Technology and Applications of sheet bending
Sheet bending technology involves the process of forming metal sheets into desired shapes using mechanical or hydraulic forces. This process is crucial across various industries, including automotive, aerospace, construction, and manufacturing.
Types of Sheet Bending:
1. Press Brake Bending: Utilizes a press brake machine to exert force on the sheet metal, creating bends at predetermined angles. This method is versatile and suitable for producing a wide range of shapes and sizes.
2. Roll Bending: Involves passing the sheet metal through rollers to gradually curve or bend it. This method is used for producing cylindrical or conical shapes, such as tubes or pipes.
Applications:
1. Automotive Industry: Used in manufacturing vehicle components like chassis, brackets, and panels. Sheet bending ensures parts meet design specifications and structural requirements.
2. Aerospace Industry: Critical for fabricating aircraft components such as fuselage panels, wing ribs, and structural supports. Precision and strength are paramount in aerospace applications.
3. Construction: Employed in creating architectural features, HVAC ducts, roofing components, and structural supports. Sheet bending allows for customization to fit specific building designs.
4. Manufacturing: Essential for producing appliances, machinery enclosures, electronic equipment housings, and various consumer goods. Bending technology ensures efficient production and product durability.
Technological Advancements:
Modern advancements include computer numerical control (CNC) systems that enhance accuracy, repeatability, and automation in sheet bending processes. Simulation software allows engineers to predict and optimize bending outcomes, reducing material waste and production time.
Challenges and Considerations:
Factors such as material type (e.g., aluminum, steel), thickness, bend radius, and tooling selection influence the bending process. Techniques like air bending, bottoming, and coining offer flexibility in achieving different bend angles and surface finishes.
In conclusion, sheet bending technology is integral to diverse industries, enabling the fabrication of complex components with precision and efficiency. Continuous advancements in machinery and techniques further enhance capabilities, supporting innovation and quality in manufacturing practices.
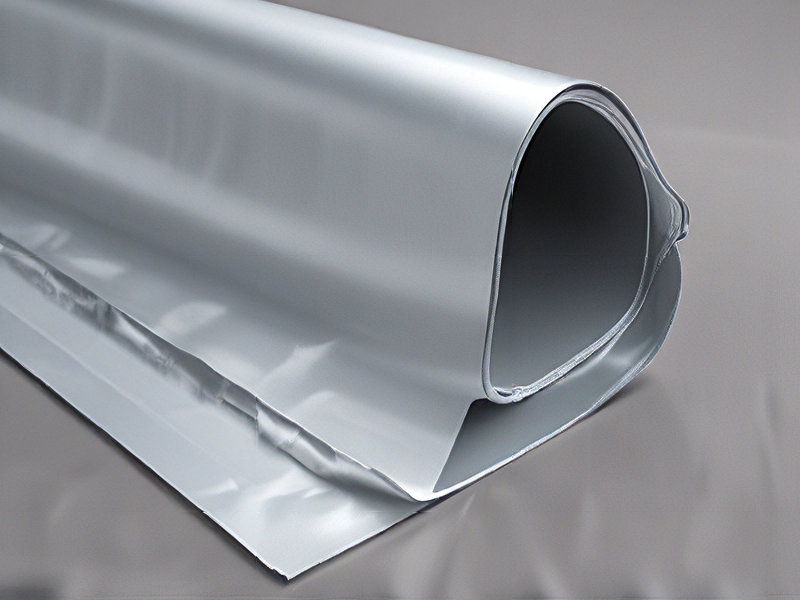
Quality Testing Methods for sheet bending and how to control quality
Quality testing methods for sheet bending typically involve both visual inspections and measurements:
1. Visual Inspection: Ensure bends are smooth without cracks, wrinkles, or other deformations. Check for consistent angles and dimensions according to specifications.
2. Measurement Checks: Use tools like calipers, micrometers, or height gauges to measure bend angles, radii, and dimensions. Compare these measurements against design blueprints or tolerance limits.
3. Surface Quality: Inspect for scratches, dents, or surface imperfections that could affect functionality or aesthetics.
4. Fixture Checks: Ensure the sheet is securely held during bending to prevent slippage or misalignment that can lead to defects.
5. Material Testing: Verify material properties such as hardness and tensile strength to ensure they meet required specifications.
To control quality:
– Standard Operating Procedures (SOPs): Develop detailed procedures for each bending operation, including setup, tooling, and inspection criteria.
