Technology and Applications of program cnc
Computer Numerical Control (CNC) technology revolutionizes manufacturing processes by automating machine tools through precise computer commands. This technology finds extensive applications across various industries, including automotive, aerospace, electronics, and healthcare.
In manufacturing, CNC machines execute complex tasks such as milling, turning, drilling, and grinding with exceptional accuracy and repeatability. These machines rely on CAD (Computer-Aided Design) and CAM (Computer-Aided Manufacturing) software to convert digital designs into precise instructions, known as G-code, which guides the CNC machine’s movements.
The versatility of CNC machines allows for the production of intricate components and prototypes, enhancing productivity and reducing lead times. In automotive manufacturing, CNC machining fabricates engine components, chassis parts, and intricate molds. Aerospace industries use CNC for manufacturing turbine blades, fuselage components, and structural parts with stringent tolerances.
Medical applications benefit from CNC’s ability to produce custom prosthetics, implants, and surgical instruments with high precision, tailored to patient-specific requirements. Additionally, CNC technology facilitates rapid prototyping in product development cycles by enabling quick iteration and testing of designs.
Moreover, advancements such as multi-axis machining and additive manufacturing (3D printing) further expand CNC capabilities, enabling the production of complex geometries and integrating multiple operations into single setups.
In conclusion, CNC technology continues to drive innovation across industries by improving manufacturing efficiency, precision, and flexibility. As technology advances, CNC machines are expected to play an increasingly pivotal role in shaping the future of automated manufacturing processes.
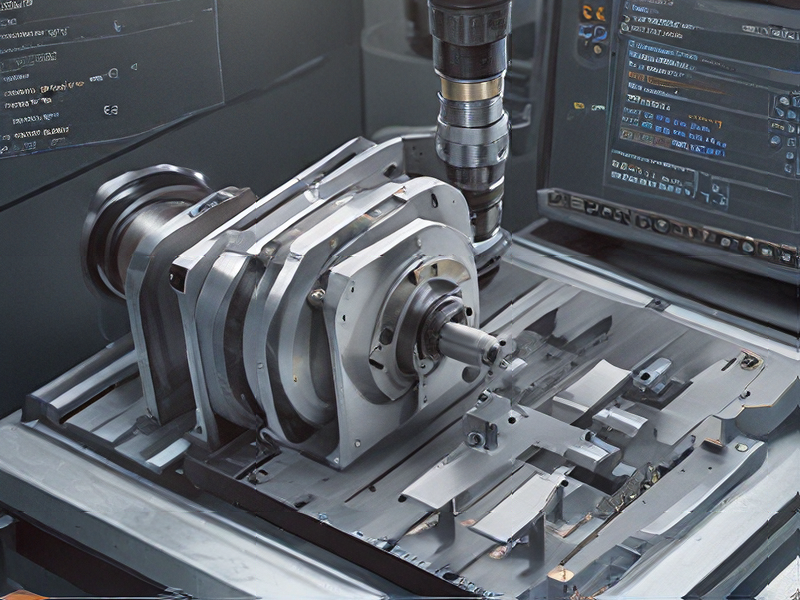
Quality Testing Methods for program cnc and how to control quality
To ensure quality in CNC (Computer Numerical Control) programs, several methods can be employed:
1. Simulation and Verification: Utilize software simulations to visualize toolpaths and machining operations before actual implementation. This helps detect errors in programming that could lead to defective parts.
2. Prototype Testing: Produce initial prototypes using the CNC program to validate dimensions, tolerances, and overall part functionality. This hands-on testing ensures that the program generates parts according to specifications.
3. Dimensional Inspection: Employ precision measurement tools like calipers, micrometers, or coordinate measuring machines (CMM) to verify critical dimensions of machined parts against CAD/CAM designs.
4. Tool and Material Checks: Ensure proper selection and condition of cutting tools and materials. Implement checks to confirm tool wear and material quality throughout the machining process.
5. Process Documentation and Standardization: Maintain detailed documentation of CNC programs, setup procedures, and quality standards. Standardizing processes helps in consistent quality control and facilitates troubleshooting.
6. Feedback and Continuous Improvement: Establish a feedback loop where operators and quality control personnel provide input on program effectiveness and identify areas for improvement. Regularly update programs based on these insights.
