Technology and Applications of carbon steel versus cast iron
Carbon steel and cast iron are two distinct materials with unique properties and applications in various industries.
Carbon Steel:
Carbon steel is primarily composed of iron and carbon, with trace amounts of other elements. It is known for its strength, hardness, and durability. Carbon steel can be further categorized into low, medium, and high carbon steels, each offering different properties suitable for specific applications.
– Technology: Carbon steel is manufactured through the process of smelting iron ore with carbon in blast furnaces or electric arc furnaces. Depending on the carbon content and alloying elements added (such as manganese, chromium, or nickel), the properties of carbon steel can be tailored to meet specific requirements.
– Applications: It finds extensive use in structural components, machinery parts, automotive components, pipelines, and tools due to its strength and machinability. It is also used in construction and infrastructure projects where its load-bearing capacity and durability are beneficial.
Cast Iron:
Cast iron, on the other hand, contains a higher carbon content (typically 2-4%) compared to carbon steel. This high carbon content contributes to its brittleness but also provides unique properties.
– Technology: Cast iron is produced by melting iron along with high-carbon content (and sometimes silicon) in a furnace and then pouring it into molds. This process allows for complex shapes and intricate designs.
– Applications: Cast iron is favored for applications requiring wear resistance, thermal conductivity, and damping capacity, such as engine blocks, cookware, pipes, and architectural elements. Its ability to retain heat makes it ideal for cooking surfaces.
Comparison:
– Carbon steel is more ductile and less brittle than cast iron, making it suitable for applications requiring toughness and impact resistance.
– Cast iron excels in applications needing hardness, wear resistance, and thermal stability but is prone to brittleness.
In conclusion, while both carbon steel and cast iron have distinct advantages depending on the application, the choice between them hinges on specific performance requirements such as strength, hardness, machinability, and resistance to wear and corrosion.

Quality Testing Methods for carbon steel versus cast iron and how to control quality
Quality testing methods for carbon steel and cast iron focus on ensuring material properties meet specifications and performance requirements. For carbon steel, common methods include:
1. Chemical Composition Analysis: Using techniques like optical emission spectroscopy or X-ray fluorescence to verify elemental composition, ensuring it meets standards like ASTM A36 or AISI 1045.
2. Mechanical Testing: Includes tensile testing to assess strength, ductility, and elongation, as well as hardness testing (e.g., Rockwell or Brinell scales) to determine resistance to indentation.
3. Microstructural Examination: Optical or electron microscopy to inspect grain structure, identifying any anomalies that could affect mechanical properties or weldability.
4. Non-Destructive Testing (NDT): Techniques such as ultrasonic testing or magnetic particle inspection to detect internal defects or inconsistencies without damaging the material.
Quality control involves rigorous adherence to these testing methods at various stages of production, from raw material inspection to finished product evaluation. For cast iron, similar methods apply but with considerations for its specific composition and casting process nuances, such as:
1. Chemical Analysis: Ensuring the correct percentage of carbon, silicon, and other alloying elements for the desired casting properties (e.g., ASTM A48 for gray iron).
2. Dimensional Inspection: Checking casting dimensions against CAD models or engineering drawings to ensure accuracy and adherence to tolerances.
3. Visual Inspection: Surface examination for defects like porosity, cracks, or surface finish irregularities that could affect performance or aesthetics.
4. Mechanical and Metallurgical Testing: Verifying mechanical properties (e.g., tensile strength, hardness) and microstructure analysis (e.g., nodularity in ductile iron) to ensure castings meet specified standards.
Implementing robust quality management systems and conducting regular audits are essential to control quality effectively. This includes documenting test results, addressing non-conformities promptly, and continuously improving processes to meet customer expectations and regulatory requirements.