– Training: Train operators on proper bending techniques, measurement methods, and quality standards.
– Regular Maintenance: Keep bending equipment calibrated and maintained to prevent inaccuracies.
– Quality Assurance Checks: Conduct regular audits and random checks to monitor process adherence and product quality.
By integrating these methods and controls, manufacturers can ensure consistent, high-quality sheet bending operations that meet customer requirements and standards.
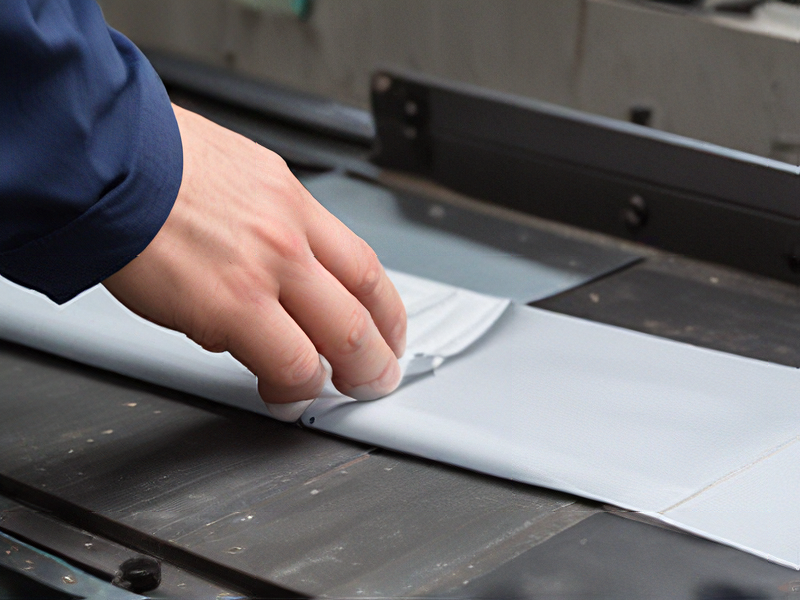
Tips for Procurement and Considerations when Purchasing from sheet bending
When purchasing sheet bending services, consider the following tips to ensure a successful procurement process:
1. Supplier Capability Assessment: Evaluate potential suppliers based on their experience, equipment capabilities, and quality certifications (ISO, ASME, etc.). This ensures they can meet your specific bending requirements.
2. Quality Standards: Insist on quality assurance measures such as material traceability, inspection protocols, and adherence to industry standards. This guarantees that the bent sheets meet your specifications and regulatory requirements.
3. Cost and Value: Compare quotes from multiple suppliers, balancing cost with the value offered in terms of quality, lead times, and additional services (e.g., finishing, packaging). Avoid choosing solely based on the lowest price to ensure overall satisfaction.
4. Technical Expertise: Engage with suppliers who demonstrate technical expertise and are proactive in offering suggestions for improving designs or optimizing manufacturing processes. This partnership can lead to better outcomes and cost efficiencies.
5. Lead Times and Flexibility: Assess suppliers’ ability to meet your project timelines and their flexibility to accommodate changes in order volume or specifications. Clear communication on lead times and production schedules is crucial for project planning.
6. Customer References and Reviews: Seek references from previous clients and review online feedback platforms to gauge suppliers’ reliability, responsiveness to issues, and overall customer satisfaction.
7. Contractual Agreements: Establish clear contractual terms covering pricing, delivery schedules, quality standards, warranties, and dispute resolution mechanisms. This mitigates risks and ensures both parties are aligned on expectations.
8. Environmental and Ethical Practices: Consider suppliers’ commitment to sustainable practices, including waste management and energy efficiency. Ethical considerations such as labor practices and compliance with local regulations are also important.
By focusing on these considerations, you can streamline your procurement process for sheet bending services while ensuring high-quality outcomes and positive supplier relationships.