By integrating these methods, manufacturers can effectively control the quality of CNC programs, ensuring accurate, repeatable production of machined parts while minimizing errors and waste.
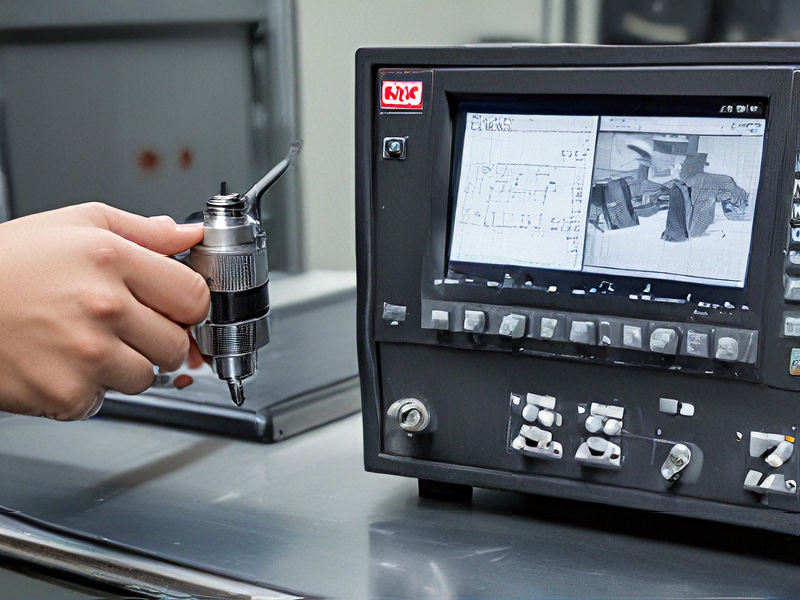
Tips for Procurement and Considerations when Purchasing from program cnc
When procuring from CNC programs, especially for CNC (Computer Numerical Control) machines or related equipment, several considerations are crucial:
1. Machine Specifications: Understand the exact specifications required for your operations. This includes the machine size, axis configurations, spindle power, and maximum feed rates relevant to your production needs.
2. Accuracy and Precision: CNC machines are known for their precision. Ensure that the machines you consider meet your required tolerances and accuracy levels, especially if your applications demand high precision.
3. Software Compatibility: Check the compatibility of the CNC machine with your existing software systems. This includes CAD/CAM software and any other production management tools you use.
4. Supplier Reputation: Research the reputation and reliability of the CNC program or supplier. Look for reviews, testimonials, and references from other customers to gauge their service quality and after-sales support.
5. Support and Training: Consider what support and training options are available. Proper training for your operators is crucial for maximizing productivity and minimizing downtime.
6. Maintenance and Service Contracts: Inquire about maintenance schedules and service contracts. Understand what is covered under warranty and what additional services are available post-purchase.
7. Cost and Value: Compare quotes from different suppliers, but also consider the overall value. A slightly higher initial cost may be justified if it includes better support, training, or longer-term reliability.
8. Future Expansion: Anticipate future needs and whether the CNC program can support scalability. This includes potential upgrades, additional machines, or changes in production requirements.
9. Compliance and Safety: Ensure that the CNC machines comply with safety regulations and industry standards. This is crucial for maintaining a safe working environment and avoiding legal issues.
10. Feedback and Continuous Improvement: After implementation, gather feedback from operators and regularly assess the performance of the CNC program. This helps in identifying areas for improvement and optimizing machine utilization.
By considering these factors, you can make a well-informed decision when procuring CNC machines or equipment from a CNC program, ensuring that they meet your operational needs effectively.