Tips for Procurement and Considerations when Purchasing from carbon steel versus cast iron
When deciding between carbon steel and cast iron for procurement, consider the following:
1. Material Properties: Carbon steel is known for its strength and durability, making it suitable for heavy-duty applications. Cast iron, on the other hand, is more brittle but has excellent heat retention properties.
2. Cost and Availability: Carbon steel tends to be more affordable and readily available in various grades and forms. Cast iron can be more expensive and less versatile in terms of shapes and sizes.
3. Maintenance and Care: Carbon steel requires regular maintenance to prevent rusting, including seasoning and proper drying after use. Cast iron also needs seasoning but is more prone to rust if not properly cared for.
4. Heat Conductivity: Cast iron has superior heat retention and even distribution, making it ideal for cooking applications. Carbon steel heats up and cools down quickly, which is beneficial for certain industrial processes.
5. Weight and Handling: Cast iron is significantly heavier than carbon steel, which can affect transportation costs and ease of handling.
6. Application Specifics: Consider the specific requirements of your application. For example, if you need a material for high-temperature cooking or for items that require significant strength, carbon steel might be preferable. For items that benefit from excellent heat retention and uniform cooking, cast iron could be the better choice.
7. Environmental Impact: Evaluate the environmental considerations of each material, including their recyclability and carbon footprint from production to disposal.
When making a procurement decision between carbon steel and cast iron, prioritize the material properties that align with your operational needs, budget constraints, and environmental considerations. Each material offers distinct advantages depending on the application, so understanding these factors will ensure you select the most suitable option.

FAQs on Sourcing and Manufacturing from carbon steel versus cast iron in China
When sourcing and manufacturing from China, choosing between carbon steel and cast iron involves several considerations:
1. Material Properties: Carbon steel offers higher tensile strength and is generally more durable than cast iron. Cast iron, however, has better compressive strength and is more resistant to wear and corrosion.
2. Cost: Carbon steel tends to be cheaper to manufacture due to simpler production processes and lower material costs. Cast iron, especially for intricate designs, may be more expensive due to its casting process.
3. Manufacturing Processes: Carbon steel is typically formed through rolling or forging, making it easier to produce consistent shapes and sizes. Cast iron requires casting, which involves pouring molten metal into molds, suitable for complex shapes but potentially costly and time-consuming.
4. Applications: Carbon steel is versatile and commonly used in structural components, machinery, and tools. Cast iron is favored for cookware, machine beds, and engine blocks due to its heat retention and vibration damping properties.
5. Quality Control: Both materials require stringent quality control measures in manufacturing. Carbon steel’s uniformity aids in easier quality assurance, while cast iron’s casting process demands careful monitoring to avoid defects.
6. Supplier Expertise: China has extensive expertise in manufacturing both materials. Suppliers specializing in carbon steel may offer more competitive pricing and faster production times compared to those focused on cast iron.
Ultimately, the choice between carbon steel and cast iron in China hinges on specific product requirements, budget constraints, and the expertise of your chosen supplier. Clear communication and thorough vetting of potential suppliers are crucial to ensuring the desired quality and cost-effectiveness of your manufacturing process.
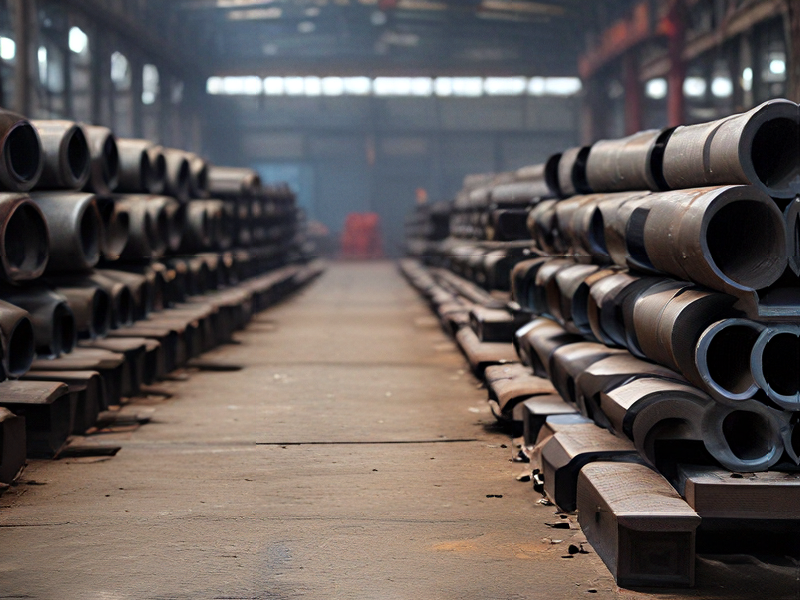