sheets plastic
When purchasing 4×8 sheets of plastic, consider the following tips and considerations to ensure you make the right procurement decisions:
1. Material Type: Decide on the specific type of plastic sheeting you need based on its intended use. Options include acrylic, polycarbonate, PVC, and HDPE, each with varying strengths, durability, and chemical resistance.
2. Thickness: Determine the appropriate thickness of the plastic sheet based on the required strength and application. Thicker sheets offer more durability but can be heavier and more expensive.
3. Size Accuracy: Verify that the sheets are precisely 4×8 feet to fit your project requirements without the need for additional cutting, which can waste material and time.
4. Quality Standards: Ensure the sheets meet relevant quality standards and certifications for your industry or application, such as ASTM (American Society for Testing and Materials) standards.
5. Supplier Reputation: Choose a reputable supplier known for consistent quality, reliable delivery times, and good customer service. Check reviews and ask for references if necessary.
6. Cost Considerations: Compare prices from different suppliers while considering shipping costs and potential discounts for bulk purchases to optimize your procurement budget.
7. Environmental Impact: Evaluate the environmental impact of the plastic material you’re purchasing and consider eco-friendly options if applicable.
8. Handling and Storage: Plan for the safe handling and storage of the sheets upon delivery to prevent damage or deformation that could affect their usability.
9. Application Compatibility: Ensure the chosen plastic material is suitable for your specific application in terms of temperature resistance, UV stability, and chemical resistance.
10. Long-term Durability: Consider the expected lifespan of the plastic sheets in relation to your project’s requirements to avoid premature replacement costs.
By carefully considering these factors, you can make informed decisions when purchasing 4×8 plastic sheets that align with your project needs, budget constraints, and environmental considerations.
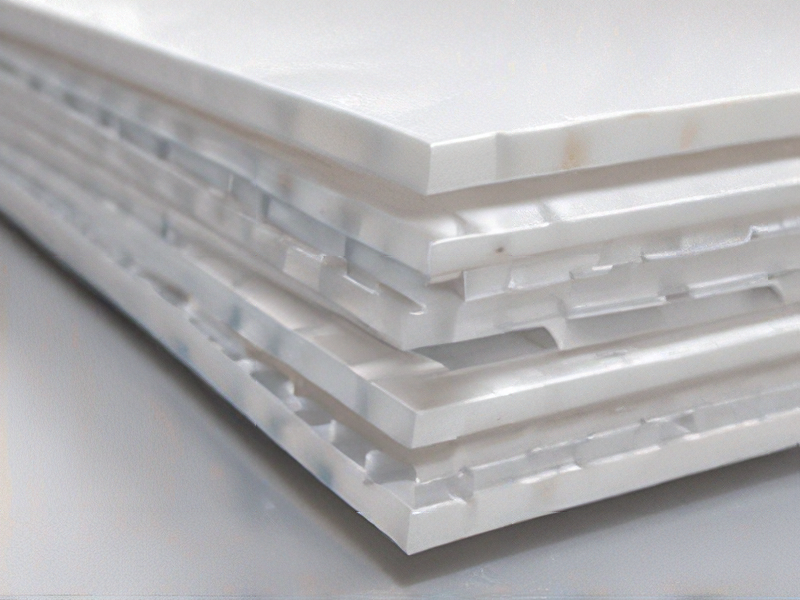
FAQs on Sourcing and Manufacturing from 4×8 sheets plastic in China
When sourcing and manufacturing 4×8 sheets of plastic in China, several key considerations and frequently asked questions (FAQs) arise:
1. Quality Assurance: How can I ensure the quality meets my standards?
– Engage with suppliers who have a proven track record and ask for samples or visit their facilities if feasible. Implementing clear quality control measures and inspections throughout production is crucial.
2. Material Options: What types of plastic materials are available?
– China offers a wide range of plastics such as ABS, PVC, acrylic, and polycarbonate. Specify your requirements regarding durability, transparency, or specific properties needed for your application.
3. Cost Efficiency: How can I ensure competitive pricing?
– Obtain multiple quotes from different suppliers and negotiate based on volume and long-term partnership potential. Consider factors like material grade, production volume, and shipping costs.
4. Lead Times: What are typical production lead times?
– Lead times can vary based on material availability, order volume, and production schedules. Clarify expectations upfront and communicate deadlines clearly to ensure timely delivery.
5. Customization: Can I customize sheet size, thickness, and color?
– Yes, many manufacturers in China offer customization options. Provide detailed specifications for size, thickness, color, and any additional features required.
6. Packaging and Shipping: How are products packaged and shipped?
– Packaging should ensure protection during transit. Discuss packaging options with suppliers and consider factors like container loading efficiency and shipping methods (sea freight, air freight).
7. Quality Control: What measures are in place to maintain product quality?
– Suppliers may have quality certifications (ISO, QC standards) and inspection processes. Specify quality criteria and inspections to be conducted during and after production.
8. Communication and Support: How can I effectively communicate with suppliers?
– Clear communication channels are crucial. Establish a single point of contact, utilize digital communication tools, and clarify expectations regarding updates and feedback.
Navigating sourcing and manufacturing 4×8 plastic sheets in China requires thorough research, clear communication, and adherence to quality standards throughout the process to ensure successful outcomes.
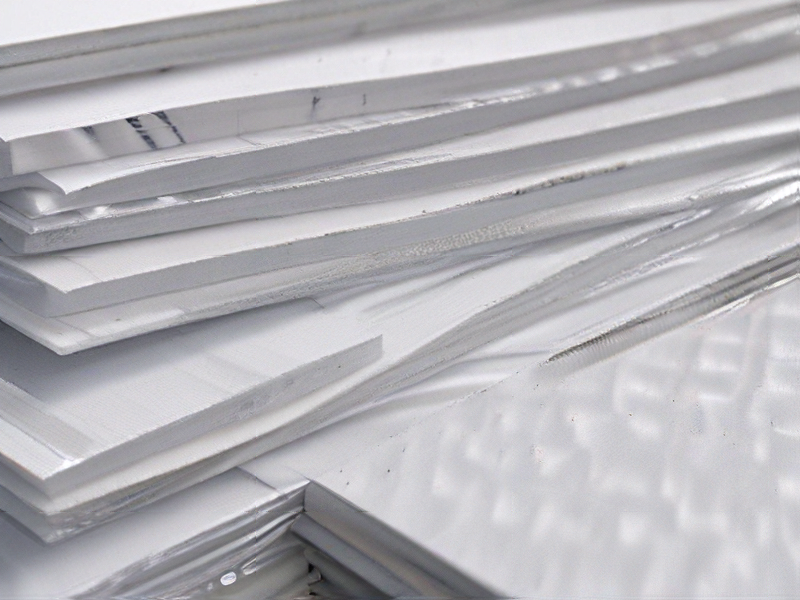