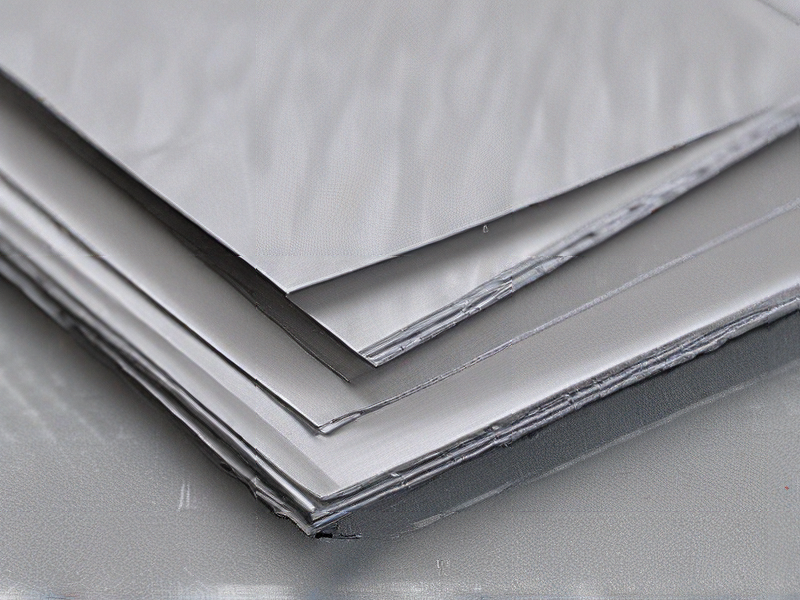
FAQs on Sourcing and Manufacturing from sheet bending in China
When sourcing sheet bending services from China, several frequently asked questions (FAQs) typically arise:
1. What are the advantages of sourcing sheet bending from China?
China offers competitive pricing due to lower labor and production costs. They also have a vast network of manufacturers capable of handling large volumes and complex designs.
2. How can I ensure quality when sourcing from China?
Select manufacturers with certifications like ISO 9001, which indicate adherence to international quality standards. Conducting factory audits and requesting samples can also verify their capabilities.
3. What materials can be used for sheet bending in China?
Chinese manufacturers work with various materials such as stainless steel, aluminum, carbon steel, and specialized alloys. They can accommodate different thicknesses and finishes according to specifications.
4. What production volumes can Chinese manufacturers handle?
Most Chinese manufacturers are equipped to handle both small-scale and large-scale production runs. They often have flexible production capabilities to meet varying customer demands.
5. How can I manage logistics and shipping from China?
Many manufacturers in China have experience with international shipping and can manage logistics efficiently. Clear communication regarding shipping terms, lead times, and incoterms is crucial for smooth delivery.
6. What are common challenges when sourcing from China?
Challenges may include language barriers, cultural differences, intellectual property protection, and longer lead times due to shipping distances. Working with reputable manufacturers and establishing clear contracts can mitigate these risks.
7. Are there specific regulations or tariffs to consider?
It’s essential to stay informed about import regulations, tariffs, and trade agreements that may impact the cost and timeline of importing sheet metal products from China. Engaging with a customs broker or logistics expert can provide guidance on these matters.
By addressing these FAQs, businesses can navigate the complexities of sourcing and manufacturing sheet bending services in China more effectively.
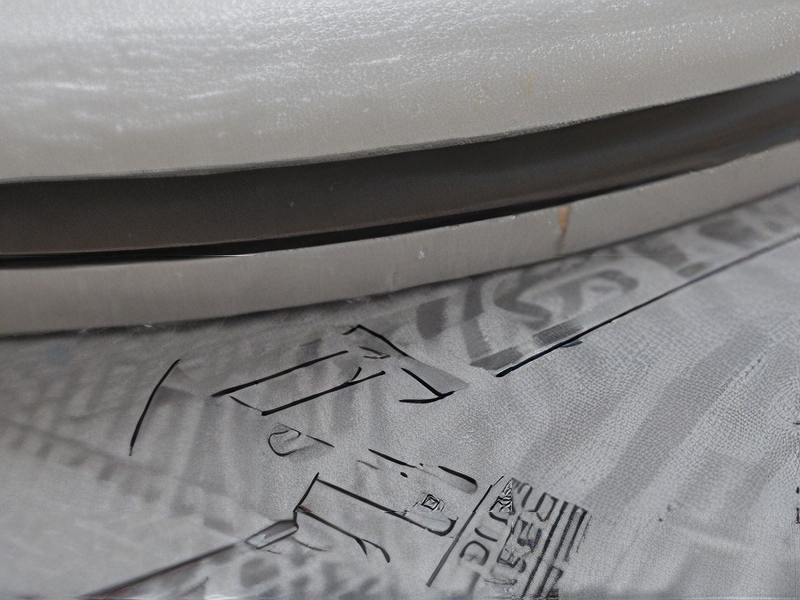