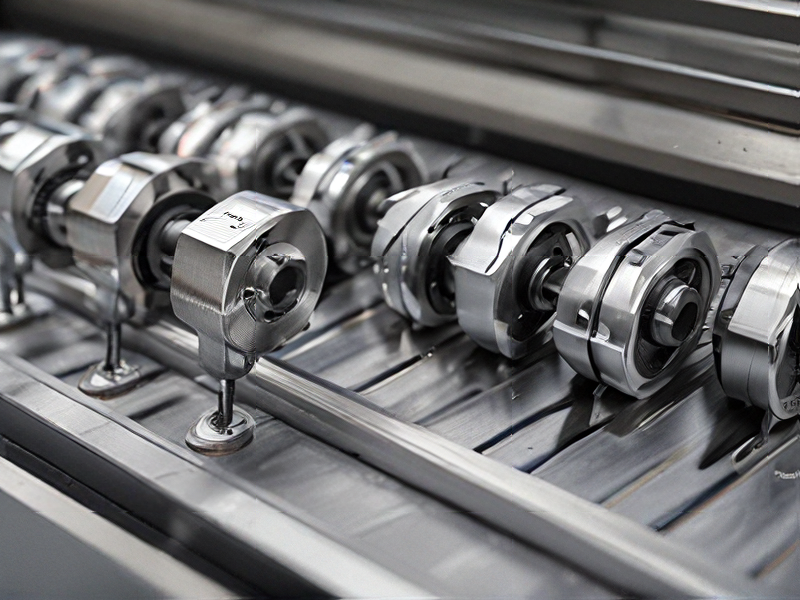
FAQs on Sourcing and Manufacturing from program cnc in China
When sourcing and manufacturing CNC programs in China, consider these frequently asked questions (FAQs):
1. What are the key considerations when sourcing CNC machining services in China?
It’s crucial to assess the supplier’s capabilities, quality standards, lead times, and their experience with your specific CNC requirements. Verify their equipment, certifications (like ISO), and their ability to communicate effectively in your language.
2. How do I ensure quality when outsourcing CNC manufacturing to China?
Quality assurance starts with supplier selection. Conduct thorough due diligence, including site visits if possible. Implement clear specifications and quality control processes. Request samples and prototypes before full-scale production to assess accuracy and finishing.
3. What are the typical lead times for CNC manufacturing in China?
Lead times vary based on complexity, quantity, and supplier capacity. Generally, expect initial lead times to be longer due to setup and prototyping phases. Once production starts, lead times can be more predictable with proper scheduling and communication.
4. How do I protect my intellectual property (IP) when outsourcing CNC programs to China?
Ensure suppliers sign non-disclosure agreements (NDAs) and have robust IP protection measures in place. Consider registering your designs and patents in China if applicable. Limit the information shared with suppliers to only what’s necessary for production.
5. What are the common challenges when sourcing CNC programs from China?
Language barriers, cultural differences, logistics, and potential quality issues are common challenges. Effective communication, clear contracts, and regular inspections can mitigate these risks.
Navigating these considerations with diligence and clear communication will help streamline sourcing and manufacturing of CNC programs in China effectively.
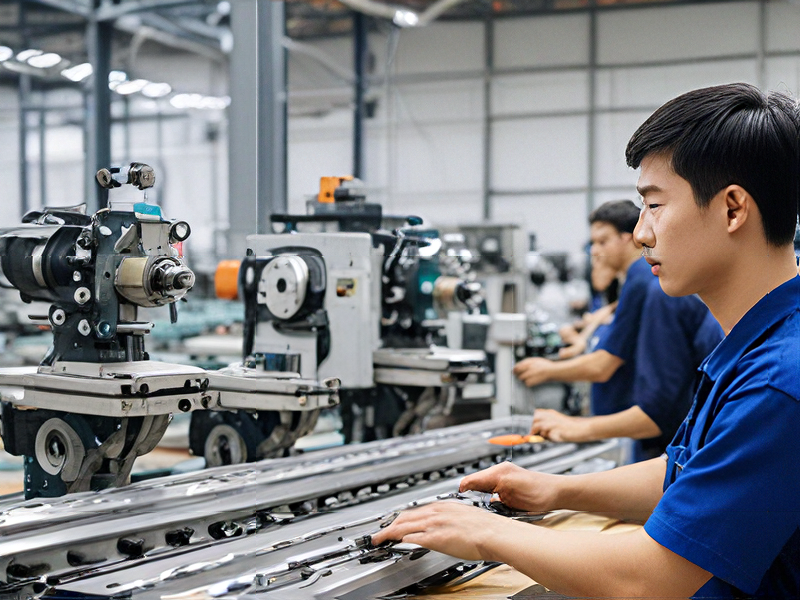